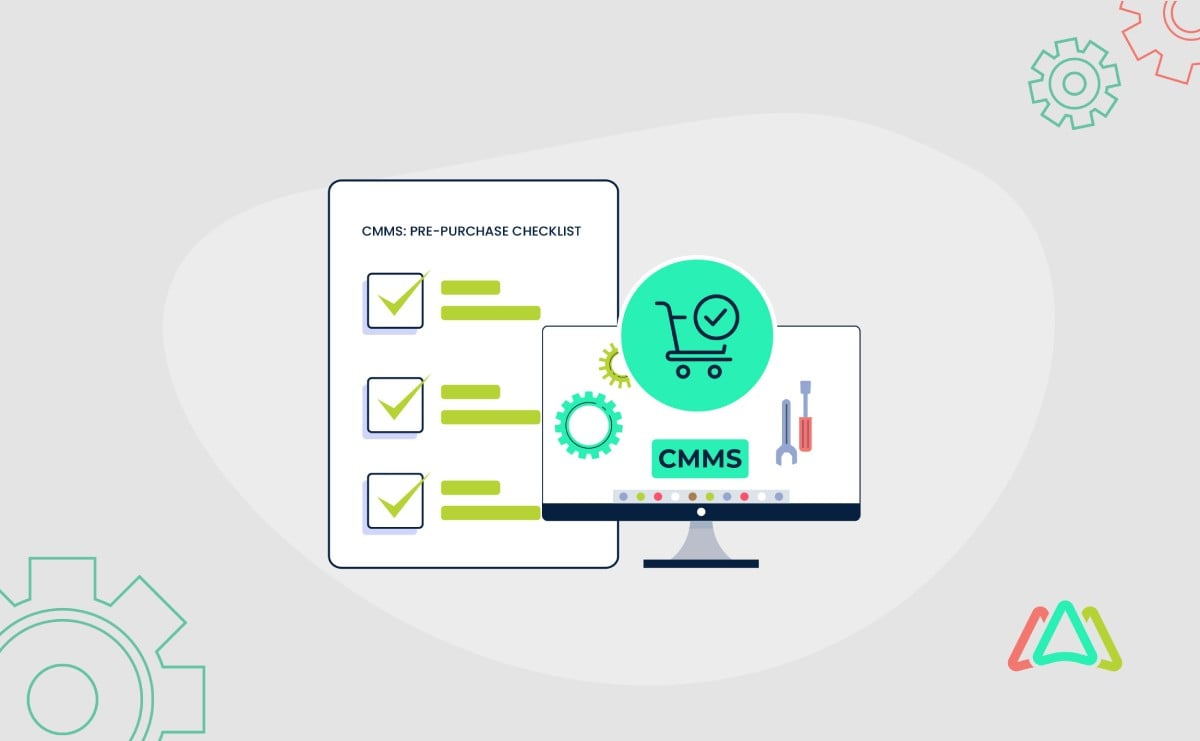
10 Things to Do Before Purchasing a CMMS that Helps Success
There is much to consider when purchasing a Computerized Maintenance Management System (CMMS). Making that move will involve considerable time, resources, and financial outlay. Taking several steps before purchasing a CMMS will help ensure its implementation and long-term success.
1. Define Your Objectives and Goals
Simply put, this involves outlining what you want to achieve with the CMMS. This initial step is crucial because it will ensure that your selected CMMS will meet your organization's specific needs and requirements. Involve stakeholders when taking into account the following:
Your current maintenance practices
Think about your workflows and resource allocations. Also, identify your organization’s pain points, inefficiencies, and areas that need improvement.
Set measurable goals
Consider specific, measurable, achievable, relevant, and time-bound things. Examples are reducing equipment downtime by 20% within the first year, increasing the productivity of maintenance teams by 15%, or improving inventory management accuracy to 95% or higher.
Consider long-term goals
Think about how your organization may grow or change down the road. Consider where it may be in five years or ten years. Will your needs change during these times?
2. Conduct a Needs Assessment
After evaluating your current maintenance processes and the areas needing improvement, the next step is prioritizing your organization’s needs. Rank your objectives based on their importance and urgency. Focus on critical areas that will have the most significant impact on operations. Doing so helps understand the specific features and functionalities your CMMS should have.
Identify key features and functionality
List the essential features and capabilities you need in a CMMS. Examples include work order management, preventive maintenance scheduling, asset tracking, reporting, mobile access, etc.
3. Budget Planning
Your budget will weigh heavily in determining your choices with a CMMS. Establishing a realistic budget for purchasing, implementing, and maintaining the CMMS is vital. Above all, it must align with your financial capabilities. When considering the purchase of a CMMS, several financial aspects must be evaluated.
Initial costs
The initial cost refers to the upfront expense of acquiring the CMMS software. It may include licensing fees, implementation costs, and hardware upgrades.
Subscription or licensing fees
Some CMMS solutions are offered on a subscription basis, while others require a one-time licensing fee. Compare the costs and choose the model that aligns best with your budget.
Implementation costs
These can include expenses for data migration, customization, training, and any additional resources needed to get the CMMS up and running.
Customization costs
Depending on your specific needs, you may need to customize the CMMS. Consider the cost of tailoring the system to fit your organization's unique requirements.
Integration costs
If you plan to take the CMMS integration route and pair it with other software systems (e.g., ERP, accounting software), you must factor in the cost of integration services or middleware.
Training expenses
Training your staff to use the CMMS effectively involves costs for training materials, instructor-led sessions, or online courses.
Ongoing support and maintenance
Consider the cost of ongoing technical support, updates, and maintenance. Some CMMS providers offer support packages or maintenance contracts.
Hardware costs (if applicable)
If your organization needs to invest in additional hardware to support the CMMS, such as servers or mobile devices, include these expenses in your budget.
User licenses
Depending on the CMMS, you may need to pay for user licenses. Consider how many licenses you'll need and if there are different access levels.
Total cost of ownership (TCO)
The total cost of ownership includes all costs associated with the CMMS over its expected lifespan, including initial fees, ongoing support, and additional expenses.
Regulatory compliance and licensing
Regulatory requirements may dictate the type of CMMS you need, depending on your industry. Ensure that the system you choose complies with any relevant regulations.
Renewal terms and conditions
If you opt for a subscription-based CMMS, carefully review the terms and conditions for renewals. Understand if there are any price escalations or changes in service levels.
4. User Involvement and Training
Involve the end-users (maintenance technicians, managers, etc.) in the selection process. Their input is crucial. As noted above, plan for adequate training to ensure everyone is proficient in using the system.
5. Think about Scalability
A CMMS is a long-term investment. It needs to grow with the organization and adapt to changing requirements to have sustainability. It ensures it remains an effective tool for managing maintenance operations even as the organization evolves.
Scalability refers to a CMMS's ability to handle increasing data, users, or workload without compromising performance. Specifically, scalability means the software can adapt and grow with the organization's needs. It is crucial for businesses that may experience growth over time. For example, if a company expands its operations, it might need to track more equipment, schedule more maintenance tasks, and involve more users in the CMMS. A scalable CMMS will accommodate these increased demands without significant performance degradation.
6. Think about Flexibility
Flexibility in a CMMS means that the system can be customized or configured to meet the specific needs and workflows of the organization. It can include customizing work order forms, setting up preventive maintenance schedules, defining user roles and permissions, integrating with other software systems, and even making it possible for users to customize their dashboards based on their preferences.
A flexible CMMS allows the system to adapt to an organization’s needs. Additionally, a flexible CMMS can adapt to changes in business processes or regulations. For example, a flexible system can adapt to a shift in compliance requirements.
7. Conduct Vendor Evaluation
The CMMS marketplace offers many options for buyers seeking a digital solution to improve their organization’s operations. Here, a quick review will show you different platforms, features, add-ons, terms and conditions, and price points. Evaluating a CMMS vendor is crucial in choosing a solution that aligns with your organization's maintenance management needs.
Check for industry experience
Determine if the vendor has experience working with organizations in your industry. Industry-specific knowledge can be a significant advantage. Regardless of your industry, inquire about the vendor's plans for the CMMS. They should have a clear roadmap for updates and improvements.
Customer references and reviews
A reputable vendor should be able and willing to provide potential buyers with references. Don’t hesitate to ask the vendor for customer references or case studies. Contact these references for their experience with the CMMS and its implementation.
Vendor's financial stability
Ensure that the vendor is financially stable. Ask how long the vendor has been in business and what experience its principals have had in the CMMS marketplace. These factors will indicate their ability to support and update the CMMS long-term.
Ease of use
The CMMS should be user-friendly and intuitive. Conduct a demo or trial to see if it's easy for your team to navigate and use. A hands-on experience will give you a better understanding of its capabilities.
Integration and customization capabilities
Integration capabilities can streamline your operations. Ensure the CMMS can integrate with existing software and hardware systems (e.g., ERP, IoT devices). Also, determine if the CMMS can be customized to meet specific needs because it allows you to adapt the system to match your unique workflow and reporting requirements.
Mobile accessibility
A mobile-friendly CMMS allows technicians to access and update information in the field. It is essential for remote or field-based teams. This feature should not be overlooked if this is your organization’s need now or in the foreseeable future.
Training and support
Inquire about the training and support options provided by the vendor. Ensure they offer comprehensive training for your team to use the system effectively and have access to necessary resources for ongoing use. Determine what added costs are associated with these services.
Compliance and Regulatory Support
If your industry has specific regulatory requirements (e.g., OSHA, ISO standards, GDPR, HIPPA), ensure the CMMS can help you comply. Verify that it has security measures in place to protect your data. Ask about the security measures in place to protect your data.
Total Cost of Ownership (TCO)
As noted previously, consider all costs associated with implementing and maintaining the CMMS, including licensing fees, implementation costs, training, support, and additional modules or features.
8. Understand Data Migration and Conversion
CMMS data migration and conversion refer to transferring information from an existing system (or systems) to a new CMMS. Data migration and conversion are critical because they ensure that important historical and operational data is preserved and accessible in the new system, enabling organizations to continue their maintenance operations seamlessly. This is a multiphased process that requires time, energy, and resources. It begins with data extraction and transformation, then data mapping, verification, testing, and validation, and finally, data backup and user training.
9. Conduct Pilot Testing
Pilot testing in the context of CMMS refers to testing the software on a smaller scale, typically within a specific department or area of an organization, before rolling it out to the entire organization. Pilot testing is crucial in implementing a CMMS because it helps ensure the system is effectively integrated into the organization's maintenance operations.
Selecting a test group
Choose a specific department or area representing the broader organization where you'll implement the CMMS on trial.
Testing workflows
The test group should start using the CMMS for their maintenance tasks. Testing workflows include entering work orders, tracking maintenance activities, and generating reports.
Gathering feedback
Collect feedback from the test group about their experience using the CMMS. It should include any challenges they face, suggestions for improvements, and overall satisfaction with the system.
Evaluating performance
Assess how well the CMMS is performing in terms of improving maintenance processes, reducing downtime, and enhancing efficiency within the test group.
Addressing issues
Address any issues or challenges identified during the pilot testing phase. This may involve making software adjustments, providing additional training, or refining workflows.
10. Scale Up to Full Use
Once the CMMS has been successfully tested and refined within the initial group, it can be gradually implemented across the organization. This process may involve further training, data migration, and fine-tuning based on the lessons learned during the pilot phase.
The success of a CMMS largely depends on how well it aligns with your organization's needs and processes. Planning and evaluating before purchasing can lead to a smoother and more successful implementation and positive outcomes.
TABLE OF CONTENTS
Keep Reading
Ever find yourself checking into a luxury hotel and expecting a relaxing stay, only to find a ...
11 Apr 2025
Organizations are witnessing swift changes in the business environment and confronting a ...
8 Apr 2025
Last month, news outlets and the entire internet was abuzz with the return of NASA astronauts ...
3 Apr 2025
What comes first - CMMS or predictive maintenance? If your answer is either, it is correct. ...
28 Mar 2025
Artificial intelligence (AI) talk has become commonplace. Today, engaging in business-focused ...
27 Mar 2025
Imagine a world where machines predict, diagnose, and fix their issues before they fail. This ...
25 Mar 2025
A facility maintenance plan is at the core of a facility’s operations. This organized ...
21 Mar 2025
Think of managing your maintenance operations like managing a championship sports team. Just ...
21 Mar 2025
The maintenance sector is battling a severe talent shortage that threatens to undermine ...
7 Mar 2025
Manufacturing maintenance is the backbone of industrial efficiency, ensuring machines run ...
5 Mar 2025
No one likes playing a guessing game when equipment breaks down. Yet, maintenance teams often ...
4 Mar 2025
The size of the preventive maintenance software market is discussed in millions of dollars, ...
4 Mar 2025
The organizational structure and corporate hierarchy vary from company to company. Large ...
28 Feb 2025
Maintenance procedures are essential for ensuring the longevity and reliability of machinery ...
21 Feb 2025
Sustainability is no longer just a buzzword; it's a critical component of corporate social ...
20 Feb 2025
A Computerized Maintenance Management System (CMMS) relies on accurate, well-organized data ...
18 Feb 2025
In an era where technology drives operational efficiency, Computerized Maintenance Management ...
14 Feb 2025
A Computerized Maintenance Management System (CMMS) is a key component of modern maintenance ...
13 Feb 2025
Introduction Maintenance management is the foundation of maintenance operations in industries ...
11 Feb 2025
Introduction A Computerized Maintenance Management System (CMMS) is software designed to help ...
7 Feb 2025