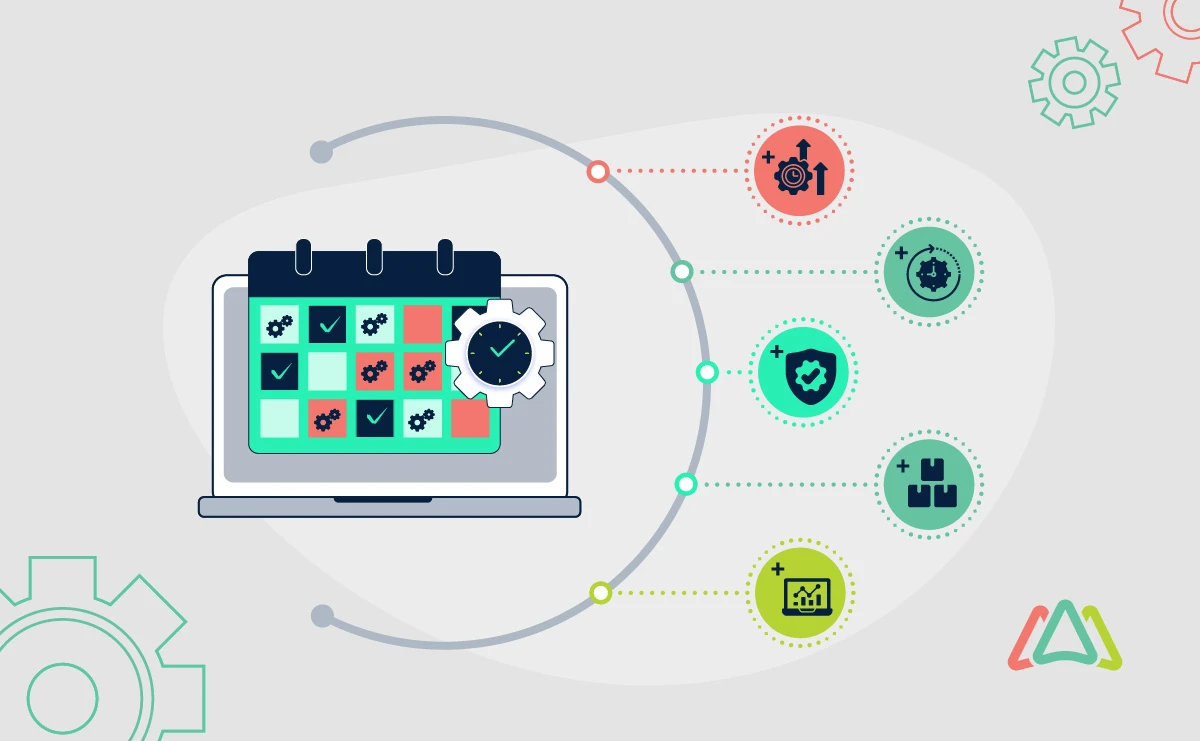
5 Benefits of Preventive Maintenance
When we think about the challenges facing modern businesses today, three objectives come to mind: operational efficiency, productivity, and cost effectiveness. Maintenance management strategies are central to achieving these goals, where leaders direct their attention to ensuring business operations run smoothly with minimal interruption. Preventive maintenance is a fundamental maintenance strategy and a hallmark feature of Computerized Maintenance Management Systems (CMMS) that is instrumental in driving operational efficiency and lowering costs.
Understanding the significant advantages of preventive maintenance is important for companies considering implementing a CMMS. By leveraging preventive maintenance through CMMS software, businesses can streamline operations, enhance asset performance, and ultimately bolster their bottom line. This article delves into five key benefits of preventive maintenance and illustrates how it positively impacts various industries.
Preventive Maintenance Benefit #1: Reduced Downtime and Increased Equipment Reliability
Equipment downtime can be a significant drain on business resources. Unplanned downtime disrupts operations and leads to lost revenue and decreased productivity. When equipment and other systems are not operational, production stalls, leading to delays in delivering goods and services to its customers. This interruption disrupts workflow schedules, causing inefficiencies and bottlenecks across various departments.
In addition to lost revenue from disrupted production, downtime often results in other costs, such as overtime pay for workers trying to catch up on missed deadlines and expensive rush orders for replacement parts. Prolonged downtime can hurt a company's reputation by diminishing customers’ trust and loyalty and jeopardizing its competitive standing in the marketplace.
Preventive maintenance, facilitated by CMMS software, helps mitigate these negative impacts by identifying and addressing potential issues before they escalate into breakdowns and lengthy downtime during major repairs. Companies can minimize the likelihood of unexpected failures by scheduling regular maintenance tasks based on equipment usage, condition, and manufacturer recommendations.
When considering how CMMS preventive maintenance plays out, let’s turn to the manufacturing sector, where production downtime directly impacts revenue. Showing the value of preventive maintenance, A.T. Kearney’s and Industry Week’s survey of 558 companies reported a 20.1% reduction in equipment downtime. Further emphasizing this point, a 2005 survey by Thomas Industry Update found that the average cost of unplanned downtimes in the automotive industry amounted to $22,000 per minute. Together, these findings indicate substantial cost savings and improved equipment reliability.
Preventive Maintenance Benefit #2: Extended Asset Lifespan
Fixed assets represent one of the most valuable investments for organizations. Maximizing their useful life expectancy is key to optimizing ROI. Maintenance management strategies should prioritize extending asset lifespan. Reactive maintenance as a strategy that focuses on addressing equipment failures as they occur doesn’t bode well when trying to maximize asset life expectancy.
With reactive maintenance, assets are exposed to unnecessary wear and tear without regular inspections, lubrication, and calibration. When this happens, small issues may escalate into more significant problems, causing irreversible damage to the equipment. Reactive maintenance often involves quick fixes that remedy the problem temporarily to save time. These solutions fail to address the root cause of the problem, resulting in recurring breakdowns and decreased reliability over time. Overall, the lack of proactive care and maintenance shortens the lifespan of assets, leading to increased repair costs, decreased operational efficiency, and reduced overall performance.
Preventive maintenance extends the life expectancy of assets by keeping them in optimal working condition through regular inspections, lubrication, and calibration. Routine inspections identify and address problems before they escalate into costly failures. Preventive maintenance mitigates wear and tear on equipment, minimizes the likelihood of unexpected breakdowns, and prevents premature deterioration. Enhancing asset longevity maximizes the return on investment while delaying the need for costly replacements and upgrades.
In the facility management sector, where buildings and infrastructure are significant assets, preventive maintenance is critical in preserving their value. Findings from a study by The Federal Energy Management Program (FEMP) underscore the benefits of preventive maintenance, showing that it reduces downtime by 30-50% and prolongs the life expectancy of equipment by as much as 20-40%.
Preventive Maintenance Benefit #3: Improved Safety and Compliance
Ensuring a safe working environment is a legal and moral obligation for businesses. Preventive maintenance helps identify and prevent safety hazards before they threaten employees or the environment. Companies can mitigate risks and avoid penalties by conducting routine inspections and adhering to regulatory compliance standards.
Using a CMMS to manage preventive maintenance helps establish standardized procedures and documentation protocols through regular inspections and maintenance activities. These strategies facilitate regulatory compliance by documenting comprehensive records of maintenance activities, inspections, and equipment certifications. This ensures that all assets are maintained according to industry regulations and safety standards. This minimizes the risk of penalties or legal liabilities due to non-compliance. Implementing CMMS software for preventive maintenance not only fosters a safer work environment but also strengthens the organization's reputation for prioritizing employee well-being and adhering to regulations.
For example, the oil and gas industry is subject to strict regulatory requirements that govern its operations. For these organizations, preventive maintenance is instrumental in ensuring the integrity of critical infrastructure and equipment. By leveraging CMMS software for maintenance management, companies can track and document compliance-related tasks, such as equipment inspections and calibration checks. These measures reduce the likelihood of accidents and ensure regulatory adherence.
Preventive Maintenance Benefit #4: Optimized Inventory and Resource Management
Efficient allocation of resources, including spare parts, tools, and labor, is paramount for effective maintenance management as it directly impacts the organization's ability to conduct timely and cost-effective maintenance activities. By optimizing the inventory of spare parts and tools, maintenance teams ensure that necessary components are readily available when needed, minimizing the downtime resulting from waiting for orders. Additionally, strategically allocating resources enables better labor utilization, ensuring that skilled technicians are deployed efficiently to address maintenance tasks based on priority and expertise. This enhances operational efficiency and reduces idle time and labor costs. As a result of transitioning from unplanned, reactive maintenance to planned, scheduled maintenance, maintenance planners reduce the need for overtime pay and higher costs for calling vendors in for emergency repairs. Finally, by closely monitoring resource utilization and costs, maintenance managers can identify opportunities for cost savings and process improvements, ultimately enhancing the overall performance and profitability of the maintenance department.
Preventive maintenance allows companies to plan and optimize their inventory levels based on predictive maintenance schedules, reducing excess inventory and minimizing stockouts. Through proactive maintenance scheduling and predictive analysis, organizations can anticipate the demand for specific parts and tools, allowing them to stock sufficient inventory without overstocking. By aligning inventory levels with preventive maintenance schedules, maintenance departments ensure critical components are available when needed, minimizing downtime associated with waiting for replacements. Additionally, preventive maintenance enables better planning for procurement and replenishment, allowing organizations to negotiate favorable commercial terms with suppliers. By optimizing inventory levels, companies can reduce carrying costs while minimizing the risk of stockouts.
In the transportation industry, where fleet maintenance is a critical component of operations, using CMMS software to manage preventive maintenance enables companies to optimize their inventory management KPIs. By tracking the usage and life expectancy of spare parts, scheduling preventive maintenance tasks, and automating reorder points, transportation and logistics companies reduce downtime and improve fleet reliability while controlling maintenance costs.
Preventive Maintenance Benefit #5: Data-Driven Decision-Making and Performance Analytics
CMMS’s preventive maintenance feature empowers maintenance managers to make data-driven decisions by providing comprehensive insights into maintenance operations. Through real-time data collection and analysis, CMMS software allows managers to track Maintenance KPIs, such as equipment uptime, maintenance costs, and workforce productivity. By accessing historical maintenance data and performance metrics, managers can identify trends, patterns, and areas for improvement, enabling informed decision-making.
Moreover, some advanced CMMS software platforms facilitate predictive maintenance by leveraging algorithms to forecast equipment failures and schedule maintenance activities proactively. This proactive approach minimizes downtime and repair costs, optimizes resource allocation, and extends asset lifespan. Predictive maintenance (PdM) one-ups traditional preventive maintenance by triggering maintenance activities only when needed rather than on a fixed interval schedule. One of the disadvantages of preventive maintenance is that it sometimes results in unnecessary maintenance tasks or over maintaining, which ends up costing more. For a deeper analysis of the advantages and disadvantages of various maintenance strategies, read this article. Through data analytics, CMMS preventive maintenance software enables maintenance managers to optimize maintenance strategies, enhance operational efficiency, and drive continuous organizational improvement.
In the healthcare sector, where equipment uptime is critical for patient care, preventive maintenance is vital in ensuring reliability and compliance. By leveraging CMMS software to track maintenance activities and analyze performance metrics, hospitals can identify areas for improvement, minimize risks, optimize maintenance schedules, and enhance the overall quality of service delivery.
Preventive maintenance facilitated by CMMS software offers many benefits for organizations across various industries. Preventive maintenance represents a strategic investment that pays dividends in the long run, from reducing downtime and extending asset life to improving safety and compliance. With preventive maintenance, businesses enhance operational efficiency, optimize resource utilization, and drive sustainable growth and profitability.
Guidelines for Implementing a CMMS Preventive Maintenance Program
1. Assess Current Maintenance Practices
Evaluate existing maintenance procedures and workflows, identify areas for improvement and inefficiencies, and determine metrics and KPIs to measure effectiveness.
2. Select Suitable CMMS Software
Research and evaluate CMMS software options, consider preventive maintenance scheduling, work order management, and reporting capabilities, and choose a solution that aligns with the organization's budget, scalability requirements, and specific needs.
3. Define Preventive Maintenance Tasks
Create a comprehensive list of equipment and assets requiring maintenance, determine maintenance schedules based on manufacturer recommendations, usage patterns, and criticality, and establish standard operating procedures (SOPs) for preventive maintenance tasks.
4. Set Up CMMS Software
Implement and configure the CMMS software, input asset information, including specifications, maintenance history, and warranty details, and configure preventive maintenance templates and schedules according to the assets’ requirements.
5. Train & Onboard Maintenance Staff
Provide training sessions on using the CMMS software effectively, educate maintenance personnel on preventive maintenance procedures and protocols, and emphasize the importance of data accuracy, documentation, and compliance with maintenance standards. Leverage your CMMS provider to assist with the CMMS software training and onboarding. Solutions providers have training specialists who are experts in onboarding end-users and can direct your team to training resources like videos, webinars, articles, etc.
6. Develop Maintenance Workflows
Define and establish workflows for creating, assigning, and tracking work orders, establish escalation procedures for addressing maintenance issues and resolving conflicts, and implement a system for prioritizing and scheduling maintenance tasks based on urgency and criticality. Workflows and processes should be tailored to the maintenance team size, resources and expertise.
7. Integrate with Existing Systems
If required, integrate the CMMS software with other relevant software applications, such as ERP, HRIS, inventory management and procurement platforms. Integrations can be tricky, and expensive. If necessary, strive for seamless data exchange and interoperability to streamline workflows and improve efficiency.
8. Launch Pilot Program
For more complex and larger maintenance operations, it’s recommended to start with a pilot program to test the effectiveness of the preventive maintenance system and solicit feedback from maintenance staff and other users.
9. Refine and Optimize Processes
It’s advised to periodically evaluate and refine the preventive maintenance processes based on performance metrics and feedback. Stay current on best practices and adjust the software based on lessons learned. Stay current on software updates, industry trends and technological advancements.
10. Promote Adoption and Culture Change
Foster a culture of proactive maintenance and accountability across the organization, Encourage collaboration between maintenance teams, operations, and management to drive continuous improvement, and recognize and reward employees for their contributions to the success of the preventive maintenance program.
TABLE OF CONTENTS
Keep Reading
Ever find yourself checking into a luxury hotel and expecting a relaxing stay, only to find a ...
11 Apr 2025
Organizations are witnessing swift changes in the business environment and confronting a ...
8 Apr 2025
Last month, news outlets and the entire internet was abuzz with the return of NASA astronauts ...
3 Apr 2025
What comes first - CMMS or predictive maintenance? If your answer is either, it is correct. ...
28 Mar 2025
Artificial intelligence (AI) talk has become commonplace. Today, engaging in business-focused ...
27 Mar 2025
Imagine a world where machines predict, diagnose, and fix their issues before they fail. This ...
25 Mar 2025
A facility maintenance plan is at the core of a facility’s operations. This organized ...
21 Mar 2025
Think of managing your maintenance operations like managing a championship sports team. Just ...
21 Mar 2025
The maintenance sector is battling a severe talent shortage that threatens to undermine ...
7 Mar 2025
Manufacturing maintenance is the backbone of industrial efficiency, ensuring machines run ...
5 Mar 2025
No one likes playing a guessing game when equipment breaks down. Yet, maintenance teams often ...
4 Mar 2025
The size of the preventive maintenance software market is discussed in millions of dollars, ...
4 Mar 2025
The organizational structure and corporate hierarchy vary from company to company. Large ...
28 Feb 2025
Maintenance procedures are essential for ensuring the longevity and reliability of machinery ...
21 Feb 2025
Sustainability is no longer just a buzzword; it's a critical component of corporate social ...
20 Feb 2025
A Computerized Maintenance Management System (CMMS) relies on accurate, well-organized data ...
18 Feb 2025
In an era where technology drives operational efficiency, Computerized Maintenance Management ...
14 Feb 2025
A Computerized Maintenance Management System (CMMS) is a key component of modern maintenance ...
13 Feb 2025
Introduction Maintenance management is the foundation of maintenance operations in industries ...
11 Feb 2025
Introduction A Computerized Maintenance Management System (CMMS) is software designed to help ...
7 Feb 2025