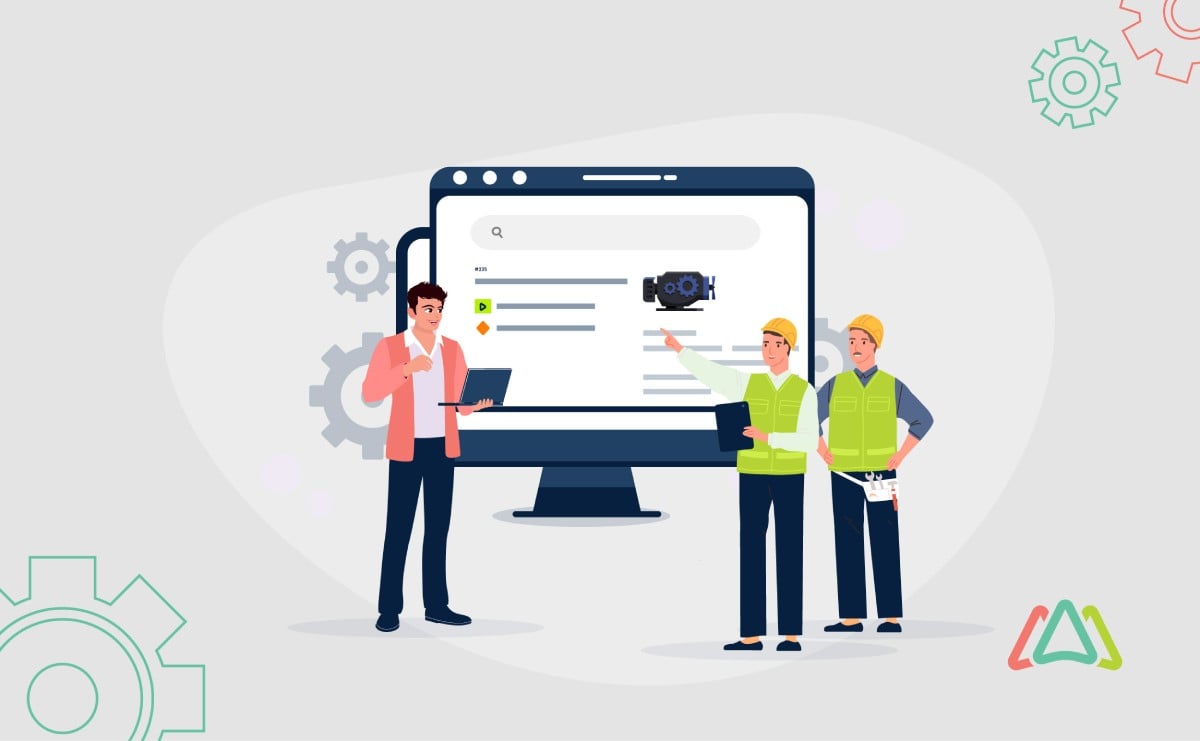
5 Creative Ways to Motivate Your Maintenance Employees to Adopt a CMMS
If you’ve been researching Computerized Maintenance Management Systems (CMMS), you already know the many benefits they deliver to your maintenance operations. You may also be aware that a CMMS’s ability to perform as it should is greatly dependent upon how well the system is implemented and adopted by its users. An essential aspect of the implementation phase is technician onboarding. This refers to ensuring that technicians, who most often represent the majority of CMMS end users, are well versed in using the CMMS features and functionality as well as incorporating it into their daily work routines. This is where the rubber hits the road because users’ resistance to embracing this new technology can be a huge impediment to successful CMMS implementation. Without technicians’ buy-in, a CMMS will underperform and not deliver the results you are looking for.
A lot has been written about why employees resist CMMS systems. The question that follows is, “how do employers motivate maintenance technicians to overcome their hesitation by seeing the value in investing their time and energy learning how to use a system that will improve their work experience?” And as you might expect, there are also numerous articles on what employers can do to break through technicians’ reluctance to adopt a CMMS. However, as many have found, this is often easier said than done. That’s where injecting creativity into the technician onboarding process can make a big difference.
In this article, we’re thinking outside the box and providing five creative and unconventional ways employers and maintenance managers can make the onboarding process more enticing and interesting to resistant technicians. As a starting point though, let’s begin by briefly reviewing the most common reasons why technicians are resistant to adopting a CMMS in the first place.
Main Reasons Maintenance Technicians Resist Adopting a CMMS
1. Don’t Fix What isn’t Broken
This refers to the belief that if a tried and true way of doing things does the job, then there shouldn’t be a need to change it. Maintenance technicians may be accustomed to traditional paper-based or manual systems. For them, the thinking is, “this works well so why look for trouble by changing to a totally new way of doing things?” Transitioning to a digital CMMS always requires time and training as well as a shift in workflow. These requirements can be intimidating or frustrating to resistant technicians.
2. Fear of the Unknown
A common reaction to having a fear of the unknown is to avoid it entirely. When it comes to maintenance technicians with a limited understanding of technology or only rudimentary computer skills, they may prefer to avoid learning how to use a CMMS because they believe it is too complex or too difficult to use. The perceived complexity of CMMS becomes their roadblock to adopting it.
3. What if…?
An upshot of having a fear of the unknown is a lack of trust in embracing something new. When it comes to a CMMS, this may originate from lack of familiarity with the system including misinformation or not clearly understanding its benefits. Add to this an inborn resistance to change as well as limited computer skills. The result is a distrust in a CMMS being a useful tool in increasing efficiency in their organization’s operations. Finally, many resistant technicians feel that by adopting a CMMS, their jobs may be at risk because it might lead to downsizing or rightsizing, redundancy and job loss, especially if the system is seen as a way to increase efficiency.
4. This isn’t for Us
It is common for organizations to develop their own culture of conduct and beliefs. In some situations, when a CMMS is being introduced, employers find themselves confronted with cultural resistance to it. This can be a major barrier to the adoption of a CMMS because there might be an ingrained culture within an organization that resists technological changes of any kind.
Commonly Cited Techniques for Motivating CMMS Adoption
The following are some commonly cited techniques that can help managers increase CMMS software adoption and buy-in from maintenance technicians and other end users.
1. Involve Technicians in the CMMS Evaluation Process
Involving maintenance technicians throughout the CMMS discovery process is helpful in promoting staff buy-in and adoption. This means involving technicians in the selection process, allowing them to give feedback about the products being reviewed and their needs and concerns. This is especially important for future users that are not familiar with CMMS platforms allowing them an opportunity to see what’s out there and understand the benefits the software can bring to their jobs and department early on. For technicians that have past experience with CMMS software, having them involved in the evaluation process allows them to see different platforms and share their past good and bad experiences and weigh in. Giving technicians a voice in product selection helps promote future buy-in and adoption.
2. Offer Hands-on CMMS Training
This seems obvious, but often gets overlooked. It is really important to invest in interactive training where technicians can get hands-on experience with the CMMS software. Most training can be delivered economically using web-conference sessions and webinars. Web-conference training can be delivered via Zoom, MS Teams, Goog Meets or other tools. There should be at least a couple of company specific training sessions scheduled that are no more than an hour long and recorded. These sessions should focus on company specific requirements. Users should also be encouraged to join future webinar sessions to stay current on new features and brush up on CMMS feature skills and understanding. For larger maintenance teams (15 or more) it can be helpful to use a mix of on-site and remote training. On-site training helps promote CMMS vendor relationships with the end users and puts a human face to the name.
3. Highlight the Benefits of CMMS
Employers and maintenance managers should emphasize how CMMS software can make their jobs easier by streamlining work orders, providing quick access to information, and automating routine tasks. A focus should be on how it can lead to reduced downtime, improved asset performance, and better overall maintenance outcomes.
4. Demonstrate CMMS Time Saving Benefits
Show technicians how using the CMMS can save them time by automating administrative tasks, providing easy access to historical data, and reducing paperwork. By demonstrating how this time saving benefit can be reinvested into more valuable tasks, such as preventive maintenance or troubleshooting, they will soon come to see a CMMS as being a useful tool.
5. Gather Feedback and Work Toward Continuous Improvement
Actively seek feedback from technicians and maintenance managers about their experience using the CMMS. Use their feedback to make improvements and address any choke points in CMMS usage. Gathering employee feedback shows them that their opinions and suggestions are valued by implementing changes based on their input.
6. Provide Adequate Resources and Support
Ensure that all technicians have access to the necessary hardware such as computers, tablets, or mobile devices, as well as a reliable internet connection to effectively use the CMMS. Employees should have easy access to technical support to promptly assist with any problems that may arise. Most CMMS platforms have a lot of online training and support resources through the provider’s knowledge center. Make sure that technicians are aware of the online resources, understand how to use them and are encouraged to use them when experiencing issues or want to learn more about the CMMS. Managers should work with the CMMS provider to demonstrate how to navigate the knowledge base and connect with their customer support. Refresher courses should be offered from time to time as well as additional training sessions when major changes or upgrades are made to the CMMS.
5 Out of the Box, Creative Ways to Motivate Technicians to Embrace a CMMS
The basics just outlined provide an excellent framework for successful user training and implementation of a CMMS within organizations that cross many industry sectors. While these are sound techniques, they may still not be enough to secure all employees’ buy-in and compliance to regular use of the CMMS during routine maintenance tasks. This is where adding a few creative elements to the onboarding process will be helpful.
Here are five creative ways to cut through resistance and effectively motivate maintenance employees to adopt your CMMS:
1. Customizable User Interfaces
It’s a given that whichever CMMS your company decides on, it should come with an intuitive and user-friendly interface. This means the system should be easy to navigate and not require any guesswork or hesitation on a technician’s part.
Beyond this, many CMMS dashboards can be customized. With this in mind, work with your maintenance team to customize dashboards and settings to suit their preferences and work styles. Afterall, some may prefer certain list views, layouts or even colors and dark or light mode if available. Encourage them to experiment by trying out different layouts and features to find what works best for them. The latter includes things like setting up alerts as well as selecting reporting features that suit their needs best. Having the freedom to personalize their dashboard, gives employees a sense of ownership and control over the system.
2. Gamification and Rewards
Games, and the rewards that follow are great ways to spark people’s interest and engage them in an activity. These same principles apply to the CMMS onboarding process. For example, during the initial phase of onboarding, create interactive training modules that include videos, simulations, and hands-on exercises. This first step makes learning fun. Next create a gamified system where employees can earn points or badges for using the CMMS regularly, completing tasks, or achieving certain milestones. Points or badges can then be exchanged for tiered rewards in the form of gift cards or added vacation days. By creating a friendly competition, technicians acquire proficiency using the CMMS as well as a willingness to do so.
3. Celebrate Onboarding Milestones
It is also important to celebrate specific milestones reached during the onboarding process. For example, this may involve receiving recognition for completing a certain module, achieving a specific competency level, or successfully using the CMMS for a designated period of time. By celebrating successes and highlighting how technicians’ contributions through CMMS adoption are positively impacting the organization results in boosting overall morale.
4. Showcase Success Stories
Consider creating a recognition program for outstanding CMMS utilization. To do this, track key performance indicators (KPIs) related to maintenance efficiency and share the positive results with the team. And be specific when sharing examples of technicians’ CMMS routine use and how it improved efficiency, reduced downtime, or saved costs. By highlighting success stories of employees or teams who have effectively integrated the CMMS into their workflow, it not only recognizes their achievements but also encourages others to follow their lead.
5. Highlight Career Growth Opportunities
Describing career growth potential associated with CMMS use is probably the most important factor in motivating reluctant technicians to buy-in. Recall earlier it was noted that employees’ fears of losing their jobs was a reason for their resistance to adopting a CMMS. By explaining how proficiency in CMMS usage can enhance their skill set and open up new career opportunities within the maintenance field, this is a sure way to dispel their concerns. In fact, not only is CMMS experience becoming a requirement for maintenance jobs, there are now many positions that are centered around CMMS experience; By adopting a CMMS, it not only helps their organization in improving efficiency in its operations, it also gives employees an important skill set that they can add to their resumes.
Conclusion
Implementing a CMMS can greatly benefit maintenance teams, but getting employees to adopt and embrace this technology can sometimes be a challenge. Many resistant employees perceive the CMMS as being too complex, too difficult or even a threat to their jobs. These factors pose obstacles that must be overcome.
In addition to utilizing the conventional CMMS onboarding practices, maintenance managers and leaders should try to apply some creative, out of the box approaches to motivate technicians to adopt the CMMS. To do so, keep the training dynamic, relevant, and engaging to achieve the best results. Offer incentives and rewards for CMMS proficiency and frequent use. By incorporating creative and fun processes into CMMS onboarding, employers can foster an environment where technicians feel empowered, confident and excited to use the system to its fullest potential.
That being said, it is equally important to balance creative approaches with effective communication, thorough hands-on training, and support throughout this process. By providing ongoing support and resources to technicians, they will feel confident and capable in using the system. Using these approaches will make it possible for a CMMS to perform as it is intended to by significantly improving an organization’s efficiency, reducing its downtime, and enhancing its overall maintenance operations.
TABLE OF CONTENTS
Keep Reading
Ever find yourself checking into a luxury hotel and expecting a relaxing stay, only to find a ...
11 Apr 2025
Organizations are witnessing swift changes in the business environment and confronting a ...
8 Apr 2025
Last month, news outlets and the entire internet was abuzz with the return of NASA astronauts ...
3 Apr 2025
What comes first - CMMS or predictive maintenance? If your answer is either, it is correct. ...
28 Mar 2025
Artificial intelligence (AI) talk has become commonplace. Today, engaging in business-focused ...
27 Mar 2025
Imagine a world where machines predict, diagnose, and fix their issues before they fail. This ...
25 Mar 2025
A facility maintenance plan is at the core of a facility’s operations. This organized ...
21 Mar 2025
Think of managing your maintenance operations like managing a championship sports team. Just ...
21 Mar 2025
The maintenance sector is battling a severe talent shortage that threatens to undermine ...
7 Mar 2025
Manufacturing maintenance is the backbone of industrial efficiency, ensuring machines run ...
5 Mar 2025
No one likes playing a guessing game when equipment breaks down. Yet, maintenance teams often ...
4 Mar 2025
The size of the preventive maintenance software market is discussed in millions of dollars, ...
4 Mar 2025
The organizational structure and corporate hierarchy vary from company to company. Large ...
28 Feb 2025
Maintenance procedures are essential for ensuring the longevity and reliability of machinery ...
21 Feb 2025
Sustainability is no longer just a buzzword; it's a critical component of corporate social ...
20 Feb 2025
A Computerized Maintenance Management System (CMMS) relies on accurate, well-organized data ...
18 Feb 2025
In an era where technology drives operational efficiency, Computerized Maintenance Management ...
14 Feb 2025
A Computerized Maintenance Management System (CMMS) is a key component of modern maintenance ...
13 Feb 2025
Introduction Maintenance management is the foundation of maintenance operations in industries ...
11 Feb 2025
Introduction A Computerized Maintenance Management System (CMMS) is software designed to help ...
7 Feb 2025