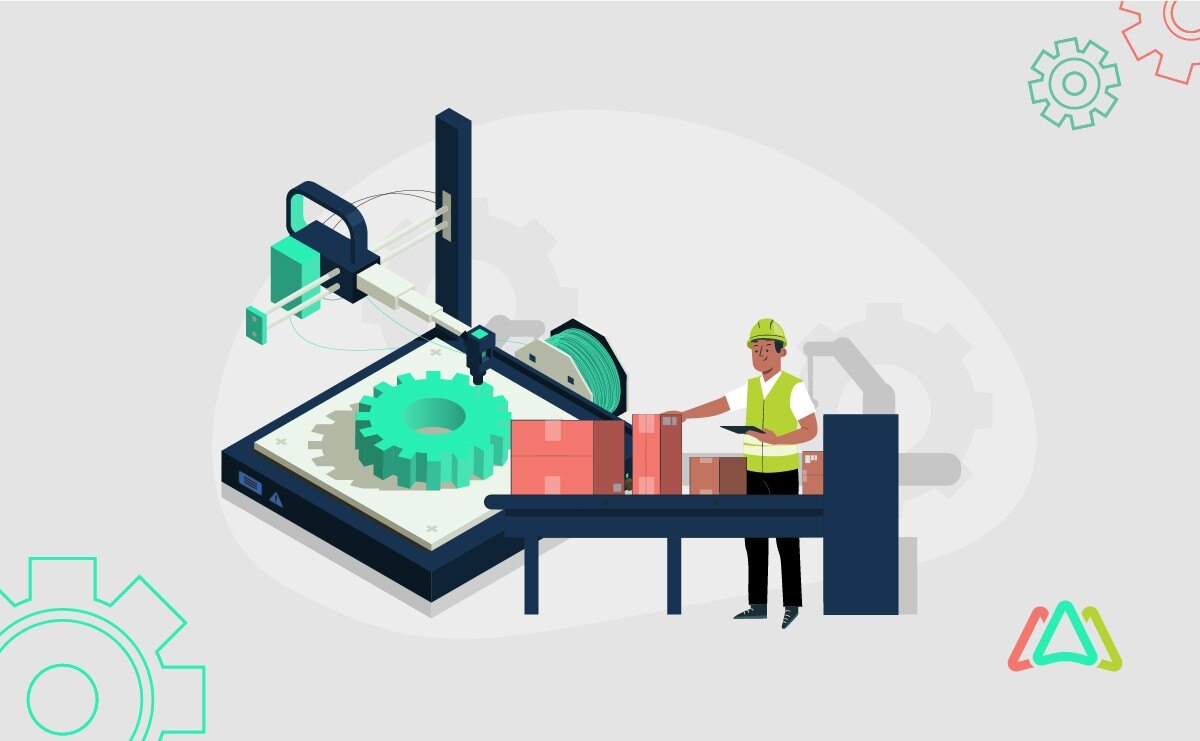
The Impact of Additive Manufacturing on Supply Chain Optimization
Additive manufacturing (AM) or 3D printing is having a huge impact on manufacturing businesses. This transformative technology is reshaping supply chains across industries, offering unprecedented flexibility and efficiency. By enabling on-demand production and localized manufacturing, additive manufacturing is disrupting traditional supply chain models.
This article explores how this innovative approach is optimizing supply chains, reducing lead times, and minimizing inventory costs. The article covers key statistics and real-world examples that demonstrate the tangible benefits of integrating additive manufacturing into organizations’ supply chain strategies.
Introduction to Additive Manufacturing
Additive manufacturing (AM), also known as 3D printing, is revolutionizing the way products are designed, produced, and distributed. This innovative technology builds objects layer by layer, using digital 3D models as blueprints. Unlike traditional manufacturing methods, AM allows for the creation of complex designs with minimal waste, offering unprecedented flexibility and customization options.
Key Benefits of Additive Manufacturing
AM technology brings several advantages to the manufacturing process:
Reduced waste:
AM significantly curbs waste production, using only the material necessary for each output.
Customization:
It enables on-demand production of tailored products, meeting specific customer needs.
Lightweight structures:
AM facilitates the creation of lighter components, which is particularly beneficial in industries like aerospace.
Impact on Supply Chains
The integration of AM into production processes is transforming traditional supply chains:
Simplified logistics:
AM reduces the need for extensive warehousing and complex transportation networks, streamlining the supply chain.
Decentralized production:
Companies can set up distributed manufacturing facilities, reducing lead times and transportation costs.
Inventory optimization:
AM eliminates the need for large inventories of semi-finished products, aligning with lean manufacturing principles.
As AM technology continues to advance, its impact on supply chain optimization is expected to grow, reshaping manufacturing strategies and business models across industries.
Benefits of Additive Manufacturing for Supply Chain Optimization
Streamlined Production and Reduced Costs
Additive manufacturing (AM) offers significant advantages for supply chain optimization. By simplifying the traditional supply chain, AM reduces costs related to transport and warehousing. This technology enables on-demand production, eliminating the need for extensive inventories and simplifying logistics requirements for specialized applications.
Enhanced Flexibility and Customization
AM allows for rapid customization and modification of objects, using only the necessary materials for each output. This flexibility enables companies to eliminate steps in the assembly phase, save on short production runs, and create customized products. The technology also facilitates the production of lighter structures, which can significantly reduce fuel consumption in industries like aviation.
Improved Sustainability and Efficiency
Implementing AM technologies reduces waste production, positively impacting environmental sustainability. Many materials used in AM are recyclable, with an estimated 95% to 98% of metal powder being reusable. Additionally, AM enables the consolidation of multiple components into a single part, simplifying assembly and reducing points of failure.
Advantages of Additive Manufacturing for Supply Chain Optimization
Reduced Lead Times
One of the most significant impacts of AM on supply chains is the reduction in lead times. Traditional manufacturing requires complex processes, with raw materials needing to be sourced, parts shipped across continents, and intricate assembly lines. Additive manufacturing eliminates many of these steps by enabling on-demand production.
Example:
In the aerospace industry, Finnair upgrades its Airbus A320 fleet with new 3D printed components, reducing production times and achieving lead timings savings of up to 75%. With localized manufacturing hubs, companies can also respond more rapidly to customer demand.
Streamlined Inventory Management
AM minimizes the need to maintain large inventories of spare parts, as products can be printed on demand. This shift from a "make-to-stock" to a "make-to-order" model is especially beneficial for industries with complex, high-value components. As a result, companies can reduce the capital tied up in excess inventory and lower storage costs, streamlining supply chain operations. Companies can produce items as needed, reducing storage costs and minimizing obsolescence risks.
According to a recent Massachusetts Institute of Technology (MIT) report, additive manufacturing can reduce spare parts inventory by 90% in the car industry.
Example:
General Electric (GE) uses 3D printing for its aviation division, producing spare parts for jet engines when needed, reducing both warehousing and logistics costs.
Enhanced Customization and Flexibility
AM offers unparalleled flexibility in product design and customization. It allows for increased geometric complexity without higher costs, enabling businesses to adapt to changing market demands quickly. This agility is crucial in today's fast-paced business environment. This flexibility is invaluable in industries such as healthcare, automotive, and consumer goods, where tailored solutions are often required.
Example:
Ford uses 3D printing to create custom jigs and tools for its assembly lines. This reduces production setup times and enables the company to produce parts specifically tailored to individual models and customer preferences.
Sustainable and Resilient Supply Chains
AM contributes to more sustainable practices by reducing waste and lowering the carbon footprint associated with traditional manufacturing. It also enhances supply chain resilience by enabling decentralized production. Distributing manufacturing across multiple facilities helps mitigate risks associated with disruptions at a single location, ensuring continuity of supply.
According to LuxCreo, additive manufacturing could reduce material waste by up to 90%, significantly lowering the environmental footprint of manufacturing processes.
Example:
During the COVID-19 pandemic, companies used AM to quickly produce critical medical supplies, including PPE, facial shields, and valves for respiratory machines, overcoming the supply chain disruptions caused by global shutdowns.
Optimized Component Design
AM's design freedom allows for lightweight and functional integration of parts. This can significantly reduce material costs, simplify assembly processes, and lower transportation expenses.
Example:
According to Science Direct, additive manufacturing (AM) for aerospace components offers several benefits, including reduced lead times and costs, the ability to design and produce complex geometries for lightweight structures, consolidation of multiple parts, and enhanced performance. These advantages help meet budget and timeline constraints, leading to better management of both programmatic and technical risks.
Use Cases and Examples of Additive Manufacturing Improving Supply Chains
Streamlining Production and Inventory
Additive manufacturing (AM) is revolutionizing supply chains by enabling on-demand, localized production. This technology allows companies to produce parts at or near the point of need, significantly reducing transportation costs and lead times. By maintaining digital inventories, businesses can produce spare parts as needed, minimizing obsolete stock and saving physical storage space.
Industry-Specific Applications
In the aviation sector, AM enables manufacturers to produce standard parts using traditional methods while simultaneously creating low-demand components, effectively reducing inventory levels. The aerospace industry has seen significant benefits, with AM-optimized designs making parts 35% to 65% more lightweight, streamlining the supply chain, and improving fuel efficiency.
Customization and Rapid Response
AM technology allows for almost instant customization and modification of objects, using only the necessary materials for each output. This capability enables mass customization and enhances perceived value for consumers. During the COVID-19 pandemic, AM demonstrated its agility by rapidly producing millions of medical components, including ventilator parts and personal protective equipment, showcasing its potential to address urgent supply chain challenges.
Challenges and Limitations of Additive Manufacturing Adoption
Material and Quality Control Issues
While additive manufacturing (AM) offers significant benefits for supply chain optimization, it faces several hurdles in widespread adoption. One primary challenge is the limited range of materials suitable for AM processes. Not all metals and plastics can be effectively temperature-controlled for 3D printing, restricting the versatility of AM applications. Additionally, maintaining consistent quality, especially in large-scale production, remains a significant concern. Factors such as layer adhesion and structural integrity require careful monitoring to ensure product reliability.
Cost and Knowledge Barriers
The high price of AM machinery presents a substantial barrier to entry for many businesses. This initial investment can be prohibitive, particularly for smaller companies or those in developing countries. Furthermore, there's a notable lack of documented studies on AM adoption in certain industries and regions, creating knowledge gaps that hinder effective implementation. The shortage of skilled professionals proficient in AM technology further compounds these challenges.
Regulatory and Intellectual Property Concerns
As AM becomes more accessible, concerns about intellectual property theft and counterfeiting are growing. The ease of replicating designs digitally raises questions about protecting proprietary information. Moreover, strict regulatory requirements, especially in sectors like medical devices and aerospace, pose additional hurdles for AM adoption. Navigating these complex regulatory landscapes while ensuring compliance can be time-consuming and resource-intensive for businesses looking to integrate AM into their supply chains.
The Future of Additive Manufacturing and Its Impact on Supply Chains
Revolutionizing Production and Distribution
As Industry 4.0 continues to transform manufacturing, additive manufacturing (AM) stands at the forefront of innovation. According to Deloitte's survey of US manufacturing executives, continuous investment in digital technologies is driving operational efficiency and supply chain resilience. AM, or 3D printing, is poised to revolutionize production processes and distribution models, offering unprecedented flexibility and customization capabilities.
Enhanced Supply Chain Agility
The integration of AM with other Industry 4.0 technologies like IoT and Al is set to improve supply chain responsiveness dramatically. By leveraging advanced analytics and visualization, manufacturers can anticipate and mitigate disruptions more effectively. This synergy enables on-demand production, reducing inventory costs and accelerating product development cycles.
Challenges and Opportunities
While AM presents immense potential, it also brings challenges. Cybersecurity concerns and the need for workforce upskilling are critical considerations. However, the opportunities for mass customization, reduced waste, and localized production far outweigh these hurdles. As AM technology matures, we expect to see a shift towards more distributed, agile supply chains that can rapidly adapt to changing market demands and global uncertainties.
Conclusion
As businesses consider the transformative potential of additive manufacturing for their supply chain, they must be mindful that this technology is not just a futuristic concept but a present reality reshaping industries. By embracing 3D printing, businesses can achieve greater flexibility, reduced costs, and enhanced sustainability in their operations. The statistics and examples presented underscore the significant impact AM can have on supply chain optimization. To stay competitive, businesses should explore ways additive manufacturing can benefit their specific operations.
TABLE OF CONTENTS
Keep Reading
Your company recently invested funds and time for new CMMS software, and six months later, it ...
1 Jul 2025
As Computerized Maintenance Management Systems (CMMS) become more connected and cloud-based, ...
1 Jul 2025
Edge computing is an innovative technology that enables data to be processed at the source, ...
24 Jun 2025
Facility management has undergone a significant transformation in recent times. Take, for ...
20 Jun 2025
A facility maintenance plan is at the core of a facility’s operations. This organized ...
19 Jun 2025
In the early days, preventive maintenance could be done effectively with a trained eye and a ...
17 Jun 2025
Sticky notes fall off, whiteboard grids get wiped, and spreadsheets never beep when a ...
13 Jun 2025
Handing a slice of your maintenance workload to a contractor is less about “giving up ...
12 Jun 2025
Downtime in enterprise environments doesn’t just mean a stop in operations; it means lost ...
10 Jun 2025
Understanding equipment functionality is crucial for effective repairs. A clear, systematic ...
6 Jun 2025
Maintenance managers know that every unplanned equipment failure is more than a simple ...
5 Jun 2025
What keeps a facility running smoothly? Initially, many of us may zoom in on its equipment, ...
29 May 2025
In today's digital world, every decision needs to pass the test of strategic and operational ...
27 May 2025
The business world is very different from a decade ago. Technological advancements have grown ...
23 May 2025
Picture this: a maintenance technician inspects a complex pump system. Instead of typing a ...
20 May 2025
For most of the 20th century, maintenance teams mainly applied a reactive approach to ...
9 May 2025
Imagine visiting a manufacturing plant where maintenance technicians gather around a large ...
8 May 2025
Maintenance management faces complexities across all industries, escalating with ...
6 May 2025
Ever find yourself checking into a luxury hotel and expecting a relaxing stay, only to find a ...
11 Apr 2025
Organizations are witnessing swift changes in the business environment and confronting a ...
8 Apr 2025