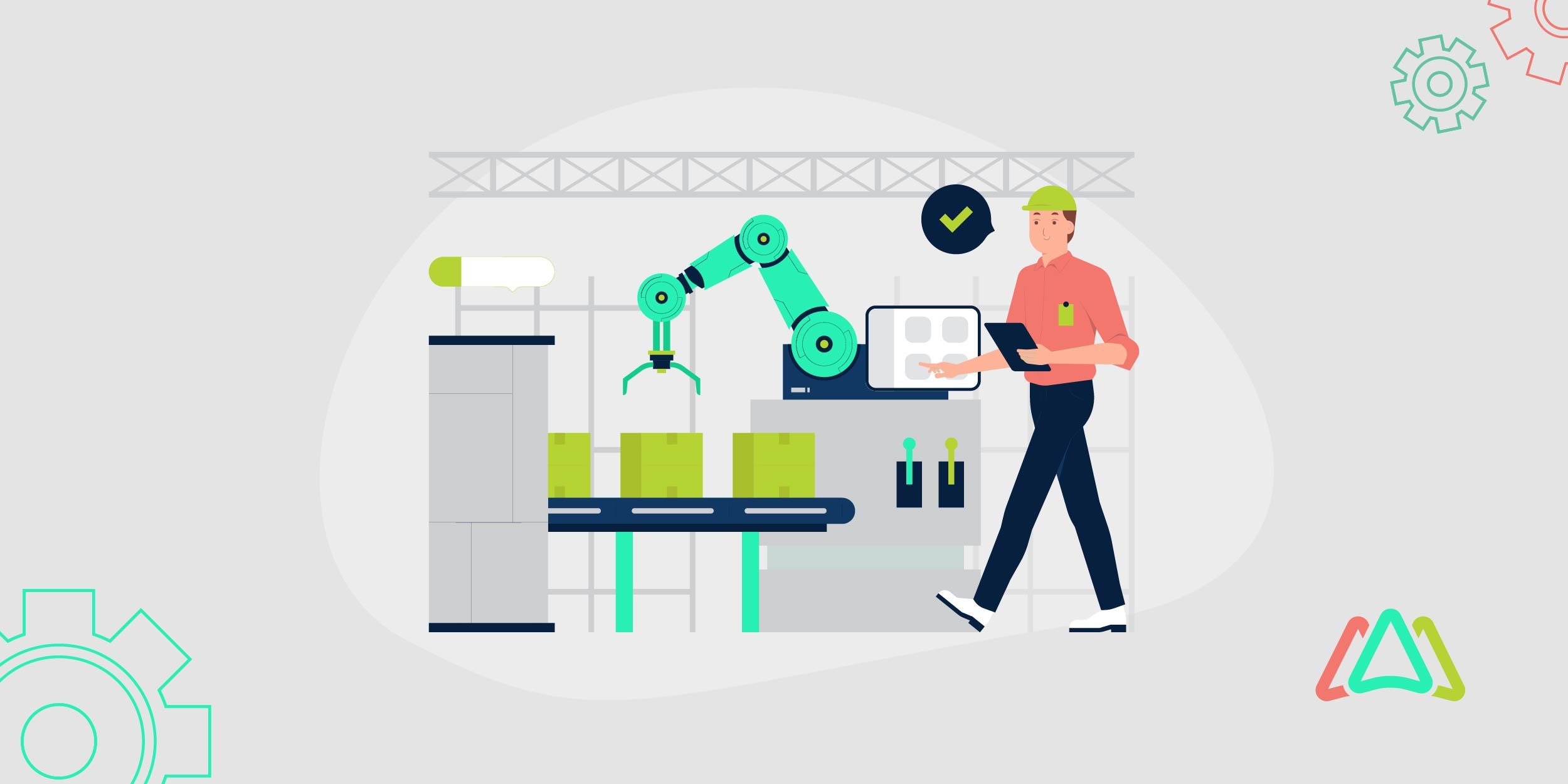
Agile Maintenance 101: A Proactive Approach to Asset Management
Organizations are witnessing swift changes in the business environment and confronting a range of challenges that significantly affect their operational effectiveness and efficiency. Global pandemics, changing demand, and unstable oil prices are significant disruptions that force companies to find more responsive asset management strategies. Modern operations are becoming too complex for traditional asset management practices. As such, there is now an acute need to move toward agile maintenance frameworks capable of rapid, informed responses to dynamic operating conditions and asset health.
This article delves into the core principles of agile maintenance, exploring how a proactive asset management strategy can lead to improved efficiency, reduced costs, and enhanced reliability. This article emphasizes the importance of agile decision-making and integrated systems for the success of organizations in unpredictable times.
What is Agile Maintenance?
Just as modern cars use smart sensors to detect issues before they become serious, Agile Maintenance is about staying proactive. It relies on continuous monitoring to track real-time equipment health, responsiveness to make quick, data-driven adjustments, and collaboration between maintenance teams, operators, and IT to prevent breakdowns before they happen.
In simpler terms, agile maintenance means having the ability to be flexible and respond to production demands and equipment wear or react to external disruption, be it supply chain or technical. It maximizes the performance and longevity of machines. With changing times, conventional maintenance techniques are proving less effective, and the emphasis has moved to smarter & responsive systems.
The Core Principles of Agile Maintenance
Agile maintenance is based on a few key ideas that help keep machines running smoothly while reducing unnecessary labor and time, as well as reducing costs.
Efficiency & Speed
With agile maintenance, failures and changes in asset conditions are handled quickly to help reduce downtime and improve productivity. It helps teams identify problems early, respond quickly, and plan maintenance effectively, reducing interference with operations.
Iterative Improvement
Sensors do real-time data collection and alert teams before the issue occurs instead of waiting for a failure. This allows for faster decision-making.
Flexibility
Instead of being on a fixed maintenance schedule, maintenance teams adjust what they do for the machine based on machine conditions. Agile maintenance does not adhere to a strict maintenance schedule, and maintenance interventions are performed only when needed.
Collaboration
Execution thrives on teamwork in Agile Maintenance. Maintenance teams, IT specialists, and machine operators join forces, relying on their individual skill sets to prevent problems, resolve issues, and maximize the machine’s performance. Maintenance teams are empowered to make quicker and smarter decisions, minimizing downtime and ensuring efficiencies by sharing data and insights in real time.
Data-Driven Decision Making
Data-driven decisions underpin the agile maintenance approach. To streamline this process, AI and IoT look at performance trends to predict and solve issues before they arise.
Advantages of Agile Maintenance
“A stitch in time saves nine.” The sooner you fix small issues, the less likely they are to turn into costly problems. Here are some of the key benefits of Agile Maintenance:
Lower Maintenance Costs
Traditional preventive maintenance involves performing unnecessary preventive tasks and inspections, consuming valuable resources. With an agile maintenance approach, companies do maintenance only when required. This avoids using additional labor and incurring extra costs for spare parts when not needed.
Increased Equipment Lifespan
Just like regular oil changes help a car last longer, Agile maintenance prevents excessive wear and tear on industrial machinery. By continuously monitoring equipment health and addressing minor issues before they escalate, companies extend the lifespan of critical assets, reducing the need for costly replacements of parts or the whole machine. Fixed scheduled maintenance often results in performing tasks that are not necessary (over maintenance) but also runs the risk of missing corrective maintenance when needed, which can result in costly failures and longer downtime.
Enhanced Predictive Maintenance
IoT sensors, AI, and machine learning are used in agile maintenance to detect failures ahead of time. Rather than reacting to breakdowns, companies get advance warnings about asset performance degradation. This enables service technicians to make repairs as needed and before a more serious and expensive breakdown happens. This minimizes emergency repairs, prevents production interruptions, and maximizes operational efficiency by keeping machines in optimal condition.
Increased Productivity
Fewer chronic breakdowns and streamlined maintenance schedules equate to more staff time spent producing instead of troubleshooting broken-down equipment. Forecasting upkeep has resulted in better availability of the machine in the oil & gas, DNA, and energy sectors and has induced a substantial rise in the return on investment (ROI). This results in businesses receiving greater output from their equipment while incurring lower spending on repairs and downtime.
These advantages have allowed many companies to function more effectively, eliminate wasteful spending, and, most importantly, increase overall asset dependability.
Agile vs. Traditional Maintenance
The old saying is, ‘Fix the roof while the sun is shining.’ Traditional maintenance in the usual sense waits for it to rain, while with agile maintenance, teams are aware that a storm is coming and strengthen the roof so that it does not leak.
Traditional maintenance methods are working on a precisely scheduled basis, maintaining equipment regardless of the need, or taking action once failure has occurred. Either way, the result is inefficiency, wasting resources and/or time through performing unnecessary maintenance tasks or dealing with unexpected service outages that could have been avoided.
Agile maintenance, by contrast, adjusts in real time to actual conditions and employs smart technology like AI and sensors to anticipate issues before they arise. This leads to quicker response times, decreased breakdowns, and reduced costs. Conventional maintenance wastes money by either carrying out unnecessary work or waiting too long to correct a problem.
How to Implement Agile Maintenance
To transition from traditional maintenance to agile, follow the steps below.
Step 1: Build an Agile Maintenance Team
Maintenance is not an isolated undertaking and should not be treated as such. Maintenance engineers, IT specialists, and operators should work together as a team. When these roles work together, decision-making accelerates, and issues are tackled at the moment rather than passed from person to person. It’s a little bit like having a well-coordinated soccer team as opposed to a bunch of players running off in different directions.
Step 2: Leverage Technology
Technology is the backbone of agile maintenance. Without it, there will be problems. A computerized maintenance management system (CMMS) can track assets, IoT sensors can monitor equipment performance in real time, and AI-powered predictive analytics can detect failures before they happen.
Step 3: Implement Agile Maintenance Workflows
Instead of handling maintenance as one big single task, break it down into smaller, manageable actions. The goal is to prioritize tasks based on how critical they are instead of blindly following a fixed schedule.
Step 4: Establish a Feedback Loop
Agile maintenance is not a “set it and forget it” approach. Ensure there is continuous monitoring and improvement. By analyzing failure trends and adjusting strategies accordingly, maintenance teams can stay proactive instead of reactive.
By following these steps, an organization can transition from outdated maintenance methods to a smarter, more efficient approach. As the saying goes, “Work smarter, not harder,” and agile maintenance is the perfect example of that.
Common Challenges and How to Overcome Them
Transitioning to Agile Maintenance (AM) can significantly improve efficiency, but like any major shift, it comes with obstacles. Here’s how to tackle them effectively:
Resistance to Change
Naturally, people find it difficult to adopt a new way of doing things, especially when they’re used to traditional maintenance methods. The key to overcoming this challenge is proper education—“show, not tell.” Show the team how agile maintenance makes their jobs easier, safer, and faster. Leadership should also actively support the transition by encouraging collaboration and celebrating small successes to reinforce their commitment to change.
High Initial Cost
Investing in IoT sensors, AI-driven data, and new training programs can be expensive, especially in the beginning. To reduce financial risks, start small with a pilot project and conduct a few tests on some critical assets before scaling up.
Data Overload
The maintenance team may feel overwhelmed by the huge amount of unnecessary machine data collected by the sensor system. The solution here is to use AI-driven analytics to filter out the unneeded data and highlight and find patterns in the most relevant information. This saves time and energy so the team can focus on what’s important.
Skills Gap
Not all maintenance teams are trained on the new level of predictive maintenance or IoT technology. Organizations should invest in employee training that provides adequate knowledge on how to use these technologies. Encouraging cross-functional collaboration between IT, engineers, and operations can also help bridge the gap.
By addressing these challenges early, companies can fully leverage agile maintenance for better efficiency and lower costs.
Conclusion
The landscape of maintenance is undergoing a significant transformation, becoming smarter, faster, and increasingly automated. This shift is not merely a trend, but a substantial evolution backed by data. According to Fortune Business Insights, the global predictive maintenance market, valued at $10.93 billion in 2024, is on a trajectory of rapid growth. It is projected to reach $13.65 billion in 2025 and soar to an impressive $70.73 billion by 2032. These figures underscore the accelerating adoption and the immense potential of predictive maintenance within the broader maintenance landscape.
This rapid growth and projected expansion highlight the urgency for organizations to transition to agile maintenance strategies. The benefits of embracing this shift are multifaceted and substantial. Agile maintenance, with its proactive and data-driven approach, enables organizations to significantly reduce costs. By predicting and preventing equipment failures, organizations can avoid costly downtime, repairs, and replacements. Moreover, agile maintenance enhances the reliability and availability of assets, leading to improved operational efficiency and productivity. By minimizing unplanned outages and disruptions, organizations can ensure smoother operations and better meet customer demands.
In addition to cost savings and improved reliability, agile maintenance also contributes to a reduction in operational headaches. By proactively addressing maintenance needs, organizations can avoid the stress and challenges associated with reactive maintenance, such as emergency repairs and equipment failures. Agile maintenance provides organizations with greater control and predictability, enabling them to plan and execute maintenance activities in a more efficient and effective manner.
The time for organizations to embrace agile maintenance is now. The benefits are clear, and the consequences of inaction are significant. Organizations that fail to adapt to this evolving landscape risk falling behind their competitors, incurring higher costs, and experiencing operational inefficiencies. The transition to agile maintenance may require an initial investment in technology, training, and process changes. However, the long-term benefits far outweigh the initial costs. By embracing agile maintenance, organizations can position themselves for success in the digital age, ensuring their assets are well-maintained, their operations are efficient, and their bottom line is healthy. The future of maintenance is agile, and organizations that recognize this and take action will reap the rewards for years to come in the future.
TABLE OF CONTENTS
Keep Reading
Ever find yourself checking into a luxury hotel and expecting a relaxing stay, only to find a ...
11 Apr 2025
Last month, news outlets and the entire internet was abuzz with the return of NASA astronauts ...
3 Apr 2025
What comes first - CMMS or predictive maintenance? If your answer is either, it is correct. ...
28 Mar 2025
Artificial intelligence (AI) talk has become commonplace. Today, engaging in business-focused ...
27 Mar 2025
Imagine a world where machines predict, diagnose, and fix their issues before they fail. This ...
25 Mar 2025
A facility maintenance plan is at the core of a facility’s operations. This organized ...
21 Mar 2025
Think of managing your maintenance operations like managing a championship sports team. Just ...
21 Mar 2025
The maintenance sector is battling a severe talent shortage that threatens to undermine ...
7 Mar 2025
Manufacturing maintenance is the backbone of industrial efficiency, ensuring machines run ...
5 Mar 2025
No one likes playing a guessing game when equipment breaks down. Yet, maintenance teams often ...
4 Mar 2025
The size of the preventive maintenance software market is discussed in millions of dollars, ...
4 Mar 2025
The organizational structure and corporate hierarchy vary from company to company. Large ...
28 Feb 2025
Maintenance procedures are essential for ensuring the longevity and reliability of machinery ...
21 Feb 2025
Sustainability is no longer just a buzzword; it's a critical component of corporate social ...
20 Feb 2025
A Computerized Maintenance Management System (CMMS) relies on accurate, well-organized data ...
18 Feb 2025
In an era where technology drives operational efficiency, Computerized Maintenance Management ...
14 Feb 2025
A Computerized Maintenance Management System (CMMS) is a key component of modern maintenance ...
13 Feb 2025
Introduction Maintenance management is the foundation of maintenance operations in industries ...
11 Feb 2025
Introduction A Computerized Maintenance Management System (CMMS) is software designed to help ...
7 Feb 2025
Introduction Due to a growing awareness of the need to combat climate change, the green ...
6 Feb 2025