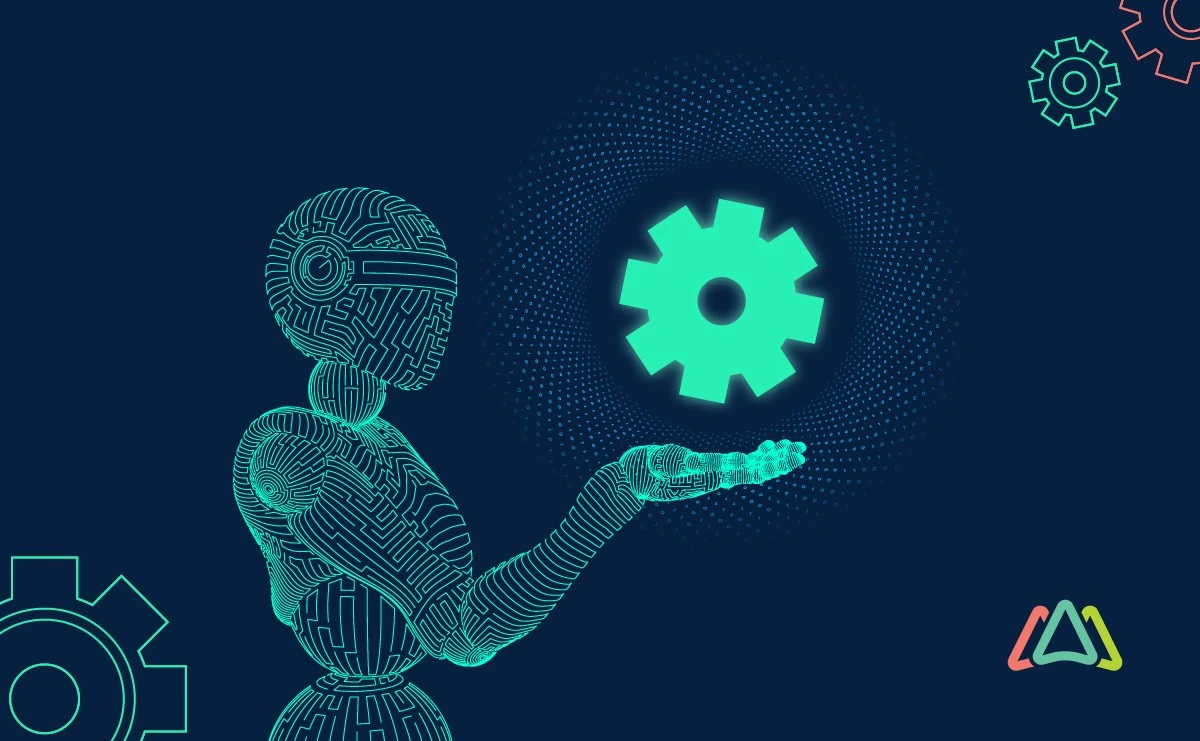
AI Powered CMMS Solutions: Driving Efficiency with Precision
In today's technologically advanced world, businesses are increasingly using Artificial Intelligence (AI) to enhance their maintenance operations through CMMS solutions. The convergence of AI and CMMS creates a dynamic synergy that revolutionizes the way businesses operate.
According to an article by Gartner, 70% of captured manufacturing data remains unused due to a number of complexities. Having unused data leaves a CMMS system underutilized and unable to reach its full operating potential.
AI brings advanced capabilities to CMMS software, enabling businesses to understand vast amounts of maintenance data and derive data-driven insights from it.
By analyzing the extensive data collected by CMMS systems, AI algorithms can identify patterns, predict equipment failures, and optimize maintenance schedules. This predictive maintenance approach helps businesses shift from reactive to proactive strategies, reducing unexpected breakdowns and maximizing equipment uptime. This alone offers huge cost saving.
Before the advent of AI, CMMS solutions relied on traditional approaches for maintenance management. In this context, it is important to understand them and the constraints they imposed on businesses.
Pre-AI CMMS: Traditional Approaches and Limitations
Reactive Maintenance
Pre-AI CMMS solutions primarily supported reactive maintenance practices, where maintenance activities were triggered by equipment failures or breakdowns. This approach often resulted in unplanned downtime, increased costs, and a lack of control over maintenance schedules.
Manual Processes
Maintenance operations were often managed manually, using paper-based systems or rudimentary digital tools. This manual approach led to inefficiencies, data inaccuracies, and a lack of real-time visibility into maintenance activities, hindering effective tracking and analysis.
Limited Predictive Maintenance Capabilities
Pre-AI CMMS solutions lacked advanced predictive capabilities. Without AI-powered analytics, businesses struggled to detect potential equipment failures or maintenance needs in advance. This limitation prevented them from adopting proactive maintenance strategies, resulting in suboptimal asset performance and increased maintenance costs.
Inventory Management Challenges
Traditional CMMS systems had difficulty accurately forecasting spare parts requirements, leading to issues such as stock outages or overstocking. This impacted maintenance efficiency and increased costs due to delayed repairs or excess inventory carrying costs.
Reporting and Analytics Limitations
Previously, generating comprehensive reports and extracting actionable insights from maintenance data required manual effort and time-consuming processes. This hindered effective decision-making, performance evaluation, and limited opportunities for continuous improvement.
While these traditional approaches served businesses to a certain extent, they had limitations in terms of efficiency, cost-effectiveness, and proactive maintenance strategies.
A study by Boeing suggests that despite calendar-based maintenance, 85% of equipment fails, and one-third of all maintenance investments are wasted through ineffective maintenance management strategies and methods.
The integration of AI into CMMS is essential to enable predictive maintenance, automation, optimized inventory management, and advanced analytics. AI-powered CMMS solutions empower businesses to adopt proactive strategies, optimize asset performance, reduce costs, and achieve operational excellence.
The Integration of AI and IoT with CMMS Solutions
The integration of Artificial Intelligence (AI) and Internet of Things (IoT) with CMMS solutions marks a significant advancement in maintenance management, making it possible for businesses to embrace proactive strategies and optimize their maintenance practices.
This association emerged due to technological advancements and the need for more advanced and efficient maintenance management practices. The integration of AI and IoT with CMMS was driven by factors such as:
Technological Advancements
The rapid development of AI and IoT technologies provided opportunities for enhancing maintenance management. AI offered advanced analytics and predictive capabilities, while IoT enabled real-time data collection from connected devices and sensors. This created the foundation for integrating AI and IoT with CMMS.
Data Availability and Connectivity
The availability of IoT devices and sensors allowed businesses to collect massive amounts of data from equipment and assets. Real-time data and increased connectivity facilitated the integration of IoT devices with CMMS systems, enabling data-driven decision-making, predictive maintenance, and remote monitoring.
Demand for Proactive Maintenance
As noted, traditional maintenance practices were reactive, leading to unplanned downtime and inefficient resource allocation. AI and IoT present an opportunity to shift to proactive maintenance strategies. AI algorithms and IoT-enabled sensors enable businesses to predict equipment failures, monitor asset conditions, and take proactive maintenance actions.
Optimization and Efficiency Goals
Organizations were challenged to find ways of optimizing asset performance, reducing maintenance costs, and enhancing operational efficiency. AI and IoT provides capabilities to leverage real-time data, predictive analytics, and automation that aligns with these optimization goals. Integrating AI and IoT with CMMS makes it possible to improve maintenance processes, resource utilization, and decision-making.
Industry 4.0 and Digital Transformation
The Industry 4.0 movement and digital transformation initiatives encouraged businesses to adopt new technologies for improved efficiency and competitiveness. AI and IoT were integral to the Industry 4.0 vision, and CMMS systems played a crucial role in enabling the integration of these technologies within maintenance management.
The powerful combination of AI and IoT integration is reshaping how businesses utilize CMMS software. Let's explore the five impactful ways AI and IoT are transforming the use of CMMS software in businesses.
5 Ways AI is Impacting the way Businesses use CMMS Software
The integration of AI and IoT with CMMS is revolutionizing the way businesses use CMMS software for maintenance management. This transformative combination brings about significant changes in efficiency, cost savings, and decision-making capabilities. Here's a closer look at how the integration of AI and IoT with CMMS is impacting businesses:
Predictive Maintenance
AI algorithms utilize real-time data from IoT sensors to predict equipment failures or maintenance needs before they occur. This proactive approach allows businesses to schedule maintenance activities, optimize resource allocation, and minimize costly downtime. Predictive maintenance leads to increased equipment reliability, improving operational efficiency and customer satisfaction.
Condition Monitoring and Real-time Insights
IoT sensors continuously collect data on equipment performance, which is instantly fed into the CMMS system. AI algorithms analyze this data, identifying patterns and anomalies, providing maintenance teams with real-time insights for informed decision-making and proactive maintenance actions.
Remote Monitoring and Control
IoT-enabled CMMS solutions enable businesses to remotely monitor equipment performance and control operations. Real-time data transmission from IoT devices allows maintenance teams to track asset health, detect abnormalities, and remotely diagnose issues, thus improving response times and resource allocation.
Enhanced Resource Management
AI-powered CMMS software optimizes resource allocation by considering factors such as skills, availability, and workload. By analyzing data from IoT devices, historical records, and maintenance schedules, businesses can streamline work order management and ensure efficient utilization of resources.
Data-driven Decision-making
The integration of AI and IoT with CMMS provides businesses with access to vast amounts of data for analysis and decision-making. AI algorithms process and analyze maintenance data, uncovering patterns, trends, and insights. This enables businesses to make data-driven decisions, identify optimization opportunities, and track key performance indicators for continuous improvement.
Furthermore, by leveraging AI and IoT with CMMS, organizations can not only optimize their maintenance processes but also monitor energy consumption in real-time. This integration enables businesses to drive energy optimization, reduce environmental impact, and embrace sustainable practices while reaping the benefits of advanced technologies.
Towards a Sustainable Tomorrow - Integrating AI and IoT with CMMS for Energy Optimization and Environmental Stewardship
As the world grapples with the challenges of climate change and the urgent need for sustainable practices, businesses are increasingly turning to advanced technologies to enhance energy management and promote sustainability. One such powerful combination is the integration of AI and IoT with CMMS Software. This integration holds immense potential for businesses seeking to optimize energy consumption, reduce environmental impact, and achieve their sustainability goals. The following is a closer look at how the integration of AI and IoT with CMMS software is empowering energy management and sustainability efforts:
Real-time Energy Monitoring
IoT sensors deployed throughout facilities gather real-time data on energy usage, capturing information such as electricity consumption, temperature, and environmental conditions. These data are seamlessly integrated into the CMMS software, enabling businesses to monitor energy consumption patterns, identify inefficiencies, and make data-driven decisions to optimize energy usage.
Predictive Energy Analytics
By utilizing AI algorithms, businesses are able to analyze historical and real-time data from IoT sensors to predict future energy consumption patterns. This makes it possible to utilize proactive energy management strategies, such as load balancing, peak demand management, and energy demand forecasting. Predictive energy analytics empowers organizations to take preemptive measures to reduce energy waste, optimize energy distribution, and drive significant cost savings.
Equipment Performance Optimization
The integration of AI and IoT with CMMS software allows for comprehensive monitoring of equipment performance. IoT sensors collect data on parameters such as energy usage, operational efficiency, and maintenance needs. AI algorithms analyze these data to identify anomalies, deviations, or signs of equipment degradation. This enables businesses to proactively address maintenance requirements, optimize equipment performance, and minimize energy-intensive breakdowns.
Smart Energy Controls and Automation
Real-time data from IoT sensors can trigger automated responses, such as adjusting temperature settings, turning off unnecessary lighting, or optimizing energy-intensive processes. Smart energy controls and automation ensure energy-efficient operations and minimize human intervention.
Sustainability Reporting and Compliance
With accurate and real-time energy data at their fingertips, businesses can generate comprehensive reports on energy consumption, greenhouse gas emissions, and sustainability metrics. This helps organizations to track progress, identify areas for improvement, and meet regulatory requirements more efficiently.
The success of any AI-powered CMMS system hinges on the quality of the data it receives. These data inputs enable the system to generate precise outcomes and empower organizations to make informed maintenance decisions.
AI-powered CMMS systems are only as good as the Data fed into them!
To unleash the full power of an AI-powered CMMS system, businesses need to undergo a digital transformation. The effectiveness of an AI-powered CMMS depends on the quality and completeness of the data it processes. By ensuring high-quality data from sources like IoT sensors, equipment logs, and historical records, organizations are able to make reliable and well-informed maintenance decisions.
Organizations need to engage subject matter experts and data scientists in identifying and curating the right data sets for training and fine-tuning the CMMS. Digitizing institutional knowledge and building a comprehensive database is the first essential step towards harnessing the full potential of the AI-powered CMMS.
An International Society of Automation (ISA) article reports that manufacturers lose $647 billion to downtime on a global basis across all industry sectors.
The integration of AI and IoT with CMMS software presents a transformative opportunity for businesses to reduce losses attributed to downtime and achieve sustainability objectives. Embracing this powerful integration paves the way for a future where businesses can thrive while making significant contributions towards energy efficiency and environmental stewardship.
TABLE OF CONTENTS
Keep Reading
Ever find yourself checking into a luxury hotel and expecting a relaxing stay, only to find a ...
11 Apr 2025
Organizations are witnessing swift changes in the business environment and confronting a ...
8 Apr 2025
Last month, news outlets and the entire internet was abuzz with the return of NASA astronauts ...
3 Apr 2025
What comes first - CMMS or predictive maintenance? If your answer is either, it is correct. ...
28 Mar 2025
Artificial intelligence (AI) talk has become commonplace. Today, engaging in business-focused ...
27 Mar 2025
Imagine a world where machines predict, diagnose, and fix their issues before they fail. This ...
25 Mar 2025
A facility maintenance plan is at the core of a facility’s operations. This organized ...
21 Mar 2025
Think of managing your maintenance operations like managing a championship sports team. Just ...
21 Mar 2025
The maintenance sector is battling a severe talent shortage that threatens to undermine ...
7 Mar 2025
Manufacturing maintenance is the backbone of industrial efficiency, ensuring machines run ...
5 Mar 2025
No one likes playing a guessing game when equipment breaks down. Yet, maintenance teams often ...
4 Mar 2025
The size of the preventive maintenance software market is discussed in millions of dollars, ...
4 Mar 2025
The organizational structure and corporate hierarchy vary from company to company. Large ...
28 Feb 2025
Maintenance procedures are essential for ensuring the longevity and reliability of machinery ...
21 Feb 2025
Sustainability is no longer just a buzzword; it's a critical component of corporate social ...
20 Feb 2025
A Computerized Maintenance Management System (CMMS) relies on accurate, well-organized data ...
18 Feb 2025
In an era where technology drives operational efficiency, Computerized Maintenance Management ...
14 Feb 2025
A Computerized Maintenance Management System (CMMS) is a key component of modern maintenance ...
13 Feb 2025
Introduction Maintenance management is the foundation of maintenance operations in industries ...
11 Feb 2025
Introduction A Computerized Maintenance Management System (CMMS) is software designed to help ...
7 Feb 2025