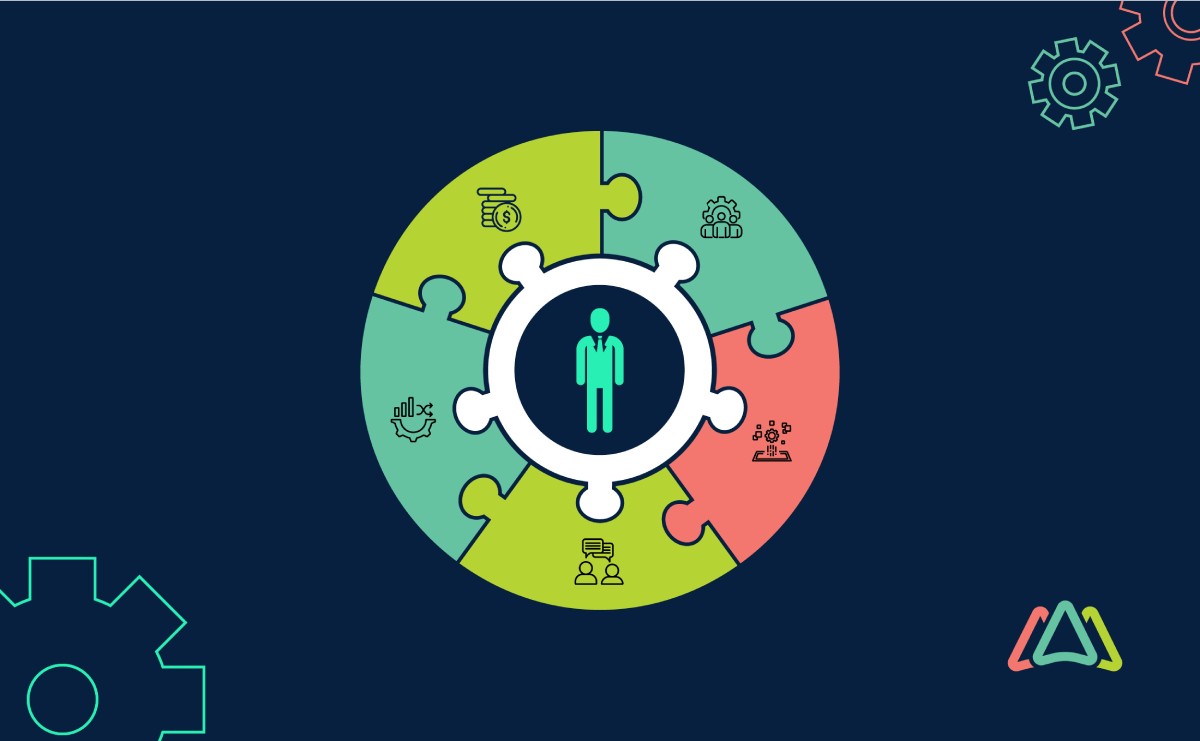
Challenges Faced by Maintenance Leaders and How to Overcome Them
Maintenance leaders are the driving force behind an organization’s maintenance strategies and continuous improvement efforts.They are responsible for ensuring the smooth functioning and reliability of assets, equipment, and facilities. Maintenance leaders are typically tasked with creating and executing maintenance plans, allocating resources, managing a team of technicians, and making decisions on how to optimize maintenance processes.
Effective maintenance leadership is of utmost importance to any organization that relies on equipment and assets to deliver products or services. The role of maintenance leaders extends far beyond just fixing things when they break down. Their strategic vision and management expertise are vital in maintaining optimal performance, minimizing downtime, and maximizing the lifespan of critical assets.
While their role is critical, it is not without its hurdles. The purpose of this blog is to shed light on some of the challenges and complexities faced by maintenance leaders today.
Challenge 1: Budget Constraints and Resource Allocation
1.1 Dealing with Limited Budgets for Maintenance Activities
One of the primary challenges faced by maintenance leaders is the constant pressure to achieve optimal maintenance outcomes with limited financial resources. Maintenance budgets are often constrained due to competing organizational priorities, cost-cutting initiatives, or unforeseen economic downturns. Budget constraints have a direct effect on maintenance leaders’ performance. Limited budget can hinder the ability to conduct timely preventive maintenance, invest in modern technologies, and adequately train maintenance teams.
Solution:
- Data-Driven Decisions: Maintenance leaders must gather and analyze historical data on maintenance costs, equipment breakdowns, and the impact of deferred maintenance. Use a CMMS to store and analyze maintenance data. This data-driven approach can help make a strong case for adequate budget allocations. CFOs are more likely to release funds when there is a solid business case to do so. A CMMS can help leaders in identifying areas where additional funding is needed.
- Prioritize Critical Assets: Identify and prioritize critical assets or equipment that are essential for operations. Allocate a larger portion of the budget to maintaining and ensuring the reliability of these key assets.
- Long-Term Planning: Advocate for long-term planning and investment in maintenance activities. Demonstrating the potential savings from proactive maintenance can help justify the need for adequate funding.
1.2 Allocating Resources Efficiently and Prioritizing Tasks
Maintenance leaders often face the challenge of distributing limited resources, including manpower, time, and equipment, across a wide range of maintenance tasks. Failure to allocate resources efficiently can lead to extended downtime, decreased productivity, and potential safety risks.
Solution:
- Risk-Based Approach: Adopt a risk-based approach to prioritize maintenance tasks. Focus on critical assets or systems that, if they fail, could have severe consequences for operations, safety, or the environment.
- Preventive Maintenance Planning: Use a CMMS to implement preventive maintenance plans based on equipment condition, usage patterns, and manufacturer's recommendations. Proactive maintenance reduces the likelihood of costly breakdowns.
- Cross-Training: Cross-train maintenance technicians to handle multiple tasks. This enhances flexibility in resource allocation and ensures that essential skills are available even when some team members are unavailable.
1.3 Justifying Maintenance Expenses
Maintenance leaders often find it challenging to justify maintenance expenditures, especially when maintenance activities may not have an immediate, tangible impact on revenue generation.
Solution:
- Align with Organizational Goals: Tie maintenance management strategies to the overall goals of the organization. Emphasize how effective maintenance directly contributes to increased productivity, reduced downtime, improved customer satisfaction and the company’s bottom line.
- Cost-Benefit Analysis: Conduct thorough cost-benefit analyses for proposed maintenance projects. Use the reporting and analytics features within the CMMS software to track return on investment. The reports in CMMS software can generate reports on maintenance history and costs, total cost of ownership of assets, depreciation, and more. When properly used, a CMMS can help maintenance managers identify assets that should be replaced instead of continuing to maintain them.
- Performance Metrics: Develop and track key performance indicators (KPIs) that demonstrate the effectiveness of maintenance activities. Highlight improvements in equipment reliability, mean time between failures (MTBF), and overall equipment effectiveness (OEE).
Challenge 2: Workforce Management and Skill Shortages
2.1 Retaining Skilled Maintenance Technicians
Once skilled technicians are hired, retaining them becomes a significant challenge. Moreover, as skilled technicians are retiring, businesses are finding it difficult to bring on new talent to replace them and retain them. Skilled maintenance professionals are highly sought after, and competitors may try to lure them away with better offers. Lack of growth opportunities and recognition can also lead to high turnover rates.
Solution:
- Career Development Plans: Create personalized career development plans for each maintenance technician. Provide opportunities for additional training, certifications, and advancement within the organization.
- Competitive Compensation and Benefits: Offer competitive salaries and comprehensive benefits packages to attract and retain skilled technicians. Regularly review compensation to ensure it aligns with industry standards. Websites like Payscale and Glassdoor offer good insights into what other companies are offering in terms of salaries and benefits, break these down by states and regions.
- Recognition and Appreciation: Recognize and appreciate the hard work of maintenance technicians regularly. Acknowledgment can be in the form of verbal praise, awards, or opportunities for advancement based on merit. Maintenance leaders can leverage a CMMS to highlight KPIs that maintenance teams and individuals should be hitting and recognize high performers.
2.2 Bridging the Gap Between Experienced and Younger Technicians
As experienced maintenance technicians near retirement, there is a potential knowledge gap between seasoned professionals and younger, less experienced technicians. Use the CMMS to capture and transfer critical institutional knowledge vital to maintain operational efficiency.
Solution:
- Knowledge Sharing Platforms: Implement knowledge sharing platforms within the organization to capture the expertise and experience of retiring technicians. These platforms can include documentation, video tutorials, and mentorship programs.
- Mentoring Programs: Pair younger technicians with experienced mentors to facilitate the transfer of knowledge and skills. Mentors can provide guidance, answer questions, and help younger technicians develop their abilities.
- Cross-Generational Collaboration: Foster an environment where younger technicians feel comfortable seeking advice from experienced colleagues. Encourage open communication and collaboration between different age groups to leverage diverse perspectives.
2.3 Lack of Interest in Maintenance as a Viable Career
The maintenance industry faces several workforce-related challenges, such as an aging workforce, a lack of interest in maintenance careers among younger generations, and a shortage of skilled technicians. The demand for maintenance services continues to grow, but finding and retaining qualified talent becomes increasingly difficult.
Solution:
- Promote Maintenance as a Viable Career: Collaborate with educational institutions and industry partners to raise awareness about maintenance careers. Highlight the rewarding aspects of the profession, such as job stability, opportunities for growth, and the essential role maintenance plays in various industries.
- Apprenticeship and Training Programs: Establish apprenticeship programs to attract and develop young talent. These programs provide hands-on experience, technical training, and mentorship, giving aspiring maintenance technicians a head start in their careers.
- Employee Referral Programs: Encourage current employees to refer potential candidates to fill maintenance positions. Incentives such as bonuses or rewards can motivate employees to actively participate in recruitment efforts.
Challenge 3: Keeping up with Industry Standards, Technological Advancements, and Digitalization
The digital transformation of maintenance operations has become a necessity to enhance efficiency, optimize resources, and ensure the reliability of assets. However, this journey is not without its challenges. Maintenance leaders can employ the following solutions as they navigate evolving industry standards, technological advancements, and digitalization.
3.1 Constantly Evolving Industry and Regulatory Standards
As industries grow and technologies advance, industry standards for maintenance practices evolve. Keeping up with these changes and ensuring compliance can be daunting for maintenance leaders. Failure to adhere to updated standards can lead to reduced operational efficiency, safety risks, and potential legal repercussions.
Solution:
- Ongoing Education: Encourage teams to engage in continuous education and professional development programs. Participating in industry workshops, webinars, and conferences helps them stay informed about the latest trends and best practices.
- Collaborate with Industry Associations: Establish connections with industry associations and trade groups. These organizations often provide updates on changing standards and offer resources to assist in implementing compliant maintenance practices.
- Regular Audits: Conduct regular audits to assess the organization's adherence to industry standards. This proactive approach allows identifying areas for improvement and implementing necessary changes promptly.
3.2 Embracing Technological Advancements
Technological advancements offer transformative opportunities for maintenance operations. However, the pace at which new technologies emerge can be overwhelming for maintenance leaders. Selecting the right technology and ensuring a smooth integration process pose significant challenges.
Solution:
- Technology Roadmap: Develop a technology roadmap that aligns with the organization's maintenance goals and long-term objectives. This roadmap should outline the step-by-step adoption of technologies over time, considering budgetary constraints and resource availability.
- Pilot Projects: Implement pilot projects to evaluate the feasibility and effectiveness of new technologies on a small scale. Pilot projects provide valuable insights into how technologies perform in real-world scenarios and allow for fine-tuning before full-scale adoption.
- Collaboration with Vendors: Work closely with technology vendors and suppliers. They can provide expert guidance, product demonstrations, and training to ensure the successful integration of new technologies.
3.3 Embracing Digitalization in Maintenance Operations
The transition from processes that are traditional paper-based or use spreadsheets, to digital systems can be challenging. Resistance to change, a lack of digital literacy among maintenance teams, and concerns about data security are common hurdles faced by maintenance leaders during the digitalization process.
Solution:
- Change Management: Implement a comprehensive change management strategy that involves all stakeholders, from management to frontline maintenance staff. Clearly communicate the benefits of digitalization and address concerns through transparent and open communication.
- Training and Upskilling: Provide extensive training and upskilling programs for maintenance teams to ensure they are comfortable with digital tools and systems. When evaluating CMMS or similar software, ensure that products selected are easy to use and offer excellent support. Investing in workforce development is essential for successful digital transformation.
- Data Security Measures: Implement robust data security measures to protect sensitive maintenance information. Talk to your vendor about CMMS data security and assure the maintenance team that data privacy and security are a top priority.
Challenge 4: Communication and Collaboration
Effective communication and collaboration are crucial for successful maintenance operations. Maintenance leaders must foster clear lines of communication both within the maintenance team and across various departments and stakeholders. Additionally, overcoming communication barriers in diverse teams and collaborating effectively with stakeholders are essential for achieving maintenance objectives. Utilizing a Computerized Maintenance Management System (CMMS) can significantly aid in addressing these challenges and improving communication and collaboration. Most maintenance software products have mobile apps, in app messaging, and configurable real time notification settings. CMMSs also include dashboards to easily share important KPIs so all team members understand how the maintenance department is performing.
4.1 Fostering Effective Communication between Maintenance and Other Departments
Communication breakdowns between maintenance teams and other departments can lead to misunderstandings, delays, and inefficiencies. Each department may have its priorities, making it challenging for maintenance leaders to align maintenance activities with the overall goals of the organization.
Solution:
- Regular Meetings: Organize regular meetings between maintenance leaders and representatives from other departments to discuss ongoing maintenance needs, upcoming projects, and potential challenges. These meetings foster transparency and ensure that everyone is on the same page.
- Shared CMMS Platform: Implement a CMMS that offers a shared platform for all departments or one that has integration capabilities with ERP, and other financial tools. This allows real-time access to maintenance data, work orders, and progress updates, facilitating better communication and collaboration.
- Performance Metrics: Define key performance indicators (KPIs) that are relevant to both maintenance and other departments. Tracking these metrics allows everyone to see how maintenance activities contribute to the overall success of the organization.
4.2 Overcoming Communication Barriers in Diverse and Remote Teams
Maintaining effective communication in a diverse team, where team members may have different languages, cultural backgrounds, or work styles, can be challenging. Similarly, when maintenance teams are located in different geographical regions, coordinating activities and sharing information becomes more complex.
Solution:
- Multilingual Support: If the team is multilingual, provide language training or employ translation tools to bridge communication gaps. Clear communication channels and standardized procedures help ensure understanding. A CMMS with multilingual support and virtual collaboration tools allows maintenance teams from diverse backgrounds and geographical locations to communicate seamlessly.
- Virtual Collaboration Tools: Utilize virtual collaboration tools, such as video conferencing and instant messaging platforms, to facilitate real-time communication between team members across different locations. The centralized nature of a CMMS ensures that all team members have access to the same data and information, fostering a cohesive and collaborative work environment.
- Establish Communication Protocols: Set clear communication protocols that outline how information should be shared, who to contact for specific issues, and how to handle emergencies in different regions.
Challenge 5: Handling Change and Continuous Learning
Change is an inevitable part of the maintenance landscape, driven by evolving technologies, shifting industry trends, and organizational restructuring. Navigating these changes while fostering a culture of continuous learning is vital for maintenance leaders to ensure their teams remain efficient and effective.
5.1 Leading Through Organizational Changes and Restructuring
Organizational changes, such as mergers, acquisitions, or restructuring, can lead to uncertainty and resistance among maintenance teams. Maintaining morale and productivity during these transitions becomes a significant challenge for maintenance leaders.
Solution:
- Transparent Communication: Provide clear and open communication about the reasons for the changes and the expected impact on maintenance operations. Address concerns and uncertainties to build trust among the team.
- Lead by Example: Demonstrate adaptability and resilience as a maintenance leader during times of change. Showcase a positive attitude and emphasize the opportunities that come with organizational restructuring.
- Team Involvement: Involve the maintenance team in the decision-making process whenever possible. Encouraging their input and suggestions helps them feel valued and engaged during transitions.
5.2 Promoting a Culture of Continuous Learning among Maintenance Teams
Encouraging a culture of continuous learning can be challenging, especially in environments where maintenance teams focus solely on reactive repairs. Shifting the mindset towards proactive learning and improvement requires sustained effort from maintenance leaders.
Solution:
- Learning Opportunities: Provide opportunities for maintenance teams to attend workshops, webinars, and industry conferences. Encourage the pursuit of certifications and other qualifications to enhance their skills.
- Knowledge Sharing: Facilitate knowledge sharing sessions among maintenance team members. Encourage experienced technicians to mentor newer members, fostering a collaborative learning environment.
- Recognition and Rewards: Recognize and reward maintenance technicians who actively participate in continuous learning efforts. Highlighting the importance of learning within the organization motivates others to follow suit.
A CMMS supports continuous learning by providing access to a wealth of maintenance data, historical records, and performance metrics. This data-driven approach allows maintenance teams to analyze past performance, identify areas for improvement, and implement new strategies for continuous growth.
As the custodians of critical assets and equipment, maintenance leaders play a crucial role in ensuring the smooth functioning of organizations. Proactive maintenance leadership is essential to anticipate challenges, identify opportunities for improvement, and drive operational excellence. By fostering a culture of innovation, embracing new technologies, and making data-driven decisions, maintenance leaders can lead their teams towards higher efficiency, lowering costs, reduced downtime, and increased reliability.
TABLE OF CONTENTS
Keep Reading
Ever find yourself checking into a luxury hotel and expecting a relaxing stay, only to find a ...
11 Apr 2025
Organizations are witnessing swift changes in the business environment and confronting a ...
8 Apr 2025
Last month, news outlets and the entire internet was abuzz with the return of NASA astronauts ...
3 Apr 2025
What comes first - CMMS or predictive maintenance? If your answer is either, it is correct. ...
28 Mar 2025
Artificial intelligence (AI) talk has become commonplace. Today, engaging in business-focused ...
27 Mar 2025
Imagine a world where machines predict, diagnose, and fix their issues before they fail. This ...
25 Mar 2025
A facility maintenance plan is at the core of a facility’s operations. This organized ...
21 Mar 2025
Think of managing your maintenance operations like managing a championship sports team. Just ...
21 Mar 2025
The maintenance sector is battling a severe talent shortage that threatens to undermine ...
7 Mar 2025
Manufacturing maintenance is the backbone of industrial efficiency, ensuring machines run ...
5 Mar 2025
No one likes playing a guessing game when equipment breaks down. Yet, maintenance teams often ...
4 Mar 2025
The size of the preventive maintenance software market is discussed in millions of dollars, ...
4 Mar 2025
The organizational structure and corporate hierarchy vary from company to company. Large ...
28 Feb 2025
Maintenance procedures are essential for ensuring the longevity and reliability of machinery ...
21 Feb 2025
Sustainability is no longer just a buzzword; it's a critical component of corporate social ...
20 Feb 2025
A Computerized Maintenance Management System (CMMS) relies on accurate, well-organized data ...
18 Feb 2025
In an era where technology drives operational efficiency, Computerized Maintenance Management ...
14 Feb 2025
A Computerized Maintenance Management System (CMMS) is a key component of modern maintenance ...
13 Feb 2025
Introduction Maintenance management is the foundation of maintenance operations in industries ...
11 Feb 2025
Introduction A Computerized Maintenance Management System (CMMS) is software designed to help ...
7 Feb 2025