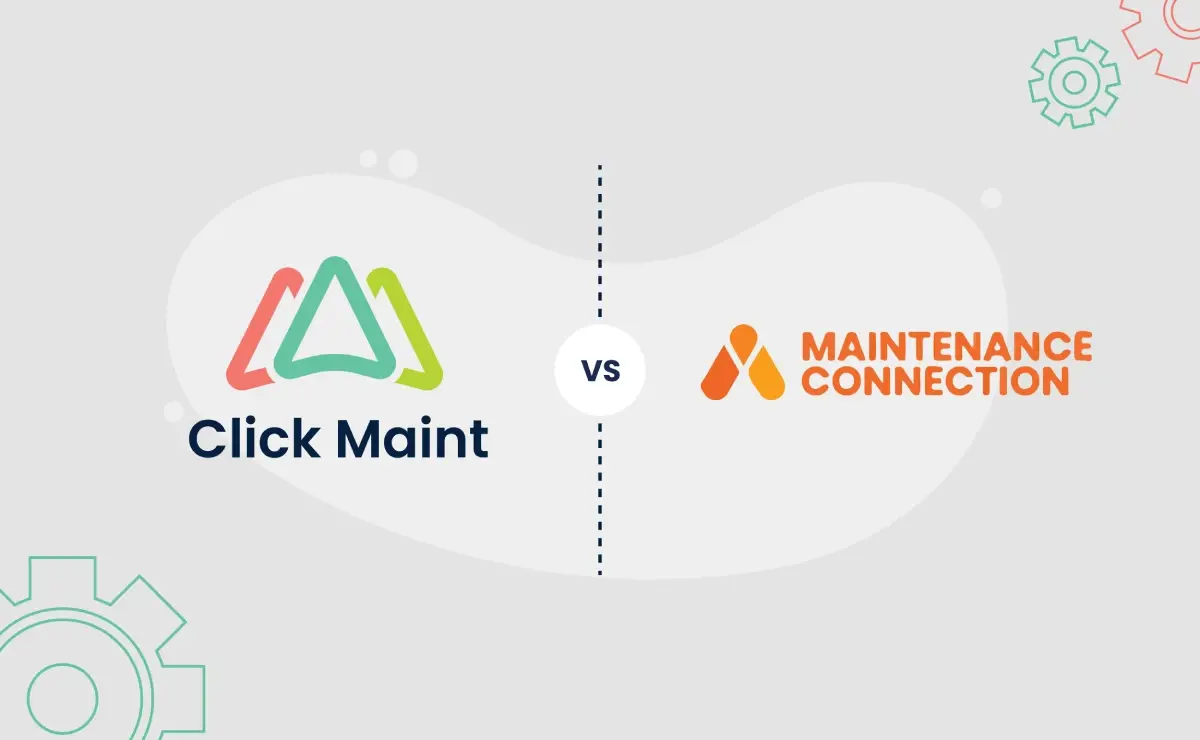
A Compelling Maintenance Connection CMMS Alternative to Consider
Two notable contenders stand out in the realm of computerized maintenance management systems (CMMS): Click Maint and Maintenance Connection. As you research and evaluate maintenance management solutions, understanding the nuances between these platforms will help to make an informed decision on which solution best fits your maintenance team’s needs. This comprehensive comparison guide will delve into the key features, functionality, and industry fit of both Click Maint and Maintenance Connection.
By examining the pros and cons of each solution, you'll gain valuable insights into which CMMS best aligns with your organization's unique needs and objectives. Whether you're a small business seeking agility or a large enterprise requiring robust capabilities, this analysis will equip you with the knowledge to choose the ideal CMMS for your maintenance management strategy.
Overview of Click Maint and Maintenance Connection CMMS
When choosing a Computerized Maintenance Management System (CMMS), it's important to understand each solution's key offerings.
Let's dive into an overview of Click Maint and Maintenance Connection, two popular CMMS options in the market.
Click Maint: Simplicity Meets Efficiency
Click Maint positions itself as a user-friendly, cost-effective maintenance management solution tailored for small and mid-sized businesses. Its intuitive interface allows for quick implementation, making it an attractive option for companies looking to streamline their maintenance operations without a steep learning curve. One of the key challenges for maintenance teams using CMMS software is that some users are not tech savvy, and therefore, user adoption is low. Another challenge is that many organizations don’t use all the functionality available to them in their paid subscription. Reliable Plantdid a study that found 94.7% of maintenance managers don’t use all the functionality available in their CMMS. Click Maint addresses these challenges by making its software easy to use regardless of users’ tech competency. This applies to both the desktop app and the mobile app. Click Maint's mobile app empowers field technicians to access and update information on-the-go, enhancing overall productivity.
Maintenance Connection: Comprehensive Asset Management
Maintenance Connection offers a robust CMMS platform designed to handle complex maintenance needs. It excels in work order management and covers planned, preventative, and reactive maintenance for intricate assembly lines and individual components. This solution is particularly well-suited for industrial manufacturing, healthcare, facility management, and government organizations. Maintenance Connection focuses on offering robust functionality over ease of use and simplicity.
Key Features and Functionality Comparison
When comparing Click Maint and Maintenance Connection, it's essential to understand their core features and how they stack up against each other. Both CMMS solutions offer the essential functionality that are expected in a CMMS (maintenance requests, work orders, preventive maintenance, inspection, asset and inventory management, vendor and supplier management and reports and KPIs). But these two CMMSs differ significantly in functional depth, customers they cater to, price, and ease of use.
Work Order Management
Click Maint:
Click Maint provides a user-friendly interface for managing work orders, making it ideal for small to mid-sized businesses. Its intuitive design allows for quick CMMS implementation and ease of use.
Maintenance Connection:
Maintenance Connection, on the other hand, offers more comprehensive work order management capabilities with customizable workflow settings that are suitable for complex industrial settings and large-scale operations.
Both systems support planned, preventive, and reactive maintenance. However, Maintenance Connection excels in managing complex assemblies
and individual components in production lines. It provides advanced features for developing maintenance intelligence, optimizing costs, and improving asset longevity.
Asset Management
Click Maint:
Click Maint makes asset tracking easy. It includes all the essential features that one would expect in a CMMS like asset registry, maintenance history, parent / child and hierarchy, downtime tracking, associate parts, warranty tracking and QR code scanning. Users can also associate preventive maintenance work orders and reactive work orders to assets. Assets can be managed from desktop and the mobile app.
Maintenance Connection:
Maintenance Connection’s asset management functionality goes deep, and includes additional features like IoT sensors, condition monitoring, asset lifecycle and depreciation reporting. With these advanced features comes complexity, however. It’s robust for sure and well suited for complex industrial settings, but probably overkill for small and mid sized operations that don’t require these features.
Mobile Capabilities
While both CMMS solutions offer mobile apps, Maintenance Connection's mobile functionality is more robust. It enables field service teams to not only manage work orders, PMs and requests on the go, but also extends other functionality like purchase order creation and approval from mobile devices. Click Maint mobile does not offer this functionality currently. Both have the ability to upload photos to work orders, assets, requests using mobile phone cameras and also have QR code scanning capabilities. Maintenance Connections mobile app is more robust, but a lot more complex and less user-friendly than Click Maint’s mobile CMMS app.
Reporting and Analytics
Maintenance Connection:
Maintenance Connection stands out with its extensive reporting capabilities, offering deeper insights into maintenance operations. The reporting tools are very customizable and allow users to build and extract almost any report you can think of. Reports can be saved and emailed out to users on a scheduled basis.
Click Maint:
Click Maint, while providing essential reporting features, focuses on simplicity and ease of use, making it more accessible for smaller organizations with less complex reporting needs. Users can report on maintenance history, costs, backlog, downtime, and KPIs like mean time to repair (MTTR) and mean-time between failure (MTBF).
Industry Fit Analysis for Each CMMS Solution
Click Maint: Ideal for Small to Mid-sized Businesses
Click Maint's user-friendly interface and cost-effective solution make it an excellent fit for small to mid-sized businesses across various industries.
Its agile nature and customer-centric approach allow for quick implementation, making it particularly suitable for companies looking to streamline their maintenance operations without a lengthy setup process.
The mobile app feature ensures that field teams can access critical information on the go, enhancing overall efficiency. Most businesses using Click Maint can start managing work orders and PMs within the first 30 days.
Maintenance Connection: Tailored for Complex Operations
Maintenance Connection caters to larger organizations with complex maintenance needs, particularly in industrial manufacturing, healthcare, facility management, and government sectors.
Its comprehensive work order management capabilities excel in handling planned, preventative, and reactive maintenance for intricate assembly lines and individual components.
This CMMS is well-suited for multi-site operations and organizations requiring detailed asset lifecycle management. With all the extra functionality comes extra cost and time to implement.
Choosing the Right Fit
When selecting the right CMMS software between these solutions, consider your organization's size, industry, and specific maintenance requirements.
Click Maint offers a more straightforward, budget-friendly option for smaller operations, while Maintenance Connection provides a robust, feature-rich platform for larger enterprises with intricate maintenance needs.
Evaluate factors such as scalability, mobile capabilities, and integration requirements to determine which solution aligns best with your long-term maintenance strategy and operational goals.
Pros and Cons of Click Maint vs Maintenance Connection
Click Maint Advantages and Drawbacks
Click Maint shines as a user-friendly, cost-effective solution for small to mid-sized businesses. Its intuitive interface and mobile app make it easy for teams to adopt and use on the go.
Quick implementation and strong customer support further enhance its appeal.
However, it may lack some of the more advanced features required by larger enterprises or complex industrial operations.
Maintenance Connection Strengths and Limitations
Maintenance Connection offers a robust, comprehensive CMMS suitable for larger organizations and complex industrial environments. Its extensive feature set, including advanced work order management and multi-site capabilities, makes it ideal for manufacturing, healthcare, and government sectors. The option for on-premise or cloud deployment provides flexibility. However, the system's complexity requires a steeper learning curve, longer implementation time and higher implementation costs. User licenses are also much more costly compared with Click Maint. Maintenance Connection user licenses cost between $80 and $150/month per user where Click Maint is only $35/month per user.
Factors that Help You Decide Your Apt Fit
Your choice between Click Maint and Maintenance Connection ultimately depends on your organization's size, industry, and specific needs.
Click Maint is best for smaller operations seeking an agile, easy-to-use solution with quick ROI.
Maintenance Connection is better suited for larger enterprises requiring comprehensive asset management across multiple sites or industries with complex maintenance needs.
Consider factors like budget, implementation time, and required features when making your decision.
Which CMMS is the Best Fit for Your Needs?
Choosing the right CMMS solution depends on your organization's specific requirements, industry, and scale of operations.
Let's break down the key factors to consider when deciding between Click Maint and Maintenance Connection.
Company Size and Industry
Click Maint is ideal for small to mid-sized businesses seeking a user-friendly, cost-effective solution. Its agile approach and quick implementation make it perfect for companies looking to streamline their maintenance processes without a hefty investment.
Maintenance Connection, on the other hand, caters to larger organizations in industries like manufacturing, healthcare, and government. Its comprehensive features and multi-site capabilities make it suitable for complex operations. Software and implementation costs are significantly higher for Maintenance Connection given that it is a robust enterprise solution.
Functionality and Scalability
If you need basic maintenance management with a focus on ease of use, Click Maint's straightforward interface and mobile app might be your best bet. It's particularly suitable for businesses transitioning from spreadsheet-based systems.
For organizations requiring advanced features like predictive maintenance, enterprise asset management, and in-depth reporting, Maintenance Connection offers a more robust solution.
Its ability to handle complex workflows and integrate with other systems makes it highly scalable.
Budget and Implementation
Consider your budget and implementation timeline.
Click Maint offers a more affordable option with rapid deployment, which is ideal for businesses looking to adopt a CMMS quickly.
Maintenance Connection, while potentially more expensive, provides a feature-rich platform that can deliver significant long-term value for larger organizations willing to invest in a comprehensive solution.
Conclusion
As you evaluate Click Maint and Maintenance Connection, consider your organization's specific needs and priorities. Both CMMS solutions offer robust features, but their strengths align differently with various industries and company sizes.
Click Maint excels for small to mid-sized businesses seeking an intuitive, cost-effective solution with agile support.
Maintenance Connection caters to larger enterprises, particularly in manufacturing, healthcare, and facilities management, offering comprehensive functionality and multi-site capabilities.
Ultimately, the best fit depends on your industry, scale of operations, and desired level of complexity. By carefully assessing each platform's strengths against your requirements, you can select the CMMS that will optimize your maintenance operations and drive long-term efficiency.
Addendum: How to Choose the Best CMMS Alternative for your Budget?
Choosing the right Computerized Maintenance Management System (CMMS) might seem complicated, but it becomes manageable when you break it down into simple steps. Think of a CMMS as a helpful digital tool that keeps machines running smoothly, helps track repairs, and stops problems before they start. It saves time, money, and effort, just like regular check-ups keep you healthy, regular maintenance keeps equipment in shape.
Since there are over 300–400 CMMS tools available online, it’s important to pick one that works best for your needs and your budget. Here’s a simplified path to making the right choice:
-
Know what you need – Figure out what features your business requires, like work order tracking or preventive maintenance. Consider how many people will use the system and what each person needs access to.
-
Set a realistic budget – Don’t just look at the subscription cost; consider onboarding, training, and long-term support. Sometimes cheaper options offer less help, while more expensive ones include better service and features.
-
Try before you buy – Request demos or free trials from at least two vendors. This helps you see how the software works in real life and whether it’s easy to use. Look for mobile access and a simple design so your team actually uses it.
-
Look for support and safety – Good customer service and strong data protection are key. Choose vendors with proven reputations, and if your business has strict security needs, ask for their security certifications.
-
Think long-term – Make sure the software can grow with your business and connect easily with other tools you use, like accounting or scheduling systems.
In a world full of choices, buyers today are in a strong position. Most CMMS companies offer flexible plans and fast support. If you take the time to evaluate, demo, and test a few options, you’ll find a system that fits your needs perfectly, without going over budget.
More CMMS Alternatives to Consider
Keep reading our other blogs on various other CMMS alternatives to consider.
TABLE OF CONTENTS
Keep Reading
Imagine you're going through a compliance audit, and the inspector asks for maintenance ...
10 Jul 2025
Maintenance managers understand that disasters are unpredictable and can have a massive ...
4 Jul 2025
Asset lifespan is a key concern for executives and maintenance and facility management teams. ...
3 Jul 2025
Your company recently invested funds and time for new CMMS software, and six months later, it ...
1 Jul 2025
As Computerized Maintenance Management Systems (CMMS) become more connected and cloud-based, ...
1 Jul 2025
Edge computing is an innovative technology that enables data to be processed at the source, ...
24 Jun 2025
Facility management has undergone a significant transformation in recent times. Take, for ...
20 Jun 2025
A facility maintenance plan is at the core of a facility’s operations. This organized ...
19 Jun 2025
In the early days, preventive maintenance could be done effectively with a trained eye and a ...
17 Jun 2025
Sticky notes fall off, whiteboard grids get wiped, and spreadsheets never beep when a ...
13 Jun 2025
Handing a slice of your maintenance workload to a contractor is less about “giving up ...
12 Jun 2025
Downtime in enterprise environments doesn’t just mean a stop in operations; it means lost ...
10 Jun 2025
Understanding equipment functionality is crucial for effective repairs. A clear, systematic ...
6 Jun 2025
Maintenance managers know that every unplanned equipment failure is more than a simple ...
5 Jun 2025
What keeps a facility running smoothly? Initially, many of us may zoom in on its equipment, ...
29 May 2025
In today's digital world, every decision needs to pass the test of strategic and operational ...
27 May 2025
The business world is very different from a decade ago. Technological advancements have grown ...
23 May 2025
Picture this: a maintenance technician inspects a complex pump system. Instead of typing a ...
20 May 2025
For most of the 20th century, maintenance teams mainly applied a reactive approach to ...
9 May 2025
Imagine visiting a manufacturing plant where maintenance technicians gather around a large ...
8 May 2025