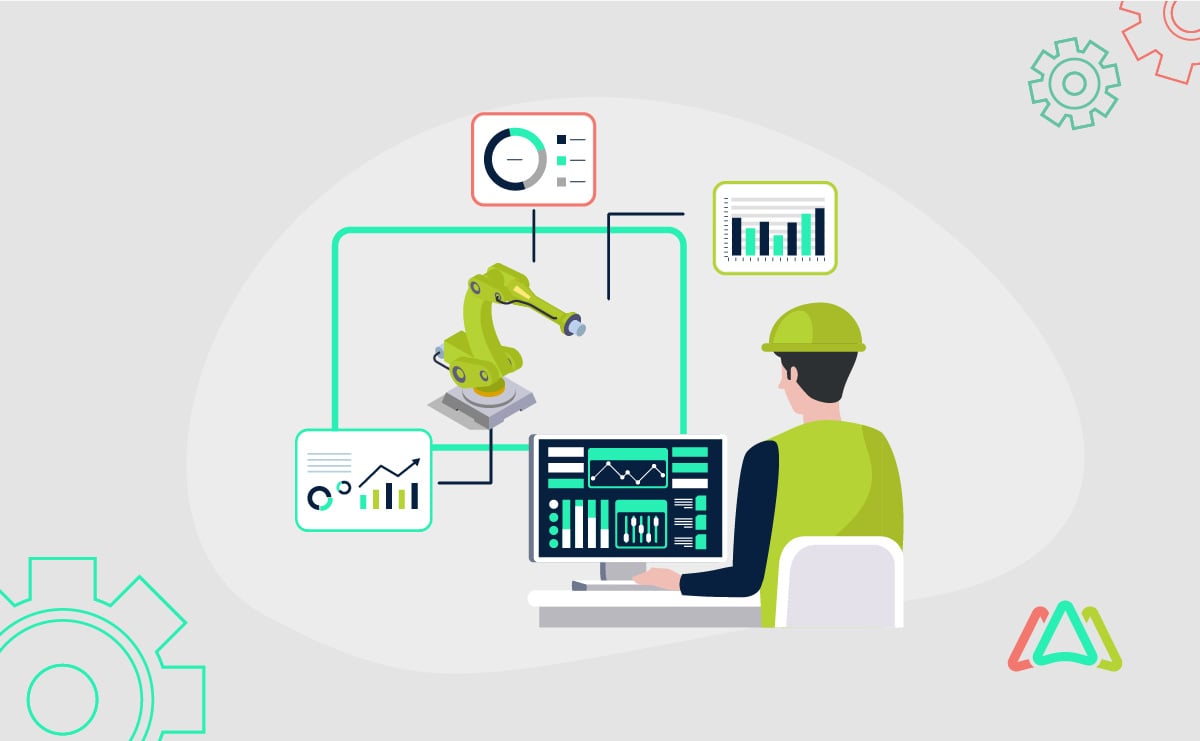
Transform Your Maintenance Strategy Using CMMS Data Insights
Businesses are increasingly turning to data-driven decision-making as a means to optimize their people, processes, and systems — and maintenance management typically follow suit. However, to develop a maintenance strategy properly, one must have a thorough understanding of the current state of one's facility. These days, systems within businesses are becoming more and more complex, thus requiring data-based maintenance management strategies in any company that values efficiency. This is where having a Computerized Maintenance Management System (CMMS) can become a game-changer.
A Computerized Maintenance Management System (CMMS) centralizes essential maintenance data and automates key processes within a facility. It organizes critical information such as asset details, maintenance schedules, work orders, and performance metrics, providing a single source of truth for maintenance operations.
By leveraging this data, organizations can streamline workflows, enhance visibility across assets, and optimize resource allocation. Key insights derived from CMMS data enable predictive maintenance, reduce downtime, and lower costs, transforming maintenance strategies from reactive to proactive.
In this article, we will explore how data from CMMS software can reshape maintenance strategies, diving into its impact on efficiency, cost savings, and operational reliability.
Using CMMS Data Insights for a Proactive Maintenance Strategy
Using data-driven insights from maintenance management system software as the basis for decision-making, a computerized maintenance management system (CMMS) transforms organizations from reactive operation to predictive maintenance. Businesses can determine trends, measure resource efficiency, and prevent expensive failures through actual analysis with KPI tracking and real-time dashboards. Many organizations still depend on ineffective practices because they don't have any access to CMMS data. For example, some often use their equipment until they finally fail, while some do not have a systematic method of setting inventory levels. In turn, these can cause more downtime, higher repair costs, and missed optimization opportunities.
The following are some ways in which CMMS data can empower organizations in some of the crucial areas of maintenance and operations, with practical examples that contrast the CMMS approach with its traditional counterparts:
From Reactive to Predictive Maintenance
Moving from reactive maintenance—fixing issues only after they arise—to predictive maintenance can save businesses significant time and costs. For example, analyzing historical data on equipment failures can reveal patterns, such as increased breakdowns after a specific usage threshold. This insight allows maintenance teams to schedule repairs or replacements before failures occur, reducing unplanned downtime.
A manufacturing plant, for instance, might use CMMS data to predict that a conveyor belt requires maintenance every 3,000 operational hours, enabling the team to perform upkeep during scheduled downtime rather than in the middle of production.
Enhanced Asset Performance Monitoring
CMMS systems track essential KPIs like the mean time to repair (MTTR) and between failures (MTBF) to monitor asset performance. Businesses can regularly review these metrics to pinpoint underperforming equipment and address issues. For instance, if an HVAC system consistently requires repairs within short intervals, the CMMS can flag this trend, prompting an investigation into possible root causes such as poor installation or inadequate maintenance. By addressing these factors, organizations can extend the equipment’s lifecycle and reduce operational disruptions.
Improved Resource Management
CMMS data ensures resources like inventory and manpower are allocated efficiently. For example, by analyzing spare part usage trends, a facility can maintain optimal stock levels, avoiding overstocking while ensuring critical components are always available. Similarly, task trend analysis helps allocate manpower effectively; if data shows a peak in maintenance requests during summer due to increased HVAC usage, managers can adjust staffing levels accordingly. A hotel chain might use this approach to ensure their technicians are adequately distributed across properties during peak seasons.
Accurate Data Collection and Centralization
Accurate and centralized data is the backbone of a successful maintenance strategy. CMMS platforms collect data from multiple sources—assets, maintenance logs, and inspections—into a unified system. For example, a logistics company managing a fleet of vehicles can use a CMMS to consolidate data on fuel usage, tire wear, and engine performance. This centralized information ensures no detail is overlooked, enabling cohesive planning and eliminating data silos that often lead to inefficiencies.
Actionable Insights from Dashboards
CMMS dashboards convert complex data into visual insights, making it easier for managers to identify trends and make decisions. For instance, a factory supervisor might notice from the dashboard that a specific machine has been running at reduced efficiency for several weeks. This insight could prompt an inspection that uncovers a worn-out component, which can then be replaced before causing a significant failure. Such real-time visibility helps prioritize tasks and prevent minor issues from escalating.
Implement Data-Driven Decisions
The ultimate value of CMMS lies in its ability to drive informed decisions. By analyzing data trends, organizations can adjust maintenance schedules, focus on high-performing assets, and plan long-term investments. For instance, an energy company might use CMMS insights to prioritize maintenance on wind turbines generating the most electricity, ensuring maximum output. This targeted approach reduces costs, improves productivity, and enhances the reliability of critical assets.
Choosing the Right CMMS for Your Needs
Reaping the benefits of maintenance management usually boils down to choosing the correct CMMS. Several options are there, but you need to be realistic about your specific business needs and compare features to get the ideal business fit. A perfect CMMS brings high returns regarding streamlining processes and supporting the best decision-making as your operations expand. Below, we’ve outlined what you need to watch out for and questions to pose when evaluating possible CMMS solutions.
Key Features to Look For
When choosing a CMMS, it’s important to focus on features that align with your operational goals and long-term requirements. Below is a detailed explanation of the key features to prioritize:
Advanced Analytics
A powerful CMMS should provide more than just basic data logging; it should offer detailed analytics to identify trends, predict maintenance needs, and track performance. For example, advanced analytics can highlight recurring issues in specific equipment, allowing you to address underlying causes rather than repeatedly repairing symptoms. These insights help prioritize tasks and allocate resources efficiently.
Intuitive Interface
A user-friendly interface ensures quick adoption by your team, minimizing the learning curve and maximizing efficiency. Features like drag-and-drop scheduling, real-time notifications, and simple navigation make daily tasks easier for technicians and managers alike. For instance, a CMMS with a clean dashboard can provide an at-a-glance view of pending work orders, overdue tasks, and asset performance metrics, saving time and reducing errors.
Cloud Accessibility
A cloud-based CMMS allows you to access the system from anywhere, ensuring flexibility for remote teams or multi-site operations. This is especially valuable for industries with dispersed assets, such as utility providers or logistics companies. For example, a field technician can update work orders or check inventory levels directly from a mobile device, reducing delays and improving communication with the office team.
Integration Options
Integration capabilities ensure the CMMS works seamlessly with your existing tools, such as ERP, IoT devices, or financial systems. For example, integrating IoT sensors with your CMMS enables real-time equipment monitoring, triggering automatic maintenance alerts when performance thresholds are crossed. Similarly, integration with ERP systems can streamline workflows by syncing inventory data and budgeting details, reducing duplication and errors.
Questions to Ask Vendors
When evaluating CMMS vendors, you need to ask the right questions to make sure that the solution aligns with your business requirements and long-term goals.
Here are some important questions to consider:
- Can the CMMS be tailored to meet your unique operational needs, such as specific workflows or reporting formats?
- Does the vendor provide adequate training, onboarding, and support to help your team quickly adapt to the system?
- Can the system grow with your business, accommodating more users, assets, or locations as needed?
- Does the system offer mobile functionality for on-the-go updates and remote access for field teams?
- What measures are in place to protect sensitive maintenance and operational data?
What kind of support is available post-implementation, such as live chat, phone support, or dedicated account managers? - How long does it typically take to deploy the system, and what resources are needed during the implementation phase?
- How often is the system updated, and are there additional costs for upgrades or ongoing maintenance?
- Is the CMMS compatible with your existing tools, such as ERP systems, IoT devices, or other software?
- Can the vendor provide case studies or examples of how their CMMS has delivered ROI for businesses similar to yours?
Make Your Maintenance Strategy More Efficient
In short, maintaining optimized operations for maintenance has become a necessity for any business that ever hopes to increase efficiency while reducing costs and maintaining competitiveness in the market. A Computerized Maintenance Management System (CMMS) optimizes maintenance operations from reactive to proactive strategies, ensuring that an organization has reliable equipment and continuity of operations. The insurance made available through predictive insights, which prevents costly downtimes, is evidence that keeps resource allocation centralized and allows businesses to make data-driven decisions concerning tangible results.
Selecting the right CMMS tailored to your operational needs is a crucial step in transforming maintenance management. Key features such as advanced analytics, user-friendly interfaces, cloud accessibility, and strong integration should therefore be focused on while asking the proper vendor questions so you can deliver just the right solution for the goals you're trying to reach with your organization, as well as one that would grow with your business. With the proper CMMS in place, not only will it allow for more efficient maintenance procedures, but it will also open new doors to productivity and cost savings that propel your organization more quickly toward long-term success.afety.
TABLE OF CONTENTS
Keep Reading
Ever find yourself checking into a luxury hotel and expecting a relaxing stay, only to find a ...
11 Apr 2025
Organizations are witnessing swift changes in the business environment and confronting a ...
8 Apr 2025
Last month, news outlets and the entire internet was abuzz with the return of NASA astronauts ...
3 Apr 2025
What comes first - CMMS or predictive maintenance? If your answer is either, it is correct. ...
28 Mar 2025
Artificial intelligence (AI) talk has become commonplace. Today, engaging in business-focused ...
27 Mar 2025
Imagine a world where machines predict, diagnose, and fix their issues before they fail. This ...
25 Mar 2025
A facility maintenance plan is at the core of a facility’s operations. This organized ...
21 Mar 2025
Think of managing your maintenance operations like managing a championship sports team. Just ...
21 Mar 2025
The maintenance sector is battling a severe talent shortage that threatens to undermine ...
7 Mar 2025
Manufacturing maintenance is the backbone of industrial efficiency, ensuring machines run ...
5 Mar 2025
No one likes playing a guessing game when equipment breaks down. Yet, maintenance teams often ...
4 Mar 2025
The size of the preventive maintenance software market is discussed in millions of dollars, ...
4 Mar 2025
The organizational structure and corporate hierarchy vary from company to company. Large ...
28 Feb 2025
Maintenance procedures are essential for ensuring the longevity and reliability of machinery ...
21 Feb 2025
Sustainability is no longer just a buzzword; it's a critical component of corporate social ...
20 Feb 2025
A Computerized Maintenance Management System (CMMS) relies on accurate, well-organized data ...
18 Feb 2025
In an era where technology drives operational efficiency, Computerized Maintenance Management ...
14 Feb 2025
A Computerized Maintenance Management System (CMMS) is a key component of modern maintenance ...
13 Feb 2025
Introduction Maintenance management is the foundation of maintenance operations in industries ...
11 Feb 2025
Introduction A Computerized Maintenance Management System (CMMS) is software designed to help ...
7 Feb 2025