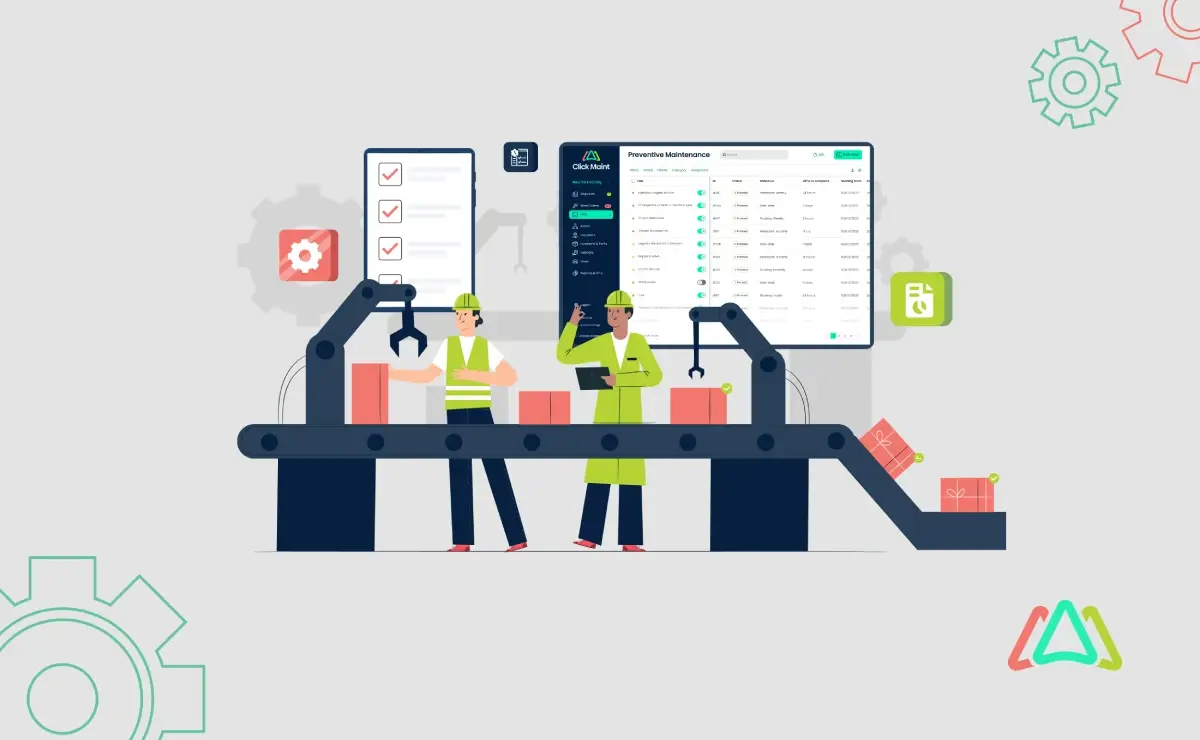
Essential CMMS Features for Small Manufacturing Businesses
Introduction
Small businesses are defined as organizations with at most 100 employees. Yet despite their small structure, they are often called the backbone of the economy because they drive economic growth, create jobs and foster innovation. The U.S. Small Business Administration (SBA) reports that small businesses account for 99.9% of all U.S. businesses and employ nearly half of the country’s private workforce.
However, like their large business counterparts, small businesses face the same challenges of an ever-demanding economy. For this reason, they constantly seek ways to streamline operations and improve efficiency. In that regard, Computerized Maintenance Management Systems (CMMS) have emerged as a solution designed to automate and enhance maintenance operations for businesses of all sizes.
Here, we’ll explore the key CMMS features essential for small manufacturing businesses, focusing on ease of use, mobile capabilities, work orders, preventive maintenance, and fast implementation. We also identify what features are not essential for this specific group, highlighting small businesses’ particular needs that will enhance their maintenance processes.
Understanding the Needs of Small Manufacturing Businesses
Small manufacturing businesses typically have 100 or fewer employees and maintenance teams of 10 or less. These businesses often face unique challenges in maintenance management, such as limited resources, tight budgets, and the need to maintain high productivity levels with minimal downtime. Effective maintenance management is crucial for these businesses to keep their equipment running smoothly and avoid costly breakdowns. A CMMS can provide a centralized platform to manage maintenance tasks, track equipment history, and ensure that maintenance activities are carried out efficiently and on schedule.
The importance of a CMMS for small manufacturing businesses cannot be overstated. It helps streamline maintenance processes, improve equipment reliability, and enhance operational efficiency. By utilizing the right CMMS features, small businesses can overcome maintenance challenges and focus on their core manufacturing activities. This boosts productivity and contributes to long-term business growth and success.
Let’s now turn to the specific features that make CMMS the preferred maintenance management solution for small manufacturing businesses.
Ease of Use
When selecting a CMMS, an intuitive and user-friendly interface is paramount for small manufacturing businesses. With already demanding roles, maintenance teams can only afford to spend a little time learning complex software.
Key CMMS features contributing to ease of use include customizable dashboards that present relevant information at a glance and simple navigation that allows users to access necessary functions quickly. Additionally, requiring minimal CMMS training and technical expertise ensures that the maintenance team can use it immediately, minimizing downtime and accelerating the return on investment.
User-friendly CMMS software systems also tend to have better adoption rates among staff, leading to more consistent and accurate maintenance records. The systems’ ease of use ensures that even those with limited technical skills can utilize the CMMS to its full potential, fostering a more organized and proactive maintenance environment. Ultimately, a CMMS that prioritizes ease of use helps small manufacturing businesses maximize efficiency and maintain a high standard of operational reliability.
Mobile Capabilities
The advantages of mobile access to a CMMS for small manufacturing businesses are notable. Mobile capabilities allow maintenance teams to access and update maintenance information on the go, reducing the need to be tied to a desk. Features such as mobile apps and responsive design allow technicians to receive real-time notifications, log maintenance activities, and access work orders directly from their mobile devices. CMMS mobile features enhance productivity by enabling maintenance tasks to be performed more efficiently and with greater flexibility.
Additionally, CMMS mobile capabilities ensure that critical maintenance information is always at the fingertips of the maintenance team, no matter where they are in the facility. This reduces delays in communication, allows for faster response times to maintenance issues, and ensures that maintenance procedures are followed consistently. As a result, small manufacturing businesses can maintain smoother operations and reduce downtime, ultimately contributing to higher productivity and cost savings.
Work Orders
Work order is pivotal in organizing and prioritizing maintenance tasks within a small manufacturing business. They help ensure that maintenance activities are carried out systematically and that no task is overlooked. Essential work order features for small manufacturing businesses include task assignment, tracking, and completion functionalities. These features allow maintenance managers to assign tasks to specific technicians, track the progress of each work order, and ensure timely completion.
A CMMS that streamlines work order management can significantly improve communication within the maintenance team. It allows for better coordination of tasks, ensuring that the right resources are allocated to the right jobs at the right time. This increases efficiency and reduces the likelihood of equipment failures and unplanned downtime. A CMMS helps small manufacturing businesses maintain a well-organized and proactive maintenance approach by improving work order management.
Preventive Maintenance
Preventive maintenance is the most sought-after CMMS feature because it reduces downtime and extends equipment lifespan in small manufacturing businesses. In other words, preventive maintenance is the “money” feature because of its financial implications for an organization’s bottom line.
Key preventive maintenance features in a CMMS include scheduling, reminders, and checklists. These features help ensure that maintenance activities are carried out regularly and systematically, preventing potential equipment failures before they occur. A CMMS can help small manufacturing businesses maintain their equipment optimally by automating preventive maintenance processes with minimal manual intervention.
Automated preventive maintenance scheduling ensures that maintenance tasks are performed consistently and on time, reducing the risk of unexpected breakdowns. Reminders and checklists provide maintenance teams with clear guidelines and procedures to follow, ensuring that all necessary steps are taken to maintain equipment properly. This improves equipment reliability and enhances overall efficiency and productivity, allowing small manufacturing businesses to focus on their core operations without worrying about maintenance issues.
Fast Implementation
A quick and efficient CMMS implementation process is essential for small manufacturing businesses. After selecting a CMMS, maintenance managers are understandably anxious to have it up and running. Moreover, lengthy and complicated implementations can disrupt daily operations and drain valuable resources.
Essential implementation features include data import and export capabilities, user-friendly setup processes, and comprehensive training resources. These features help ensure that the CMMS can be launched quickly, with minimal impact on daily operations activities.
A CMMS that offers fast implementation minimizes downtime and allows small manufacturing businesses to start reaping the benefits of improved maintenance management sooner. By providing easy-to-use setup tools and accessible training materials, the CMMS ensures that the maintenance team can quickly become proficient in using the system. This smooth transition is crucial for maintaining productivity and ensuring the business can operate efficiently during implementation.
Now, let’s review some CMMS features that are considered non-essential for small manufacturing businesses.
What are Non-Essential CMMS Features for Small Manufacturing Businesses?
While a CMMS can offer many features, not all of them are essential for small manufacturing businesses. For instance, smaller organizations may not need integration with Enterprise Resource Planning (ERP) systems and complex approval workflows. These features often cater to larger enterprises with more intricate corporate structures and processes. With their leaner operations and fewer bureaucratic hurdles, small manufacturing businesses can focus on core functionalities directly impacting their maintenance efficiency.
In addition to integration with ERP systems and complex approval workflows, several other CMMS features may be non-essential for small manufacturing businesses. These include:
-
Advanced Analytics and Reporting:
While basic reporting features are important, advanced analytics tools that offer in-depth data analysis and predictive maintenance capabilities might need to be revised for small businesses. These features are often more suited to larger organizations with the resources to utilize and fully benefit from complex data analysis.
-
Multi-Site Management:
Small manufacturing businesses typically operate from a single location or have a limited number of sites. Features designed for managing multiple facilities across different locations might not be necessary and could add unnecessary complexity to the system.
-
Extensive Customization Options:
Highly customizable CMMS software can be appealing but are often more suited to larger businesses with specific and varied requirements. Small businesses may not need or benefit from extensive customization options, and more straightforward, out-of-the-box solutions can be more practical and cost-effective.
-
Advanced Security Features:
While security is essential, advanced security features designed for large organizations with extensive data protection requirements might be optional for smaller businesses. Basic security measures, such as user authentication and regular backups, are typically adequate.
By understanding which features are not essential, small manufacturing businesses can prioritize their CMMS selection process more effectively. This ensures they invest in a system that meets their needs without unnecessary complexity or cost. Focusing on essential features like ease of use, mobile capabilities, work orders, preventive maintenance, and fast implementation allows small businesses to maximize operational efficiency with CMMS and optimize their CMMS investment significantly.
Conclusion
A CMMS can be a game-changer for small manufacturing businesses, providing them with the tools to streamline maintenance operations and improve overall efficiency. By focusing on essential features such as ease of use, mobile capabilities, work orders, preventive maintenance, and fast implementation, small manufacturing businesses can make informed decisions when selecting a CMMS that aligns with their specific needs. Understanding what features are optional for this group is crucial because it allows them to invest their resources wisely and maximize the benefits of a CMMS tailored to their requirements.
TABLE OF CONTENTS
Keep Reading
Ever find yourself checking into a luxury hotel and expecting a relaxing stay, only to find a ...
11 Apr 2025
Organizations are witnessing swift changes in the business environment and confronting a ...
8 Apr 2025
Last month, news outlets and the entire internet was abuzz with the return of NASA astronauts ...
3 Apr 2025
What comes first - CMMS or predictive maintenance? If your answer is either, it is correct. ...
28 Mar 2025
Artificial intelligence (AI) talk has become commonplace. Today, engaging in business-focused ...
27 Mar 2025
Imagine a world where machines predict, diagnose, and fix their issues before they fail. This ...
25 Mar 2025
A facility maintenance plan is at the core of a facility’s operations. This organized ...
21 Mar 2025
Think of managing your maintenance operations like managing a championship sports team. Just ...
21 Mar 2025
The maintenance sector is battling a severe talent shortage that threatens to undermine ...
7 Mar 2025
Manufacturing maintenance is the backbone of industrial efficiency, ensuring machines run ...
5 Mar 2025
No one likes playing a guessing game when equipment breaks down. Yet, maintenance teams often ...
4 Mar 2025
The size of the preventive maintenance software market is discussed in millions of dollars, ...
4 Mar 2025
The organizational structure and corporate hierarchy vary from company to company. Large ...
28 Feb 2025
Maintenance procedures are essential for ensuring the longevity and reliability of machinery ...
21 Feb 2025
Sustainability is no longer just a buzzword; it's a critical component of corporate social ...
20 Feb 2025
A Computerized Maintenance Management System (CMMS) relies on accurate, well-organized data ...
18 Feb 2025
In an era where technology drives operational efficiency, Computerized Maintenance Management ...
14 Feb 2025
A Computerized Maintenance Management System (CMMS) is a key component of modern maintenance ...
13 Feb 2025
Introduction Maintenance management is the foundation of maintenance operations in industries ...
11 Feb 2025
Introduction A Computerized Maintenance Management System (CMMS) is software designed to help ...
7 Feb 2025