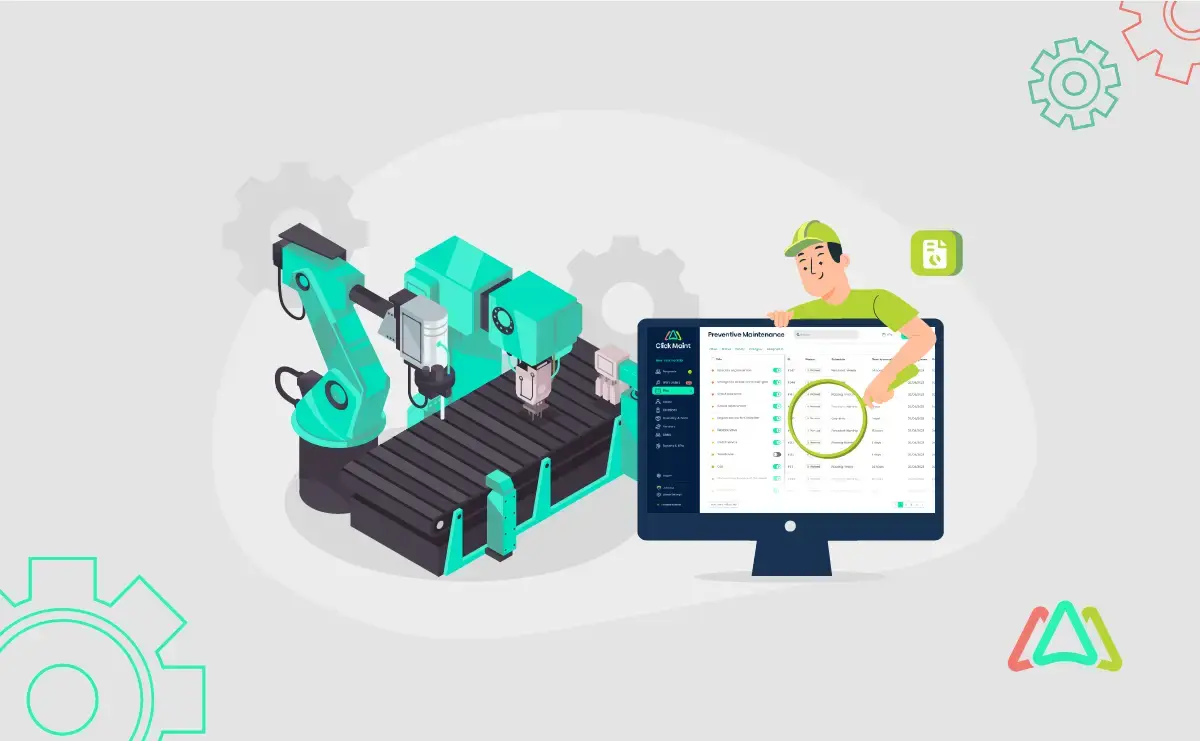
The Role of CMMS in Supporting Additive Manufacturing - Insights for Manufacturing Managers
As a manufacturing manager, you’ve likely heard the term Additive Manufacturing (AM) and some of the buzz around its potential benefits. Additive Manufacturing (AM), also known as 3D printing, is having a huge impact on the manufacturing industry by enabling the creation of complex, customized parts with minimal waste. This cutting-edge technology is reshaping production processes across industries, offering unprecedented flexibility and efficiency. However, to fully harness AM's capabilities, businesses need robust systems in place to manage and optimize manufacturers’ operations. Computerized Maintenance Management Software (CMMS) is helping organizations fill this gap. This article explores how CMMS can support manufacturing businesses' additive manufacturing initiatives by providing valuable insights to enhance productivity, reduce downtime, and maximize the return on AM investments. Discover how integrating CMMS with additive manufacturing can accelerate manufacturing operations’ production capabilities.
Overview of Additive Manufacturing
What is Additive Manufacturing?
Additive manufacturing, also known as 3D printing, is a revolutionary production method that builds three-dimensional objects by depositing materials layer by layer based on digital models. Unlike traditional subtractive manufacturing methods, additive manufacturing offers unprecedented design flexibility, material efficiency and advantages in customization, allowing for the creation of intricate, personalized products. Manufacturers can design complex models that were previously impossible or cost-prohibitive with traditional manufacturing methods.
Here are some of the advantages that AM provides:
- Customization: Tailoring products to specific needs.
- Complex Geometries: Producing intricate designs that are difficult or impossible to achieve with traditional methods.
- Reduced Waste: Using only the material needed for production.
Key Benefits of Additive Manufacturing
One of the most significant benefits of additive manufacturing is its ability to reduce waste. Unlike subtractive methods that cut away excess material, 3D printing uses only the necessary amount of raw materials. This efficiency not only minimizes environmental impact but also reduces costs associated with material waste, as only the necessary amount is used in the printing process. By leveraging additive manufacturing, businesses can produce highly specialized parts, prototype rapidly, and streamline businesses’ production processes, giving them a competitive edge in today's fast-paced manufacturing landscape. Additionally, additive manufacturing allows for rapid prototyping and iterative design, dramatically shortening product development cycles.
In short, additive manufacturing helps in:
- Rapid prototyping and iteration
- Customization and complex geometries
- Reduced waste and material costs
- On-demand production capabilities
Industry Applications
Additive manufacturing has found applications across various sectors, including aerospace, automotive, healthcare, and consumer goods. From lightweight aircraft components to personalized medical implants, this technology is pushing the boundaries of what's possible in manufacturing.
Cost-Effective Production
For small batch sizes or customized products, 3D printing can be more cost-effective than traditional manufacturing methods. Businesses benefit from reduced tooling costs and increased flexibility in production scheduling.
Supply Chain Optimization
Additive manufacturing can streamline businesses’ supply chains by enabling on-demand production and reducing inventory costs. This technology allows businesses to print spare parts as needed, minimizing storage requirements and improving overall efficiency. As the technology continues to evolve, manufacturing managers must stay informed about its potential impact on their operations and supply chains.
Understanding the Challenges of Additive Manufacturing
Additive manufacturing, while revolutionary, presents unique challenges for manufacturing managers. The process requires frequent calibration and maintenance, often leading to extended machine downtime. This downtime risk can significantly impact production schedules and overall efficiency.
Calibration and Maintenance Demands
3D printers need regular fine-tuning to maintain precision. This includes adjusting build platforms, nozzle alignments, and material feed systems. Such frequent interventions can disrupt workflows and require specialized skills.
Complexity in Maintenance Planning
The intricate nature of additive manufacturing equipment complicates maintenance planning. Each printer model may have unique requirements, and the rapid evolution of technology means maintenance protocols must constantly adapt. This complexity demands a robust system to track maintenance schedules, manage spare parts inventories, and coordinate technician expertise.
Equipment Maintenance
Additive manufacturing presents unique maintenance challenges. 3D printers require precise calibration and frequent upkeep to ensure consistent part quality. Businesses will need to monitor wear on nozzles, build platforms, and other components that directly impact print accuracy.
Part Quality Control
Maintaining uniform part quality across production runs can be difficult. Manufacturers must carefully control factors like material properties, print settings, and post-processing to achieve repeatable results. Implementing robust quality assurance processes is key.
Integration with Existing Systems
Incorporating additive manufacturing into businesses' current production workflow isn't always seamless. Manufacturers may face hurdles in aligning new 3D printing processes with traditional manufacturing methods, inventory systems, and quality control protocols. Careful planning is essential to ensure smooth integration and maximize efficiency gains.
Challenges of Additive Manufacturing Specific to Manufacturing Managers
As additive manufacturing (AM) gains traction, managers face some challenges. Quality control becomes paramount, as 3D-printed parts must meet stringent standards. Ensuring consistency across batches can be difficult due to variations in raw materials and printing conditions.
Material management presents another challenge. The diverse range of printable materials, each with specific storage and handling requirements, demands meticulous inventory control. Additionally, equipment maintenance is critical, as AM machines require regular calibration and upkeep to maintain precision. Managers must also grapple with workflow optimization. Integrating AM into existing production lines while maximizing efficiency can be complex. Finally, regulatory compliance poses ongoing challenges, particularly in industries like aerospace and healthcare, where AM parts must meet strict safety and quality standards.
How CMMS Supports Additive Manufacturing Operations
A Computerized Maintenance Management System (CMMS) plays a crucial role in optimizing additive manufacturing processes. A CMMS is designed to streamline maintenance tasks, improve equipment uptime, and enhance overall operational efficiency.
Here’s how a CMMS supports additive manufacturing:
1. Scheduled Maintenance
Statistics: According to a study by the Aptean, companies with effective CMMS systems experience up to a 20% reduction in equipment downtime.
Example: By integrating CMMS software, businesses can effectively track and manage 3D printer maintenance schedules, ensuring optimal performance and minimizing downtime. A CMMS can schedule regular maintenance for AM machines, ensuring they operate optimally. For instance, if an additive manufacturing printer requires calibration every 500 hours of operation, the CMMS can automatically alert maintenance staff to perform this task.
2. Real-Time Monitoring
By implementing real-time monitoring and scheduled maintenance, manufacturers can prevent costly downtime and ensure consistent print quality. The ability to monitor equipment in real-time can reduce overall maintenance costs by up to 30% (Source: Accenture Research).
Example: The system allows businesses to monitor material usage, helping to maintain adequate inventory levels for uninterrupted production. A CMMS integrated with IoT sensors can provide real-time data on the performance of equipment. If a sensor detects an anomaly in temperature or pressure, the system can trigger an immediate maintenance request, preventing potential breakdowns.
3. Inventory Management
CMMS software streamlines inventory management, ensuring that raw materials and replacement parts are always available. This is particularly important in additive manufacturing, where material consistency is critical. Efficient inventory management through a CMMS can reduce spare parts costs by up to 15% (Source: g3p consulting).
Example: Managing the inventory of AM materials and spare parts is crucial. A CMMS can track inventory levels, forecast future needs, and automatically reorder supplies when they fall below a certain threshold, ensuring uninterrupted production.
4. Historical and Real-Time Data Analysis
The system's data-driven decision-making capabilities enable managers to identify trends, optimize production schedules, and enhance overall efficiency. Analyzing historical maintenance data can improve equipment uptime by as much as 51% (Source: Intellicus from kyvos).
Example: With real-time data analytics, businesses can identify bottlenecks in their additive manufacturing workflow and make data-driven decisions to improve efficiency. By analyzing maintenance records and performance data, manufacturers can identify recurring issues with AM equipment. For instance, if a specific printer model consistently requires adjustments, this data can guide preventive measures to address the root cause.
5. Enhanced Reporting and Compliance
Additionally, the system's robust reporting features aid in maintaining preventive maintenance compliance with industry standards and regulations, providing a comprehensive audit trail for quality assurance purposes.
Improved reporting capabilities can boost efficiency of predictive maintenance and prevent up to 82% of typical asset failures. (Source: Forbes).
Example: Additionally, a CMMS helps businesses with asset lifecycle management, from design to disposal, facilitating quality control and regulatory compliance. A CMMS provides comprehensive reports on maintenance activities, equipment performance, and downtime. These insights help manufacturing managers make informed decisions about process improvements and resource allocation.
Ultimately, implementing a CMMS in manufacturers’ additive manufacturing operations can lead to increased productivity, reduced costs, and enhanced product quality.
Essential CMMS Features for Additive Manufacturing
Inventory Management
In additive manufacturing, efficient inventory management is crucial. A robust CMMS system for manufacturing helps track raw materials, such as powders and filaments, ensuring optimal stock levels. This feature prevents production delays and reduces waste, ultimately improving operational efficiency.
Equipment Monitoring
CMMS platforms offer real-time monitoring of 3D printers and related equipment. By tracking machine performance, maintenance schedules, and operational data, managers can proactively address issues before they escalate. This predictive approach minimizes downtime and extends the lifespan of expensive additive manufacturing equipment.
Quality Control Integration
Advanced CMMS solutions integrate seamlessly with quality control processes. By recording and analyzing production data, these systems help maintain consistency in 3D-printed parts. This feature is especially valuable in industries with strict quality standards, such as aerospace and medical device manufacturing.
Case Studies of CMMS Improving Additive Manufacturing
Streamlined Operations at Siemens and GE
Companies like Siemens and GE implemented a CMMS to manage their additive manufacturing processes, resulting in a 60% faster repair time for burner tips and a 90% reduction in repair time for turbines. The system's predictive maintenance capabilities allowed them to anticipate potential issues before they occurred, minimizing disruptions to production schedules.
Enhanced Quality Control in Inkjet Technology
The liquid binder jet device company utilized CMMS to track and analyze data from their 3D inkjet technology. This led to a 40% decrease in defective parts and a 20% improvement in first-pass yield, along with design freedom. High print speed and large build volume at a relatively low cost. The system's real-time monitoring and reporting features enabled quick identification and resolution of quality issues, ensuring consistent product excellence.
Conclusion
In conclusion, implementing a robust CMMS is crucial for manufacturing managers looking to optimize additive manufacturing processes. By leveraging real-time data, predictive maintenance, and streamlined workflows, businesses can significantly enhance operational efficiency, reduce downtime, and improve product quality. As the additive manufacturing industry continues to evolve, staying ahead of the curve with advanced CMMS solutions will be key to maintaining a competitive edge. By embracing these technologies and best practices, businesses will be well-positioned to drive innovation, reduce costs, and meet the ever-changing demands of the market. Take the next step in the additive manufacturing journey by exploring how a CMMS can transform businesses’ operations today.
TABLE OF CONTENTS
- Overview of Additive Manufacturing
- Industry Applications
- Understanding the Challenges of Additive Manufacturing
- Challenges of Additive Manufacturing Specific to Manufacturing Managers
- How CMMS Supports Additive Manufacturing Operations
- Essential CMMS Features for Additive Manufacturing
- Case Studies of CMMS Improving Additive Manufacturing
- Conclusion
Keep Reading
Introduction Maintenance management is the foundation of maintenance operations in industries ...
11 Feb 2025
Introduction A Computerized Maintenance Management System (CMMS) is software designed to help ...
7 Feb 2025
Ever find yourself checking into a luxury hotel and expecting a relaxing stay, only to find a ...
11 Apr 2025
Organizations are witnessing swift changes in the business environment and confronting a ...
8 Apr 2025
Last month, news outlets and the entire internet was abuzz with the return of NASA astronauts ...
3 Apr 2025
What comes first - CMMS or predictive maintenance? If your answer is either, it is correct. ...
28 Mar 2025
Artificial intelligence (AI) talk has become commonplace. Today, engaging in business-focused ...
27 Mar 2025
Imagine a world where machines predict, diagnose, and fix their issues before they fail. This ...
25 Mar 2025
A facility maintenance plan is at the core of a facility’s operations. This organized ...
21 Mar 2025
Think of managing your maintenance operations like managing a championship sports team. Just ...
21 Mar 2025
The maintenance sector is battling a severe talent shortage that threatens to undermine ...
7 Mar 2025
Manufacturing maintenance is the backbone of industrial efficiency, ensuring machines run ...
5 Mar 2025
No one likes playing a guessing game when equipment breaks down. Yet, maintenance teams often ...
4 Mar 2025
The size of the preventive maintenance software market is discussed in millions of dollars, ...
4 Mar 2025
The organizational structure and corporate hierarchy vary from company to company. Large ...
28 Feb 2025
Maintenance procedures are essential for ensuring the longevity and reliability of machinery ...
21 Feb 2025
Sustainability is no longer just a buzzword; it's a critical component of corporate social ...
20 Feb 2025
A Computerized Maintenance Management System (CMMS) relies on accurate, well-organized data ...
18 Feb 2025
In an era where technology drives operational efficiency, Computerized Maintenance Management ...
14 Feb 2025
A Computerized Maintenance Management System (CMMS) is a key component of modern maintenance ...
13 Feb 2025
Introduction Maintenance management is the foundation of maintenance operations in industries ...
11 Feb 2025
Introduction A Computerized Maintenance Management System (CMMS) is software designed to help ...
7 Feb 2025
Ever find yourself checking into a luxury hotel and expecting a relaxing stay, only to find a ...
11 Apr 2025
Organizations are witnessing swift changes in the business environment and confronting a ...
8 Apr 2025
Last month, news outlets and the entire internet was abuzz with the return of NASA astronauts ...
3 Apr 2025
What comes first - CMMS or predictive maintenance? If your answer is either, it is correct. ...
28 Mar 2025
Artificial intelligence (AI) talk has become commonplace. Today, engaging in business-focused ...
27 Mar 2025
Imagine a world where machines predict, diagnose, and fix their issues before they fail. This ...
25 Mar 2025
A facility maintenance plan is at the core of a facility’s operations. This organized ...
21 Mar 2025
Think of managing your maintenance operations like managing a championship sports team. Just ...
21 Mar 2025
The maintenance sector is battling a severe talent shortage that threatens to undermine ...
7 Mar 2025
Manufacturing maintenance is the backbone of industrial efficiency, ensuring machines run ...
5 Mar 2025
No one likes playing a guessing game when equipment breaks down. Yet, maintenance teams often ...
4 Mar 2025
The size of the preventive maintenance software market is discussed in millions of dollars, ...
4 Mar 2025
The organizational structure and corporate hierarchy vary from company to company. Large ...
28 Feb 2025
Maintenance procedures are essential for ensuring the longevity and reliability of machinery ...
21 Feb 2025
Sustainability is no longer just a buzzword; it's a critical component of corporate social ...
20 Feb 2025
A Computerized Maintenance Management System (CMMS) relies on accurate, well-organized data ...
18 Feb 2025
In an era where technology drives operational efficiency, Computerized Maintenance Management ...
14 Feb 2025
A Computerized Maintenance Management System (CMMS) is a key component of modern maintenance ...
13 Feb 2025
Introduction Maintenance management is the foundation of maintenance operations in industries ...
11 Feb 2025
Introduction A Computerized Maintenance Management System (CMMS) is software designed to help ...
7 Feb 2025