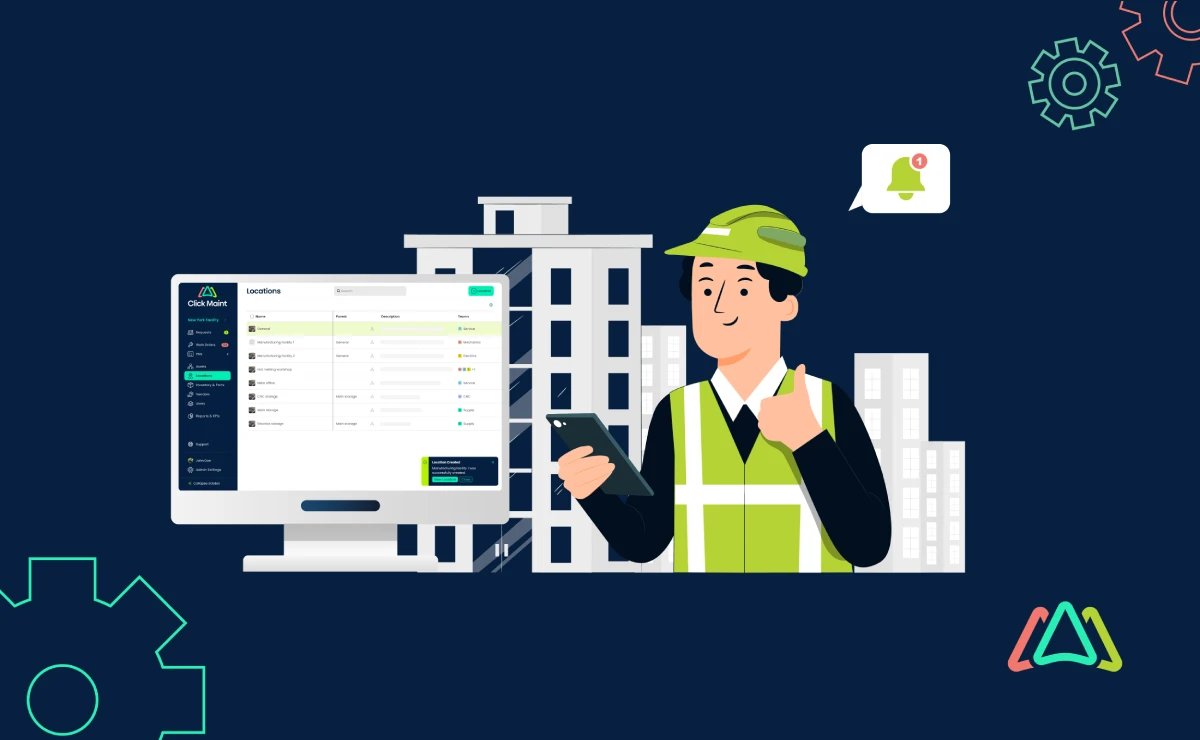
Optimizing Building Maintenance Management with CMMS
Effective building maintenance management is important for several reasons. Firstly, well-maintained facilities contribute to a safe and comfortable environment for occupants, whether they are employees, tenants, or customers. Regular maintenance also helps to extend the lifespan of building assets, reducing the need for costly repairs or replacements in the long run.
Moreover, preventative maintenance can enhance energy efficiency and sustainability, leading to lower operational costs and a reduced environmental footprint. From a regulatory standpoint, maintaining compliance with safety and health standards is essential for avoiding fines and legal liabilities.
In essence, building maintenance is not just about fixing things when they break; it's about implementing a strategic approach to ensure the smooth operation and longevity of the facility environment.
10 Benefits of Using CMMS for Building Maintenance
A Computerized Maintenance Management System (CMMS) empowers building managers, facility supervisors, and other maintenance professionals involved in building maintenance by offering a plethora of benefits such as ensuring the smooth operation and longevity of facilities. Following are some of the advantages of leveraging CMMS for building maintenance:
1. Streamlined Maintenance Processes
CMMS software centralizes all maintenance-related tasks and data in one digital platform, eliminating the need for manual record-keeping and disparate spreadsheets. This streamlines processes such as work order management, preventive maintenance scheduling, and inventory tracking, enabling maintenance teams to operate more efficiently.
2. Improved Asset Management
With CMMS, building managers gain comprehensive visibility into their assets, including equipment, machinery, and infrastructure. Asset lifecycle management and tracking maintenance history, and performance metrics in real-time becomes much easier facilitating informed decision-making regarding repair, replacement, or upgrades.
3. Enhanced Preventive Maintenance
CMMS empowers organizations to adopt a proactive approach to maintenance by implementing preventive maintenance schedules based on asset condition, usage patterns, and manufacturer recommendations. By addressing issues before they escalate, organizations can minimize downtime, extend asset lifespan, and reduce costly repairs.
4. Optimized Resource Allocation
CMMS facilitates better resource allocation by providing insights into labor, materials, and equipment requirements for maintenance tasks. Maintenance teams can allocate resources more effectively, prioritize urgent work orders, and minimize downtime, ultimately improving operational efficiency and cost-effectiveness.
5. Increased Regulatory Compliance
Compliance with safety, health, and environmental regulations is paramount for building managers. CMMS helps organizations maintain compliance by documenting maintenance activities, inspections, and audits, ensuring adherence to regulatory requirements and mitigating legal risks.
6. Data-Driven Decision-Making
CMMS generates comprehensive reports and analytics on maintenance performance, asset reliability, and resource utilization. By analyzing these insights, organizations can identify trends, pinpoint areas for improvement, and make data-driven decisions to optimize maintenance strategies and maximize efficiency.
7. Enhanced Communication and Collaboration
CMMS facilitates seamless communication and collaboration among maintenance teams, supervisors, and other stakeholders. Users can create, assign, and track work orders in real-time, share updates and notes, and access information remotely via mobile devices, fostering greater transparency and accountability.
8. Improved Inventory Management
CMMS includes inventory tracking and management functionalities, allowing organizations to maintain optimal stock levels of spare parts and materials. By monitoring inventory usage, reordering supplies, and reducing stockouts, organizations can minimize downtime and ensure timely completion of maintenance tasks.
9. Scalability and Flexibility
Whether managing a single facility or a portfolio of properties, CMMS offers scalability and flexibility to accommodate varying needs and requirements. Organizations can customize workflows, add or remove users, and integrate with other systems, ensuring that CMMS evolves alongside their business.
10. Cost Savings
Ultimately, the implementation of CMMS translates into cost savings for organizations. By optimizing maintenance processes, reducing downtime, extending asset lifespan, and minimizing costly repairs, CMMS helps organizations maximize operational efficiency and achieve a higher return on investment (ROI).
8 Key CMMS Features for Building Maintenance
1. Equipment Management
- Centralized database to catalog and track all building assets, including equipment, machinery, and infrastructure.
- Detailed asset profiles containing essential information such as maintenance history, specifications, and criticality ratings.
- Asset hierarchy functionality for organizing assets into logical groupings based on location, system, or function.
2. Preventive Maintenance
- Automated scheduling of preventive maintenance tasks based on time, usage, or condition thresholds.
- Task templates and recurring maintenance plans to streamline the creation of preventive maintenance schedules.
- Reminder notifications and alerts to ensure timely execution of scheduled maintenance activities.
3. Work Order Management
- Creation, assignment, tracking, and closure of work orders for maintenance tasks, repairs, and inspections.
- Prioritization of work orders based on urgency, criticality, and impact on operations.
- Real-time updates and status tracking to monitor the progress of work orders from initiation to completion.
4. Inventory Management
- Inventory tracking and stock level monitoring for spare parts, consumables, and maintenance supplies.
- Automated reorder points and replenishment notifications to prevent stockouts and ensure availability of necessary items.
- Integration with procurement systems to streamline the purchasing and replenishment process.
5. Mobile Accessibility
- Mobile-friendly interface and native mobile applications to enable technicians to access CMMS functionalities on smartphones and tablets.
- Offline capabilities for technicians working in remote locations or areas with limited connectivity.
- QR code scanning and photo attachments for easy documentation and identification of assets and inventory items.
6. Reporting and Analytics
- Comprehensive reporting tools to generate maintenance performance metrics, KPIs, and trend analyses.
- Customizable dashboards and data visualization tools to present information in a clear and actionable format.
- Historical data tracking and trend analysis to identify patterns, predict maintenance needs, and optimize resource allocation.
7. Integration Capabilities
- Seamless integration with other systems such as IoT sensors, Building Management Systems (BMS), and Enterprise Resource Planning (ERP) software.
- Data exchange and interoperability to facilitate automated data collection, analysis, and reporting.
- API (Application Programming Interface) access for developers to build custom integrations with third-party applications and platforms.
8. Regulatory Compliance
- Documentation management and audit trail capabilities to maintain compliance with industry regulations, safety standards, and best practices.
- Automated record-keeping and documentation of maintenance activities for regulatory inspections and audits.
- Notification alerts for upcoming inspections, certifications, and compliance deadlines to ensure timely completion of required tasks.
Implementing CMMS for Building Maintenance
Effective CMMS implementation is essential for optimizing building maintenance processes and achieving operational efficiency.
1. Assessing Maintenance Needs and Requirements
Before selecting and implementing a CMMS solution, it's essential to conduct a thorough assessment of your organization's maintenance needs and requirements. This involves:
- Inventorying Assets: Identify all building assets requiring maintenance, including equipment, systems, and infrastructure. Assess their criticality, maintenance history, and performance metrics.
- Analyzing Maintenance Workflows: Evaluate existing maintenance workflows and processes to identify pain points, inefficiencies, and areas for improvement. Determine the types of maintenance tasks performed, frequency, and resource requirements.
- Assessing Regulatory Compliance: Determine the regulatory requirements and industry standards applicable to your building maintenance operations. Ensure that the selected CMMS solution supports compliance documentation and reporting.
- Identifying Key Stakeholders: Involve key stakeholders, including maintenance technicians, supervisors, facility managers, and IT personnel, in the assessment process. Gather feedback and insights from end-users to ensure the selected CMMS meets their needs and preferences.
- Defining Objectives and Success Criteria: Establish clear objectives and success criteria for the CMMS implementation project. Determine the desired outcomes, such as improved asset reliability, reduced downtime, and increased operational efficiency.
By conducting a comprehensive assessment of maintenance needs and requirements, you can lay the foundation for a successful CMMS implementation that aligns with your organization's goals and objectives.
2. Selecting the Right CMMS Solution
Selecting the right CMMS solution is a critical decision that requires careful consideration of various factors. Here's how to choose the best CMMS solution for your building maintenance needs:
- Define Selection Criteria: Create a list of selection criteria based on your organization's requirements, such as functionality, scalability, ease of use, cost, vendor reputation, and customer support.
- Research Available Options: Research and evaluate CMMS solutions available in the market. Consider factors such as industry-specific features, deployment options (cloud-based vs. on-premises), and compatibility with existing systems. Check out our list of top 10 CMMS Software.
- Request Demos and Trials: Schedule demos and request trial access to potential CMMS solutions to evaluate their usability, features, and performance. Involve key stakeholders in the evaluation process to gather feedback and insights.
- Assess Vendor Reputation: Assess the reputation and track record of CMMS vendors, including their experience in the industry, customer reviews, and case studies. Word of month and software listing websites like G2 and Capterra can help with comparing available options. Choose a vendor with a proven track record of successful implementations and ongoing support.
- Consider Integration Capabilities: Ensure that the selected CMMS solution offers integration capabilities with other systems and software used in your organization, such as ERP systems, IoT devices, and building automation systems.
- Evaluate Total Cost of Ownership: Consider the total cost of ownership, including upfront costs, subscription fees, implementation costs, and ongoing maintenance and support fees. Choose a solution that offers the best value for your budget.
By selecting the right CMMS solution that aligns with your organization's needs and objectives, you can lay the foundation for a successful implementation that delivers tangible benefits and ROI.
3. Customization and Configuration for Specific Maintenance Tasks and Workflows
Once you've selected a CMMS solution, the next step is to customize and configure it to meet your specific maintenance tasks and workflows. Here's how to tailor the CMMS to your organization's needs:
- Define Custom Fields and Data Attributes: Customize the CMMS by defining custom fields and data attributes to capture relevant information specific to your maintenance tasks and assets. This may include equipment specifications, maintenance procedures, and regulatory compliance requirements.
- Configure Workflows and Processes: Configure workflows and processes within the CMMS to mirror your organization's maintenance procedures. Define roles, responsibilities, and approval workflows for creating, assigning, and completing work orders.
- Set Up Preventive Maintenance Schedules: Set up preventive maintenance schedules based on asset criticality, usage patterns, and manufacturer recommendations. Define maintenance tasks, frequencies, and notification alerts to ensure timely execution.
- Import Data and Assets: Import existing asset data, maintenance records, and inventory information into the CMMS to populate the database. Ensure data accuracy and consistency in CMMS data import by cleansing and validating data before importing.
- Provide User Training and Support: Train maintenance technicians, supervisors, and other users on how to use the CMMS effectively. Provide hands-on training sessions, user manuals, and ongoing support to ensure a smooth transition and adoption.
By customizing and configuring the CMMS to align with your organization's maintenance tasks and workflows, you can maximize its effectiveness and realize the full benefits of automation, efficiency, and reliability in building maintenance management.
2 Key Components of Setting Up Your CMMS for Success
1. Data Entry and Asset Management in Building Maintenance
Effective data entry and asset management are foundational elements of CMMS implementation for building maintenance. Here's how to ensure success in this area:
- Centralized Data Storage: Begin by centralizing all relevant maintenance data within the CMMS. This includes asset information, maintenance histories, work orders, and inventory records. Ensure that data is accurately entered and organized in a logical structure for easy retrieval.
- Comprehensive Asset Profiles: Create detailed profiles for each building asset within the CMMS. Include key information such as asset name, description, location, serial number, manufacturer details, warranty information, and maintenance history. Attach relevant documentation and schematics to asset profiles for reference.
- Asset Hierarchy Setup: Establish an asset hierarchy within the CMMS to categorize assets based on their relationship and hierarchy within the building structure. This hierarchy helps organize assets into logical groupings, making it easier to manage and track maintenance activities.
- Standardized Naming Conventions: Implement standardized naming conventions for assets and equipment to ensure consistency and clarity across the CMMS. Use descriptive and intuitive names that facilitate easy identification and searchability.
- Data Validation and Quality Assurance: Regularly review and validate data entered into the CMMS to ensure accuracy and completeness. Implement quality assurance processes to identify and correct any discrepancies or inconsistencies in asset information.
By prioritizing data entry and asset management within your CMMS, you can establish a solid foundation for efficient building maintenance operations and ensure that all relevant information is readily accessible when needed.
2. Establishing Preventive Maintenance Schedules for Facility Management
Preventive maintenance is essential for proactively addressing potential issues before they escalate into costly problems. Here's how to establish preventive maintenance schedules effectively within your CMMS:
- Asset Prioritization: Begin by prioritizing assets based on criticality, usage frequency, and impact on operations. Identify high-priority assets that require regular preventive maintenance to maintain optimal performance and reliability.
- Maintenance Task Identification: Identify the specific maintenance tasks and inspections required for each asset to prevent potential failures or breakdowns. This may include routine inspections, lubrication, calibration, cleaning, and component replacements.
- Frequency Determination: Determine the frequency at which preventive maintenance tasks should be performed based on factors such as manufacturer recommendations, industry best practices, and asset performance data. Adjust frequencies as needed based on asset condition and usage patterns.
- Schedule Creation: Use the scheduling features within the CMMS to create preventive maintenance schedules for each asset. Define the frequency, start date, duration, and recurrence pattern for each maintenance task to ensure timely execution.
- Notification and Alert Setup: Configure notification alerts within the CMMS to remind maintenance personnel of upcoming preventive maintenance tasks. Ensure that notifications are sent to the appropriate individuals or teams well in advance to allow for adequate preparation and planning.
- Documentation and Record-Keeping: Document all preventive maintenance activities within the CMMS, including task completion dates, technician notes, and any issues identified during inspections. Maintain comprehensive maintenance records for each asset to track maintenance history and compliance with regulatory requirements.
By establishing preventive maintenance schedules within your CMMS, you can proactively manage building assets, minimize downtime, and extend equipment lifespan, ultimately optimizing facility performance and reducing operational costs.
Setting up your CMMS for success requires careful planning, attention to detail, and a commitment to data accuracy and process efficiency. By focusing on data entry, asset management, and preventive maintenance scheduling, you can leverage the full capabilities of your CMMS to streamline building maintenance operations and achieve long-term success.
TABLE OF CONTENTS
Keep Reading
Ever find yourself checking into a luxury hotel and expecting a relaxing stay, only to find a ...
11 Apr 2025
Organizations are witnessing swift changes in the business environment and confronting a ...
8 Apr 2025
Last month, news outlets and the entire internet was abuzz with the return of NASA astronauts ...
3 Apr 2025
What comes first - CMMS or predictive maintenance? If your answer is either, it is correct. ...
28 Mar 2025
Artificial intelligence (AI) talk has become commonplace. Today, engaging in business-focused ...
27 Mar 2025
Imagine a world where machines predict, diagnose, and fix their issues before they fail. This ...
25 Mar 2025
A facility maintenance plan is at the core of a facility’s operations. This organized ...
21 Mar 2025
Think of managing your maintenance operations like managing a championship sports team. Just ...
21 Mar 2025
The maintenance sector is battling a severe talent shortage that threatens to undermine ...
7 Mar 2025
Manufacturing maintenance is the backbone of industrial efficiency, ensuring machines run ...
5 Mar 2025
No one likes playing a guessing game when equipment breaks down. Yet, maintenance teams often ...
4 Mar 2025
The size of the preventive maintenance software market is discussed in millions of dollars, ...
4 Mar 2025
The organizational structure and corporate hierarchy vary from company to company. Large ...
28 Feb 2025
Maintenance procedures are essential for ensuring the longevity and reliability of machinery ...
21 Feb 2025
Sustainability is no longer just a buzzword; it's a critical component of corporate social ...
20 Feb 2025
A Computerized Maintenance Management System (CMMS) relies on accurate, well-organized data ...
18 Feb 2025
In an era where technology drives operational efficiency, Computerized Maintenance Management ...
14 Feb 2025
A Computerized Maintenance Management System (CMMS) is a key component of modern maintenance ...
13 Feb 2025
Introduction Maintenance management is the foundation of maintenance operations in industries ...
11 Feb 2025
Introduction A Computerized Maintenance Management System (CMMS) is software designed to help ...
7 Feb 2025