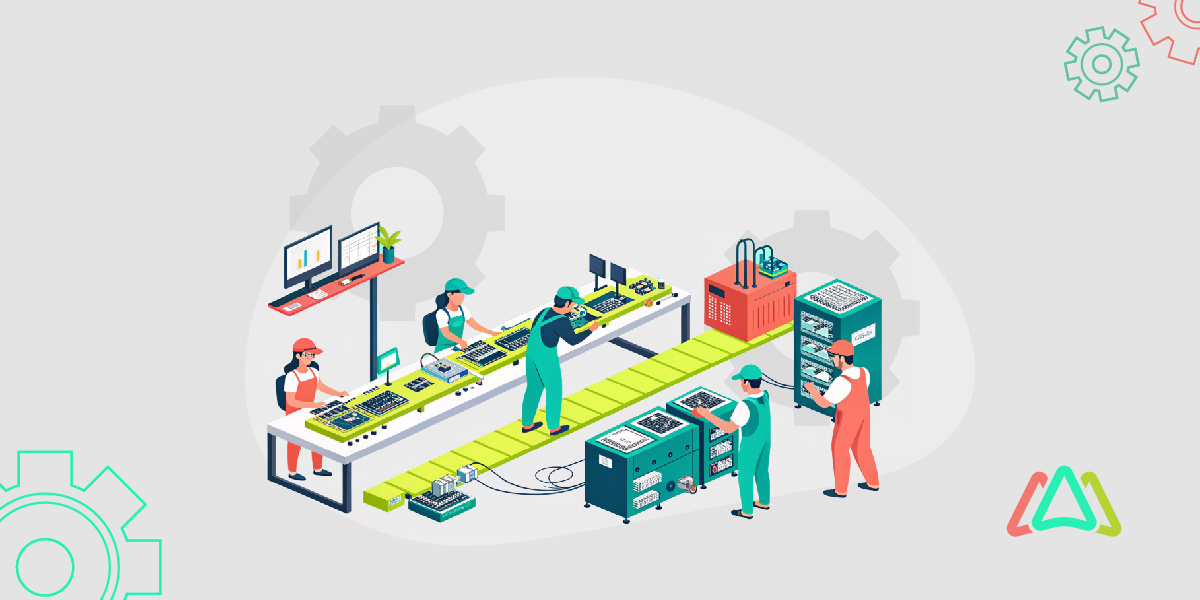
CMMS for Discrete Manufacturing or Process Manufacturing
Maintenance challenges are a constant struggle, with unplanned downtime costing manufacturers an average of $260,000 per hour, according to industry studies. Addressing these challenges requires more than just reactive fixes; it demands a proactive, data-driven approach using a CMMS. In manufacturing, efficiency, and reliability are non-negotiable. However, when it comes to maintenance management, does discrete manufacturing or process manufacturing benefit more from a Computerized Maintenance Management System (CMMS)?
In this article, we take a deep dive into the role of CMMS in both discrete and process manufacturing, compare their unique needs, and explore shared advantages. You’ll discover the challenges CMMS addresses, factors to consider when choosing a solution, and why Click Maint excels in adapting to both manufacturing types.
By the end, you’ll have a clear understanding of how to evaluate CMMS for your specific industry and the benefits it offers. Whether you're optimizing assembly lines or refining raw materials, this guide will provide actionable insights to help you leverage CMMS effectively. So, is one manufacturing style truly better suited for CMMS?
What is Discrete Manufacturing?
Discrete manufacturing involves the production of individual, countable items such as cars, electronics, or furniture. Each product is distinct, often assembled from multiple components, and can be easily disassembled if necessary. Industries like automotive, aerospace, and consumer goods are prominent examples. However, maintenance in discrete manufacturing presents unique challenges, including managing diverse equipment types, scheduling maintenance during frequent production changes, and ensuring minimal disruption to assembly lines.
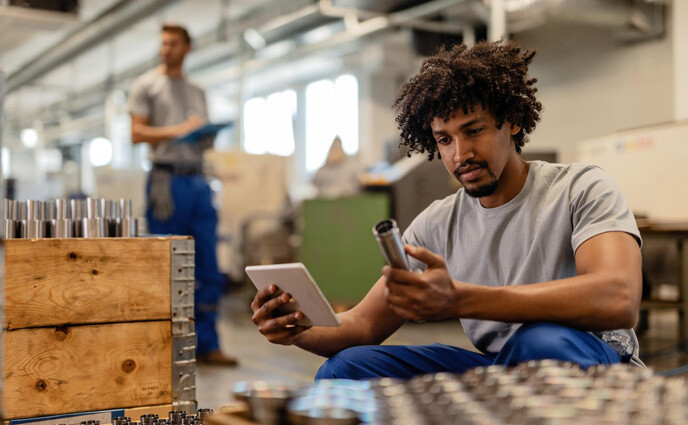
What is Process Manufacturing?
Process manufacturing produces goods in bulk through chemical, biological, or mechanical processes, such as food, beverages, or pharmaceuticals. Unlike discrete products, these outputs cannot be disassembled. Industries like oil & gas, food processing, and pharmaceuticals heavily rely on process manufacturing. Key maintenance challenges include ensuring equipment reliability for continuous production, adhering to strict regulatory requirements, and minimizing downtime to prevent costly disruptions.
The Role of CMMS in Manufacturing
A Computerized Maintenance Management System (CMMS) is a powerful tool that streamlines maintenance operations, ensuring smoother manufacturing processes. It centralizes data, providing an accessible hub for equipment information, maintenance schedules, and inventory tracking. With CMMS software, manufacturers can schedule preventive and predictive maintenance, minimizing unplanned downtime and improving overall equipment reliability. Additionally, CMMS generates compliance and operational reports, aiding in regulatory adherence and performance analysis.
CMMS Software for manufacturing is essential for both types of manufacturing - discrete and process. For discrete manufacturing, it simplifies the maintenance of diverse equipment types and adapts to frequent production shifts. Conversely, in process manufacturing, CMMS ensures continuous operations, prevents costly downtime, and meets stringent regulatory standards. By enabling proactive maintenance and real-time data analysis, CMMS empowers manufacturers to achieve higher productivity, lower costs, and improved product quality across all operations.
CMMS in Discrete vs. Process Manufacturing - Comparative Analysis
Aspect |
CMMS in Discrete Manufacturing |
CMMS in Process Manufacturing |
Which Benefits More? |
---|---|---|---|
Equipment and Asset Tracking |
Offers detailed tracking for a wide range of individual equipment. |
Ensures consistent monitoring of assets in continuous production lines. |
Both benefit equally, though discrete manufacturing requires more flexibility due to equipment diversity. |
Maintenance Needs |
Manages diverse machines with varying maintenance schedules and needs. |
Predictive maintenance helps prevent contamination and ensures quality. |
Process manufacturing benefits more due to its reliance on continuous uptime and quality control. |
Adaptability |
Excels in adapting to frequent product design or production line changes. |
Maintains stable operations in formula-driven, less dynamic processes. |
Discrete manufacturing benefits more due to its dynamic production environment. |
Regulatory Compliance |
Tracks and logs maintenance activities for industry compliance. |
Automates documentation for strict regulatory standards. |
Process manufacturing benefits more due to the stringent nature of its regulatory environment. |
Downtime Management |
Minimizes disruptions during changeovers or maintenance windows. |
Prevents costly downtime in continuous production environments. |
Process manufacturing benefits more because downtime directly impacts production volume and quality. |
Shared Benefits
Both discrete and process manufacturing operations share significant advantages when utilizing a CMMS. One of the standout benefits is scalability, which allows the system to seamlessly accommodate businesses of varying sizes, from small-scale manufacturers to large enterprises. Additionally, CMMS consistently reduces maintenance costs by enhancing efficiency and minimizing unplanned downtime, ensuring smoother operations across the board.
Furthermore, the use of real-time data empowers both types of manufacturers to make informed decisions. This data-driven approach optimizes asset performance and facilitates strategic operational planning, making CMMS an invaluable tool in any manufacturing setting.
Challenges of CMMS
Challenge |
Impact on Discrete Manufacturing |
Impact on Process Manufacturing |
Solutions |
---|---|---|---|
Initial Investment |
High upfront cost, particularly for small or medium-sized manufacturers. |
Significant cost due to integration with continuous processes. |
Highlight ROI and offer phased implementations to reduce financial strain. |
Learning Curve |
Training required to handle diverse equipment and frequent schedule changes. |
Training needed for regulatory-heavy industries with complex processes. |
Comprehensive user training and vendor support can ease the transition. |
System Integration |
Complexity arises from the need to integrate CMMS with dynamic workflows. |
Customization may be needed to fit process-specific requirements. |
Partnering with CMMS vendors for tailored solutions ensures smoother integration. |
Key Takeaway
While discrete manufacturing benefits from CMMS’s adaptability and asset tracking, process manufacturing often gains a greater advantage due to the critical need for uptime, quality control, and compliance. The final decision should hinge on your business priorities, whether flexibility or regulatory adherence is your primary concern.
How to Choose the Right CMMS for Your Manufacturing Needs
Choosing the right CMMS is a critical step in optimizing your maintenance processes. With so many options available, it can be overwhelming to determine which system best aligns with your unique operational needs. Whether you're in discrete manufacturing or process manufacturing, the right CMMS can drive efficiency, minimize downtime, and enhance asset management. In this section, we’ll walk you through the key considerations and features to look for when selecting a solution that will empower your team and support your long-term goals. Let’s explore how the right choice can transform your maintenance strategy and set you on a path to operational excellence.
Factors to Consider
Selecting the right CMMS begins with evaluating the size and complexity of your operations. Larger or more intricate manufacturing environments often require a scalable solution that can adapt to evolving needs. For discrete manufacturing, consider systems that accommodate frequent equipment changeovers, while for process manufacturing, prioritize features that support stringent regulatory compliance. Additionally, assess your budget and expected ROI to ensure the solution aligns with your financial goals and delivers long-term value.
Features to Look For
Look for a CMMS that offers flexibility and customization to cater to your industry’s specific demands, whether it’s managing asset hierarchies in discrete manufacturing or meeting compliance standards in process manufacturing. The system should feature an intuitive, user-friendly interface that simplifies onboarding for your team. Scalability is key. Ensure the CMMS can grow with your business as your operations expand or evolve. This will ensure that as your maintenance needs change, your solution continues to deliver value, optimizing efficiency across your entire operation.
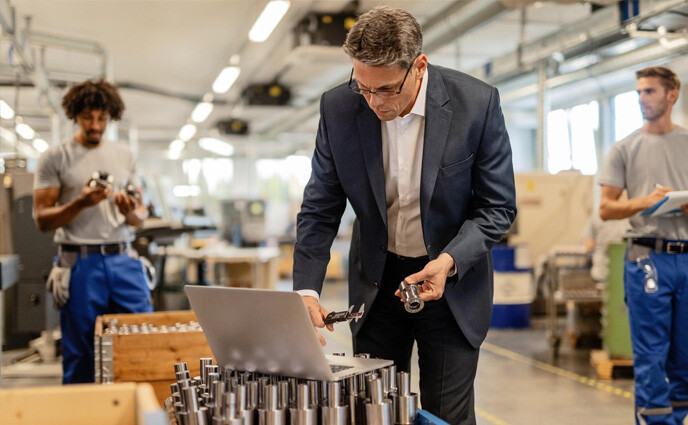
Why Click Maint Excels in Both Manufacturing Types
Click Maint is a user-friendly CMMS solution tailored to meet the maintenance needs of small to mid-sized businesses (SMBs) across both discrete and process manufacturing. Its focus on preventive maintenance and efficient work order management makes it an ideal choice for companies seeking simplicity and scalability.
Seamless Integration and Scalability
Click Maint integrates into existing systems and adapts to operations of varying sizes. Whether tracking parts in discrete manufacturing or managing bulk materials in process manufacturing, its flexibility ensures smooth alignment with unique workflows.
Customizable Workflows
Click Maint’s configurable features cater to the specific needs of manufacturers, such as managing complex BOMs (Bill of Materials) for discrete industries or streamlining flow-based processes in process manufacturing. Its adaptability ensures users can tailor the system to suit their operations.
Practical Analytics for Proactive Maintenance
Click Maint leverages real-time data to support proactive maintenance strategies. Discrete manufacturers can avoid disruptions in assembly lines, while process industries can ensure continuous production by addressing issues early.
Simple, Intuitive, and Reliable
With an intuitive interface designed for easy adoption, Click Maint minimizes the learning curve for teams. Its robust customer support ensures smooth implementation, helping businesses quickly realize value from the solution.
Click Maint empowers manufacturers to enhance productivity, lower costs, and improve maintenance efficiency, making it the smart choice for SMBs in both discrete and process manufacturing.
Conclusion
A CMMS delivers transformative benefits for both discrete and process manufacturing by enhancing maintenance efficiency, reducing downtime, and ensuring regulatory compliance. While discrete manufacturers value flexibility and detailed asset tracking, process industries benefit from predictive maintenance and streamlined workflows tailored to their unique needs.
When choosing a CMMS, consider solutions that align with your operation’s size, complexity, and specific challenges. Look for features that offer scalability, customization, and ease of use to ensure long-term adaptability and success.
Click Maint is designed to meet the demands of both discrete and process manufacturing with tailored solutions and outstanding support.
TABLE OF CONTENTS
Keep Reading
Introduction Selecting the right Computerized Maintenance Management System (CMMS) is a ...
31 Jan 2025
More than ever, industries increasingly rely on CMMS (Computerized Maintenance Management ...
30 Jan 2025
Enterprise Asset Management (EAM) software has become a cornerstone for organizations aiming ...
23 Jan 2025
Effective maintenance management requires systems that can streamline operations and ensure ...
17 Jan 2025
Businesses are increasingly turning to data-driven decision-making as a means to optimize ...
15 Jan 2025
Imagine your business is thriving, your team is productive, and everything seems to be on ...
14 Jan 2025
Computerized Maintenance Management Systems (CMMS) are recognized as the go-to solution for ...
13 Jan 2025
Microsoft Excel has been a staple in business for many years. The spreadsheet software is ...
7 Jan 2025
2025 is upon us, and many organizations are pushing to improve the performance of their ...
3 Jan 2025
In today’s business world, where every second counts and downtime can mean disaster, ...
2 Jan 2025
Picture this: a bustling factory floor where machines hum efficiently, a luxury hotel where ...
31 Dec 2024
As sustainability becomes a global focus, facility management has a unique opportunity to ...
24 Dec 2024
Imagine a world where your maintenance team predicts machine failures before they occur, ...
20 Dec 2024
Computerized Maintenance Software Systems (CMMS) entered the marketplace during the 1960s, ...
14 Dec 2024
In today's economic climate, businesses are facing some real challenges. The ups and downs in ...
14 Dec 2024
The 2024 U.S. election marks a pivotal moment in shaping the nation’s policy landscape, ...
9 Dec 2024
According to market analysis, the global CMMS market is projected to grow from USD 1,035.94 ...
4 Dec 2024
Introduction After spending countless hours researching a Computerized Maintenance Management ...
3 Dec 2024
In manufacturing, workplace accidents and non-compliance can have severe consequences. To ...
28 Nov 2024
Imagine maintaining a car. Regular oil changes, tire rotations, and inspections keep it ...
22 Nov 2024