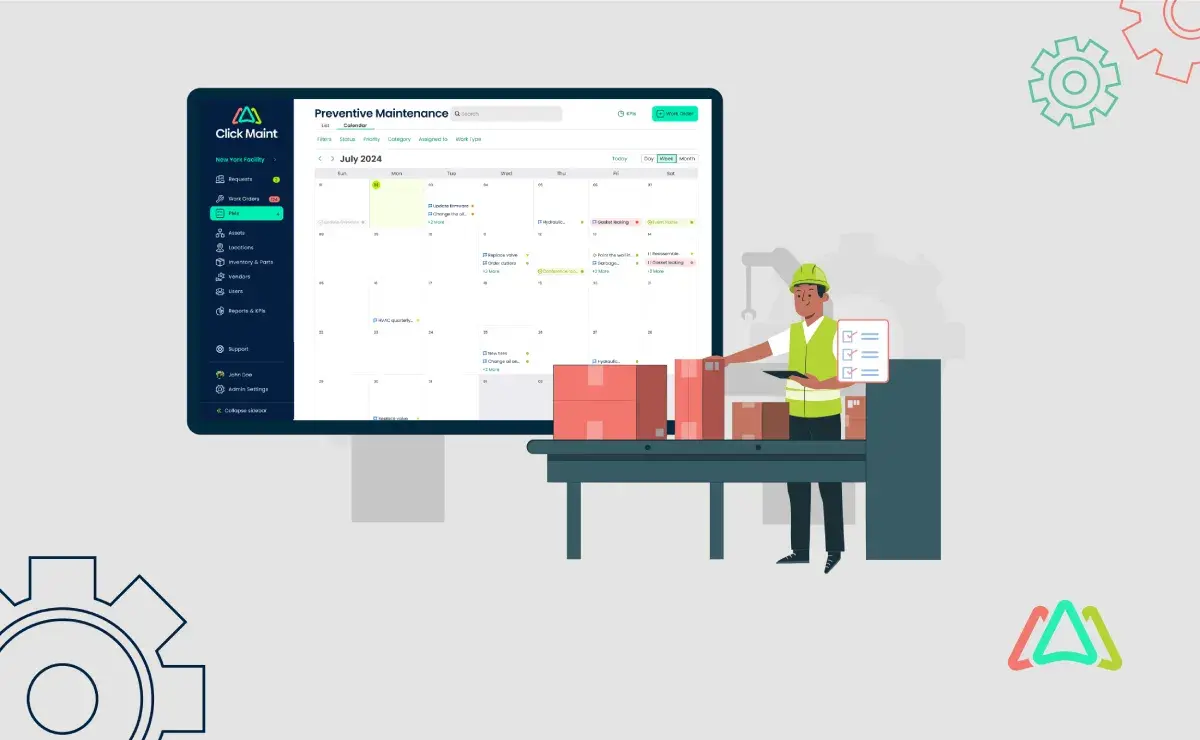
How Small Businesses Can Use CMMS Software for Preventive Maintenance
Introduction
Computerized Maintenance Management System (CMMS) software is a powerful tool designed to streamline maintenance operations for businesses of all sizes. It offers features such as asset management, work order management, preventive maintenance scheduling, inventory management, and reporting capabilities. CMMS enables businesses to centralize their maintenance processes, track assets, optimize maintenance schedules, and improve overall efficiency. Preventive maintenance plays a key role in the success of small businesses by helping them avoid costly downtime, extend the lifespan of equipment, minimize repair expenses, and ensure operational continuity. By addressing maintenance needs, small businesses can enhance productivity, reduce risks, and maintain a competitive edge in their respective industries.
This article explores how small businesses can leverage CMMS software to implement effective preventive maintenance programs. It will delve into the benefits of preventive maintenance, the role of CMMS in facilitating maintenance management, and practical guidance for small businesses looking to set up their maintenance program strategies.
Implementing a preventive maintenance program with CMMS offers numerous benefits, including increased equipment reliability, reduced downtime, improved safety, enhanced asset performance, and lower maintenance costs. By utilizing CMMS for preventive maintenance, small businesses can achieve greater operational efficiency and maximize the lifespan of their assets.
Understanding Preventive Maintenance
Preventive maintenance refers to the proactive approach of regularly inspecting, servicing, and maintaining equipment and assets to prevent breakdowns, reduce the risk of failures, and extend their lifespan. It involves scheduled maintenance tasks, such as lubrication, parts replacement, calibration, and inspections, performed before equipment failure occurs.
The importance of preventive maintenance for small businesses cannot be overstated. It helps minimize downtime, optimize asset performance, reduce repair costs, ensure workplace safety, and maintain productivity. By addressing maintenance needs before they escalate into major issues, small businesses can avoid disruptions to operations.
Key Components of a Preventive Maintenance Program
A comprehensive preventive maintenance software program consists of several key components:
1. Equipment Inventory:
Identifying and cataloging all equipment and assets that require maintenance.
2. Maintenance Schedule:
Establishing a regular schedule for performing maintenance tasks based on manufacturer recommendations, operational requirements, and industry standards.
3. Task Lists:
Creating detailed task lists outlining specific maintenance activities to be performed during each maintenance session.
4. Maintenance Procedures:
Developing standardized operating procedures and protocols for performing maintenance tasks safely and efficiently.
5. Documentation:
Maintaining accurate records of maintenance activities, including work orders, inspection reports, equipment history, and maintenance logs.
6. Performance Metrics:
Defining maintenance key performance indicators (KPIs) to measure the effectiveness of the preventive maintenance program, such as mean time between failures (MTBF) and equipment uptime.
Challenges Faced by Small Businesses in Implementing Preventive Maintenance
Small businesses encounter several challenges when implementing preventive maintenance programs:
1. Limited Resources:
Small businesses often have limited budgets, manpower, and technical expertise to dedicate to preventive maintenance efforts.
2. Time Constraints:
Balancing preventive maintenance activities with day-to-day operations can be challenging for small businesses, leading to scheduling conflicts and delays.
3. Data Management:
Managing and organizing maintenance data, including equipment records, maintenance schedules, and work orders, can be overwhelming for small businesses without proper systems in place.
4. Resistance to Change:
Employees may resist adopting new preventive maintenance practices or technologies, hindering the implementation process.
Despite these challenges, small businesses can overcome them by prioritizing preventive maintenance, investing in suitable tools and resources, and growing a culture of maintenance excellence within the organization.
Designing a Preventive Maintenance Program with CMMS
Assessing Maintenance Needs and Requirements
The first step in designing a preventive maintenance program with CMMS is to assess the organization's maintenance needs and requirements. This involves conducting a thorough evaluation of equipment and assets to identify maintenance tasks, frequency of maintenance, and criticality of equipment. By understanding maintenance needs, small businesses can prioritize resources, allocate budgets effectively, and develop a comprehensive preventive maintenance strategy.
Creating Maintenance Schedules and Task Lists
Once maintenance needs are identified, the next step is to create maintenance schedules and task lists using CMMS software. Maintenance schedules outline when specific maintenance tasks need to be performed based on factors such as equipment usage, manufacturer recommendations, and regulatory requirements. Task lists detail the specific maintenance activities to be performed during each maintenance session, including inspections, lubrication, calibration, and parts replacement. By creating detailed schedules and task lists, small businesses can ensure that maintenance activities are performed consistently and systematically, reducing the risk of equipment failures and downtime.
Setting up Equipment Profiles and Maintenance Plans
CMMS software allows small businesses to set up equipment profiles and create customized maintenance plans for each piece of equipment or asset. Equipment profiles contain detailed information about each asset, including specifications, maintenance history, and criticality. Equipment maintenance plans define the specific maintenance tasks, schedules, and procedures for each asset based on its unique requirements. By setting up equipment profiles and maintenance plans, small businesses can tailor their preventive maintenance programs to the specific needs of each asset, maximizing efficiency and effectiveness.
Defining KPIs and Performance Metrics for Monitoring
To measure the effectiveness of the preventive maintenance program, small businesses need to define key performance indicators (KPIs) and performance metrics for monitoring. Common KPIs include mean time between failures (MTBF), equipment uptime, maintenance costs, and compliance with maintenance schedules. By monitoring KPIs and performance metrics using CMMS software, small businesses can track the performance of their preventive maintenance program, identify areas for improvement, and make data-driven decisions to optimize maintenance strategies and maximize asset reliability.
Implementing Preventive Maintenance Tasks with CMMS
Scheduling and Assigning Maintenance Tasks
CMMS software enables small businesses to streamline the scheduling and assignment of preventive maintenance tasks. With CMMS, maintenance managers can create detailed maintenance schedules based on equipment requirements and workforce availability. Tasks can be easily assigned to technicians or maintenance teams, ensuring accountability and efficient resource allocation.
Generating Work Orders and Notifications
CMMS automates the generation of work orders and notifications for preventive maintenance tasks. Once maintenance tasks are scheduled, CMMS automatically generates work orders detailing the required maintenance activities, instructions, and deadlines. Notifications are sent to technicians or maintenance personnel, alerting them to upcoming tasks and ensuring timely execution.
Recording and Tracking Maintenance Activities
CMMS facilitates the recording and tracking of maintenance activities throughout the preventive maintenance process. Technicians can use CMMS to record details of completed tasks, including work performed, parts used, and any issues encountered. Maintenance activities are logged in the system, providing a comprehensive maintenance history for each asset and enabling tracking of maintenance trends over time.
Analyzing Maintenance Data for Insights and Improvements
CMMS software provides powerful analytics tools for analyzing maintenance data and identifying insights for improvements. By analyzing maintenance data, such as equipment downtime, maintenance costs, and asset performance metrics, small businesses can identify trends, root causes of issues, and areas for optimization. This data-driven approach enables continuous improvement of the preventive maintenance program, leading to enhanced efficiency, reduced costs, and increased asset reliability.
Best Practices for Effective Preventive Maintenance
Regular Inspections and Condition Monitoring
Regular inspections and condition monitoring are fundamental to effective preventive maintenance. Small businesses should conduct routine inspections of equipment and assets to identify potential issues early on. Condition monitoring techniques, such as vibration analysis, thermography, and oil analysis, can help detect abnormalities and predict potential failures before they occur. By proactively monitoring equipment health, businesses can prevent costly breakdowns and ensure optimal performance.
Proactive Equipment Maintenance and Replacement
Proactive equipment maintenance and replacement involve preemptive actions to address potential issues and extend the lifespan of assets. Small businesses should prioritize preventive maintenance tasks, such as lubrication, calibration, and parts replacement, to minimize wear and tear and prevent premature failure. Additionally, businesses should consider proactive equipment replacement strategies based on factors such as asset age, performance degradation, and technological advancements, ensuring continued reliability and efficiency.
Utilizing Predictive Maintenance Techniques
Predictive maintenance techniques leverage data analytics and predictive algorithms to anticipate equipment failures and schedule maintenance activities accordingly. By analyzing equipment data, such as operating parameters, performance trends, and failure patterns, small businesses can identify early indicators of potential failures and take proactive measures to address them. Predictive maintenance minimizes unplanned downtime, reduces maintenance costs, and optimizes asset reliability and performance.
Continuous Improvement and Optimization of the PM Program
Continuous improvement and optimization are essential for maintaining the effectiveness of the preventive maintenance program over time. Small businesses should regularly review and evaluate their PM program, identifying areas for improvement and implementing changes accordingly. This may involve refining maintenance procedures, adjusting maintenance schedules, upgrading technology, or providing additional training for staff. By fostering a culture of continuous improvement, businesses can ensure that their preventive maintenance program remains efficient, effective, and aligned with organizational goals.
Conclusion
CMMS streamlines maintenance operations, reduces downtime, lowers costs, and enhances asset reliability for small businesses. Adopting CMMS empowers small businesses to proactively manage maintenance, improve efficiency, and stay competitive in their industries. Small businesses should prioritize implementing a preventive maintenance program with CMMS, focusing on assessing needs, setting up schedules, asset tracking activities, and continuously improving processes for long-term success.
TABLE OF CONTENTS
Keep Reading
Ever find yourself checking into a luxury hotel and expecting a relaxing stay, only to find a ...
11 Apr 2025
Organizations are witnessing swift changes in the business environment and confronting a ...
8 Apr 2025
Last month, news outlets and the entire internet was abuzz with the return of NASA astronauts ...
3 Apr 2025
What comes first - CMMS or predictive maintenance? If your answer is either, it is correct. ...
28 Mar 2025
Artificial intelligence (AI) talk has become commonplace. Today, engaging in business-focused ...
27 Mar 2025
Imagine a world where machines predict, diagnose, and fix their issues before they fail. This ...
25 Mar 2025
A facility maintenance plan is at the core of a facility’s operations. This organized ...
21 Mar 2025
Think of managing your maintenance operations like managing a championship sports team. Just ...
21 Mar 2025
The maintenance sector is battling a severe talent shortage that threatens to undermine ...
7 Mar 2025
Manufacturing maintenance is the backbone of industrial efficiency, ensuring machines run ...
5 Mar 2025
No one likes playing a guessing game when equipment breaks down. Yet, maintenance teams often ...
4 Mar 2025
The size of the preventive maintenance software market is discussed in millions of dollars, ...
4 Mar 2025
The organizational structure and corporate hierarchy vary from company to company. Large ...
28 Feb 2025
Maintenance procedures are essential for ensuring the longevity and reliability of machinery ...
21 Feb 2025
Sustainability is no longer just a buzzword; it's a critical component of corporate social ...
20 Feb 2025
A Computerized Maintenance Management System (CMMS) relies on accurate, well-organized data ...
18 Feb 2025
In an era where technology drives operational efficiency, Computerized Maintenance Management ...
14 Feb 2025
A Computerized Maintenance Management System (CMMS) is a key component of modern maintenance ...
13 Feb 2025
Introduction Maintenance management is the foundation of maintenance operations in industries ...
11 Feb 2025
Introduction A Computerized Maintenance Management System (CMMS) is software designed to help ...
7 Feb 2025