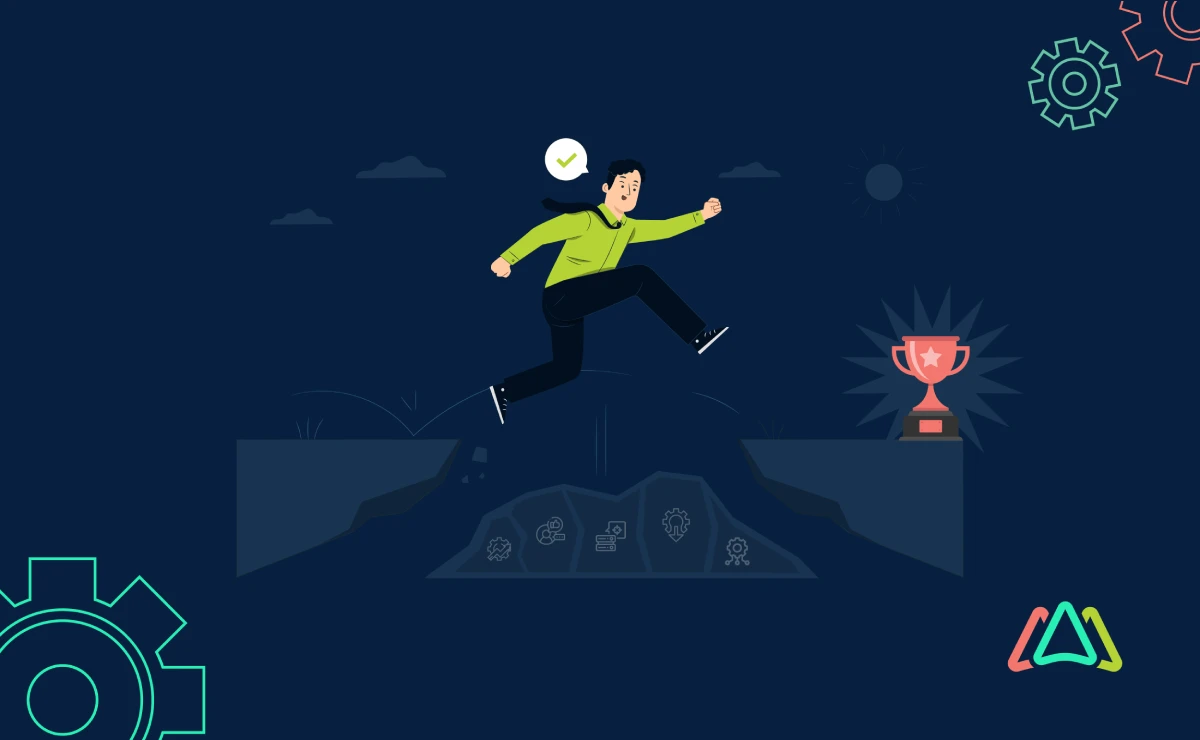
5 Mistakes to Avoid When Implementing a CMMS
Introduction
It’s understandable that after spending months researching Computerized Maintenance Management Systems (CMMS) and settling on the one that meets your company’s needs, you’d be anxious to fire it up and get started. If you’re a smaller maintenance operation with a team of 5 or fewer and oversee a small facility with 50 assets, getting set up and started is pretty simple and can be done within a couple of days. However, for operations with larger teams, multiple departments, alternating shifts, a large number and variety of assets, and multiple sites, implementing a CMMS will take time and careful planning. When companies jump the gun and dive into their CMMS without much planning, users can run into some roadblocks or “pitfalls.”
This article explores common pitfalls CMMS users often encounter when they jump the gun and start their CMMS rollout prematurely without a well-planned implementation process.
Mistake #1: Underutilization of CMMS Features
Most CMMS applications have many features and modules. In an effort to get set up quickly and start reaping the benefits of the CMMS, many users don’t yet fully grasp all the features available and how they are interrelated. Today, there are a lot of CMMS products where users can sign up for a free trial and purchase the software online without a demo or speaking to a sales representative. This is not a bad thing, but if you have a larger operation with many team members, you should get a solid understanding of what modules and features you have access to and how they work together.
In some cases, users avoid features they perceive as too complicated. Neglecting to explore the advanced CMMS features, these users may be missing out on key features that can help improve their operations.
Meter-based PMs, for example, require a little more effort to learn and understand than time-based PM scheduling. If the organization has equipment and machines that are better off with meter-based PM schedules, it makes sense to spend a little more time getting trained on the capabilities and how to configure them. Another common example is scheduling reports. Many users see the reports module and use the canned reports or set up their own. But too often, admin users don't realize that in some CMMS systems, reports can be scheduled and emailed out to outside contacts like executives who may not be users. Rather than manually creating monthly and quarterly reports, using the scheduled reports with email sharing saves a lot of time.
To avoid this, admin users should ensure that they receive thorough training on all aspects of the CMMS to the extent they are comfortable utilizing both basic and advanced features. This helps them improve their maintenance and save money in the long run. Going further, users should subscribe to product update notifications from the CMMS software vendor and ensure that they stay connected with their assigned account manager. They should meet quarterly or bi-annually so that they stay up to date on new product releases and what’s on the roadmap.
Mistake #2: Lack of Data Accuracy and Maintenance
Over time, CMMS data can become outdated and inaccurate. This happens when equipment changes and team members fail to enter the new equipment data into the CMMS correctly. When the data isn't reliable, errors result and negatively impact the maintenance department. CMMS software can only perform actions based on the data entered into its system. It cannot discern good from bad data entries. It becomes a case of “garbage in—garbage out!”
For example, a CMMS software sends an alert indicating that a piece of equipment requires a specific part, but that part has already been replaced. The team member who replaced the part forgot to enter the information into the CMMS. An oversight such as this one can lead to delays and safety issues.
To avoid further recurrences of this kind, robust data management protocols should be implemented, including clear rules for entering data and checking the system regularly for mistakes. Conducting periodic audits of the CMMS database can also help identify discrepancies, inconsistencies, or missing data that must be addressed. Above all, everyone who uses the CMMS should understand the importance of accurate data and the need to follow the rules.
Many CMMS applications have ways to enforce data integrity; for example, on work orders, requests, and asset forms, admin users can require specific fields to be completed before creating or completing a work order. If a work order is assigned to a technician, you can configure the software not to allow it to be closed until labor hrs are logged. Small configurations like these help to ensure that data is entered correctly. In addition, managers should ensure that they train staff and clearly communicate the importance of having good data and standards that are expected from them. Help them understand the big picture and how it affects the whole maintenance department and company.
By proactively addressing data quality issues and promoting a culture of accountability, organizations can maintain the integrity of their CMMS data and maximize the system's benefits. This, in turn, enables more informed decision-making, improved maintenance planning, and, ultimately, greater operational efficiency and reliability.
Mistake #3: Poor CMMS Integration with Other Business Applications
CMMS integrations are complex and need to be set up properly and tested to ensure the integration works as expected. Poor integration of the CMMS with other systems within the organization can significantly hinder operational efficiency and limit the system's overall effectiveness. When the CMMS operates in isolation from other critical systems, such as Enterprise Resource Planning (ERP), asset management, or Internet of Things (IoT) sensors, it creates information silos and prevents a comprehensive understanding of operations.
For example, consider a manufacturing company that deploys its CMMS to track maintenance schedules while its ERP system independently manages inventory and purchasing. Without integration between these systems, maintenance technicians may not have real-time access to inventory levels, leading to delays in procuring necessary parts and extending equipment downtime.
To address this pitfall, CMMS admins must prioritize compatibility and interoperability when selecting a CMMS and actively pursue integration with existing systems. Seamless integration enables data exchange across departments and provides a holistic view of operations, enhancing decision-making and efficiency. For example, integrating the CMMS with the ERP system allows maintenance schedules to be synchronized with inventory levels, ensuring that parts are available when needed and minimizing equipment downtime. Similarly, integration with IoT platforms can enable real-time monitoring of equipment performance, facilitating proactive maintenance and reducing the risk of unexpected failures. By overcoming the barrier of inadequate integration, organizations can unlock the full potential of their CMMS and optimize maintenance operations.
Mistake #4: Ignoring CMMS User Feedback and Resistance to Change
A familiar challenge stakeholders face during CMMS implementation is resistance from users who are hesitant to transition from traditional maintenance practices. A significant source of hesitation rests on users who find the CMMS interface overwhelming. Others may hesitate to take on a new way of doing things when their current process works well. Still, others may worry that their positions may become redundant with CMMS adoption. Disregarding user feedback and failing to address their concerns can result in significant barriers to adoption, ultimately leading to suboptimal system utilization.
For example, maintenance technicians who are used to managing work orders manually using paper-based systems balk at a new CMMS being introduced to automate these processes. Their concerns relate to being unfamiliar with the software or concerns about increased workload because of it. If their feedback and concerns are not taken seriously, the technicians may revert to their old maintenance methods, undermining the potential benefits of the CMMS.
To mitigate this pitfall, CMMS admins must actively engage with users, solicit their feedback, and address their concerns promptly, thoroughly, and effectively. This involves creating channels for open communication where users feel comfortable expressing their thoughts and providing input on the CMMS implementation process.
Holding regular meetings or conducting surveys to gather feedback can help identify pain points and areas for improvement. As previously noted, providing comprehensive training and ongoing support to users is essential for building confidence and trust and promoting acceptance of the CMMS. By listening to user feedback and addressing resistance to change, stakeholders can foster a culture of collaboration and ensure that the CMMS is embraced as a valuable tool for enhancing maintenance operations. Even more importantly, maintenance managers need to connect the dots and demonstrate how the new CMMS has the potential to save the company money through transitioning from costly run-to-fail reactive maintenance to preventive, reducing equipment downtime, extending asset life, and equipping the organization with data that enables better decision making.
Mistake #5: Neglecting Continuous Improvement
Neglecting continuous improvement after implementing a CMMS can hinder the system's ability to adapt to changing organizational needs and technological advancements. The CMMS software is continually updated, adding new features to keep up with industry and regulatory changes. Treating the CMMS implementation process as a “once and done” project instead of an ongoing process of optimization and enhancement can lead to stagnation and missed opportunities for efficiency gains.
Consider a facility that implemented a CMMS with the overall goal of streamlining its maintenance operations. Initially, the CMMS met expectations by helping improve scheduling and work order management. However, when regular performance assessments and updates were not conducted to address emerging challenges or incorporate new features, the CMMS became outdated and failed to keep pace with evolving maintenance requirements.
To avoid this pitfall, stakeholders must establish mechanisms for continuous improvement to ensure that the CMMS evolves alongside the organization's needs and industry developments. This involves conducting regular reviews to assess the system's effectiveness and identify areas needing enhancement. Analyzing key performance indicators (KPIs) such as equipment downtime, maintenance costs, and work order completion rates can pinpoint inefficiencies or operation bottlenecks.
Establishing feedback loops with CMMS users is a helpful way to collect insights and suggestions for improvement directly from users who engage with the system daily. By comparing what works best in the industry and trying out new technologies, stakeholders can find ways to improve maintenance and get the most out of the CMMS. As already mentioned above, users should stay connected with their assigned account manager. They should meet quarterly or bi-annually so that they stay up to date on new product releases and what’s on the roadmap. Admin users should also encourage their team to attend the CMMS software vendor’s webinars on new releases and be proactive in learning new features and capabilities. Managers should disseminate new updates via email and discuss them in team meetings. For larger teams, ask the software vendor to conduct regular demos of new features and product updates every time there is a big release.
Conclusion
Successfully implementing and utilizing a CMMS requires careful consideration of potential pitfalls and proactive strategies to overcome them. From underutilizing features to neglecting continuous improvement, each pitfall can hinder the CMMS's effectiveness and undermine its ability to streamline maintenance operations as it is designed to do. By prioritizing user training, fostering accountability, and actively soliciting feedback, stakeholders can address resistance to change and ensure that the CMMS is recognized as a valuable tool for enhancing efficiency and reliability.
Furthermore, organizations can experience the full potential of their CMMS investment by integrating the CMMS with existing systems, maintaining data accuracy, and continuously seeking opportunities for improvement. These steps lead to cost savings and increased productivity, enabling the organization to stay competitive in a rapidly evolving climate. By avoiding these pitfalls and implementing best practices, stakeholders can mobilize the power of CMMS technology to achieve operational excellence and long-term success.
TABLE OF CONTENTS
Keep Reading
Ever find yourself checking into a luxury hotel and expecting a relaxing stay, only to find a ...
11 Apr 2025
Organizations are witnessing swift changes in the business environment and confronting a ...
8 Apr 2025
Last month, news outlets and the entire internet was abuzz with the return of NASA astronauts ...
3 Apr 2025
What comes first - CMMS or predictive maintenance? If your answer is either, it is correct. ...
28 Mar 2025
Artificial intelligence (AI) talk has become commonplace. Today, engaging in business-focused ...
27 Mar 2025
Imagine a world where machines predict, diagnose, and fix their issues before they fail. This ...
25 Mar 2025
A facility maintenance plan is at the core of a facility’s operations. This organized ...
21 Mar 2025
Think of managing your maintenance operations like managing a championship sports team. Just ...
21 Mar 2025
The maintenance sector is battling a severe talent shortage that threatens to undermine ...
7 Mar 2025
Manufacturing maintenance is the backbone of industrial efficiency, ensuring machines run ...
5 Mar 2025
No one likes playing a guessing game when equipment breaks down. Yet, maintenance teams often ...
4 Mar 2025
The size of the preventive maintenance software market is discussed in millions of dollars, ...
4 Mar 2025
The organizational structure and corporate hierarchy vary from company to company. Large ...
28 Feb 2025
Maintenance procedures are essential for ensuring the longevity and reliability of machinery ...
21 Feb 2025
Sustainability is no longer just a buzzword; it's a critical component of corporate social ...
20 Feb 2025
A Computerized Maintenance Management System (CMMS) relies on accurate, well-organized data ...
18 Feb 2025
In an era where technology drives operational efficiency, Computerized Maintenance Management ...
14 Feb 2025
A Computerized Maintenance Management System (CMMS) is a key component of modern maintenance ...
13 Feb 2025
Introduction Maintenance management is the foundation of maintenance operations in industries ...
11 Feb 2025
Introduction A Computerized Maintenance Management System (CMMS) is software designed to help ...
7 Feb 2025