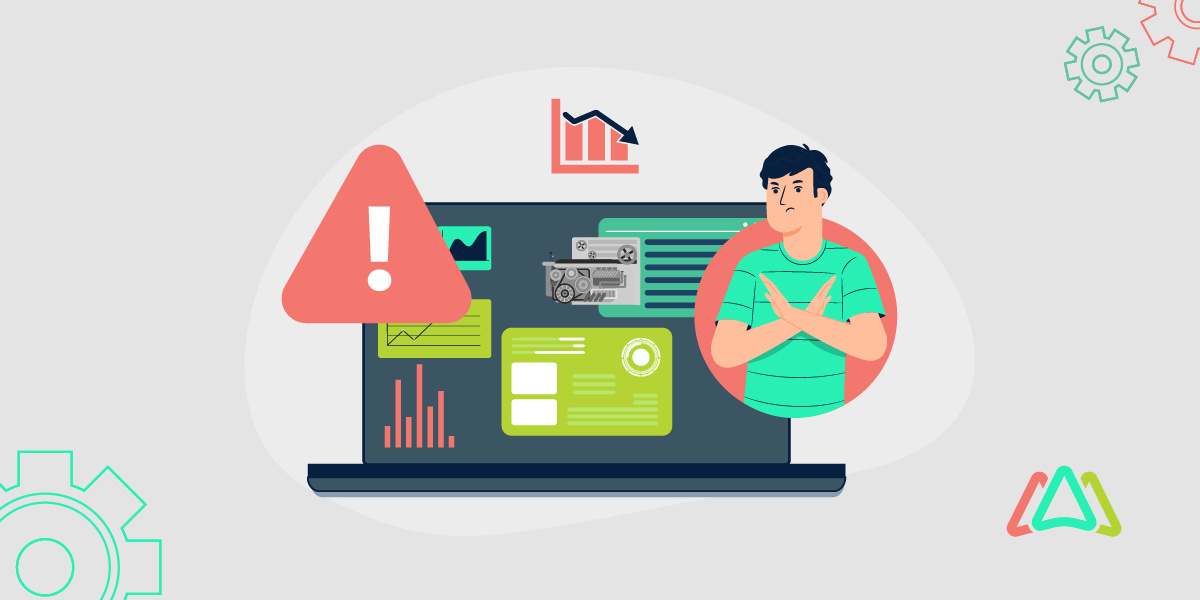
Consider CMMS Implementation Risks
Computerized Maintenance Management Systems (CMMS) are recognized as the go-to solution for companies wanting to improve maintenance operation efficiency, minimize downtime, and increase their bottom line. However, one major caudicle to this claim is a failure to be aware of potential CMMS implementation risks. Consider the following:
Approximately 80% of CMMS projects fail to deliver expected results due to low user adoption, lack of planning, or insufficient resources dedicated to the implementation process. Of these, the most common cause of failure is inadequate user adoption—where employees resist using the system or find it too complex.
Let’s start with the basics by understanding what a CMMS can do.
Briefly, a CMMS software is designed to streamline and optimize maintenance operations by centralizing data related to equipment, work orders, inventory, and maintenance schedules. Its primary goal is to help organizations efficiently manage assets, reduce downtime, improve productivity, and extend equipment lifespans through better maintenance task planning and execution. However, these goals can only be achieved by being aware of and avoiding common risks in CMMS implementation.
Poor CMMS implementation practices, such as failing to involve key stakeholders during selection, can lead to mismatched systems and limited use. These challenges and others that follow highlight the importance of careful planning, resource allocation, and ongoing support during CMMS implementation. Let’s examine some of them now.
Lack of Clear Goals and Objectives
A common pitfall in CMMS implementation is the failure to have well-defined goals and objectives before the software is selected. Without consideration of these factors, company stakeholders run the risk of under-utilization, inefficiency, and failure. Additionally, without clear goals, team members may pursue goals that are out of sync with those of others. For example, some teams may focus on reducing reactive maintenance, while others prioritize optimizing preventive schedules. This misalignment often leads to conflicting expectations among stakeholders, undermining the system's value, utility, and adoption rates.
Undefined objectives can also result in selecting or configuring a CMMS that doesn’t fully meet an organization’s needs. For example, choosing a system with complex features that will never be utilized wastes resources, time, and money. At the same time, it may overlook essential capabilities. This CMMS implementation risk can hinder operational improvements and benefits to a company. By failing to clarify an organization’s specific pain points—such as improving asset uptime, reducing maintenance costs, or streamlining inventory tracking—they risk implementing a system that fails to provide measurable value.
Insufficient Executive Support
Executive support is a critical component of a successful CMMS implementation. However, it is often not given much weight. Without strong leadership backing, CMMS projects may suffer from unclear priorities, a lack of accountability, or a misperception by team members that they hold little value. Executives’ involvement is vital in championing the system by ensuring it aligns with organizational goals, allocating necessary resources, and empowering teams to prioritize implementation efforts. When this support is absent, maintenance teams may struggle to gain buy-in from other departments, delaying the implementation process and reducing its overall effectiveness.
Poor Planning and Preparation
Thorough planning and preparation are essential when implementing a CMMS. When lacking or not done correctly, it can lead to a failure in CMMS implementation. Often, organizations underestimate the complexity of the process, which involves evaluating current maintenance workflows, gathering accurate data, and aligning system capabilities with operational goals. Critical tasks such as accurate data migration, user training, and system testing may be rushed or overlooked without a structured implementation plan. This results in errors, inefficiencies, and an implementation that falls short of meeting organizational needs.
Poor planning often overlooks the need to anticipate challenges—such as resistance to change, incomplete data, or technical integration issues. Failing to plan for these challenges may cause unnecessary delays or require costly rework. Rushing this phase of CMMS implementation can be costly, frustrating, and disappointing.
Inadequate Data Preparation
In the previous section, we briefly noted migration issues caused by poor CMMS implementation planning. In this section, we will examine how inadequate data preparation poses a risk to CMMS implementation.
Since a CMMS relies on accurate and comprehensive data to manage maintenance tasks, track equipment history, and analyze performance metrics, it compromises the system’s ability to deliver precise and actionable insights when data is incomplete, outdated, or improperly formatted.
Organizations frequently underestimate the effort required to collect, validate, and migrate data into the CMMS. Depending on the size and scope of an organization, this critical process takes time because it involves gathering information about thousands of assets, including equipment specifications, maintenance history, and parts inventory. When working with legacy systems or paper-based records, errors may be a factor to be corrected before migration. Taking these steps is essential to avoid populating the CMMS with flawed data.
Ignoring Change Management
Effective change management during a CMMS implementation ensures the system’s success. Because a CMMS comes with significant changes to workflows, requiring employees to alter how they schedule, execute, and track maintenance tasks, user buy-in is needed. Without a change management strategy, employees may feel overwhelmed or resistant, viewing the new system as a disruption rather than a tool for improvement. This resistance can lead to poor user adoption, reduced productivity, and an underutilized system failing to deliver its intended benefits.
Lack of User Training and Engagement
A lack of CMMS training and engagement can derail even the most well-planned CMMS implementations. Without sufficient training, users may struggle with the system's interface, leading to errors in data entry, incomplete records, or underutilization of key features. For instance, technicians unfamiliar with logging work orders or updating asset details might revert to old habits, such as relying on paper records, which undermines the digital system’s purpose.
User adoption often stems from resistance to change, particularly if users are not involved in the implementation process or fail to see the value of the CMMS in their daily tasks. Employees may view the system as an added burden rather than a tool to streamline their workload. A disengaged workforce can result in low adoption rates, making it nearly impossible to achieve the system's intended benefits.
Inadequate Post-Implementation Support
User support does not end even with a successful CMMS deployment. Not having post-implementation support poses a significant risk to the system’s long-term success. Encountering technical issues, data inaccuracies, or challenges in adapting the system to evolving organizational needs are realities of ongoing CMMS use. Left unaddressed, users may lose confidence in the CMMS, leading to decreased usage and a gradual return to inefficient manual processes. A lack of post-implementation refresher training poses a related risk in the form of underutilizing the system.
Failure to Measure Success
Getting caught up in successful user adoption sometimes distracts maintenance managers from their need to measure success during and after CMMS implementation. This critical oversight can leave organizations incapable of assessing the system’s effectiveness in facilitating operational changes. This lack of evaluation can lead to wasted resources and unaddressed inefficiencies, ultimately undermining the system’s potential.
Measuring success requires establishing key performance indicators (KPIs) during the planning phase. These KPIs might include metrics such as mean time between failures (MTBF), work order completion rates, or inventory accuracy. Organizations that neglect this step often struggle to align the CMMS with their operational goals, making it challenging to demonstrate value to stakeholders. Moreover, failure to monitor ongoing performance prevents organizations from identifying opportunities for improvement, such as refining workflows or expanding system functionality to address new challenges.
Managing the CMMS Risk
CMMSs are excellent tools for improving overall company operations. However, a CMMS can only be valuable and effective when the risks outlined here are avoided. Unfortunately, the consequences of CMMS implementation risks often diminish the software's potential benefits.
Successful CMMS implementation involves careful planning, stakeholder engagement, and ongoing support. Key risks such as unclear goals, inadequate data preparation, poor user training, and resistance to change must be proactively addressed to avoid common CMMS implementation risks.
Choosing the right CMMS, establishing robust change management practices, and measuring success through well-defined KPIs are essential for ensuring the system delivers its intended value. Organizations should approach CMMS implementation as a strategic initiative, prioritizing collaboration, communication, and adaptability. By focusing on these critical success factors, they can achieve the full potential of a CMMS.
TABLE OF CONTENTS
Keep Reading
Asset lifespan is a key concern for executives and maintenance and facility management teams. ...
3 Jul 2025
Your company recently invested funds and time for new CMMS software, and six months later, it ...
1 Jul 2025
As Computerized Maintenance Management Systems (CMMS) become more connected and cloud-based, ...
1 Jul 2025
Edge computing is an innovative technology that enables data to be processed at the source, ...
24 Jun 2025
Facility management has undergone a significant transformation in recent times. Take, for ...
20 Jun 2025
A facility maintenance plan is at the core of a facility’s operations. This organized ...
19 Jun 2025
In the early days, preventive maintenance could be done effectively with a trained eye and a ...
17 Jun 2025
Sticky notes fall off, whiteboard grids get wiped, and spreadsheets never beep when a ...
13 Jun 2025
Handing a slice of your maintenance workload to a contractor is less about “giving up ...
12 Jun 2025
Downtime in enterprise environments doesn’t just mean a stop in operations; it means lost ...
10 Jun 2025
Understanding equipment functionality is crucial for effective repairs. A clear, systematic ...
6 Jun 2025
Maintenance managers know that every unplanned equipment failure is more than a simple ...
5 Jun 2025
What keeps a facility running smoothly? Initially, many of us may zoom in on its equipment, ...
29 May 2025
In today's digital world, every decision needs to pass the test of strategic and operational ...
27 May 2025
The business world is very different from a decade ago. Technological advancements have grown ...
23 May 2025
Picture this: a maintenance technician inspects a complex pump system. Instead of typing a ...
20 May 2025
For most of the 20th century, maintenance teams mainly applied a reactive approach to ...
9 May 2025
Imagine visiting a manufacturing plant where maintenance technicians gather around a large ...
8 May 2025
Maintenance management faces complexities across all industries, escalating with ...
6 May 2025
Ever find yourself checking into a luxury hotel and expecting a relaxing stay, only to find a ...
11 Apr 2025