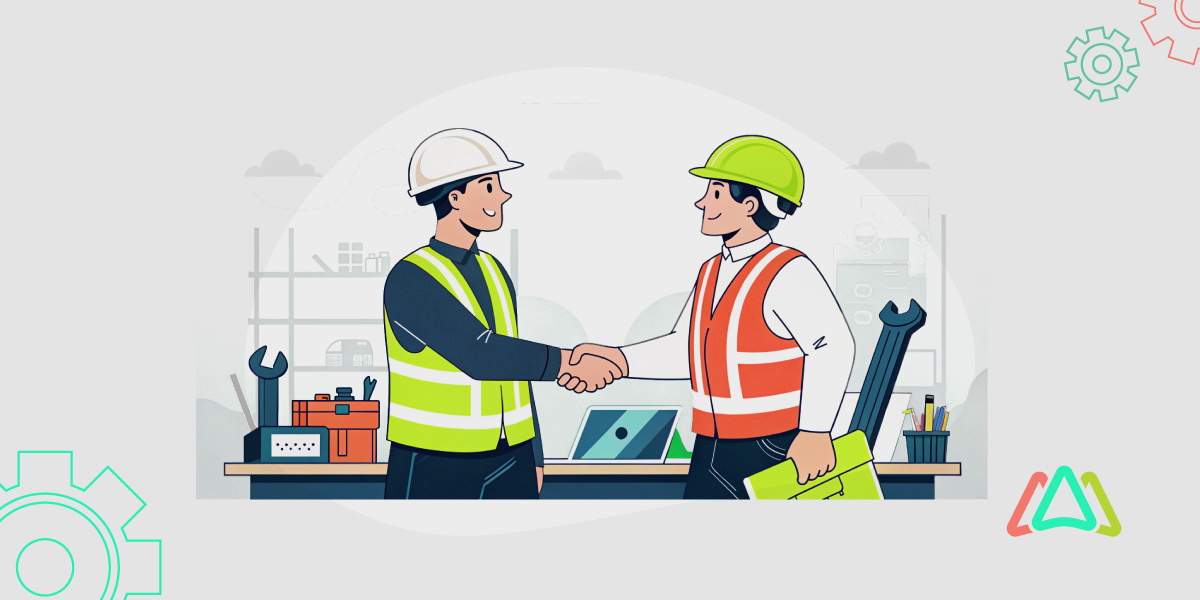
How to Manage Maintenance Outsourcing with a CMMS
According to market analysis, the global CMMS market is projected to grow from USD 1,035.94 billion in 2024 to USD 2,064.3 billion by 2032, driven by its ability to streamline maintenance processes, reduce downtime, and optimize costs. As operational demands rise, maintenance remains the backbone of efficiency, prompting many organizations to outsource it for specialized expertise and improved focus.
However, outsourcing maintenance tasks presents its own set of challenges. Miscommunication between internal teams and external vendors, difficulty in tracking vendor performance, and ensuring contract compliance can lead to inefficiencies, costly delays, and strained vendor relationships.
In this article, we’ll explore how a CMMS can transform the way you manage outsourced maintenance, from reducing inefficiencies to improving accountability. Whether you’re struggling with vendor coordination or seeking to improve cost control, this guide will show you how a CMMS can revolutionize your operations and elevate your maintenance strategy.
What is Maintenance Outsourcing?
Maintenance outsourcing is the practice of hiring an external service provider to manage and perform maintenance activities for an organization. It involves transferring the responsibility of planning, scheduling, and executing maintenance tasks to a third-party provider. This approach is often employed to reduce costs, improve efficiency, and enhance the quality of maintenance services. Additionally, outsourcing allows businesses to access specialized skills and resources that may not be available in-house.
Examples of Maintenance Outsourcing
Maintenance outsourcing is widely practiced across industries. Common services offered by maintenance outsourcing providers include preventive maintenance (to avoid equipment failures), corrective maintenance (to address breakdowns), predictive maintenance (to anticipate issues), and asset management. By outsourcing, businesses can focus on their core operations while ensuring that skilled professionals handle maintenance.
Why Outsourcing Maintenance?
Outsourcing maintenance has become a strategic choice for businesses across industries, offering a range of compelling benefits. By partnering with external experts, organizations can reduce costs, access specialized skills, and ensure operational flexibility. It allows businesses to focus on their core activities while leaving complex maintenance tasks to professionals equipped with the right tools and expertise. From manufacturing plants to facilities management, outsourcing ensures streamlined operations, better resource allocation, and improved overall efficiency.
Cost Savings
Outsourcing maintenance helps businesses save costs by eliminating the need to hire and train in-house teams and reducing expenses on specialized tools and equipment.
Access to Expertise
Outsourcing maintenance provides access to skilled technicians and industry specialists, allowing businesses to leverage their expertise for handling complex or specialized tasks.
Scalability
Outsourcing maintenance offers scalability, enabling businesses to adjust services based on operational needs and manage seasonal demand fluctuations without overburdening in-house teams.
Challenges with Maintenance Outsourcing
While outsourcing offers clear benefits, it also presents challenges that can disrupt operations if not managed properly. Here are some common issues you may encounter:
Communication Gaps
Communication gaps between in-house teams and vendors can lead to delays, errors, and reduced efficiency. Misunderstandings often arise when maintenance requirements are not clearly documented, making it harder for vendors to meet expectations and causing unnecessary disruptions to operations.
Quality Control
Maintaining quality control in outsourced maintenance can be challenging, as ensuring vendors meet desired standards is not always straightforward. Vendors may prioritize speed over thoroughness, which can compromise maintenance outcomes and affect overall reliability.
Loss of Operational Control
Outsourcing maintenance can sometimes lead to a loss of control over key aspects of the maintenance process, such as deadlines, compliance, and data security. Companies may find it difficult to track progress, ensure adherence to instructions, or maintain accurate records without a robust management system in place.
Role of CMMS in Maintenance Outsourcing
A Computerized Maintenance Management System (CMMS) can minimize the risks and challenges of maintenance outsourcing. By centralizing information, streamlining processes, and enhancing communication, a CMMS bridges the gap between in-house teams and external vendors, ensuring seamless collaboration and operational efficiency.
Centralized Information and Enhanced Communication
A CMMS centralizes maintenance data, including work orders, service histories, and vendor contracts, providing both in-house teams and vendors with consistent, up-to-date information. Real-time updates and integrated messaging ensure clear communication, reducing delays and keeping all stakeholders aligned on priorities and timelines.
Streamlined Processes and Automation
CMMS automates key maintenance workflows, such as scheduling, approvals, and reporting. Tasks can be assigned automatically, reducing manual intervention, while reports are effortlessly generated to provide a clear view of maintenance progress. This level of automation eliminates inefficiencies, enabling outsourced maintenance tasks to run smoothly and on schedule.
Vendor Performance Monitoring and Accountability
With real-time reporting and performance tracking, a CMMS ensures vendors meet service level agreements (SLAs) and performance standards. Metrics such as response times and task completion rates help hold vendors accountable, ensuring maintenance tasks are performed to the highest standards and providing data-driven insights for continuous improvement.
Proactive Maintenance and Cost Control
A CMMS leverages predictive maintenance capabilities to identify potential equipment issues before they escalate, reducing emergency repairs and equipment downtime. This proactive approach not only extends the life of assets but also helps businesses maintain control over maintenance budgets, identifying cost-saving opportunities while ensuring predictable operational expenses.
Step-by-Step Guide to Managing Outsourced Maintenance with CMMS
Step 1
Identify Outsourcing Needs
The first step is to assess which maintenance tasks or equipment would benefit from outsourcing. Consider factors such as cost efficiency, skill requirements, and the potential to improve response times. Clearly defining these needs will help you set goals that guide the entire outsourcing process.
Step 2
Choose the Right CMMS
Select a CMMS that offers the features necessary to manage outsourced maintenance effectively. Key features to prioritize include vendor management, real-time tracking, and robust reporting capabilities. A CMMS like ours provides seamless vendor coordination, ensuring that you can manage outsourced tasks with full visibility and control. Some CMMS solutions have vendor portals that allow vendors to interact with work orders they have been assigned without having to be users. CMMS software can also auto-assign work orders to vendors and notify them by email, minimizing manual communication between the company and the 3rd party vendor.
Step 3
Set Up Vendors in the CMMS
Once you've chosen a CMMS, the next step is to set up your vendors within the system. Add essential details such as contact information, contracts, and service agreements. Additionally, you can create customized workflows tailored to each vendor and specific maintenance tasks, streamlining the process and ensuring that everything runs smoothly.
Step 4
Plan and Schedule Maintenance Tasks
With your CMMS software in place, use its features to schedule tasks based on urgency, service level agreements (SLAs), and equipment needs. The system ensures that both in-house and external teams have visibility into the maintenance calendar, reducing scheduling conflicts and improving overall efficiency.
Step 5
Monitor and Optimize Performance
Track vendor performance and maintenance outcomes using the CMMS’s built-in analytics tools. Monitor metrics like compliance, response times, and cost-effectiveness. If needed, adjust contracts, workflows, or vendor relationships based on insights to optimize the outsourced maintenance process continuously.
Choosing the Right CMMS for Outsourced Maintenance
Selecting the right CMMS is a critical step in ensuring the success of your outsourced maintenance strategy. With numerous options available, prioritizing the right features and capabilities can make all the difference in managing vendors, streamlining workflows, and maintaining control over operations. Here’s what to focus on:
Key Features to Look For
When selecting a CMMS, prioritize systems that offer comprehensive vendor management tools, such as SLA tracking, performance monitoring, and activity logs, to ensure transparency and accountability in outsourced maintenance. Real-time task tracking is also important, as it allows you to monitor progress, identify delays, and ensure deadlines are met, reducing miscommunication. Customizable reporting and analytics provide insights into maintenance costs, vendor performance, and equipment reliability, enabling data-driven decisions. Additionally, seamless integration with existing systems, mobile accessibility, and automation features such as scheduling and notifications will streamline workflows, reduce manual work, and enhance efficiency for both in-house teams and vendors.
Consider Your Business Needs
When choosing a CMMS, it’s essential to align the system with your specific business needs. For instance, if you operate in a highly regulated industry, you should prioritize compliance tracking features. Scalability is also important, ensuring that the CMMS can grow with your business and accommodate additional vendors or larger operations. Additionally, consider the ease of use, as a user-friendly interface will facilitate quicker adoption by both your internal team and external vendors.
Trial and Vendor Support
Before committing to a CMMS, take advantage of free trials or demos to evaluate how well it meets your needs. Additionally, choose a provider with strong customer support and training resources to ensure smooth implementation and ongoing success.
By focusing on these factors, you’ll be better equipped to choose a CMMS that not only supports your current outsourcing goals but also scales to meet future demands, ensuring efficiency and reliability across all maintenance operations.
Conclusion: Why a CMMS is Essential for Outsourced Maintenance
In summary, a CMMS is a game-changer when it comes to managing outsourced maintenance. Centralizing information, improving communication, and tracking performance streamlines processes, enhances vendor accountability, and boosts overall efficiency. The benefits of using a CMMS for outsourced maintenance are clear: reduced downtime, better cost control, and a more proactive approach to maintenance.
For efficient outsourcing management and maximizing your ROI, a CMMS is essential. Don’t let manual processes or miscommunication hinder your operations—take control with a CMMS solution designed to optimize your maintenance workflow.
TABLE OF CONTENTS
Keep Reading
Ever find yourself checking into a luxury hotel and expecting a relaxing stay, only to find a ...
11 Apr 2025
Organizations are witnessing swift changes in the business environment and confronting a ...
8 Apr 2025
Last month, news outlets and the entire internet was abuzz with the return of NASA astronauts ...
3 Apr 2025
What comes first - CMMS or predictive maintenance? If your answer is either, it is correct. ...
28 Mar 2025
Artificial intelligence (AI) talk has become commonplace. Today, engaging in business-focused ...
27 Mar 2025
Imagine a world where machines predict, diagnose, and fix their issues before they fail. This ...
25 Mar 2025
A facility maintenance plan is at the core of a facility’s operations. This organized ...
21 Mar 2025
Think of managing your maintenance operations like managing a championship sports team. Just ...
21 Mar 2025
The maintenance sector is battling a severe talent shortage that threatens to undermine ...
7 Mar 2025
Manufacturing maintenance is the backbone of industrial efficiency, ensuring machines run ...
5 Mar 2025
No one likes playing a guessing game when equipment breaks down. Yet, maintenance teams often ...
4 Mar 2025
The size of the preventive maintenance software market is discussed in millions of dollars, ...
4 Mar 2025
The organizational structure and corporate hierarchy vary from company to company. Large ...
28 Feb 2025
Maintenance procedures are essential for ensuring the longevity and reliability of machinery ...
21 Feb 2025
Sustainability is no longer just a buzzword; it's a critical component of corporate social ...
20 Feb 2025
A Computerized Maintenance Management System (CMMS) relies on accurate, well-organized data ...
18 Feb 2025
In an era where technology drives operational efficiency, Computerized Maintenance Management ...
14 Feb 2025
A Computerized Maintenance Management System (CMMS) is a key component of modern maintenance ...
13 Feb 2025
Introduction Maintenance management is the foundation of maintenance operations in industries ...
11 Feb 2025
Introduction A Computerized Maintenance Management System (CMMS) is software designed to help ...
7 Feb 2025