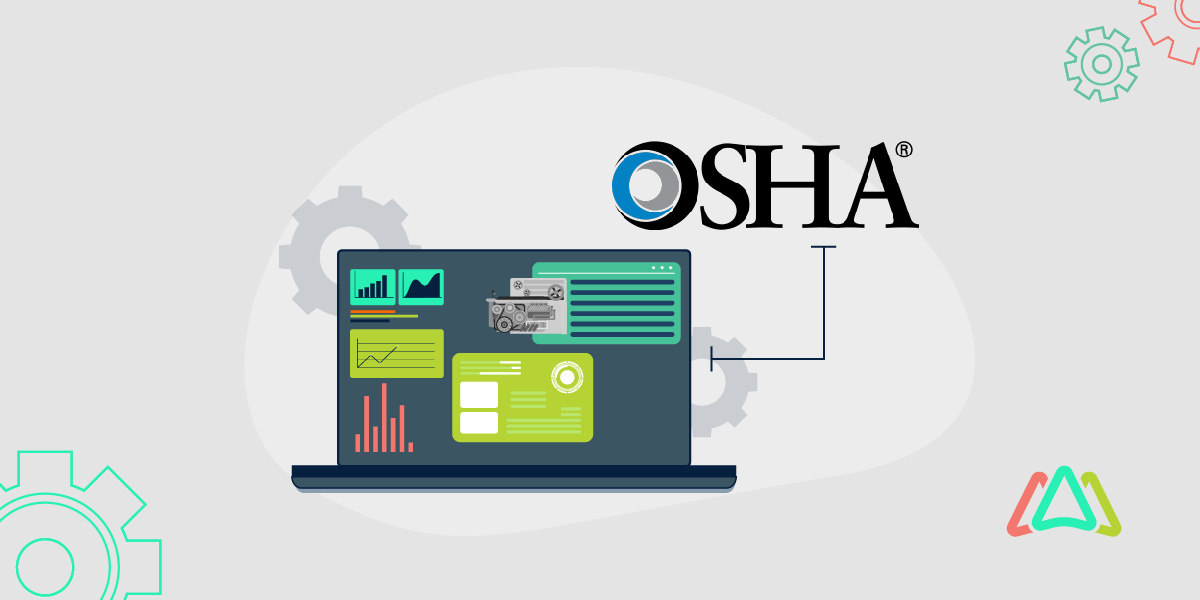
A CMMS for OSHA Compliance
Imagine your business is thriving, your team is productive, and everything seems to be on track. Unexpectedly, an OSHA inspection turns your world upside down. Suddenly, you’re faced with hefty fines, operational disruptions, and the lingering question, “How did we miss this?”
OSHA penalties are no small matter. Each year, businesses lose billions due to non-compliance, whether it’s missed maintenance schedules, incomplete safety records, or overlooked risk assessments. It’s not just about the fines—it’s about the safety of your team and the reputation of your organization.
But let’s be honest: navigating OSHA’s complex regulations can be overwhelming. The good news? You don’t have to do it alone. A CMMS (Computerized Maintenance Management System) could be your ultimate ally in simplifying compliance, automating processes, and keeping your business audit-ready.
Ready to discover how to stay ahead of the curve? Let’s dive in.
What is OSHA Compliance?
OSHA, or the Occupational Safety and Health Administration, is a U.S. government agency dedicated to ensuring safe and healthy working conditions for employees. OSHA compliance means adhering to the safety regulations and standards set by the agency to minimize workplace risks, prevent accidents, and protect workers.
According to OSHA, workplace injuries and illnesses cost businesses over $1 billion in direct costs every week. For industries reliant on equipment and maintenance, non-compliance can significantly amplify these risks, leading to costly fines, accidents, and operational downtime.
Compliance isn’t just about avoiding penalties; it’s about promoting a culture of safety and accountability within your organization while safeguarding both employees and assets.
Key OSHA Maintenance and Compliance Requirements
To meet OSHA standards, organizations must focus on critical areas of safety and maintenance:
Equipment Maintenance
Regular servicing and upkeep of machinery are vital to ensure smooth and safe operations. Preventive maintenance reduces the risk of equipment failures that could result in safety hazards or production downtime.
Safety Audits
Conducting routine inspections is essential to identifying and rectifying potential workplace hazards. These audits promote a safer environment and help organizations stay prepared for regulatory inspections.
Hazard Communication
Providing employees with comprehensive training on hazardous materials and ensuring easy access to safety data sheets are fundamental for OSHA compliance. Clear communication about risks enhances workplace safety and reduces incidents.
Maintenance Documentation
Keeping detailed records of all maintenance activities, including inspections, repairs, and updates, ensures accountability. These documents serve as critical evidence of compliance during audits or investigations.
Challenges of Achieving OSHA Compliance Without a CMMS
Meeting OSHA compliance requirements is no small feat, especially when relying on manual processes. Without a centralized system like a CMMS, organizations often face significant hurdles that can jeopardize both safety and compliance. Your company might face the following challenges when attempting to meet OSHA requirements without a CMMS.
Lack of Proper Documentation
Manually tracking compliance activities often leads to incomplete or misplaced records. OSHA inspectors expect detailed documentation of maintenance, inspections, and safety audits. Failing to produce accurate records during an inspection can result in hefty fines.
Inconsistent Risk Assessments
Assessing workplace hazards manually is prone to human error. Inconsistent or incomplete evaluations leave businesses vulnerable to undetected risks, increasing the chances of accidents or violations.
Difficulty in Tracking Maintenance Schedules and Inspections
Manual systems make it challenging to stay on top of maintenance tasks and inspections. Overlooked schedules or missed inspections can lead to unsafe equipment, which is a direct violation of OSHA standards.
Real-World Consequences
Non-compliance can result in severe penalties, workplace accidents, or even fatalities.
By highlighting these challenges, it’s clear that manual processes not only hinder compliance but also increase operational risks. A CMMS eliminates these pitfalls, offering a streamlined approach to OSHA compliance.
How a CMMS Simplifies OSHA Compliance
Streamlining Preventive Maintenance
A CMMS automates inspection schedules and maintenance tasks, ensuring they are completed on time and consistently. It eliminates the risk of human error that often accompanies manual processes. By maintaining a regular preventive maintenance schedule, businesses can ensure that equipment stays safe, operational, and fully compliant with OSHA standards. This proactive approach reduces downtime, improves workplace safety, and minimizes the likelihood of non-compliance.
Generating Critical Reports for OSHA
A CMMS's reporting capabilities are key for OSHA compliance. Real-time tracking of safety audits, equipment maintenance history, and incident logs ensures all necessary data is readily available during inspections. Features like automated templates and analytics simplify the creation of critical reports, such as inspection checklists or compliance documents. These capabilities provide a clear and organized view of a company’s compliance status, saving time and stress during audits.
Enhancing Risk Assessments
CMMS software plays a vital role in identifying and mitigating workplace hazards. Advanced analytics enable businesses to spot patterns, assess risks, and implement preventive measures. By storing historical data, companies can perform trend analysis to continuously improve safety strategies and maintain compliance with OSHA requirements.
Essential CMMS Features to Achieve OSHA Compliance
A CMMS (Computerized Maintenance Management System) is essential for organizations striving to meet OSHA compliance. Its features are specifically designed to streamline processes, enhance workplace safety, and minimize the risks of non-compliance.
Automated Scheduling and Reminders
One of the most critical features of a CMMS is its ability to automate maintenance and inspection schedules. By sending timely reminders, it ensures tasks are never overlooked, reducing the risk of equipment failure and OSHA violations.
User-Friendly Dashboards
Tracking safety KPIs becomes seamless with a CMMS. Intuitive dashboards provide a real-time view of compliance metrics, allowing businesses to identify and address issues proactively.
Reporting Tools
Built-in reporting tools make compliance documentation easy. From maintenance logs to safety audits, CMMS enables the creation and retrieval of OSHA-ready reports at the click of a button.
Integration Capabilities
A good CMMS software integrates with other safety systems, such as incident management tools or hazard tracking software, creating a centralized compliance ecosystem.
Mobile Accessibility
With mobile-friendly features, staff can access and update maintenance schedules or compliance data in real-time, even from the field, ensuring no detail is missed.
Benefits of Using a CMMS for OSHA Compliance
Implementing a CMMS offers numerous advantages, especially when it comes to OSHA compliance. Here are some key benefits that make it an invaluable tool for businesses:
Reduced Risk of OSHA Violations and Fines
A CMMS helps businesses stay ahead of compliance requirements by automating maintenance schedules, inspections, and documentation. Accurate record-keeping and timely reminders can help organizations avoid costly violations and fines.
Improved Workplace Safety and Employee Well-Being
A CMMS creates a safer work environment by maintaining equipment and promptly addressing potential hazards. This not only prevents accidents but also boosts employee morale, as employees know their well-being is prioritized.
Enhanced Productivity through Preventive Maintenance
A CMMS makes proactive maintenance easier. It minimizes unexpected equipment failures, ensuring smooth operations. This approach saves time, keeps machinery in optimal condition, and boosts overall efficiency.
Cost Savings from Avoiding Downtime and Penalties
Downtime due to equipment failure or non-compliance can be costly. A CMMS prevents such disruptions by ensuring all safety and maintenance tasks are completed on time, saving businesses significant expenses in the long run.
Steps for Successful CMMS Implementation for OSHA Compliance
Implementing a CMMS effectively is essential for maximizing its benefits in achieving OSHA compliance. Here’s a step-by-step guide to ensure a successful implementation:
Assess Organizational Needs
Begin by conducting a thorough gap analysis of your current compliance processes. Identify areas where your organization falls short of OSHA requirements, such as documentation, maintenance schedules, or risk assessments. This evaluation will help you pinpoint the features and capabilities you need in a CMMS.
Choose the Right CMMS
Selecting the ideal CMMS is critical. Look for a system that offers scalability to grow with your organization, reporting capabilities for compliance documentation, and a user-friendly interface to encourage adoption. Integration with existing tools and mobile accessibility should also be key considerations.
Train Staff
The success of a CMMS depends on how well your team uses it. Provide comprehensive training to ensure employees understand the system’s features and how to use them effectively. To encourage engagement and accountability, highlight the CMMS's role in maintaining OSHA compliance.
Continuous Monitoring and Optimization
Once implemented, continually evaluate your compliance status using the CMMS. Monitor key metrics, review reports, and use the system’s analytics to identify trends and areas for improvement. Regular updates and optimizations will ensure your CMMS remains a reliable compliance tool.
By following these steps, you can leverage CMMS to simplify OSHA compliance while improving overall efficiency and safety.
The Path to Proactive OSHA Compliance
OSHA compliance is vital for workplace safety and operational efficiency. Non-compliance risks hefty fines, reputational damage, and, most critically, employee safety.
A CMMS simplifies compliance by automating maintenance tasks, generating accurate reports, and enhancing risk assessments. It equips your organization with the tools to stay ahead of regulatory demands and ensure a safer work environment.
TABLE OF CONTENTS
Keep Reading
Ever find yourself checking into a luxury hotel and expecting a relaxing stay, only to find a ...
11 Apr 2025
Organizations are witnessing swift changes in the business environment and confronting a ...
8 Apr 2025
Last month, news outlets and the entire internet was abuzz with the return of NASA astronauts ...
3 Apr 2025
What comes first - CMMS or predictive maintenance? If your answer is either, it is correct. ...
28 Mar 2025
Artificial intelligence (AI) talk has become commonplace. Today, engaging in business-focused ...
27 Mar 2025
Imagine a world where machines predict, diagnose, and fix their issues before they fail. This ...
25 Mar 2025
A facility maintenance plan is at the core of a facility’s operations. This organized ...
21 Mar 2025
Think of managing your maintenance operations like managing a championship sports team. Just ...
21 Mar 2025
The maintenance sector is battling a severe talent shortage that threatens to undermine ...
7 Mar 2025
Manufacturing maintenance is the backbone of industrial efficiency, ensuring machines run ...
5 Mar 2025
No one likes playing a guessing game when equipment breaks down. Yet, maintenance teams often ...
4 Mar 2025
The size of the preventive maintenance software market is discussed in millions of dollars, ...
4 Mar 2025
The organizational structure and corporate hierarchy vary from company to company. Large ...
28 Feb 2025
Maintenance procedures are essential for ensuring the longevity and reliability of machinery ...
21 Feb 2025
Sustainability is no longer just a buzzword; it's a critical component of corporate social ...
20 Feb 2025
A Computerized Maintenance Management System (CMMS) relies on accurate, well-organized data ...
18 Feb 2025
In an era where technology drives operational efficiency, Computerized Maintenance Management ...
14 Feb 2025
A Computerized Maintenance Management System (CMMS) is a key component of modern maintenance ...
13 Feb 2025
Introduction Maintenance management is the foundation of maintenance operations in industries ...
11 Feb 2025
Introduction A Computerized Maintenance Management System (CMMS) is software designed to help ...
7 Feb 2025