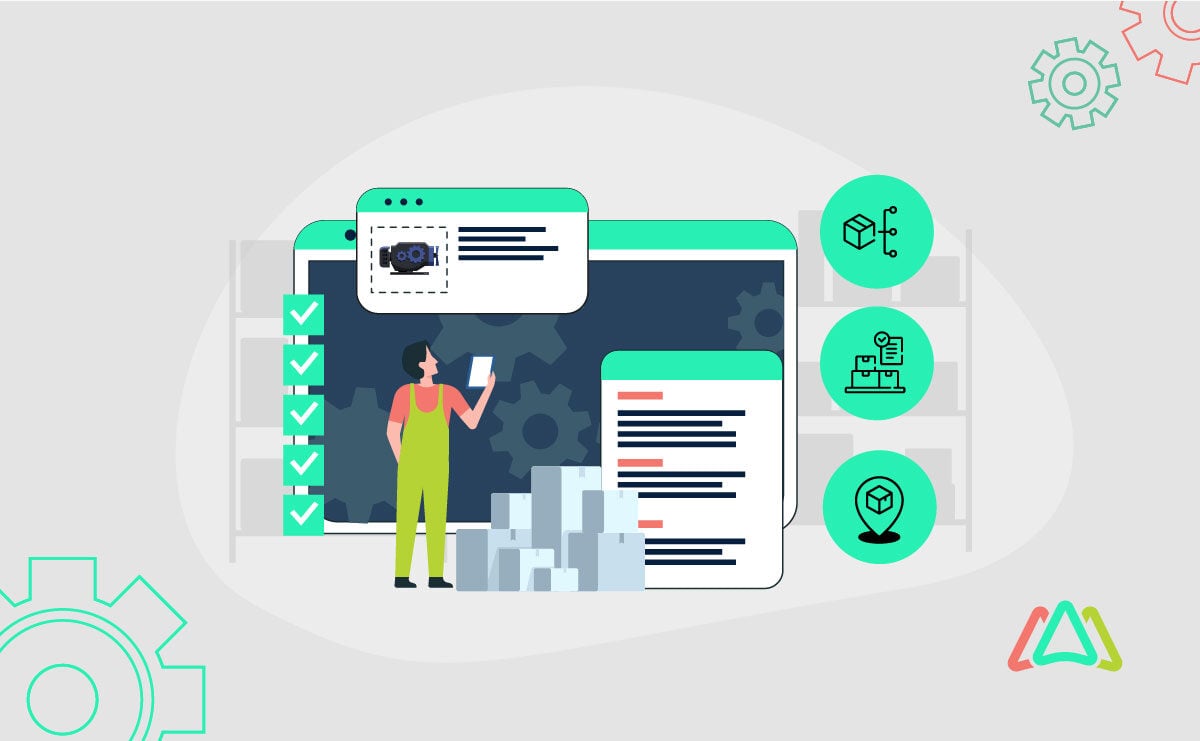
How to Set up Your Parts Inventory in Your CMMS
A parts inventory refers to the comprehensive catalog of all components, tools, and spare parts essential for maintaining and repairing equipment and facilities. This inventory serves as a centralized repository where information about each part, such as its description, part number, location, and quantity, is stored and managed. Proper setup of your parts inventory ensures that your team has quick access to the right parts when they need them, helping you avoid operational disruptions, extended downtime, and expensive rush orders. In this guide, we'll walk you through the key steps to setting up your parts inventory, ensuring you leverage your system to its full potential and maintain a smooth-running operation.
Role of CMMS in Optimizing Parts Inventory
A CMMS helps optimize your parts inventory by organizing items, tracking usage, and setting automated reorder points to prevent stockouts or overstocking. It provides real-time visibility into available parts, ensures proper categorization, and streamlines supplier management. With automated alerts and detailed reporting, a CMMS software ensures that essential parts are always on hand, minimizing downtime and improving overall maintenance efficiency.
Key Components of a CMMS Parts Inventory
- Centralized Inventory Database: A single repository for all parts information, ensuring easy access and management.
- Real-Time Tracking and Reporting Capabilities: Provides up-to-date visibility on inventory levels and usage patterns.
- Automated Reorder Triggers and Alerts: Automatically notifies users when stock reaches reorder points, preventing shortages.
- Integration with Work Orders and Maintenance Tasks: Links parts inventory with maintenance schedules, ensuring the right parts are available when needed.
For a comprehensive solution, check out our Inventory Management System to optimize your parts inventory management.
Benefits of Parts Inventory Management in CMMS
- Improved Equipment Uptime and Reliability: Quick access to essential components reduces downtime.
- Optimized Inventory Levels: Maintains ideal stock levels, minimizing overstocking and stockouts.
- Streamlined Procurement and Vendor Management: Automates reorder points for timely restocking.
- Cost Savings from Predictive Planning: Minimizes emergency purchases and lowers overall costs.
- Data-Driven Decisions: Analytics provide insights to optimize inventory performance and enhance maintenance operations.
Types of Parts to Include in Your Inventory
- Critical Parts: Vital for emergency repairs and preventing downtime.
- Consumables: Frequently used items like lubricants and filters.
- Non-Critical Parts: Infrequently used but necessary for specific equipment.
- Rotating or Spare Equipment Parts: For backup equipment.
- Vendor-Managed Inventory (VMI): Items managed by suppliers.
Step-by-Step Guide to Setting Up Your Parts Inventory in a CMMS
Start by conducting a physical audit of your current parts inventory. This involves going through your storage areas and listing everything you have on hand, from critical components to consumables and tools. As you gather this information, categorize parts into logical groups, such as electrical components, mechanical tools, or safety equipment, while also noting each item’s condition and current stock level. This assessment gives you a clear picture of what you need to keep, reorder, or discard.
Step 2: Inputting Part Information into Your CMMS
Once your audit is complete, the next step is to enter each part's details into your CMMS. Ensure that the following information is recorded:
- Part name and description
- Part number or SKU
- Manufacturer and supplier details
- Location within storage areas
- Unit of measurement (e.g., pieces, liters, meters)
- Current stock level
- Usage frequency (if available)
Accurate data entry ensures your system is ready to track and manage parts effectively. Many CMMS solutions allow you to upload bulk data, saving time if you have large inventories.
Step 3: Organize Storage Locations
It’s important to map physical storage locations to the parts listed in your CMMS. Create a logical layout that aligns with how your team works. This could involve organizing shelves by part type or criticality. In your CMMS, link each part to its physical location using bin numbers, shelf labels, or zone markers. This step ensures that when a technician looks up a part, they know exactly where to find it, speeding up the maintenance process.
Step 4: Set Minimum and Maximum Stock Levels
To avoid running out of parts or overstocking, set minimum and maximum stock levels for each item. Use past usage data or your team’s experience to decide the reorder point. Set up automatic alerts in your CMMS to notify managers when supplies are low, ensuring critical parts are always available without storing too much.
Step 5: Set Up Vendors and Suppliers in CMMS
A successful inventory setup also involves inputting vendor and supplier details into your CMMS. For each part, link relevant vendors to make it easy to reorder components when needed. This step may include:
- Vendor name, contact information, and website
- Preferred vendors for specific parts
- Pricing and lead time information
This integration streamlines the procurement process and makes it easier for your team to manage supplier relationships.
Step 6: Assigning Roles and Permissions for Inventory Management
For effective inventory management, it’s essential to define roles and permissions within your CMMS. Determine who has access to view, edit, and approve inventory transactions. Typical roles might include:
- Technicians can view stock levels and request parts.
- Inventory Managers can add or update part records, manage stock levels, and order parts.
- Supervisors can review inventory usage and approve purchases.
Restricting access to certain tasks reduces errors and ensures accountability.
Step 7: Regularly Update and Maintain Your Inventory
Once your parts inventory is set up, the work doesn’t stop there. Routine maintenance is key to keeping your inventory accurate. Implement regular audits and cycle counts to confirm stock levels and adjust records if needed. Your CMMS should serve as the single source of truth, so encourage technicians to update the system every time parts are issued or received. Periodically review stock levels, reorder points, and supplier performance to make necessary adjustments and keep everything running smoothly.
By following these steps, you'll build an efficient parts inventory system that ensures your maintenance team has what they need when they need it while keeping costs under control.
Best Practices for User Training and Adoption
Proper training ensures your team can confidently manage and utilize the CMMS for inventory tasks. Here are a few effective training methods:
- Workshops and Group Sessions: Organize in-person or virtual workshops to introduce users to the system’s features and workflows. Walk them through how to search for parts, update stock levels, and generate reports.
- Hands-on Sessions: Provide practical, scenario-based exercises that allow users to perform tasks directly in the CMMS, such as logging a part request or updating vendor details.
- Step-by-Step Tutorials: Develop guides or video tutorials for specific processes, like setting reorder points or assigning parts to work orders. These resources offer ongoing support that users can refer back to when needed.
- Role-Specific Training: Tailor sessions to different roles (e.g., technicians, inventory managers) to focus on the tasks they’ll perform most frequently, ensuring relevance and engagement. Work with your CMMS provider and leverage training documentation and resources, as well as live training sessions from their customer success team.
Encouraging User Adoption through CMMS
Beyond training, it’s essential to create a culture that promotes consistent use of the CMMS for inventory management. Here are strategies to encourage CMMS adoption:
- Demonstrate Value: Showcase how the CMMS enhances workflows and minimizes downtime. Highlight specific features that simplify tasks and improve efficiency.
- Share Success Stories: Present real-life success stories and key performance metrics to illustrate the positive impact of the CMMS on operations. This builds trust and confidence among team members.
- Encourage Early Adopters: Encourage team members to engage with the system by offering rewards for early adopters. Recognizing their contributions can foster enthusiasm and promote wider usage across the team.
By combining effective training with strategies that promote adoption, your team will be better equipped to manage inventory efficiently, ensuring long-term success with your CMMS.
Common Mistakes to Avoid When Setting Up Parts Inventory in CMMS
Even with the best intentions, mistakes can hinder the effectiveness of your parts inventory. Here are some common pitfalls to watch out for:
Poor Data Entry
Inaccurate or incomplete information, such as missing part numbers, incorrect stock levels, or vague descriptions, can lead to confusion and delays. It’s important to standardize data entry practices and double-check records to ensure accuracy from the start.
Lack of Regular Updates
Inventory data can quickly become outdated if it isn’t consistently maintained. Failing to update stock levels, reorder points, or vendor information may result in stockouts or excess inventory. Regular audits and encouraging real-time updates in the CMMS prevent these issues.
Overcomplicating the System
While detailed categorization is helpful, creating overly complex classifications can overwhelm users and slow down processes. Strike a balance between organization and simplicity to keep the system user-friendly.
Ignoring Usage Trends and Forecasts
Neglecting to track usage patterns can lead to poor forecasting and inefficient stock management. Monitoring trends helps set optimal stock levels and prevents emergency purchases.
Inadequate Training and Permissions Management
If users aren’t properly trained or given the right permissions, they might struggle with the system or misuse it. Ensure role-specific training and assign clear responsibilities to maintain accountability.
Avoiding these common mistakes will help you set up a parts inventory that runs smoothly, ensuring efficiency, reduced costs, and better maintenance outcomes.
Conclusion
A well-organized parts inventory is the backbone of efficient maintenance operations. It minimizes downtime, reduces unnecessary costs, and ensures that the right parts are available when needed. By properly setting up and maintaining your inventory, you streamline workflows and enhance the overall effectiveness of your maintenance team.
Now that you understand the steps involved, it’s time to put them into practice. Start with an audit of your existing inventory, input accurate data into your CMMS, and implement regular updates to keep things running smoothly. The sooner you act, the quicker you’ll experience the benefits of improved inventory management, fewer delays, smarter spending, and better maintenance outcomes.
Take the first step today and transform how your team manages inventory for long-term success!
TABLE OF CONTENTS
Keep Reading
Ever find yourself checking into a luxury hotel and expecting a relaxing stay, only to find a ...
11 Apr 2025
Organizations are witnessing swift changes in the business environment and confronting a ...
8 Apr 2025
Last month, news outlets and the entire internet was abuzz with the return of NASA astronauts ...
3 Apr 2025
What comes first - CMMS or predictive maintenance? If your answer is either, it is correct. ...
28 Mar 2025
Artificial intelligence (AI) talk has become commonplace. Today, engaging in business-focused ...
27 Mar 2025
Imagine a world where machines predict, diagnose, and fix their issues before they fail. This ...
25 Mar 2025
A facility maintenance plan is at the core of a facility’s operations. This organized ...
21 Mar 2025
Think of managing your maintenance operations like managing a championship sports team. Just ...
21 Mar 2025
The maintenance sector is battling a severe talent shortage that threatens to undermine ...
7 Mar 2025
Manufacturing maintenance is the backbone of industrial efficiency, ensuring machines run ...
5 Mar 2025
No one likes playing a guessing game when equipment breaks down. Yet, maintenance teams often ...
4 Mar 2025
The size of the preventive maintenance software market is discussed in millions of dollars, ...
4 Mar 2025
The organizational structure and corporate hierarchy vary from company to company. Large ...
28 Feb 2025
Maintenance procedures are essential for ensuring the longevity and reliability of machinery ...
21 Feb 2025
Sustainability is no longer just a buzzword; it's a critical component of corporate social ...
20 Feb 2025
A Computerized Maintenance Management System (CMMS) relies on accurate, well-organized data ...
18 Feb 2025
In an era where technology drives operational efficiency, Computerized Maintenance Management ...
14 Feb 2025
A Computerized Maintenance Management System (CMMS) is a key component of modern maintenance ...
13 Feb 2025
Introduction Maintenance management is the foundation of maintenance operations in industries ...
11 Feb 2025
Introduction A Computerized Maintenance Management System (CMMS) is software designed to help ...
7 Feb 2025