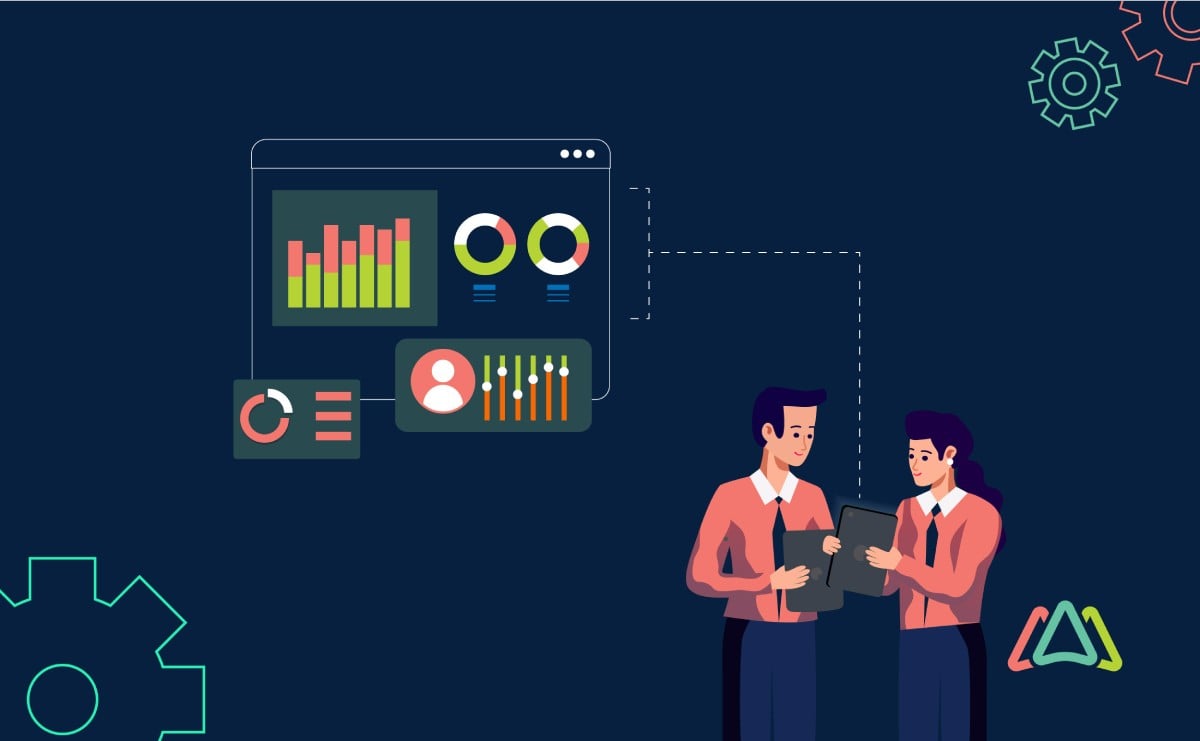
8 Tips for Maintenance Managers Implementing CMMS Software for the First Time
CMMS Software Implementation
Regardless of where you’re at in the Computerized Maintenance Management System (CMMS) exploration process, there’s no better time than now to consider what’s involved when implementing a system once you have it. Maintenance and facility managers should have a solid game plan in place for implementing a CMMS in advance.
A good starting point is understanding exactly what CMMS implementation is all about. In technical terms, CMMS implementation refers to the process of adopting and integrating a CMMS software that helps organizations manage their maintenance operations more efficiently and effectively. Since a CMMS is a software that assists in planning, organizing, tracking, and managing maintenance tasks, work orders, assets, inventory, and related activities within an organization, it needs actual data for it to do its work. Depending on the size and nature of your operation, the data may entail upwards of several thousand records related to equipment, parts, vendors and suppliers etc.
Implementing a CMMS for the first time can be a complex and time consuming undertaking because it involves setting up the system from scratch. According to ReliablePlant.com, collecting all of the necessary and data needed for the CMMS is what gives managers the most grief and one of the biggest reasons for implementation failure. Depending on the size of the maintenance team and operation, effectively gathering all of the data can require 6-12 months.
Determining what data will be collected (equipment model, serial numbers, cost, warranty data, preventive maintenance, procedures and frequencies, parts and parts information) and how that data will be collected is a key ingredient of a successful CMMS implementation plan.
Why Proper CMMS Software Implementation matters?
Proper CMMS software implementation is crucial for several reasons. It helps organizations efficiently manage their maintenance activities, enhance productivity, and achieve cost savings. Here are some of the many reasons why correct CMMS implementation is so important:
Standardization of Processes
CMMS implementation encourages the standardization of maintenance processes across the organization and even those with multiple sites. This results in greater consistency and reliability in all of its operations.
Data-Driven Decision Making
Data-driven decision making is a direct result of effective CMMS implementation. The software provides valuable insights into maintenance operations, enabling informed decision-making. This includes tracking key performance indicators (KPIs), analyzing trends, and identifying areas for improvement.
Regulatory Compliance
For industries with regulatory requirements, comprehensive implementation helps maintain compliance by tracking maintenance activities, inspections, and documentation needed for audits.
Cost Saving
By implementing preventive maintenance strategies and optimizing maintenance schedules, organizations can benefit by avoiding unanticipated and costly breakdowns, as well as emergency repairs. Over time, these initiatives result in significant cost savings.
Having identified some of the key benefits of proper CMMS implementation, let’s review the ways maintenance managers can be helped to successfully undertake this important process. For the purpose of this discussion, we’ll begin our discussion of the implementation process even before a CMMS selection has been made.
8 Tips for Successful CMMS Implementation
1. Define Clear Objectives
The first step is to identify the specific goals you want to achieve through the CMMS implementation. Since no two organizations function exactly alike, your CMMS must be able to achieve your specific goals. Objectives should be broken down into key performance indicators (KPIs) that can measure the success of the implementation and CMMS investment. KPIs can assess how well CMMS operations strategies have improved work order efficiency, reduced downtime, or produced better inventory management. Having clear objectives with KPIs to measure performance will guide the entire process.
2. Involve Stakeholders
The decision to switch to a digital maintenance management solution represents a huge change for the entire organization. It’s therefore essential to get input from all relevant parties, including maintenance technicians, supervisors, as well as end-users of the system. Involving stakeholders in the process goes a long way in reducing anxiety and resistance to change. This can be accomplished by communicating the benefits of the system clearly, addressing concerns, and providing ongoing support to help your team adapt to the new way of working. For these reasons, involving organization stakeholders early on in the process will increase their buy-in to the upcoming change and also ensures that the software will meet their needs . Depending on the size of your organization, this input can be gathered during a series of meetings or through surveys, or perhaps a combination of both methods.
3. Choose the Right Software
Having identified your goals, KPIs and needs, you’re now ready to select a CMMS software that aligns with your organization's size, industry, and requirements. When selecting a CMMS, consider factors such as ease of use, cost, scalability, mobile accessibility, and integration capabilities with other systems you use. Spend time comparing what different vendors in the CMMS marketplace have to offer. Look for differences in system features, pricing, and support options. Ask for demonstrations, free trials, and be sure to check vendors’ track records before making a final decision.
When it comes to seeking references for CMMS vendors, you can contact the vendors directly to ask for client references or case studies that showcase successful implementations. Other sources for CMMS implementation references can be easily obtained by exploring CMMS software reviews, and industry reports. These sources provide insights gathered from other organizations that have already undergone CMMS implementation.
4. Data Migration and Integration
Here comes the fun part! In simple terms, data migration and integration involves feeding your organization’s data into the CMMS so it can do the job you want it to do. This article is geared toward maintenance professionals moving to a CMMS for the first time so for most readers you will not be migrating existing data from other platforms into the new CMMS. CMMS providers will have ways to streamline this process including data import templates that show how data must be configured and documented within the CMMS platform. Import templates are typically Excel or Google Sheets files for the main objects; Assets, Parts, Vendors, Users, Locations, and Work Orders that you would want to upload in bulk rather than inputting these items one at a time. For smaller operations (with 50 or less assets, 5 or less users), inputting the assets, and other objects as you go without a bulk import can be done pretty easily. Once you have selected your provider, ask your representative to share the import templates so you can review them.
If you have existing maintenance data in spreadsheets or other systems, begin by planning how to migrate it to the new CMMS. Smooth data migration and integration with other software such as Enterprise Resource Planning (ERP) systems, are important for accurate and comprehensive asset management. Since a CMMS’s performance is only as good as the data entered into it, ensuring data accuracy and integrity is absolutely essential during the migration process.
5. Customization and Configuration
Tailor your CMMS to match your maintenance workflows and processes. Customize fields, forms, and reports to ensure the software supports your unique processes while keeping it user-friendly. At this stage you will be able to configure asset hierarchies, work order templates, preventive maintenance schedules, user roles, and user permissions. Make sure you review the out of the box field names that the CMMS software includes and determine if they will work for your maintenance operation. Work with your representative to understand if fields can be hidden, added, renamed and made required. Smaller, less complex maintenance operations usually won’t require a lot of customization and custom workflows, and will work fine with the out of the box / default CMMS settings. Larger operations are more likely to require custom configurations.
6. Thorough Training
Provide comprehensive training to all users who will interact with the CMMS. This includes maintenance staff, managers, and administrators. The training process should include hands-on training sessions and resources to address any user difficulties or confusion. CMMS users should be made aware of how to access technical support if and when the need arises.
Training should be specific to the user role. For example, maintenance technicians whose primary focus is updating and completing work orders and PMs, should have training that helps them accomplish this. Training for technicians should not focus on managing user permissions, setting custom configurations, and generating reports. These software functions are geared toward admin users and training should only include them. For best outcomes, break training into role based sessions; administrators, technicians and operators, requesters.
On-site training can be great as it helps establish a more personal relationship with the software provider. On-site training is more expensive and often gets crammed into 1-2 long all day sessions. Less is absorbed in long all day sessions. If budget permits, using a combination of on-site and remote (web conference) training is best. But if you have to choose between on-site and remote web conference training, the latter is better. Web-conference is more flexible, costs less and can be broken down into 30 min or 1 hr. sessions that will be retained. They can also be recorded and used for future training resources. Periodically, there may be times when refresher sessions are appropriate particularly when the CMMS vendor makes software upgrades. Remember, a well-trained team that is comfortable with the software will be more likely to use it effectively and consistently.
7. Start Small
For larger implementations involving multiple sites or locations, start with a pilot. The purpose of starting small is to test CMMS functionality. This limited approach to CMMS deployment allows you to identify and address any issues early on, and refine the system before rolling it out across the entire organization.
8. Rollout, then Monitor and Refine
After adjustments have been made during the pilot implementation, it’s time to deploy the CMMS across the entire organization or targeted departments. After implementation, it’s important to continuously monitor the system's performance and gather feedback from users. Regularly review key performance indicators (KPIs) to track improvements and identify areas that need refinement. Make adjustments in maintenance programs as needed, and continue monitoring.
Conclusion
Remember, successful CMMS implementation is not just a one time exercise; it’s an ongoing process. To ensure that your organization is getting the best value from your CMMS, regularly assess how the system is meeting your objectives and make adjustments as needed to optimize its impact on your maintenance operations.
TABLE OF CONTENTS
Keep Reading
Ever find yourself checking into a luxury hotel and expecting a relaxing stay, only to find a ...
11 Apr 2025
Organizations are witnessing swift changes in the business environment and confronting a ...
8 Apr 2025
Last month, news outlets and the entire internet was abuzz with the return of NASA astronauts ...
3 Apr 2025
What comes first - CMMS or predictive maintenance? If your answer is either, it is correct. ...
28 Mar 2025
Artificial intelligence (AI) talk has become commonplace. Today, engaging in business-focused ...
27 Mar 2025
Imagine a world where machines predict, diagnose, and fix their issues before they fail. This ...
25 Mar 2025
A facility maintenance plan is at the core of a facility’s operations. This organized ...
21 Mar 2025
Think of managing your maintenance operations like managing a championship sports team. Just ...
21 Mar 2025
The maintenance sector is battling a severe talent shortage that threatens to undermine ...
7 Mar 2025
Manufacturing maintenance is the backbone of industrial efficiency, ensuring machines run ...
5 Mar 2025
No one likes playing a guessing game when equipment breaks down. Yet, maintenance teams often ...
4 Mar 2025
The size of the preventive maintenance software market is discussed in millions of dollars, ...
4 Mar 2025
The organizational structure and corporate hierarchy vary from company to company. Large ...
28 Feb 2025
Maintenance procedures are essential for ensuring the longevity and reliability of machinery ...
21 Feb 2025
Sustainability is no longer just a buzzword; it's a critical component of corporate social ...
20 Feb 2025
A Computerized Maintenance Management System (CMMS) relies on accurate, well-organized data ...
18 Feb 2025
In an era where technology drives operational efficiency, Computerized Maintenance Management ...
14 Feb 2025
A Computerized Maintenance Management System (CMMS) is a key component of modern maintenance ...
13 Feb 2025
Introduction Maintenance management is the foundation of maintenance operations in industries ...
11 Feb 2025
Introduction A Computerized Maintenance Management System (CMMS) is software designed to help ...
7 Feb 2025