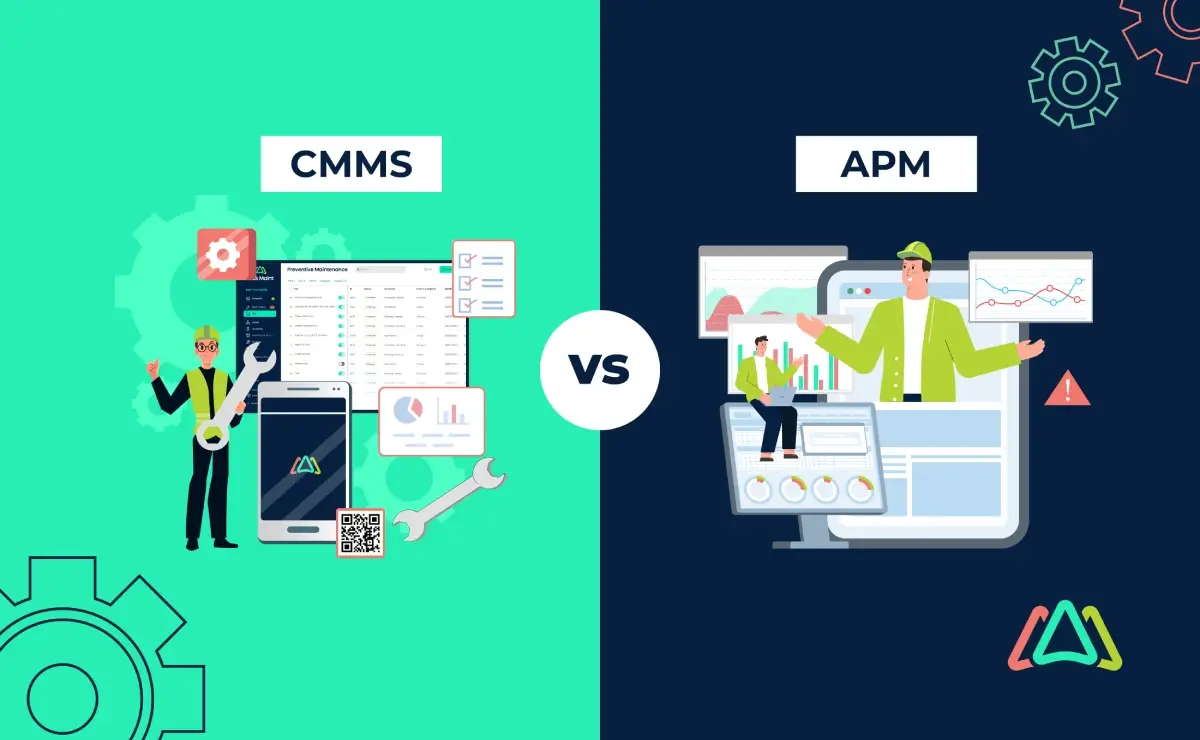
Key Differences & Similarities between CMMS Software & APM
Introduction:
In today's fast-paced and technology-driven world, businesses constantly seek ways to optimize their operations and improve efficiency. Two popular solutions that aid in achieving these goals are Computerized Maintenance Management System (CMMS) software and Asset Performance Management (APM) systems. While both solutions are designed to enhance maintenance and asset management processes, they have distinct features and functionalities. Here, we’ll explore the five key differences between CMMS software and APM systems and discuss where these solutions overlap and their unique characteristics.
Describing CMMS and APM Solutions
CMMS Software
CMMS is a computer-based system that helps organizations manage and maintain their assets, equipment, and facilities. It provides a centralized platform for tracking work orders, scheduling preventive maintenance, managing inventory, and generating reports. The primary goal of CMMS software is to streamline maintenance operations, reduce downtime, and extend the lifespan of assets.
CMMS software is crucial in modern organizational management because it meshes various maintenance functions into one cohesive platform. Beyond its foundational tasks of managing assets and facilities, CMMS software facilitates comprehensive data analysis, enabling organizations to make informed decisions about resource allocation and maintenance strategies.
Drawing on the software’s predictive maintenance capabilities helps maintenance managers identify potential equipment failures preemptively, thus minimizing unplanned downtime and maximizing operational efficiency. Moreover, CMMS software supports regulatory compliance by maintaining detailed maintenance records and ensuring adherence to industry standards and safety protocols. Its implementation improves asset reliability, reduces operational costs, and enhances overall industry productivity.
APM Systems
APM systems, on the other hand, focus on optimizing asset performance and reliability. These systems utilize advanced analytics, machine learning, and predictive maintenance techniques to monitor asset health, identify potential failures, and optimize maintenance strategies. APM systems aim to maximize asset uptime, minimize maintenance costs, and improve overall operational efficiency.
APM systems are designed to enhance asset performance and reliability by fostering a proactive organizational maintenance culture. By continuously analyzing data from various sensors and equipment, APM systems can detect anomalies and trends that might indicate impending issues. This continuous monitoring allows for real-time insights and immediate corrective actions, significantly reducing the risk of unexpected breakdowns.
Additionally, APM systems often integrate with other enterprise systems, providing a holistic view of asset performance across the entire operation. This integration facilitates strategic planning and decision-making, ensuring maintenance activities align with broader business goals. Adopting APM systems leads to a more resilient and agile operation capable of sustaining high-performance levels even in dynamic and challenging environments.
Let’s turn to the areas where CMMS and APM differ and sometimes overlap.
Key Differences Between CMMS and APM Solutions
Scope of Functionality
CMMS Software:
CMMS software's functionality scope extends beyond basic maintenance tasks, encompassing features that enhance operational efficiency and resource management. These systems offer detailed scheduling capabilities, ensuring preventive maintenance is carried out optimally to minimize disruption.
CMMS software also supports compliance management by maintaining accurate inspections, repairs, and regulatory adherence records, which are crucial in heavily regulated industries like healthcare and manufacturing. Furthermore, it facilitates seamless communication between maintenance teams and other departments, fostering collaboration and reducing response times to maintenance issues.
CMMS software generates comprehensive reports and analytics, helping organizations identify trends, optimize inventory levels, and make data-driven decisions to enhance asset reliability and performance.
APM Systems:
APM systems extend their functionality beyond traditional maintenance management by integrating sophisticated analytical tools to understand asset behavior and performance better. These systems utilize machine learning algorithms and predictive analytics to forecast potential issues before they lead to significant problems, enabling more strategic and effective maintenance planning.
By continuously analyzing data from a wide array of sources, including IoT devices and operational databases, APM systems can identify inefficiencies and opportunities for improvement that need to be apparent through standard monitoring methods. This holistic approach allows for dynamic optimization of maintenance schedules, reducing downtime and operational costs.
Additionally, APM systems often integrate with broader enterprise resource planning (ERP) systems, enhancing the ability to align maintenance activities with overall business objectives and improving asset lifecycle management. This makes APM systems particularly valuable in complex, asset-intensive industries such as energy, oil and gas, and transportation, where maximizing asset uptime and performance is critical.
Overlap in Functionality Between CMMS and APM:
CMMS and APM systems aim to enhance asset management by improving maintenance procedures and asset reliability. They overlap in their ability to track and manage maintenance activities, monitor asset health, and provide insights to optimize maintenance strategies. This overlap can be beneficial as it allows organizations to leverage the strengths of both systems, leading to more comprehensive and effective maintenance and asset management.
Integration and Connectivity
CMMS Software:
CMMS software is designed to integrate with other enterprise systems, such as ERP, accounting, and asset management tools, and enhance data visibility and operational efficiency. By connecting seamlessly with these systems, CMMS enables automated data exchange, ensuring that maintenance activities are informed by real-time asset tracking. This integration allows organizations to optimize resource allocation, minimize downtime, and improve overall asset reliability through predictive maintenance strategies.
APM Systems:
In contrast to CMMS software, APM systems offer more sophisticated integration capabilities that extend beyond traditional enterprise systems. These systems leverage real-time data from IoT devices, SCADA systems, and various data sources to provide comprehensive insights into asset performance. By integrating APM systems with these diverse sources, organizations gain a deeper understanding of asset health, enabling proactive maintenance and operational decision-making. This holistic approach enhances asset reliability and supports strategic planning by aligning maintenance efforts with broader business objectives.
Overlap in Integration and Connectivity Between CMMS and APM
CMMS and APM systems integrate with various enterprise systems such as ERP, accounting, and asset management tools, facilitating seamless data exchange and streamlined workflows. They also connect with IoT devices and sensors to capture real-time asset data, enhancing the accuracy and timeliness of maintenance activities.
CMMS and APM systems provide organizations with a comprehensive view of asset health and performance, optimizing maintenance and operational efficiency. This integration capability in both solutions gives organizations a comprehensive view of asset health and performance.
Focus on Optimization
CMMS Software:
CMMS software primarily focuses on optimizing maintenance processes and improving asset reliability. It helps organizations streamline work order management, reduce downtime, and ensure timely maintenance activities.
CMMS software provides tools for tracking maintenance costs, managing spare parts inventory, and generating maintenance reports. By optimizing maintenance operations, CMMS software helps organizations improve asset lifecycle management and reduce overall maintenance costs.
Additionally, CMMS software often includes features for scheduling preventive maintenance tasks, enabling organizations to address potential issues before they lead to equipment failure. This proactive approach improves asset longevity and contributes to safer operational environments by reducing the likelihood of unexpected breakdowns and associated risks.
APM Systems:
APM systems go beyond maintenance optimization by maximizing asset performance and reliability. These systems use advanced analytics and predictive maintenance techniques to optimize maintenance strategies, minimize downtime, and improve asset utilization.
APM systems provide insights into asset health, performance trends, and potential failure modes. By optimizing maintenance activities based on real-time data and predictive analytics, APM systems enable organizations to achieve higher asset uptime and reduce maintenance costs.
Furthermore, APM systems often incorporate machine learning algorithms that continuously learn from historical data, allowing for more accurate predictions of asset behavior and more effective maintenance planning. This advanced optimization level enhances operational efficiency and supports long-term strategic goals by aligning asset performance with business objectives and sustainability targets.
Overlap in Focus on Optimization Between CMMS and APM:
CMMS and APM systems optimize maintenance processes to improve asset reliability and reduce maintenance costs. They streamline work order management, track maintenance costs, and manage spare parts inventory to enhance operational efficiency. While CMMS focuses on maintenance task optimization, APM extends this by using advanced analytics and predictive techniques to maximize overall asset performance and utilization.
Conclusion
CMMS software and APM systems are valuable solutions for improving maintenance and asset management processes. While CMMS software focuses on maintenance management and streamlining operations, APM systems provide advanced analytics and predictive maintenance capabilities to optimize asset performance. Understanding the key differences between these solutions is crucial for organizations to choose the right system that aligns with their needs and goals. Organizations can enhance maintenance efficiency, reduce downtime, and achieve higher asset reliability by utilizing the strengths of CMMS software and APM systems.
TABLE OF CONTENTS
Keep Reading
Asset lifespan is a key concern for executives and maintenance and facility management teams. ...
3 Jul 2025
Your company recently invested funds and time for new CMMS software, and six months later, it ...
1 Jul 2025
As Computerized Maintenance Management Systems (CMMS) become more connected and cloud-based, ...
1 Jul 2025
Edge computing is an innovative technology that enables data to be processed at the source, ...
24 Jun 2025
Facility management has undergone a significant transformation in recent times. Take, for ...
20 Jun 2025
A facility maintenance plan is at the core of a facility’s operations. This organized ...
19 Jun 2025
In the early days, preventive maintenance could be done effectively with a trained eye and a ...
17 Jun 2025
Sticky notes fall off, whiteboard grids get wiped, and spreadsheets never beep when a ...
13 Jun 2025
Handing a slice of your maintenance workload to a contractor is less about “giving up ...
12 Jun 2025
Downtime in enterprise environments doesn’t just mean a stop in operations; it means lost ...
10 Jun 2025
Understanding equipment functionality is crucial for effective repairs. A clear, systematic ...
6 Jun 2025
Maintenance managers know that every unplanned equipment failure is more than a simple ...
5 Jun 2025
What keeps a facility running smoothly? Initially, many of us may zoom in on its equipment, ...
29 May 2025
In today's digital world, every decision needs to pass the test of strategic and operational ...
27 May 2025
The business world is very different from a decade ago. Technological advancements have grown ...
23 May 2025
Picture this: a maintenance technician inspects a complex pump system. Instead of typing a ...
20 May 2025
For most of the 20th century, maintenance teams mainly applied a reactive approach to ...
9 May 2025
Imagine visiting a manufacturing plant where maintenance technicians gather around a large ...
8 May 2025
Maintenance management faces complexities across all industries, escalating with ...
6 May 2025
Ever find yourself checking into a luxury hotel and expecting a relaxing stay, only to find a ...
11 Apr 2025