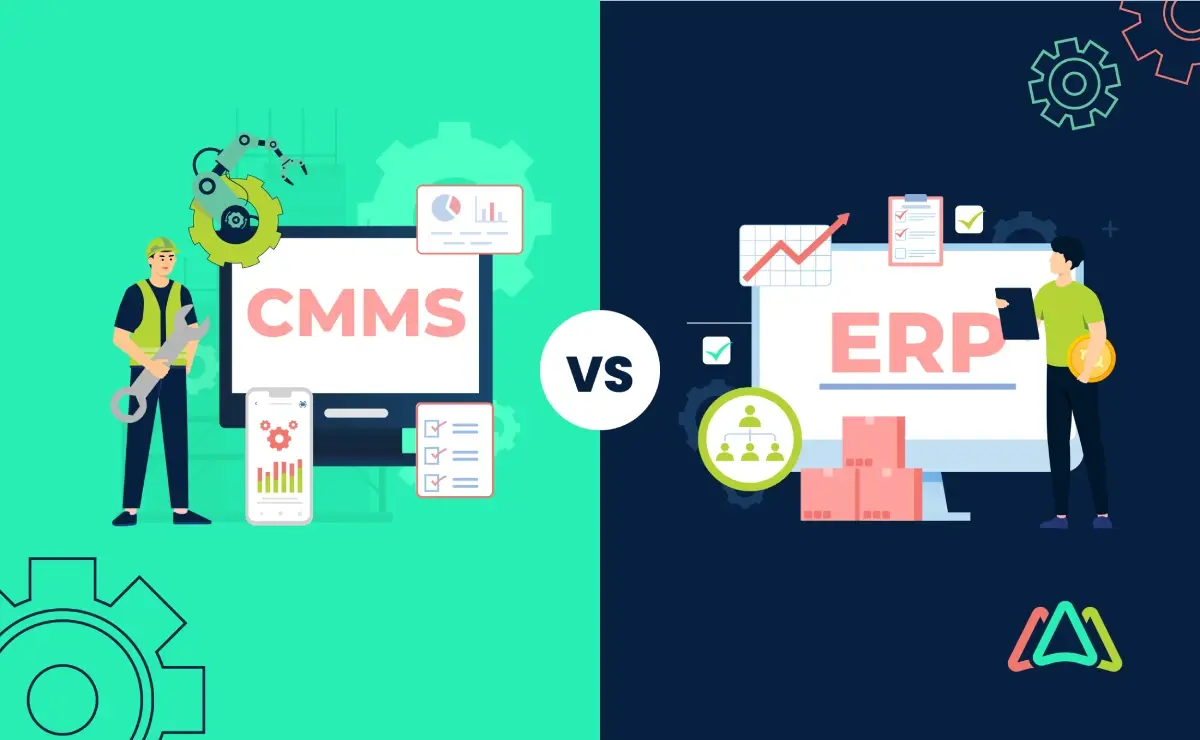
CMMS vs. ERP: Understanding the Differences and Choosing the Right System for Your Business
A Computerized Maintenance Management System (CMMS) is a software application designed to streamline maintenance management tasks for organizations. Its primary functions include scheduling and tracking maintenance activities, managing work orders, maintaining equipment histories, and ensuring compliance with regulatory standards. CMMS helps organizations improve the efficiency and effectiveness of their maintenance operations by providing real-time data and analytics on equipment performance and maintenance tasks. This leads to reduced downtime, increased asset lifespan, and better resource allocation.
On the other hand, Enterprise Resource Planning (ERP) is a comprehensive software system that integrates various business processes and functions into a unified platform. Its primary functions include managing finance, human resources, supply chain, procurement, inventory, and customer relationship management (CRM). ERP systems provide a centralized database that facilitates real-time information sharing across departments, improving coordination, decision-making, and operational efficiency. By automating and standardizing business processes, ERP systems help organizations reduce costs, enhance productivity, and achieve strategic goals.
The primary goal of this article is to elucidate the fundamental differences between CMMS and ERP systems and remove any confusion. While both are essential tools for organizational efficiency, they serve distinct purposes and are designed to address different aspects of business operations. Understanding these differences is important for organizations to make informed decisions about which system to implement based on their specific needs and goals.
What is CMMS?
1. Core Functions and Features
1.1 Maintenance Scheduling and Planning
- Automated Scheduling: CMMS systems automate the scheduling of preventive maintenance tasks, ensuring that equipment is serviced regularly and on time. This helps prevent unexpected breakdowns and prolongs the lifespan of assets.
- Task Planning: Maintenance managers can plan detailed maintenance activities, assign tasks to technicians, and set priorities based on the criticality of the equipment.
1.2 Work Order Management
- Work Order Creation: CMMS allows for easy creation of work orders, detailing the maintenance tasks that need to be performed, along with relevant instructions and deadlines.
- Tracking and Completion: The system tracks the status of work orders from initiation to completion, ensuring that maintenance activities are carried out efficiently and recorded accurately.
1.3 Asset Tracking and Management
- Asset Database: CMMS maintains a comprehensive database of all assets, including information on their location, specifications, maintenance history, and warranty details.
- Asset Lifecycle Management: The system helps manage the entire lifecycle of assets, from acquisition and installation to maintenance and eventual disposal or replacement.
1.4 Inventory and Spare Parts Management
- Inventory Control: CMMS tracks the inventory levels of spare parts and supplies, ensuring that necessary items are available when needed without overstocking.
- Reorder Alerts: The system can generate alerts when inventory levels fall below predefined thresholds, prompting timely reordering and avoiding stockouts.
1.5 Reporting and Analytics
- Performance Metrics: CMMS provides detailed reports and analytics on various aspects of maintenance operations, such as work order completion rates, equipment downtime, and maintenance costs.
- Data-Driven Decisions: By analyzing historical data and identifying trends, maintenance managers can make informed decisions to optimize maintenance strategies and improve overall efficiency.
2. Benefits of CMMS
2.1 Improved Maintenance Efficiency and Reduced Downtime
- Streamlined Processes: CMMS automates and streamlines maintenance processes, reducing the time and effort required to manage work orders and schedule tasks.
- Proactive Maintenance: By ensuring timely and regular maintenance, CMMS helps minimize equipment downtime and prevents costly emergency repairs.
2.2 Better Asset Utilization and Lifespan
- Optimal Performance: Regular maintenance ensures that assets operate at their optimal performance levels, enhancing productivity and efficiency.
- Extended Lifespan: Properly maintained equipment lasts longer, delaying the need for costly replacements and reducing overall capital expenditures.
2.3 Enhanced Compliance and Safety
- Regulatory Compliance: CMMS helps organizations adhere to industry regulations and standards by maintaining accurate records of maintenance activities and ensuring that inspections and certifications are up to date.
- Safety Improvements: By ensuring that equipment is properly maintained and safe to use, CMMS contributes to a safer working environment for employees.
3. Examples of CMMS Solutions
1. Click Maint
- Overview: Click Maint is a user-friendly CMMS solution designed for small to medium-sized businesses. It offers features such as work order management, preventive maintenance scheduling, and inventory tracking.
- Benefits: Click Maint is known for its ease of use, affordability, and effective maintenance tracking capabilities, making it a popular choice for organizations looking to improve their maintenance operations.
2. Limble
- Overview: Limble is a versatile CMMS that provides comprehensive maintenance management tools, including asset tracking, work order management, and real-time reporting. It is designed to be accessible from any device, offering flexibility for maintenance teams.
- Benefits: Limble stands out for its robust feature set and mobile accessibility, which enable maintenance teams to stay connected and productive whether they are on-site or in the field.
3. Fiix
- Overview: Fiix is a powerful CMMS solution that integrates seamlessly with other business systems such as ERP and IoT devices. It offers advanced features like predictive maintenance, automated workflows, and detailed analytics.
- Benefits: Fiix is praised for its scalability, advanced integrations, and strong analytics capabilities, making it an excellent choice for organizations seeking to leverage data-driven maintenance strategies.
What is ERP?
ERP is a software solution that consolidates and integrates the various business processes, aspects, functions and data.
1. Core Functions and Features
1.1 Financial Management and Accounting
- General Ledger: ERP systems centralize financial data, including accounts receivable, accounts payable, and financial reporting, providing accurate insights into financial health.
- Budgeting and Forecasting: Tools for budget creation, forecasting, and variance analysis enable proactive financial management.
1.2 Human Resources and Payroll
- Employee Management: ERP manages employee data, including payroll processing, benefits administration, and performance evaluations.
- Workforce Planning: Tools for workforce planning, recruitment, and training ensure optimal resource allocation and talent management.
1.3 Supply Chain and Inventory Management
- Inventory Control: ERP tracks inventory levels in real-time, optimizing inventory management and reducing stockouts.
- Procurement: Streamlines procurement processes from vendor selection to payment, ensuring cost-effective sourcing and supplier management.
1.4 Customer Relationship Management (CRM)
- Sales and Marketing: CRM tools manage customer interactions and automate sales processes, improving lead generation, conversion rates, and customer retention.
- Service Management: Enhances customer service through case management, service scheduling, and resolution tracking.
1.5 Business Intelligence and Reporting
- Data Analytics: ERP systems analyze business data to generate insights into performance metrics, trends, and forecasts.
- Real-time Reporting: Dashboards and customizable reports provide stakeholders with actionable information for strategic decision-making.
2. Benefits of ERP
2.1 Integrated Business Processes and Data
- Centralized Data: ERP integrates data from various departments into a single platform, eliminating data silos and ensuring consistency across the organization.
- Process Standardization: Standardized workflows and business processes streamline operations and improve cross-functional collaboration.
2.2 Improved Decision-Making through Comprehensive Data Analysis
- Data-driven Insights: ERP systems provide real-time analytics and predictive modeling, enabling informed decision-making and proactive planning.
- Scenario Planning: What-if analysis and scenario modeling help anticipate market changes and optimize resource allocation.
2.3 Enhanced Operational Efficiency and Cost Savings
- Automation: ERP automates repetitive tasks and workflows, reducing manual errors and improving operational efficiency.
- Cost Control: Optimize resource allocation, reduce inventory carrying costs, and negotiate better supplier contracts through ERP-driven insights.
3. Examples of ERP Solutions
3.1 SAP ERP
- Overview: SAP ERP is a market-leading ERP solution known for its scalability and comprehensive suite of modules, including finance, HR, supply chain, and CRM.
- Features: Offers robust analytics, industry-specific functionalities, and integration with other SAP solutions for end-to-end business management.
3.2 Oracle ERP Cloud
- Overview: Oracle ERP Cloud provides a flexible and scalable ERP solution delivered through the cloud, catering to various industries with modules for financials, procurement, project management, and more.
- Features: Built-in AI and machine learning capabilities, real-time reporting, and seamless integration with Oracle's broader cloud ecosystem.
3.3 Microsoft Dynamics 365
- Overview: Microsoft Dynamics 365 is a modular ERP and CRM solution that integrates seamlessly with Microsoft Office 365 and Azure cloud services.
- Features: Offers flexibility to choose specific modules like finance, operations, sales, and customer service, with advanced analytics and AI-driven insights.
ERP systems revolutionize business operations by integrating core functions, optimizing processes, and providing actionable insights for strategic decision-making. Choosing the right ERP solution depends on organizational needs, industry requirements, and scalability considerations to drive sustainable growth and competitive advantage.
Key Differences Between CMMS and ERP
1. Scope and Focus
CMMS: Focused on Maintenance and Asset Management
CMMS (Computerized Maintenance Management System) is primarily focused on managing maintenance activities and optimizing asset performance. It is designed to streamline maintenance operations, track work orders, manage assets, and ensure compliance with maintenance schedules and regulations.
ERP: Comprehensive System Covering Multiple Business Functions
ERP (Enterprise Resource Planning) is a comprehensive software system that integrates core business processes and functions into a unified platform. Beyond maintenance management, ERP systems encompass financial management, human resources, supply chain management, customer relationship management (CRM), and more. ERP aims to improve overall organizational efficiency and facilitate data-driven decision-making across all departments.
2. Functional Depth
CMMS: In-depth Maintenance Management Features
CMMS provides specialized features for maintenance management, such as preventive maintenance scheduling, work order management, asset tracking, and inventory management of spare parts. These functionalities are tailored to meet the specific needs of maintenance teams and technicians.
ERP: Broad Functionality Across Various Business Areas
ERP systems offer extensive functionality across multiple business areas beyond maintenance, including finance, accounting, procurement, HR management, sales, and CRM. Each module within an ERP system is interconnected, allowing for seamless data flow and comprehensive business process management.
3. Integration and Compatibility
CMMS: May Require Integration with Other Systems for Full Functionality
CMMS systems may need to integrate with other enterprise systems, such as ERP, to enhance functionality. Integration ensures that maintenance data can be synchronized with other business processes, such as financial reporting or inventory management.
ERP: Designed to be an All-in-One Solution, Often with Built-in Modules
ERP is designed as a unified system with built-in modules that cover various aspects of business operations. This integration eliminates the need for separate software solutions and facilitates real-time data sharing and reporting across departments.
4. Implementation and Complexity
CMMS: Typically Easier and Faster to Implement
Implementing CMMS software is generally quicker and less complex compared to ERP systems. CMMS implementation focuses primarily on configuring maintenance workflows, training maintenance staff, and ensuring data migration from legacy systems, if applicable.
ERP: More Complex Implementation, Often Requiring Significant Time and Resources
ERP implementations are more complex and involve significant planning, customization, and integration efforts across multiple departments. Organizations often need to allocate ample time and resources for ERP implementation, including comprehensive business process mapping, training sessions, and change management strategies.
Balancing Maintenance and Business Integration
While maintenance and business integration serve distinct purposes, their effective integration is critical for achieving holistic organizational success. Here’s how organizations can strike a balance:
1. Strategic Alignment
Align maintenance strategies with broader organizational goals and priorities to ensure that maintenance activities contribute to overall business objectives, such as cost reduction, customer satisfaction, or innovation.
2. Technology Integration
Implement integrated software solutions, such as ERP systems that include CMMS functionalities, to streamline maintenance operations while ensuring data integration with finance, HR, and other business functions.
3. Continuous Improvement
Foster a culture of continuous improvement where feedback loops from maintenance operations inform process optimizations and innovations across the organization. Leverage data analytics to drive informed decision-making and enhance operational efficiencies.
4. Collaboration and Communication
Facilitate collaboration between maintenance teams and other departments to share insights, coordinate activities, and align strategies. Clear communication channels ensure that maintenance priorities support overall business objectives effectively.
While maintenance and overall business integration address different aspects of organizational management, their synergy is essential for achieving sustainable growth, operational excellence, and competitive advantage in today’s dynamic business landscape. Organizations that prioritize both maintenance excellence and seamless business integration are better positioned to adapt to changing market conditions, meet customer expectations, and drive long-term success.
TABLE OF CONTENTS
Keep Reading
Ever find yourself checking into a luxury hotel and expecting a relaxing stay, only to find a ...
11 Apr 2025
Organizations are witnessing swift changes in the business environment and confronting a ...
8 Apr 2025
Last month, news outlets and the entire internet was abuzz with the return of NASA astronauts ...
3 Apr 2025
What comes first - CMMS or predictive maintenance? If your answer is either, it is correct. ...
28 Mar 2025
Artificial intelligence (AI) talk has become commonplace. Today, engaging in business-focused ...
27 Mar 2025
Imagine a world where machines predict, diagnose, and fix their issues before they fail. This ...
25 Mar 2025
A facility maintenance plan is at the core of a facility’s operations. This organized ...
21 Mar 2025
Think of managing your maintenance operations like managing a championship sports team. Just ...
21 Mar 2025
The maintenance sector is battling a severe talent shortage that threatens to undermine ...
7 Mar 2025
Manufacturing maintenance is the backbone of industrial efficiency, ensuring machines run ...
5 Mar 2025
No one likes playing a guessing game when equipment breaks down. Yet, maintenance teams often ...
4 Mar 2025
The size of the preventive maintenance software market is discussed in millions of dollars, ...
4 Mar 2025
The organizational structure and corporate hierarchy vary from company to company. Large ...
28 Feb 2025
Maintenance procedures are essential for ensuring the longevity and reliability of machinery ...
21 Feb 2025
Sustainability is no longer just a buzzword; it's a critical component of corporate social ...
20 Feb 2025
A Computerized Maintenance Management System (CMMS) relies on accurate, well-organized data ...
18 Feb 2025
In an era where technology drives operational efficiency, Computerized Maintenance Management ...
14 Feb 2025
A Computerized Maintenance Management System (CMMS) is a key component of modern maintenance ...
13 Feb 2025
Introduction Maintenance management is the foundation of maintenance operations in industries ...
11 Feb 2025
Introduction A Computerized Maintenance Management System (CMMS) is software designed to help ...
7 Feb 2025