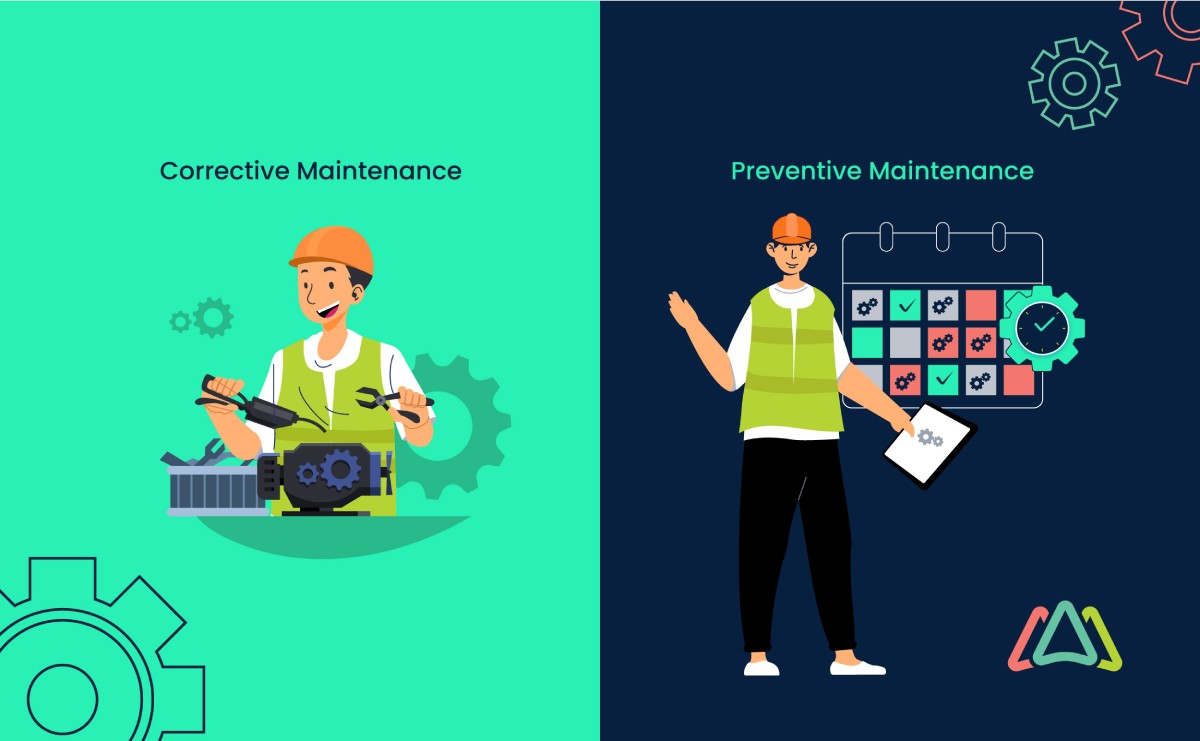
When Should You Use Corrective Maintenance vs. Preventive Maintenance?
Computerized Maintenance Management Software (CMMS) is a powerful tool for organizations seeking ways to improve the efficiency and productivity in their maintenance operations as well as prolonging the longevity of their assets. Among its many feature capabilities, managing work orders and preventive maintenance are by far, used most by CMMS users. Nearly 90% of CMMS users rely heavily on work order management to schedule, assign, and track maintenance tasks.
Most maintenance managers and professionals push toward a planned preventive maintenance strategy and try to move away from reactive, corrective maintenance. Planned maintenance, after all, is predictable, and if done right, extends the life of assets and prevents downtime. But are there times when corrective, reactive maintenance is the right approach and makes most sense? This brings us to the focus of this article which is determining when to use corrective maintenance and when we should use preventive maintenance. Because these represent two different approaches to managing and maintaining equipment, machinery, and systems, the choice between them depends on various factors, including the nature of the equipment, its criticality to operations, budget constraints, and organizational goals.
What is Corrective Maintenance?
Corrective maintenance a.k.a. "repair maintenance" or "breakdown maintenance", refers to the process of identifying, isolating, and fixing problems or faults in a system, machine, or equipment after they have occurred. With this in mind, the primary goal of corrective maintenance is to restore the equipment to its normal operating condition and ensure it functions properly in the most expeditious way.
Key Characteristics of Corrective Maintenance:
Reactive Response
Corrective maintenance is carried out in response to a specific failure or malfunction that arises suddenly. Maintenance in this situation is not planned in advance but is initiated once a problem is detected.
Diagnosis and Repair
Oftentimes, quick repairs involve band aid fixes in order to lessen the impact of production down time. Sometimes, they do the trick but not always. When repairs are needed on the same piece of equipment repeatedly, there’s a need to identify the root cause of the issue. This involves evaluating the extent of the damage, and performing the necessary repairs or replacements.
Cost Considerations
There are times when corrective maintenance may be less expensive in the short term when compared to other maintenance strategies. However, this as needed approach can also lead to higher overall costs in the long run when potential equipment damage, production delays, and increased repair expenses are taken into account.
Suitability for Non-Critical Systems
Corrective maintenance may be preferable for non-critical equipment or systems where downtime does not significantly impact operations or safety. For example, it does not make sense to do preventive maintenance on low cost printers. We “run to fail” and decide if we should repair it when it breaks down or replace it.
What is Preventive Maintenance?
Unlike corrective maintenance that deals with maintenance issues as they occur, preventive maintenance is a proactive maintenance approach that is designed to prevent equipment failures or issues before they happen. It involves performing routine inspections, repairs, and upkeep tasks on machinery and equipment at regular intervals to prevent costly repairs and downtime.
Preventive Maintenance Goals
Reducing Unplanned Downtime
By identifying and addressing potential issues before they cause a breakdown, preventive maintenance helps minimize unexpected downtime. Regardless of industry, equipment downtime is costly as it slows the production of goods and services.
Extending Equipment Lifespan
Regular maintenance can extend the life of equipment, ensuring that it operates efficiently for a longer period. Business managers want to get the highest ROI on the assets that they invest in. Implementing a preventive maintenance strategy works towards maximizing life of critical assets.
Improving Safety
Well-maintained equipment is less likely to malfunction or pose safety hazards to operators and the environment.
Optimizing Performance
Preventive maintenance ensures that equipment operates at its optimal level of performance, which can lead to better productivity and output.
Reducing Repair Costs
Fixing small issues before they escalate into major problems can save a considerable amount of money in the long run.
Types of Preventive Maintenance Approaches
CMMS software is used by many facility and maintenance professionals as a way to automate and track preventive maintenance work orders. Today’s CMMS makes managing preventive maintenance easy with flexible scheduling options, advance notifications, alerts when PMs are overdue, and mobile access. The following is a list of preventive maintenance schedules commonly in used:
Time-Based Maintenance
Tasks are performed at regular time intervals such as hourly, daily, weekly, or monthly. Equipment manuals offer recommendations for optimal maintenance scheduling.
Usage-Based Maintenance
Tasks are performed based on the amount of usage or operational hours of the equipment. For example, replacing a conveyor belt after a certain number of production cycles. Or with vehicles, an example of usage-based PMs are oil and tire changes based on mileage.
Condition-Based Maintenance
Maintenance activities are triggered by the actual condition of the equipment as assessed through various monitoring techniques such as vibration analysis, oil analysis, and thermography.
Prescriptive Maintenance
This is an advanced form of maintenance where AI and machine learning algorithms are used to recommend specific actions to optimize maintenance strategies.
Which Way to Go: Preventive vs Corrective Maintenance?
Having reviewed the basics of corrective and preventive maintenance, it’s now time to consider the factors that will direct maintenance managers in deciding which approach to apply.
Things to Consider
Criticality of the Equipment
Critical equipment is considered essential or high-value equipment that, if it fails, could lead to significant downtime, safety hazards, or production losses. Non-critical equipment are those assets where failures are less impactful and costly.
Historical Data and Failure Patterns
Review past maintenance records and analyze the frequency and nature of failures.
Cost Considerations
In terms of upfront costs and when compared to preventive maintenance, corrective maintenance is generally less expensive in the short term but may lead to higher long-term costs due to unexpected downtime, emergency repairs, and potential collateral damage. Alternatively, preventive maintenance helps avoid costly breakdowns and prolong the lifespan of equipment, and is generally less expensive over the long term.
Regulatory Compliance
Some industries have specific regulations or standards that mandate preventive maintenance practices and these may override corrective maintenance practices.
Equipment Age and Condition
Older equipment might require more frequent preventive maintenance to keep it running efficiently and reliably. Newer equipment may be more reliable and require less frequent checks.
Manufacturer's Recommendations
Follow the manufacturer's guidelines and recommendations for maintenance schedules and procedures. This is especially relevant when it comes to warranties and guarantees.
Resource Availability
Take into account the availability of manpower, tools, spare parts, and time since preventive maintenance may require more resources. However, a purely reactive maintenance approach requires having people available to repair in the event that they happen. Planned preventive maintenance allows maintenance managers to plan maintenance schedules and allocate resources in advance.
Risk Assessment
Assess the risks associated with equipment failure. Consider potential safety hazards, environmental impacts, and financial losses to help determine the best approach. If equipment failure results in high risk situations, preventive maintenance to avoid failures should be adopted.
Decision Making Guidelines
In a perfect world, there should be clear and absolute criteria that separates choosing one approach from the other. However, since equipment performance is influenced by many environmental, mechanical and human influences, the following should be viewed as a guide to decision-making.
Corrective Maintenance |
Preventive Maintenance |
|
---|---|---|
Uses: |
|
|
Advantages: |
|
|
Disadvantages: |
|
|
Another Approach to Consider
Fortunately, maintenance managers don’t have to find themselves in an either-or situation choosing between corrective and preventive maintenance. Thanks to the evolving nature of CMMS solutions, there is now another option that merges the long term benefits of preventive maintenance with the short term costing savings of corrective maintenance. The option is called predictive maintenance (PdM).
What is Predictive Maintenance (PdM)?
Like preventive maintenance, predictive maintenance is a proactive approach using data, analytics, and machine learning techniques to predict when equipment or machinery is likely to fail. Instead of following a fixed schedule or waiting for something to break, predictive maintenance uses real-time and historical data to identify the optimal time for maintenance activities. It is best suited for equipment where there are clear indicators or patterns that precede failure. Its main advantages are minimizing downtime by performing maintenance only when it's actually necessary and reducing costs by avoiding unnecessary maintenance. However, the one added cost factor is the initial investment in monitoring equipment and technology. Its use of sensors and data analytics are especially beneficial in industries where downtime can be extremely costly or safety is a critical concern, such as manufacturing, energy production, aviation, and healthcare.
Conclusion
Business owners and maintenance managers often find themselves in a quandary when it comes to deciding on a maintenance strategy that best meets their organization’s needs. As it turns out, this doesn’t have to be an either-or choice. In the CMMS world, there is no such thing as one size fits all. These systems offer many options when it comes to customizing maintenance schedules.
In arriving at the maintenance management strategy that is the best fit, begin with a cost-benefit analysis to evaluate the trade-offs between corrective and preventive maintenance. Regularly review and adjust maintenance strategies based on performance and changing circumstances. Consider a hybrid approach of corrective and preventive maintenance also known as reliability-centered maintenance or a predictive maintenance approach that uses sensors and data analytics. In the end, the choice in a maintenance strategy depends on factors like the type of equipment, its criticality to operations, and available resources.
TABLE OF CONTENTS
Keep Reading
The maintenance sector is battling a severe talent shortage that threatens to undermine ...
7 Mar 2025
Manufacturing maintenance is the backbone of industrial efficiency, ensuring machines run ...
5 Mar 2025
No one likes playing a guessing game when equipment breaks down. Yet, maintenance teams often ...
4 Mar 2025
The size of the preventive maintenance software market is discussed in millions of dollars, ...
4 Mar 2025
The organizational structure and corporate hierarchy vary from company to company. Large ...
28 Feb 2025
Maintenance procedures are essential for ensuring the longevity and reliability of machinery ...
21 Feb 2025
Sustainability is no longer just a buzzword; it's a critical component of corporate social ...
20 Feb 2025
A Computerized Maintenance Management System (CMMS) relies on accurate, well-organized data ...
18 Feb 2025
In an era where technology drives operational efficiency, Computerized Maintenance Management ...
14 Feb 2025
A Computerized Maintenance Management System (CMMS) is a key component of modern maintenance ...
13 Feb 2025
Introduction Maintenance management is the foundation of maintenance operations in industries ...
11 Feb 2025
Introduction A Computerized Maintenance Management System (CMMS) is software designed to help ...
7 Feb 2025
Introduction Due to a growing awareness of the need to combat climate change, the green ...
6 Feb 2025
When your organization decides to invest in a CMMS (Computerized Maintenance Management ...
4 Feb 2025
Introduction Selecting the right Computerized Maintenance Management System (CMMS) is a ...
31 Jan 2025
More than ever, industries increasingly rely on CMMS (Computerized Maintenance Management ...
30 Jan 2025
Maintenance challenges are a constant struggle, with unplanned downtime costing manufacturers ...
25 Jan 2025
Enterprise Asset Management (EAM) software has become a cornerstone for organizations aiming ...
23 Jan 2025
Effective maintenance management requires systems that can streamline operations and ensure ...
17 Jan 2025
Businesses are increasingly turning to data-driven decision-making as a means to optimize ...
15 Jan 2025