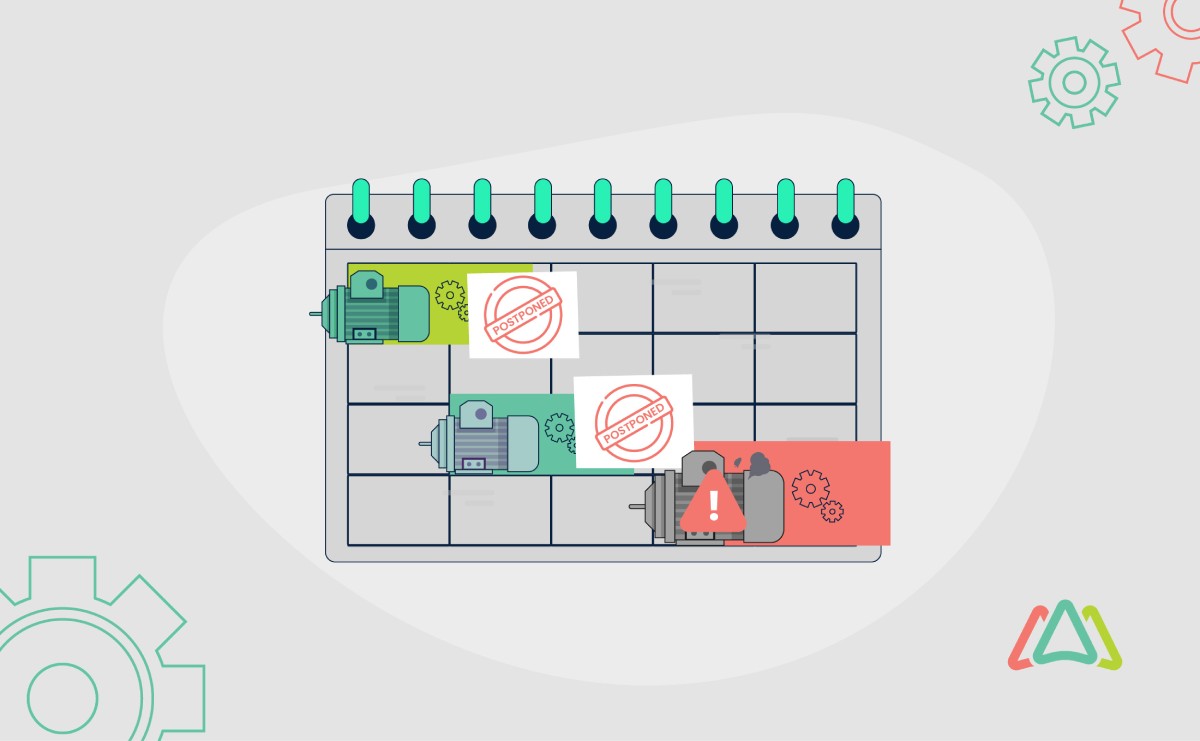
Deferred Maintenance: Insights Into the Hidden Costs of Neglect
Maintenance is an important aspect of preserving the functionality, longevity, and safety of various assets, structures, and systems. However, when maintenance tasks are delayed or neglected, it leads to what is known as deferred maintenance, a phenomenon with far-reaching consequences across sectors.
Deferred maintenance can have a profound impact on both micro and macro levels. On a micro level, it leads to increased wear and tear, reduced efficiency, and a higher likelihood of unexpected failures. On a macro level, the cumulative effect of deferred maintenance across industries compromises safety standards and negatively impacts financials.
Understanding and addressing deferred maintenance is not only a matter of financial prudence but is also essential for the sustainable and reliable functioning of the assets and infrastructure.
What is Deferred Maintenance?
Deferred maintenance is a term used to describe the practice of postponing necessary maintenance activities and repairs on assets, resulting in the deterioration of their condition over time. This delay often leads to a cascade of negative effects, impacting the functionality, safety, and overall value assets.
Characteristic features of deferred maintenance include the neglect of routine inspections, preventive maintenance tasks, and necessary repairs. Over time, this neglect allows small issues to escalate into bigger problems, increasing the scope and cost of eventual repairs.
Causes of Deferred Maintenance
1. Financial Constraints
One of the primary causes of deferred maintenance is financial constraints. Organizations often face budgetary limitations that compel them to defer maintenance activities to allocate funds elsewhere. While this decision may provide short-term relief, it often leads to more significant long-term costs as deferred issues compound over time.
2. Lack of Planning
Inadequate planning is another factor contributing to deferred maintenance. When maintenance is not incorporated into long-term planning strategies, the importance of proactive care can be overlooked. This lack of foresight can result in a reactive rather than a preventive approach, with maintenance efforts triggered only in response to critical failures.
3. Changing Priorities
Shifting priorities within organizations or individuals can lead to deferred maintenance. As objectives and goals evolve, resources may be redirected away from maintenance efforts. This can create a situation where routine upkeep is sacrificed in favor of new initiatives, leaving assets vulnerable to deterioration.
Common Examples of Deferred Maintenance
Deferred maintenance manifests in various forms across different sectors. Some common examples include:
- Structural Repairs: Postponing essential repairs to building foundations, walls, or roofs which can lead to structural instability and compromised safety.
- HVAC Systems: Neglecting routine maintenance of heating, ventilation, and air conditioning (HVAC) systems, resulting in decreased efficiency, higher energy costs, and eventual system failure.
- Roadway Maintenance: Delaying road repairs, such as fixing potholes or resurfacing, can lead to more extensive damage and safety hazards for motorists.
- Equipment Maintenance: Neglecting regular maintenance of industrial machinery, leading to increased wear and tear, decreased productivity, and the risk of costly breakdowns.
Leveraging CMMS to Track Deferred Maintenance
Deferred maintenance is a slippery slope. Proper tracking and monitoring are essential for mitigating negative outcomes. Computerized Maintenance Management Systems (CMMS) offer a systematic approach to managing, tracking, and addressing maintenance needs. Here's a description of how to track deferred maintenance and the role a CMMS plays in the process.
Tracking Deferred Maintenance
Tracking deferred maintenance involves systematic monitoring of assets, identification of maintenance needs, and documenting the postponement of necessary repairs. This can be achieved through a structured approach that includes:
- Regular Inspections: Implement routine inspections to identify potential issues before they escalate. These inspections can be scheduled based on asset type, usage, and industry standards.
- Documentation: Maintain detailed records of all maintenance activities, including completed tasks, pending repairs, and the reasons for deferment. This documentation serves as a valuable reference for decision-making and future planning.
- Asset Prioritization: Prioritize assets based on criticality, safety implications, and potential consequences of deferred maintenance. This helps in focusing resources on high-priority areas.
- Risk Assessment: Conduct a comprehensive risk assessment to evaluate the potential impact of deferred maintenance on operations, safety, and overall asset health.
How Can a CMMS Help with Tracking?
CMMS software is designed to streamline and enhance maintenance management processes. When it comes to tracking deferred maintenance, a CMMS offers several advantages:
- Asset Management: CMMS provides a centralized database for managing assets, allowing users to track the condition, history, and maintenance needs of each asset. This ensures visibility into the status of all equipment and facilities.
- Work Order Management: Users can create, schedule, and track work orders within the CMMS. This includes deferred maintenance tasks, with detailed information on the reasons for delay, estimated costs, and priority levels.
- Preventive Maintenance Scheduling: CMMS allows for the creation of preventive maintenance schedules, ensuring that routine tasks are planned and executed on time. This helps in avoiding the accumulation of deferred maintenance issues.
- Data Analysis and Reporting: CMMS systems generate insightful reports and analytics, providing a clear overview of deferred maintenance trends, costs, and the overall impact on asset performance.
- Mobile Accessibility: Many modern CMMS solutions offer mobile accessibility, allowing maintenance teams to input data, track tasks, and manage deferred maintenance on the go.
The Consequences of Deferred Maintenance
Economic Impact
1. Increased Repair Costs
One of the most immediate and tangible consequences of deferred maintenance is the escalation of repair costs. When routine maintenance tasks are delayed, small issues can snowball into larger problems, demanding extensive repairs. The financial burden of addressing neglected maintenance is often substantially higher than the cost of proactive upkeep. Businesses and individuals may find themselves grappling with unexpected expenses that could have been mitigated through timely maintenance interventions.
2. Decreased Property Value
Deferred maintenance takes a toll on the aesthetic and functional aspects of properties, resulting in a decline in their overall value. Properties that exhibit signs of neglect, such as peeling paint, deteriorating infrastructure, or outdated systems, are less attractive to potential buyers or tenants. Consequently, the market value of such assets tends to decrease, impacting the return on investment for property owners.
3. Potential Legal Consequences
Neglected maintenance can lead to legal ramifications, especially in situations where safety standards are compromised. Failure to address maintenance issues that contribute to accidents or injuries may result in legal liabilities and potential lawsuits. Inadequate maintenance can be viewed as negligence, and property owners or managers may be held legally accountable for the harm caused due to deferred maintenance-related incidents.
Operational Impact
1. Reduced Efficiency
Deferred maintenance negatively impacts the operational efficiency of assets and facilities. Equipment and systems that are not properly maintained are prone to breakdowns, malfunctions, and reduced performance. This can lead to operational inefficiencies, disrupting workflows and hindering productivity. In industrial settings, the lack of equipment reliability may result in production delays and increased downtime.
2. Increased Downtime
Downtime, both planned and unplanned, is a direct consequence of deferred maintenance. Assets that are not adequately maintained are more likely to experience failures and breakdowns, necessitating unplanned shutdowns for repairs. Planned maintenance activities may also take longer and be more extensive when deferred issues accumulate, further increasing operational downtime and impacting overall business continuity.
3. Safety Concerns
Deferred maintenance poses significant safety risks. Whether in residential, commercial, or industrial settings, neglected upkeep can lead to hazardous conditions. From structural weaknesses to malfunctioning safety systems, the consequences of deferred maintenance can compromise the well-being of occupants and workers. Safety concerns not only put people in harm's way but can also result in regulatory penalties and damage to a business’s reputation.
Long-term Repercussions
1. Strain on Budgets
The long-term financial repercussions of deferred maintenance extend beyond immediate repair costs. Continuous neglect strains budgets by necessitating larger, unplanned expenditures. The financial strain may force organizations to allocate resources away from other essential activities or investments, creating a ripple effect across the financial health of a company.
2. Impact on Reputation
Deferred maintenance can tarnish the reputation of property owners, facility managers, and businesses. The visible signs of neglect, coupled with operational inefficiencies and safety issues, can lead to negative perceptions among clients, tenants, and the public. A damaged reputation may result in decreased customer trust, difficulty attracting tenants, and a diminished ability to secure partnerships and new customers.
Industries Affected by Deferred Maintenance
1. Real Estate
In the real estate sector, deferred maintenance has profound implications for property owners, landlords, and tenants alike. Residential properties, commercial buildings, and rental units all face the risk of decreased value and diminished appeal when maintenance is deferred. Peeling paint, leaky roofs, and malfunctioning HVAC systems are not only aesthetically displeasing but can lead to legal disputes and tenant dissatisfaction, ultimately affecting occupancy rates and rental income.
2. Infrastructure and Public Facilities
Critical infrastructure, including roads, bridges, and public buildings, is particularly susceptible to the consequences of deferred maintenance. Neglected repairs can lead to compromised structural integrity, posing safety hazards for the public. Deteriorating infrastructure not only increases repair costs but also impacts transportation efficiency, public services, and overall community well-being.
3. Manufacturing and Industrial Facilities
In industrial settings, deferred maintenance directly influences operational efficiency and production capabilities. Machine breakdowns due to neglected maintenance lead to increased downtime, reduced productivity, and higher repair costs. Manufacturing facilities must prioritize proactive maintenance to ensure the reliability and longevity of their equipment, preventing disruptions that can have cascading effects on supply chains and market competitiveness.
4. Transportation
The transportation sector, encompassing vehicles, fleets, and associated infrastructure, is highly vulnerable to deferred maintenance. For public transit systems, neglected upkeep of buses, trains, and tracks can lead to service disruptions, delays, and safety concerns for passengers. In the private sector, fleet operators may face increased fuel consumption, breakdowns, and vehicle depreciation if maintenance is not conducted at regular intervals.
Each of these industries contends with unique challenges when it comes to deferred maintenance, but the common thread lies in the potential for increased costs, operational inefficiencies, and compromised safety. The importance of proactive maintenance strategies becomes evident as organizations in these sectors seek to maintain asset reliability, operational resilience, and the trust of stakeholders.
Strategies for Mitigating Deferred Maintenance
As organizations across various industries grapple with the challenges posed by deferred maintenance, implementing effective strategies becomes essential to ensure the longevity, reliability, and safety of assets.
1. Proactive Maintenance Planning
1.1 Regular Inspections and Assessments
Regular inspections and assessments form the cornerstone of proactive maintenance planning. Establishing a routine schedule for inspecting assets allows organizations to identify potential issues before they escalate. By conducting thorough assessments, maintenance teams can pinpoint areas that require attention, address minor concerns promptly, and prevent them from evolving into more significant problems. This proactive approach not only enhances asset performance but also contributes to overall operational efficiency.
1.2 Prioritizing Maintenance Needs
Not all maintenance tasks carry equal importance. Prioritizing maintenance needs based on factors such as safety, criticality, and potential consequences of neglect is essential. By categorizing tasks according to urgency and impact, organizations can allocate resources effectively. This ensures that high-priority assets and systems receive the attention they require, reducing the risk of deferred maintenance-related issues that can have severe repercussions.
2. Adequate Budgeting and Resource Allocation
2.1 Long-term Financial Planning
Adequate budgeting is a key component in mitigating deferred maintenance. Long-term financial planning allows organizations to allocate resources strategically, ensuring that maintenance activities are funded consistently. By incorporating maintenance costs into overall budgeting, organizations can avoid the pitfalls of reactive spending, which often accompanies deferred maintenance scenarios. Investing in preventive maintenance as part of a comprehensive financial strategy is a proactive measure that pays dividends in the form of reduced repair costs and increased asset lifespan.
2.2 Emergency Funds
In addition to long-term financial planning, establishing emergency funds specifically earmarked for unforeseen maintenance issues is a prudent strategy. These funds act as a safety net, allowing organizations to address critical maintenance needs promptly without compromising other budgetary allocations. Having emergency funds in place mitigates the risk of deferred maintenance due to sudden financial constraints and helps maintain a proactive stance in managing assets.
3. Utilizing Technology for Maintenance Management
3.1 CMMS (Computerized Maintenance Management Software)
Implementing a CMMS is a transformative step in modern maintenance management. CMMS streamlines the entire maintenance process, from work order creation to asset tracking and reporting. It facilitates proactive planning by providing a centralized platform for managing maintenance tasks, scheduling preventive maintenance, and tracking historical data. CMMS empowers maintenance teams with real-time insights, helping them make informed decisions, prioritize tasks, and prevent the accumulation of deferred maintenance issues.
3.2 Predictive Maintenance Tools
Predictive maintenance tools leverage data and analytics to forecast when equipment or assets are likely to fail. By employing sensors, machine learning algorithms, and historical performance data, organizations can identify potential issues before they occur. This allows for targeted maintenance interventions, reducing the need for reactive repairs and minimizing the risk of deferred maintenance. Predictive maintenance tools are particularly valuable in industries with critical, high-value assets where unplanned downtime can have severe consequences.
Embracing these strategies collectively establishes a comprehensive framework for mitigating deferred maintenance. By leveraging a CMMS, organizations gain a proactive approach to maintenance management, reducing the likelihood of deferred maintenance and its associated risks. The software empowers teams with real-time data, streamlined communication, and effective planning tools, fostering a culture of preventive maintenance rather than reactive responses.
Organizations that prioritize proactive maintenance planning, allocate resources strategically, and leverage technology to enhance maintenance management are better equipped to navigate the challenges posed by deferred maintenance, ensuring the resilience and reliability of their assets.
TABLE OF CONTENTS
Keep Reading
Ever find yourself checking into a luxury hotel and expecting a relaxing stay, only to find a ...
11 Apr 2025
Organizations are witnessing swift changes in the business environment and confronting a ...
8 Apr 2025
Last month, news outlets and the entire internet was abuzz with the return of NASA astronauts ...
3 Apr 2025
What comes first - CMMS or predictive maintenance? If your answer is either, it is correct. ...
28 Mar 2025
Artificial intelligence (AI) talk has become commonplace. Today, engaging in business-focused ...
27 Mar 2025
Imagine a world where machines predict, diagnose, and fix their issues before they fail. This ...
25 Mar 2025
A facility maintenance plan is at the core of a facility’s operations. This organized ...
21 Mar 2025
Think of managing your maintenance operations like managing a championship sports team. Just ...
21 Mar 2025
The maintenance sector is battling a severe talent shortage that threatens to undermine ...
7 Mar 2025
Manufacturing maintenance is the backbone of industrial efficiency, ensuring machines run ...
5 Mar 2025
No one likes playing a guessing game when equipment breaks down. Yet, maintenance teams often ...
4 Mar 2025
The size of the preventive maintenance software market is discussed in millions of dollars, ...
4 Mar 2025
The organizational structure and corporate hierarchy vary from company to company. Large ...
28 Feb 2025
Maintenance procedures are essential for ensuring the longevity and reliability of machinery ...
21 Feb 2025
Sustainability is no longer just a buzzword; it's a critical component of corporate social ...
20 Feb 2025
A Computerized Maintenance Management System (CMMS) relies on accurate, well-organized data ...
18 Feb 2025
In an era where technology drives operational efficiency, Computerized Maintenance Management ...
14 Feb 2025
A Computerized Maintenance Management System (CMMS) is a key component of modern maintenance ...
13 Feb 2025
Introduction Maintenance management is the foundation of maintenance operations in industries ...
11 Feb 2025
Introduction A Computerized Maintenance Management System (CMMS) is software designed to help ...
7 Feb 2025