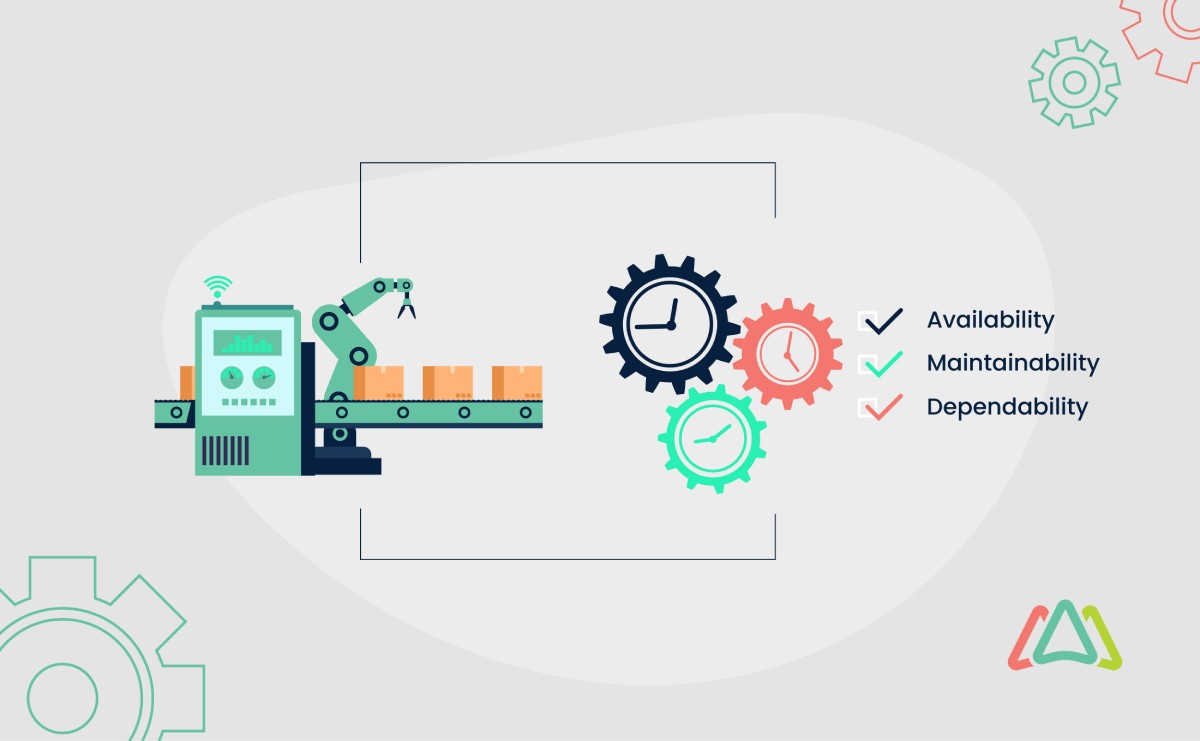
Equipment Reliability: Paving the Way to Sustainable Equipment Performance
Equipment reliability plays an important role across various industries, ranging from manufacturing and energy to healthcare and transportation. In manufacturing, equipment reliability ensures uninterrupted production, minimizes downtime and boosts productivity. In the energy sector, reliable machinery enables efficient power generation and distribution, preventing costly disruptions. Similarly, in healthcare, reliable medical equipment saves lives and improves patient outcomes. The importance of equipment reliability extends to every sector where equipment is used, as it directly impacts operational efficiency and safety.
This article provides a deeper understanding of how equipment reliability serves as a roadmap to sustainable equipment performance, fostering operational excellence and long-term success.
What is Equipment Reliability?
Equipment reliability refers to the ability of machinery, systems, and equipment to consistently perform their intended functions without failures or breakdowns. It is a measure of how well equipment maintains its performance and functionality over time under normal operating conditions. Reliable equipment ensures uninterrupted operations, minimizes downtime and contributes to overall productivity and efficiency.
Reliability is assessed based on several factors, including availability, maintainability, and dependability. Achieving equipment reliability involves implementing effective maintenance strategies, conducting regular inspections and adhering to proper operational and maintenance procedures. It also requires attention to design considerations, and the quality of materials and components used and appropriate training for personnel involved in equipment operation and maintenance.
3 Key Components of Equipment Reliability
To grasp the concept of equipment reliability, it is necessary to understand its key components. These components work together to ensure the smooth and efficient operation of equipment within an organization.
1. Availability: Ensuring Equipment is Operational When Needed
Availability refers to the ability of equipment to be operational and accessible when required. High availability minimizes downtime, maximizes productivity, and enables organizations to meet production schedules and service demands. Achieving high availability involves implementing effective maintenance strategies, such as preventive maintenance, regular inspections and prompt repairs. By proactively addressing issues and implementing robust maintenance practices, organizations can enhance equipment availability and reduce costly interruptions.
2. Maintainability: Ability to Quickly Repair and Restore Equipment
Maintainability focuses on the ease and speed with which equipment can be repaired and restored to its operational state. It encompasses factors such as the design of equipment, accessibility of components, availability of spare parts and the skills of maintenance personnel. Higher levels of maintainability ensures that equipment downtime is minimized, reducing the negative impact on production and delivery of services. Implementing a well-structured maintenance program, training maintenance staff and maintaining an inventory of critical spare parts are key elements for enhancing maintainability.
3. Dependability: Consistent Performance Under Varying Conditions
Dependability refers to the ability for equipment to perform consistently and reliably under different operating conditions. It encompasses factors such as equipment design, quality of materials and components and adherence to operational and maintenance procedures. Dependable equipment is designed to withstand variations in operating parameters, environmental conditions, and workload demands. This component of reliability ensures that equipment can deliver consistent performance, meet production targets and avoid unexpected failures. Regular performance monitoring, data analysis, and equipment inspections help identify potential issues and ensure dependable equipment performance.
Understanding and addressing these key components of equipment reliability helps organizations establish a solid foundation for reliable equipment operation, leading to improved productivity, enhanced customer satisfaction and a competitive edge in their industry.
7 Metrics to Measure Equipment Reliability
Assessing and measuring equipment reliability are essential for organizations to understand the performance and condition of their machinery and systems accurately. They allow maintenance departments to identify areas for improvement, make data-driven decisions and implement strategies to enhance reliability. Various metrics and methods are used to measure equipment reliability, providing valuable insights into the equipment's performance and its impact on overall operations. Here are some metrics used to measure equipment reliability:
1. Mean Time Between Failures (MTBF)
MTBF is a widely used metric that measures the average time elapsed between equipment failures. It provides an indication of how long equipment typically operates before experiencing a failure. Calculating MTBF involves dividing the total operational time by the number of failures within a given period. A higher MTBF value signifies greater reliability.
2. Mean Time to Repair (MTTR)
MTTR measures the average time taken to repair equipment after a failure occurs. It helps organizations assess their ability to restore equipment functionality promptly. By tracking and reducing MTTR, organizations can minimize downtime and increase availability.
3. Failure Rate
Failure rate indicates the probability of equipment failure over a specific period. It is often measured in failures per unit of time, such as failures per hour or failures per thousand operating hours. A lower failure rate implies higher reliability and longer periods of trouble-free operation.
4. Availability
Availability measures the proportion of time that equipment is operational and available for use. It considers both planned and unplanned downtime. Availability is typically calculated by dividing the total uptime by the sum of uptime and downtime, expressed as a percentage. Higher availability indicates greater reliability and operational readiness.
5. Reliability Block Diagrams (RBDs)
RBDs are graphical representations that illustrate the reliability and interdependencies of various equipment components or subsystems. They help identify critical points of failure and assess the overall reliability of complex systems.
6. Failure Modes and Effects Analysis (FMEA)
FMEA is an approach that assesses potential failure modes, their effects and the likelihood of occurrence. It helps organizations prioritize maintenance efforts and implement preventive measures to mitigate risks.
7. Condition Monitoring
Condition monitoring, such as vibration analysis, thermography and oil analysis, provide real-time data on the health and performance of equipment. By monitoring equipment conditions continuously, organizations can detect early warning signs of potential failures and take proactive measures to prevent them.
3 Key Factors that Influence Equipment Reliability
The following are three key factors that significantly impact equipment reliability:
1. Design Considerations
Well-designed equipment takes into account factors such as functionality, performance requirements and the operating environment. It considers potential stressors, such as temperature, humidity and vibrations, and incorporates appropriate safeguards and protective measures. A robust design includes redundant systems, failsafe mechanisms, and easy access for maintenance and repairs. By focusing on sound design principles, organizations can enhance equipment reliability from the outset.
2. Quality of Materials and Components
High-quality materials and components offer better durability, tolerance to stress, and resistance to corrosion. Using substandard or low-quality materials increases the risk of early wear and failure. Organizations should prioritize working with reputable suppliers and manufacturers known for their commitment to quality. Conducting thorough quality checks, including material certifications and component inspections, ensures that only reliable and durable parts are used in equipment assembly or maintenance.
3. Maintenance Practices and Schedules
Regular maintenance activities, such as inspections, cleaning and calibration, help detect and prevent issues before they lead to equipment failures. Implementing a structured maintenance program based on manufacturer guidelines, industry best practices and historical data is essential.
Organizations should use a CMMS to assign preventive maintenance tasks, document maintenance activities and track equipment performance to identify patterns and optimize maintenance intervals.
Proactive maintenance approaches, such as condition-based maintenance and predictive maintenance, can further enhance equipment reliability. Condition-based maintenance utilizes real-time data from sensors and monitoring systems to identify signs of potential failures and triggers maintenance actions. Predictive maintenance employs advanced analytics and machine learning algorithms to forecast equipment performance and determine optimal maintenance intervals.
Deploying a CMMS to Improve Equipment Reliability
1. Effective Equipment Selection and Procurement
1.1 Identify reliable suppliers and manufacturers
When selecting equipment, it is important to choose suppliers and manufacturers with a proven track record of delivering reliable products. A Computerized Maintenance Management System (CMMS) can assist in managing supplier information, maintaining a database of approved vendors and tracking their reliability and performance.
1.2 Evaluate equipment specifications and performance history
Carefully review equipment specifications to ensure they align with your operational requirements and expected performance. Additionally, a CMMS can help capture and analyze historical data on equipment performance, maintenance records and failure rates, providing valuable insights into the reliability of different equipment options.
2. Implement a Proactive Maintenance Plan
2.1 Regular inspections and preventive maintenance
Establish a proactive maintenance program that includes regular inspections and preventive maintenance activities. A CMMS can schedule and track routine inspections, trigger work orders for preventive maintenance tasks and maintain a maintenance history to ensure timely and consistent maintenance efforts.
2.2 Predictive maintenance (PdM) (e.g., condition monitoring, data analytics)
Utilize predictive maintenance to identify potential equipment failures before they occur. Some CMMS applications can integrate with condition monitoring tools, collect real-time data and analyze trends to predict failure patterns and recommend maintenance actions. It enables proactive decision-making based on data-driven insights, optimizing equipment reliability and minimizing downtime.
3. Train Maintenance Personnel
3.1 Provide proper training on equipment operation and maintenance
Well-trained maintenance personnel are essential for maintaining equipment reliability. A CMMS can facilitate training programs by documenting standard operating procedures (SOPs), storing equipment manuals and tracking training records. It ensures that maintenance personnel have easy access to relevant information and promotes consistent and accurate maintenance practices.
3.2 Encourage a culture of ownership and accountability
Fostering a culture of ownership and accountability among maintenance personnel is vital for equipment reliability. A CMMS can assign and track work orders, set deadlines and capture maintenance logs, promoting transparency and accountability. It provides visibility into maintenance activities, encourages timely completion of tasks and supports collaboration among team members.
4. Utilize Technology for Reliability Improvement
4.1 Implement remote monitoring and diagnostics
Remote monitoring technologies, combined with a CMMS, enable real-time monitoring of equipment performance and condition. Sensor data can be transmitted to the CMMS, allowing for remote diagnostics and early detection of anomalies or potential failures. It facilitates proactive maintenance planning and minimizes equipment downtime
4.2 Leverage IoT and data analytics for predictive maintenance
The Internet of Things (IoT) and data analytics play a significant role in predictive maintenance. AI powered CMMS can integrate with IoT devices, collect equipment data, and leverage data analytics to identify failure patterns, optimize maintenance schedules and enable data-driven decisions. It empowers organizations to implement predictive maintenance strategies and maximize equipment reliability.
The Synergy of Equipment Reliability and Maintainability
Equipment reliability is more than just a desirable attribute - it is a fundamental pillar of operational excellence and long-term success in today's competitive landscape. Reliable equipment minimizes disruptions, enhances productivity and improves the overall efficiency of an organization.
Moreover, reliable equipment fosters customer satisfaction and builds a positive reputation. Consistently delivering on commitments, meeting deadlines, and avoiding service disruptions enhance customer trust and loyalty. Reliability becomes a differentiating factor that sets organizations apart from their competitors.
However, in the pursuit of optimal equipment performance, it is important to recognize the interconnection between reliability and maintainability. Reliability focuses on the ability of equipment to consistently perform its intended functions without unexpected failures. Maintainability, on the other hand, refers to the ease and speed with which equipment can be repaired and restored to its operational state. It involves factors such as the design of equipment, accessibility of components, availability of spare parts, and the skills of maintenance personnel.
Reliability and maintainability are interdependent aspects that work hand in hand to ensure equipment operates at its peak efficiency. Reliable equipment is essential for minimizing downtime, improving productivity, and meeting production or service demands. However, even the most reliable equipment may occasionally require maintenance. This is where maintainability becomes crucial - the ability to quickly and effectively address any issues that arise and restore equipment to its operational state.
By focusing on both reliability and maintainability, organizations can create a robust equipment management strategy. A reliable equipment design coupled with a proactive maintenance program ensures that equipment performs consistently and efficiently while minimizing unplanned downtime. The synergy between reliability and maintainability leads to optimized equipment performance, reduced costs, enhanced safety and improved customer satisfaction.
TABLE OF CONTENTS
Keep Reading
Ever find yourself checking into a luxury hotel and expecting a relaxing stay, only to find a ...
11 Apr 2025
Organizations are witnessing swift changes in the business environment and confronting a ...
8 Apr 2025
Last month, news outlets and the entire internet was abuzz with the return of NASA astronauts ...
3 Apr 2025
What comes first - CMMS or predictive maintenance? If your answer is either, it is correct. ...
28 Mar 2025
Artificial intelligence (AI) talk has become commonplace. Today, engaging in business-focused ...
27 Mar 2025
Imagine a world where machines predict, diagnose, and fix their issues before they fail. This ...
25 Mar 2025
A facility maintenance plan is at the core of a facility’s operations. This organized ...
21 Mar 2025
Think of managing your maintenance operations like managing a championship sports team. Just ...
21 Mar 2025
The maintenance sector is battling a severe talent shortage that threatens to undermine ...
7 Mar 2025
Manufacturing maintenance is the backbone of industrial efficiency, ensuring machines run ...
5 Mar 2025
No one likes playing a guessing game when equipment breaks down. Yet, maintenance teams often ...
4 Mar 2025
The size of the preventive maintenance software market is discussed in millions of dollars, ...
4 Mar 2025
The organizational structure and corporate hierarchy vary from company to company. Large ...
28 Feb 2025
Maintenance procedures are essential for ensuring the longevity and reliability of machinery ...
21 Feb 2025
Sustainability is no longer just a buzzword; it's a critical component of corporate social ...
20 Feb 2025
A Computerized Maintenance Management System (CMMS) relies on accurate, well-organized data ...
18 Feb 2025
In an era where technology drives operational efficiency, Computerized Maintenance Management ...
14 Feb 2025
A Computerized Maintenance Management System (CMMS) is a key component of modern maintenance ...
13 Feb 2025
Introduction Maintenance management is the foundation of maintenance operations in industries ...
11 Feb 2025
Introduction A Computerized Maintenance Management System (CMMS) is software designed to help ...
7 Feb 2025