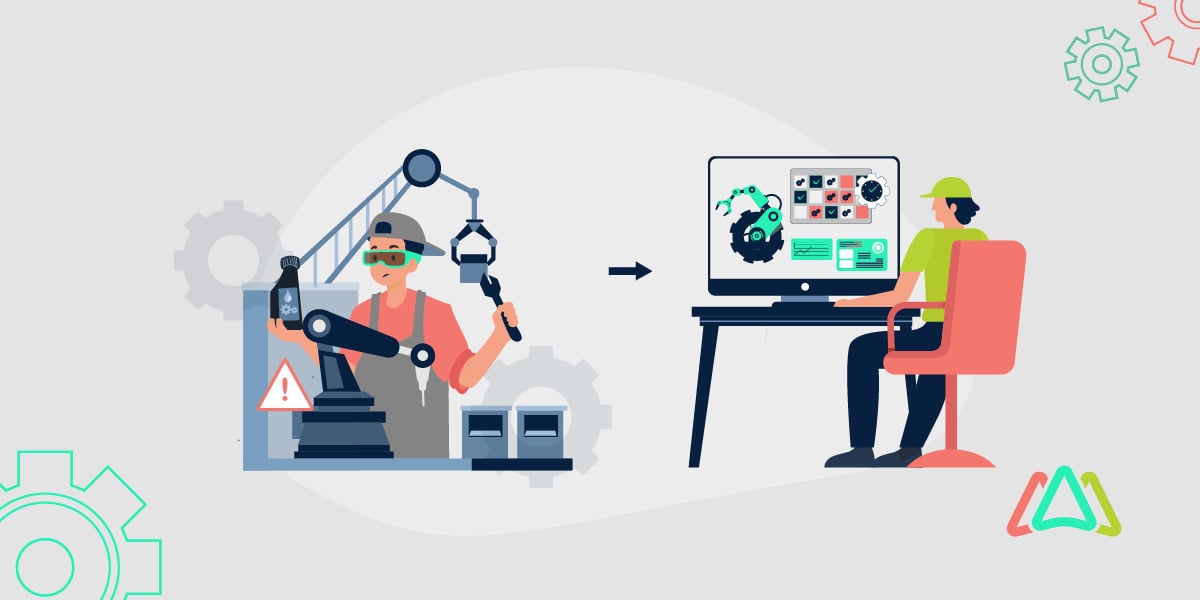
Evolution of Maintenance Management: From Manual Methods to Digital Solutions
Introduction
Maintenance management is the foundation of maintenance operations in industries ranging from manufacturing and healthcare to transportation and facility management. Ensuring that equipment and assets remain operational, reliable, and efficient directly impacts productivity, safety, and profitability. Over the years, the evolution of maintenance management has transformed how organizations approach asset upkeep, shifting from pen-and-paper approaches to sophisticated, data-driven digital solutions.
In the past, maintenance was primarily reactive, fixing equipment only after a failure occurred. With increased competition and tight operational margins, the need for structured maintenance approaches led to the development of preventive maintenance strategies. However, the real breakthrough came with the introduction of Computerized Maintenance Management Systems (CMMS), which marked a significant milestone in the evolution of maintenance management. These systems opened the door to proactive and predictive maintenance approaches, integrating technology to optimize asset performance, reduce downtime, and enhance overall operational efficiency.
Even now, the evolution of maintenance management continues with the rise of cloud-based CMMS, artificial intelligence (AI), and the Internet of Things (IoT), which are making maintenance more predictive and automated. Here, we’ll explore the journey of maintenance management's evolution, tracing its roots from manual record-keeping to cutting-edge digital solutions and highlighting key innovations and their impact on modern industries.
Early Maintenance Practices: Reactive Maintenance
In the early days of industrial maintenance management, organizations operated under a reactive maintenance model, which is often referred to as the "run-to-failure" approach. The equipment was used until it broke down, at which point repairs or replacements were performed. This method required minimal planning, and no specialized tools or tracking systems were needed. It was an easy approach but an inefficient way to manage assets.
While reactive maintenance may seem cost-effective in the short term, the associated expensive emergency repairs, unplanned downtime, and safety risks outweigh any initial benefits. Moreover, the unpredictability of failures meant that organizations had to keep large inventories of spare parts on hand, further increasing costs. Additionally, machine failures often disrupted production schedules, leading to revenue losses and customer dissatisfaction due to unanticipated delays.
As industries grew and machinery became more complex, reactive maintenance's limitations became increasingly evident. Organizations recognized the need for a more structured approach—one that would allow them to anticipate and prevent failures rather than simply react to them. This realization marked the first major shift in maintenance management evolution with the introduction of preventive maintenance strategies.
The Advent of Preventive Maintenance
Preventive maintenance introduced the concept of scheduled interventions, where maintenance tasks were carried out at regular intervals, regardless of whether a failure seemed imminent. Its objective was to reduce the likelihood of unexpected breakdowns and extend the lifespan of critical assets. By following manufacturer recommendations and historical performance data, companies could plan maintenance activities in advance, ensuring that equipment remained in optimal working condition.
The key advantage of preventive maintenance was reducing unplanned downtime. Scheduled maintenance also helped identify minor defects before they escalated into major problems, significantly reducing repair costs. An added benefit of preventive maintenance was the extended lifespan of assets. Through regular maintenance, such as lubrication, calibration, and component replacements, excessive wear and tear on equipment could be avoided, allowing it to function efficiently for longer periods. This not only reduced capital expenditures on new machinery but also enhanced overall operational reliability.
Despite these benefits, early preventive maintenance approaches also had limitations. Since maintenance activities were scheduled based on fixed time intervals rather than real-time asset conditions, some interventions occurred too early or too late. While this was a step forward from reactive maintenance, industries soon sought even more efficient ways to optimize their maintenance strategies, paving the way for the development of Computerized Maintenance Management Systems (CMMS).
Introduction of Computerized Maintenance Management Systems (CMMS)
First Generation (1960s)
The introduction of CMMS in the maintenance management1960s marked a significant milestone in the maintenance management evolution with the introduction of CMMS. These early systems were developed to help large organizations, particularly those in industries such as manufacturing and government infrastructure, manage their growing maintenance needs. The early version of CMMS consisted of basic work orders using punch cards. By today’s standards, this model could be considered rudimentary, even though it was a huge step forward in improving maintenance management.
As technology advanced, CMMS systems evolved from bulky mainframe-based programs in the 1960s and 1970s to more accessible standalone computer solutions in the 1980s. During this period, industries began to recognize the value of centralized maintenance tracking, allowing them to schedule tasks more efficiently and reduce downtime. The 1990s saw the introduction of personal computer-based CMMS, making these systems more user-friendly and affordable for medium-sized businesses. With improved graphical interfaces and database capabilities, organizations could now log maintenance history, track work orders, and generate reports more easily.
The 2000s ushered in cloud-based CMMS solutions. This giant step revolutionized maintenance management by enabling real-time data access from anywhere. These web-based platforms eliminated the need for expensive on-site servers and in-house technicians and allowed organizations to scale their maintenance operations more effectively. The increased use of mobile technology further enhanced CMMS functionality, enabling technicians to access work orders, update records, and receive alerts directly from their smartphones or tablets. Today, CMMS continues to evolve, integrating with AI, IoT, and predictive analytics, shifting maintenance strategies from reactive and preventive to intelligent, data-driven decision-making.
Digital Transformation in Maintenance
Let’s now delve more deeply into the advances just noted above.
Cloud-Based CMMS
The shift to cloud-based CMMS transformed maintenance management by offering real-time access to critical asset data from anywhere. Unlike earlier on-premise solutions, cloud-based CMMS eliminates the need for expensive servers and IT infrastructure while providing automatic updates and enhanced security. In addition, with mobile accessibility, organizations can now manage work orders, track inventory, and monitor asset performance remotely, increasing efficiency and reducing downtime.
Internet of Things (IoT) and Smart Sensors
The integration of IoT and smart sensors has revolutionized maintenance by enabling real-time monitoring of equipment conditions. These sensors collect data on various measures, including temperature, vibration, pressure, and other performance indicators. This data allows maintenance teams to detect early signs of failure well before a breakdown occurs. IoT-driven maintenance boosts efficiency by shifting from time-based to condition-based maintenance, ensuring that interventions happen only when necessary, reducing costs, and optimizing asset lifespans.
Predictive Maintenance and AI
AI-powered predictive maintenance uses machine learning algorithms to analyze historical and real-time asset data, identifying patterns that indicate potential failures. This approach is another way maintenance technicians can anticipate breakdowns and schedule maintenance precisely when needed, preventing costly unplanned downtime. By utilizing AI-driven insights, companies can optimize maintenance schedules, reduce unnecessary servicing, and extend asset longevity, resulting in significant cost savings and operational efficiency.
Integration with Enterprise Systems
Modern maintenance solutions are no longer standalone systems. This is because they now have the capability of integrating seamlessly with Enterprise Resource Planning (ERP), Asset Management Systems (AMS), and other business platforms. This synergistic approach ensures that maintenance activities align with broader business objectives, improving cross-departmental collaboration. For example, linking CMMS with inventory management helps ensure spare parts are available when needed, while integration with financial systems enables better budgeting and cost tracking. These integrations enhance visibility, streamline workflows, and support data-driven decision-making across the organization.
The Future of Maintenance Management with CMMS
AI-Driven Maintenance Optimization
As artificial intelligence (AI) continues to advance, its value for maintenance management lies in its ability to make more automated predictions. AI-driven analytics can process vast amounts of equipment data, identifying patterns that humans might miss. This enables organizations to optimize maintenance schedules, reduce unnecessary servicing, and predict failures with greater accuracy. AI is also being leveraged to remove as many mundane and repetitive tasks as possible. Some CMMS platforms are leveraging AI to identify double entry, assist with populating data, and make recommendations to users based on past examples, saving users time whenever possible.
Digital Twins and Virtual Simulations
Digital twin technology is set to revolutionize maintenance by creating virtual replicas of physical assets. These digital models use real-time data from IoT sensors to simulate equipment behavior, allowing maintenance teams to test different scenarios, predict failures, and optimize performance without disrupting actual operations. By integrating digital twins with CMMS and AI, organizations can move from reactive and preventive maintenance to fully predictive and prescriptive strategies.
Sustainability and Green Maintenance Practices
An emphasis on sustainability is increasingly driving the future of maintenance management. Organizations are adopting green maintenance practices by reducing energy consumption, minimizing waste, and implementing eco-friendly asset management strategies. Advances in IoT and AI help optimize resource use, ensuring machines operate efficiently with minimal environmental impact. Additionally, condition-based maintenance reduces unnecessary part replacements, resulting in cost savings and a more sustainable maintenance approach.
Challenges in Implementing Digital Maintenance Solutions
High Initial Investment Costs
One of the biggest challenges organizations face when adopting digital maintenance solutions like CMMSs is the high upfront costs associated with software, hardware, and infrastructure upgrades. Implementing a CMMS, IoT-enabled sensors, or AI-driven predictive maintenance tools is generally accompanied by a significant financial investment. Additionally, companies must consider the costs of training staff, data migration, and system integration, which can make smaller businesses hesitant to transition from traditional maintenance methods.
Workforce Training and Adoption
Moving from manual or legacy maintenance systems to a digital solution requires proper training and a cultural shift within the organization. Many maintenance teams, especially those accustomed to traditional methods, may resist adopting new technologies due to unfamiliarity or fear of job displacement. Ensuring a smooth transition involves providing comprehensive training, ongoing support, and demonstrating how digital tools can enhance rather than replace human expertise.
Data Security and System Integration
Digital maintenance solutions rely heavily on cloud computing, IoT, and interconnected enterprise systems, making data security a major concern. Cybersecurity threats, data breaches, and unauthorized access to critical maintenance data can pose risks to operations and livelihoods.
Future Trends in Maintenance Management
Hyperautomation in Maintenance
Hyperautomation refers to the integration of AI, machine learning, IoT, and robotic process automation (RPA) to create fully automated workflows. This trend will minimize human intervention in routine maintenance tasks, enabling predictive diagnostics, automated work order generation, and real-time asset monitoring. As hyper-automation advances, maintenance teams will shift from manual troubleshooting to strategic decision-making, further improving efficiency and reducing operational costs.
Blockchain for Maintenance of Data Integrity
As maintenance management continues to become more digital, ensuring data integrity and security is crucial. Blockchain technology offers a decentralized and tamper-proof ledger system that records maintenance activities, asset history, and compliance logs. With blockchain, organizations can enhance transparency, prevent data manipulation, and streamline audits, especially in industries with strict regulatory requirements, such as aerospace and healthcare.
Augmented Reality (AR) for Maintenance Training and Execution
Augmented Reality (AR) is transforming how maintenance teams conduct inspections, repairs, and training. AR-enabled smart glasses or mobile applications provide real-time, interactive guidance that overlays digital instructions onto physical equipment. This process allows technicians to troubleshoot issues efficiently, reducing downtime and errors.
Conclusion
The evolution of maintenance management from early pen-and-paper methods to digital solutions has revolutionized how organizations maintain their assets and drive their bottom line. What started as reactive and preventive strategies has now transitioned into predictive and AI-driven maintenance using technologies like CMMS, IoT, and cloud computing. These advancements have not only improved equipment reliability and reduced downtime but also optimized resource utilization, leading to cost savings and enhanced operational efficiency.
At the same time, challenges such as high implementation costs, workforce training, and cybersecurity risks must be carefully managed. However, with effective implementation, organizations adopting CMMS and other digital solutions will gain a competitive edge, ensuring long-term asset performance, sustainability, and resilience in an increasingly technology-driven world.
TABLE OF CONTENTS
Keep Reading
Ever find yourself checking into a luxury hotel and expecting a relaxing stay, only to find a ...
11 Apr 2025
Organizations are witnessing swift changes in the business environment and confronting a ...
8 Apr 2025
Last month, news outlets and the entire internet was abuzz with the return of NASA astronauts ...
3 Apr 2025
What comes first - CMMS or predictive maintenance? If your answer is either, it is correct. ...
28 Mar 2025
Artificial intelligence (AI) talk has become commonplace. Today, engaging in business-focused ...
27 Mar 2025
Imagine a world where machines predict, diagnose, and fix their issues before they fail. This ...
25 Mar 2025
A facility maintenance plan is at the core of a facility’s operations. This organized ...
21 Mar 2025
Think of managing your maintenance operations like managing a championship sports team. Just ...
21 Mar 2025
The maintenance sector is battling a severe talent shortage that threatens to undermine ...
7 Mar 2025
Manufacturing maintenance is the backbone of industrial efficiency, ensuring machines run ...
5 Mar 2025
No one likes playing a guessing game when equipment breaks down. Yet, maintenance teams often ...
4 Mar 2025
The size of the preventive maintenance software market is discussed in millions of dollars, ...
4 Mar 2025
The organizational structure and corporate hierarchy vary from company to company. Large ...
28 Feb 2025
Maintenance procedures are essential for ensuring the longevity and reliability of machinery ...
21 Feb 2025
Sustainability is no longer just a buzzword; it's a critical component of corporate social ...
20 Feb 2025
A Computerized Maintenance Management System (CMMS) relies on accurate, well-organized data ...
18 Feb 2025
In an era where technology drives operational efficiency, Computerized Maintenance Management ...
14 Feb 2025
A Computerized Maintenance Management System (CMMS) is a key component of modern maintenance ...
13 Feb 2025
Introduction A Computerized Maintenance Management System (CMMS) is software designed to help ...
7 Feb 2025
Introduction Due to a growing awareness of the need to combat climate change, the green ...
6 Feb 2025