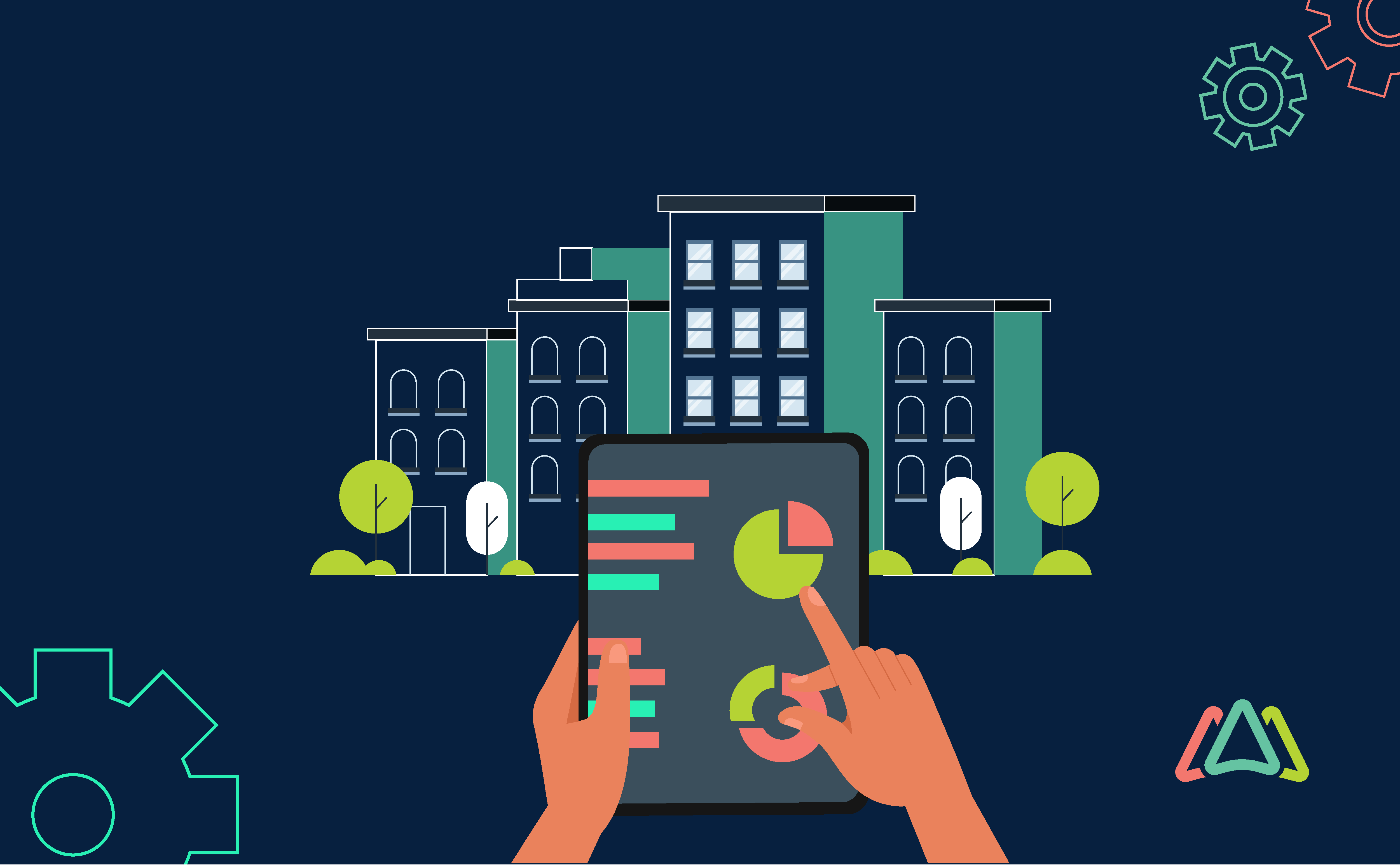
Facility Condition Assessment (FCA): Ensure the Longevity of Your Facilities
Facility Condition Assessment (FCA), is an important component of maintenance management and operations. It’s the compass that guides facility managers, property owners, and investors in maintaining and optimizing their physical assets.
FCA is a systematic process that evaluates the condition of a facility's various components, such as structural elements, mechanical systems, electrical systems, and more. It provides a comprehensive snapshot of the facility's health, helping stakeholders understand what is working well and what needs attention. This assessment extends beyond mere inspections; it involves data collection, analysis, and the strategic planning necessary to keep facilities in optimal working condition.
What is Facility Condition Assessment?
A Facility Condition Assessment (FCA) is a systematic and structured process used to evaluate the condition, performance, and overall health of a building or facility's physical components and systems. It's a detailed examination that goes beyond simple visual inspections. FCA involves collecting data, analyzing it, and generating comprehensive reports to provide a holistic view of the facility's current state.
During an FCA, various aspects of a facility are assessed, including:
- Structural Components: The integrity of the building's structure, including walls, floors, roofs, and foundations.
- Mechanical Systems: Assessment of HVAC (Heating, Ventilation, and Air Conditioning) systems, plumbing, and other mechanical equipment.
- Electrical Systems: Examination of electrical systems, including wiring, panels, and safety features.
- Life Safety Systems: Evaluation of fire suppression, alarms, and emergency exit systems.
- Interior and Exterior Elements: Inspection of interior spaces, finishes, and the condition of the building's exterior, including walls, windows, and landscaping.
Facilities and Industries that Need FCA
Types of Facilities
Commercial Buildings: Businesses with office spaces, retail stores, and shopping centers rely on FCAs to maintain comfortable and safe environments for customers and employees.
- Industrial Facilities: Manufacturers and factories use FCAs to ensure the smooth operation of machinery and to guarantee the safety of workers.
- Healthcare Facilities: Hospitals and medical centers employ FCAs to maintain a sterile and safe environment for patients, healthcare professionals, and visitors.
- Educational Institutions: Schools, colleges, and universities rely on FCAs to create conducive learning environments, ensuring the safety and comfort of students and faculty.
- Government Buildings: Federal, state, and local government facilities use FCAs to preserve and extend the life of public assets such as courthouses, libraries, and municipal buildings.
- Residential Properties: Property owners, including homeowners' associations and apartment complex managers, use FCAs to ensure the safety and quality of residential buildings.
- Infrastructure: Transportation authorities and organizations managing bridges, roads, and tunnels employ FCAs to maintain critical infrastructure.
- Hospitality Industry: Hotels and resorts use FCAs to provide guests with a comfortable and safe experience, enhancing guest satisfaction and loyalty.
- Cultural and Recreational Facilities: Museums, theaters, and sports complexes employ FCAs to preserve historic sites and ensure the safety of patrons.
Industries and Sectors
- Real Estate: Real estate developers and investors rely on FCAs to assess the condition of properties they intend to purchase, informing their investment decisions.
- Healthcare: Healthcare organizations use FCAs to comply with strict regulations and to create a safe, healing environment for patients.
- Manufacturing: Manufacturers utilize FCAs to optimize production processes by ensuring the reliability of equipment and machinery.
- Education: Educational institutions use FCAs to allocate budgets effectively, maintaining educational facilities at a high standard.
- Government: Governments at all levels employ FCAs to manage public assets, allocate resources efficiently, and maintain transparency.
Key Stakeholders in Facility Condition Assessment (FCA)
1. Facility Managers
Facility managers are at the forefront of FCAs. They oversee the day-to-day operations and maintenance of a facility. FCAs help them make data-driven decisions, prioritize repairs, and ensure that facilities are safe and efficient.
2. Property Owners
Property owners, whether individual homeowners or real estate investors, need FCAs to protect their investments. These assessments provide insights into the condition of their properties, enabling informed decisions about maintenance, renovations, or sales.
3. Investors
Investors in real estate and facilities use FCAs during due diligence. Before acquiring properties, they conduct FCAs to evaluate asset conditions and assess the potential return on investment. FCAs help them make informed choices about their investment portfolios.
Facility Condition Assessment (FCA) Process
STAGE 1: Pre-Assessment Preparation
1.1 Gathering Documentation
Before commencing the physical inspection, thorough preparation is essential. This begins with gathering documentation related to the facility. This documentation may include architectural drawings, maintenance records, equipment manuals, and historical reports. These documents provide a clearer understanding of the facility's history, design, and past maintenance practices.
- Document Storage: CMMS serves as a centralized repository for maintenance records, equipment manuals, and historical data. It ensures easy access to essential documentation during the pre-assessment phase.
1.2 Identifying Goals and Objectives
Defining clear goals and objectives is vital to the success of an FCA. This phase involves establishing what the assessment aims to achieve. Goals might include identifying critical maintenance needs, assessing compliance with safety regulations, or determining the feasibility of facility expansion. Setting objectives helps guide the assessment process and ensures that it aligns with the organization's broader mission.
- Benchmarking and Progress Tracking: CMMS software allows you to set maintenance goals, track progress, and align objectives with the FCA process, ensuring that assessments are conducted with specific goals in mind.
STAGE 2: On-Site Inspection
2.1 Inspection Teams
On-site inspections involve assembling a qualified team of professionals with expertise in various aspects of facility assessment. This team may include structural engineers, HVAC specialists, electricians, and other experts. Their collective knowledge and skills enable a thorough examination of all facility components.
- Team Coordination: CMMS tools facilitate communication and collaboration among inspection team members by providing a platform to schedule inspections, assign tasks, and share findings.
2.2 Data Collection Methods
During the on-site inspection, the assessment team employs various data collection methods. This typically involves a detailed visual examination of every aspect of the facility, supplemented by measurements, testing, and data recording. Modern FCAs often leverage technology, such as handheld devices or mobile apps, to streamline data collection and ensure accuracy.
- Mobile Access: Many CMMS vendors offer mobile apps, enabling inspectors to input data directly into the system while on-site, streamlining data collection and reducing manual paperwork.
STAGE 3: Data Analysis
3.1 Prioritization of Assets
Once the data is collected, it must be analyzed to determine the condition and performance of each asset within the facility. Prioritization is a important step that involves assessing the criticality of each asset. High-priority assets may be those essential for safety, compliance, or core operations. This step ensures that resources are allocated effectively.
- Asset Data: CMMS systems store asset information, including maintenance history and data on asset condition. This information aids in asset prioritization during the analysis.
3.2 Condition Assessment
In this phase, assets are evaluated individually, considering factors like wear and tear, age, and performance. A standardized rating system is often used to assign condition scores, helping to quantify asset health. These scores guide decision-making by indicating which assets need immediate attention and which can be scheduled for maintenance or replacement in the future.
- Condition Tracking: CMMS records asset condition scores and historical data, allowing for trend analysis and more accurate condition-based maintenance.
STAGE 4: Reporting and Documentation
4.1 Assessment Report Components
One of the key outcomes of the FCA process is the assessment report. This report provides a detailed account of the assessment findings and recommendations. It includes the following components:
- Executive Summary
- Facility Overview
- Asset Inventory Condition
- Assessment Results
- Prioritization and Recommendations
- Cost Estimates
- Visual Documentation (photographs, diagrams)
- Compliance and Safety Issues
- Long-Term Strategies
- Report Generation: Some CMMS software can generate comprehensive assessment reports, including asset information, condition scores, and maintenance recommendations, saving time and ensuring consistency in reporting.
4.2 Visual Documentation
Visual documentation plays an important role in the FCA report. Images and diagrams provide a visual record of the facility's condition. These visuals help convey the assessment's findings to stakeholders, auditors, and decision-makers, enhancing the report's clarity and impact.
- Image Attachments: CMMS software allows the assessment team to attach images and visual documentation directly to asset records, making it easy to include up to date photographs in assessment reports.
STAGE 5: Cost Estimation
5.1 Repair and Replacement Costs
Cost estimation is a fundamental aspect of the FCA process. It involves calculating the anticipated costs of repairs or replacements for assets that require attention. These cost estimates help with budget planning and resource allocation.
- Cost Tracking: CMMS tracks maintenance costs for each asset, helping in the estimation of repair and replacement costs.
5.2 Life Cycle Cost Analysis
Beyond immediate repair costs, FCAs often include life cycle cost analysis. This considers the total cost of owning, operating, and maintaining an asset over its expected lifespan. This analysis helps organizations make informed decisions about whether to repair, replace, or upgrade assets based on long-term cost considerations.
Read our article on asset lifecycle management to learn more.
- Historical Data: CMMS stores historical maintenance data, which can be used to calculate life cycle costs and replacement asset value providing a more accurate picture of the total cost of ownership.
Benefits of Facility Condition Assessment
Facility Condition Assessment (FCA) is not merely a routine inspection; it is a strategic process that yields a multitude of benefits for organizations. Understanding these advantages is key to appreciating the importance of conducting regular FCAs.
1. Cost Savings
1.1 Preventive Maintenance
- Reduced Repair Costs: FCAs identify issues before they become major problems, enabling timely and cost-effective preventive maintenance. Fixing small issues early can prevent them from developing into costly, emergency repairs. Implementing a preventive maintenance program reduces the chance of equipment breakdowns and ensures facilities are well maintained.
- Extended Asset Lifespan: Regular maintenance and timely repairs identified through FCAs extend the useful life of assets, avoiding the need for early replacements.
1.2 Budget Planning
- Informed Budgeting: FCAs provide data-driven insights into future maintenance and replacement needs. This information empowers organizations to create accurate budgets, allocate resources efficiently, and avoid unexpected financial strains.
- Financial Predictability: With FCA findings, organizations can anticipate maintenance costs, reducing financial uncertainty and ensuring that adequate funds are set aside for facility upkeep.
2. Risk Mitigation
2.1 Safety and Compliance
- Occupant Safety: FCAs help identify safety hazards within a facility, allowing for prompt rectification to ensure the safety and well-being of occupants, employees, and visitors.
- Regulatory Compliance: By assessing compliance with safety regulations and codes, FCAs help organizations avoid costly penalties and legal liabilities
2.2 Legal and Regulatory Compliance
- Avoiding Legal Issues: FCAs assist in identifying and rectifying issues that can lead to legal disputes or penalties for non-compliance with environmental, health, and safety regulations.
- Documentation: Properly documented FCAs serve as proof of due diligence in complying with regulations, potentially reducing legal liabilities.
3. Asset Management
3.1 Asset Tracking
- Efficient Inventory: FCAs establish a comprehensive inventory of assets, allowing organizations to track their condition, location, and maintenance history accurately.
- Reduced Asset Loss: Better asset tracking minimizes the risk of losing track of assets, reducing replacement costs and improving resource utilization.
3.2 Strategic Decision-Making
- Informed Capital Planning: FCAs provide data that supports long-term strategic decisions about asset management. Organizations can decide whether to repair, replace, or upgrade assets based on their condition and cost considerations.
- Resource Allocation: FCAs help allocate resources more effectively, ensuring that investments are directed toward assets that are critical to the organization's mission and objectives.
4. Long-Term Sustainability
4.1 Enhancing Facility Lifespan
- Extended Facility Life: Through preventive maintenance and timely repairs, FCAs contribute to prolonging the life of facilities, reducing the need for premature replacements.
- Preserving Value: Facilities that are well-maintained retain their value over time, protecting the organization's investment.
4.2 Sustainability Initiatives
- Energy Efficiency: FCAs often identify opportunities for energy efficiency improvements, aligning with sustainability goals and reducing operational costs.
- Environmental Impact: By assessing and mitigating environmental risks, FCAs contribute to environmentally responsible practices, which are increasingly important in today's business landscape.
Challenges in Facility Condition Assessment
While Facility Condition Assessments (FCAs) offer numerous benefits, they are not without their challenges. Understanding and addressing these challenges is important for organizations seeking to maximize the effectiveness of their assessment processes.
1. Data Accuracy
1.1 Challenges with Data Collection
Inconsistent Data Sources: FCAs often involve gathering data from various sources, which can lead to discrepancies and inaccuracies. Data may be missing or outdated, making it challenging to obtain a complete picture of the facility's condition. Multiple data sources often have differing naming conventions, standards and other inconsistencies.
Human Error: The data collection process relies on inspectors and technicians. Human error, such as misinterpretation of data or equipment oversight creates inaccuracies.
1.2 Subjectivity in Assessments
- Assessor Bias: Assessments may be subjective, influenced by the assessor's background, experience, or personal judgment. This subjectivity can lead to variations in condition scores and prioritization.
- Lack of Standardization: Inconsistent assessment criteria and rating systems across assessors or organizations can further compound subjectivity issues.
2. Budget Constraints
2.1 Allocating Resources
- Competing Priorities: Organizations often face multiple financial demands. Allocating resources for maintenance and repairs identified in FCAs may be challenging when there are competing priorities, such as expansion projects or other operational needs.
- Limited Funding: Budget constraints can limit the ability to address all identified issues promptly, potentially leading to deferred maintenance and increased costs down the line.
2.2 Balancing Maintenance Costs
- Cost vs. Benefit: Deciding when to repair, replace, or upgrade assets requires a careful cost-benefit analysis. Balancing the cost of immediate repairs against the potential long-term savings is a complex challenge.
- Resource Allocation: Properly allocating resources for both short-term maintenance and long-term capital projects while maintaining budgetary control is a delicate balance.
3. Technology Adoption
3.1 Advancements in FCA Tools
- Rapid Technological Changes: FCA tools and technology are continuously evolving. Staying current with the latest advancements can be challenging for organizations that lack dedicated IT resources or a technology adoption strategy.
- Integration Complexity: Implementing new FCA tools and integrating them with existing systems may be complex and time-consuming, requiring skilled personnel.
3.2 Training and Implementation
- Personnel Training: Adequate training is essential to ensure that assessors and facility management staff can effectively use FCA technology. Training programs may require a significant investment of time and resources.
- Managing Change: The transition to new technology or assessment methodologies may face resistance from staff accustomed to traditional processes. Managing this change is important for successful implementation.
Best Practices in Facility Condition Assessment
Effective Facility Condition Assessment (FCA) is important for maintaining facilities optimally. By following best practices, organizations can ensure that their assessments yield accurate data, meaningful insights, and actionable recommendations.
1. Regular Inspections
1.1 Frequency and Timing
- Scheduled Inspections: Establish a regular schedule for FCAs based on the type of facility and its usage. Annual assessments are common, but high-traffic facilities may require more frequent inspections.
- Timing: Consider the timing of assessments carefully. Conducting them during periods of low occupancy or downtime minimizes disruption to daily operations.
1.2 Seasonal Considerations
- Seasonal Variation: Recognize that a facility's condition can vary seasonally. Assessments should take into account seasonal factors, such as weather-related wear and tear.
- Climate-Specific Maintenance: Tailor maintenance plans to address climate-specific issues, such as preparing for winter in colder regions.
2. Comprehensive Data Management
2.1 Software Solutions
- CMMS and FMS: Implement Computerized Maintenance Management Systems (CMMS) or Facility Management Software (FMS) to streamline data collection, analysis, and reporting. These tools enhance data accuracy and provide a centralized platform for managing facility information.
- Asset Management Modules: Utilize CMMS or FMS modules dedicated to asset management to maintain an up-to-date inventory of all facility assets.
2.2 Digital Documentation
- Photographic Evidence: Incorporate digital documentation, including photographs and videos, into FCAs. Visual evidence enhances understanding by providing a clearer “picture” of current state.
- Document Scanning: Digitize historical records, blueprints, and maintenance documents and store them in a CMMS, making them easily accessible during assessments.
3. Professional Expertise
3.1 Hiring Qualified Assessors
- Certified Professionals: Employ certified facility assessors and inspectors who possess the expertise required for accurate assessments. Certification bodies such as the International Facility Management Association (IFMA) offer relevant programs.
- Multi-Disciplinary Teams: Assemble multi-disciplinary teams with expertise in architecture, engineering, systems, and safety to ensure comprehensive evaluations.
3.2 Continuous Training
- Ongoing Education: Invest in ongoing training and professional development for assessors to keep them updated on the latest technologies, assessment methodologies, and industry best practices.
- Standardization: Standardize assessment practices and criteria across your organization to minimize subjectivity and ensure consistent results.
4. Integration with Facility Management
4.1 Aligning FCA with Facility Management
- Collaboration: Foster collaboration between Facility Condition Assessment teams and Facility Management teams. Align assessment findings with long-term facility management strategies and goals.
- Data Sharing: Enable data sharing between the FCA and FM teams to ensure that maintenance and repairs are prioritized based on assessment results.
4.2 Real-time Monitoring
- CMMS Integration: Integrate FCAs with your CMMS or FMS for real-time monitoring of asset conditions. This allows for immediate action on critical maintenance needs.
- Predictive Maintenance: Leverage predictive analytics within your CMMS to forecast maintenance requirements based on historical data and FCA findings.
Green Building Assessments and FCA: A Sustainable Synergy
As sustainability becomes an increasingly important consideration for organizations, Facility Condition Assessments (FCAs) are evolving to encompass "Green Assessments." These assessments focus on evaluating a facility's environmental impact and adherence to sustainable building practices.
Key Aspects of Green Assessments:
- Environmental Impact: Green Assessments examine a facility's carbon footprint, resource consumption, and waste management practices. They identify opportunities for reducing environmental impact.
- Sustainable Materials: Evaluators consider the use of eco-friendly materials in construction and renovations, assessing their durability and impact on the environment.
- Energy Sources: Assessments include a review of the facility's energy sources, including renewable energy systems, and suggest improvements for increased energy efficiency.
- Indoor Air Quality: Green Assessments analyze the facility's ventilation systems, air quality, and use of non-toxic materials to promote occupant health.
- Compliance with Green Building Standards: Assessors ensure that the facility adheres to green building standards such as LEED (Leadership in Energy and Environmental Design) and offers recommendations for compliance.
Energy Efficiency Considerations in FCAs:
- Utility Consumption Analysis: FCAs examine energy consumption patterns and utility bills to identify areas where energy efficiency improvements can be made.
- HVAC Systems: Assessors evaluate heating, ventilation, and air conditioning (HVAC) systems for efficiency, suggesting upgrades or optimizations that reduce energy consumption.
- Lighting: Assessing lighting systems helps identify opportunities to switch to energy-efficient lighting technologies, such as LED, and implement lighting controls.
- Insulation and Sealing: FCAs assess building insulation and the sealing of windows and doors to improve thermal efficiency and reduce energy waste.
- Renewable Energy Potential: For sustainable facilities, assessors explore the feasibility of integrating renewable energy sources like solar panels or wind turbines.
Impact of Regulatory Changes on FCA Practices
The regulatory landscape regarding building codes, environmental standards, and safety regulations is continually evolving. These changes have a profound impact on FCA practices.
- Compliance Assessment: FCAs must adapt to incorporate new compliance standards and ensure that facilities meet updated requirements for safety, accessibility, and environmental sustainability.
- Legal Liability: Regulatory changes can affect an organization's legal liability. FCAs must thoroughly evaluate facilities to identify potential compliance gaps and liabilities.
- Documentation and Reporting: Regulatory changes often require more extensive documentation and reporting. FCAs must align with these new reporting requirements to avoid penalties.
- Sustainability Mandates: As sustainability regulations become more stringent, FCAs play an important role in evaluating a facility's compliance with green building codes and sustainable practices.
Incorporating FCAs into your facility management strategy is an investment in the future, one that pays dividends through improved operational efficiency, reduced risks, and a more sustainable and environmentally responsible approach to facility maintenance.
TABLE OF CONTENTS
Keep Reading
Ever find yourself checking into a luxury hotel and expecting a relaxing stay, only to find a ...
11 Apr 2025
Organizations are witnessing swift changes in the business environment and confronting a ...
8 Apr 2025
Last month, news outlets and the entire internet was abuzz with the return of NASA astronauts ...
3 Apr 2025
What comes first - CMMS or predictive maintenance? If your answer is either, it is correct. ...
28 Mar 2025
Artificial intelligence (AI) talk has become commonplace. Today, engaging in business-focused ...
27 Mar 2025
Imagine a world where machines predict, diagnose, and fix their issues before they fail. This ...
25 Mar 2025
A facility maintenance plan is at the core of a facility’s operations. This organized ...
21 Mar 2025
Think of managing your maintenance operations like managing a championship sports team. Just ...
21 Mar 2025
The maintenance sector is battling a severe talent shortage that threatens to undermine ...
7 Mar 2025
Manufacturing maintenance is the backbone of industrial efficiency, ensuring machines run ...
5 Mar 2025
No one likes playing a guessing game when equipment breaks down. Yet, maintenance teams often ...
4 Mar 2025
The size of the preventive maintenance software market is discussed in millions of dollars, ...
4 Mar 2025
The organizational structure and corporate hierarchy vary from company to company. Large ...
28 Feb 2025
Maintenance procedures are essential for ensuring the longevity and reliability of machinery ...
21 Feb 2025
Sustainability is no longer just a buzzword; it's a critical component of corporate social ...
20 Feb 2025
A Computerized Maintenance Management System (CMMS) relies on accurate, well-organized data ...
18 Feb 2025
In an era where technology drives operational efficiency, Computerized Maintenance Management ...
14 Feb 2025
A Computerized Maintenance Management System (CMMS) is a key component of modern maintenance ...
13 Feb 2025
Introduction Maintenance management is the foundation of maintenance operations in industries ...
11 Feb 2025
Introduction A Computerized Maintenance Management System (CMMS) is software designed to help ...
7 Feb 2025