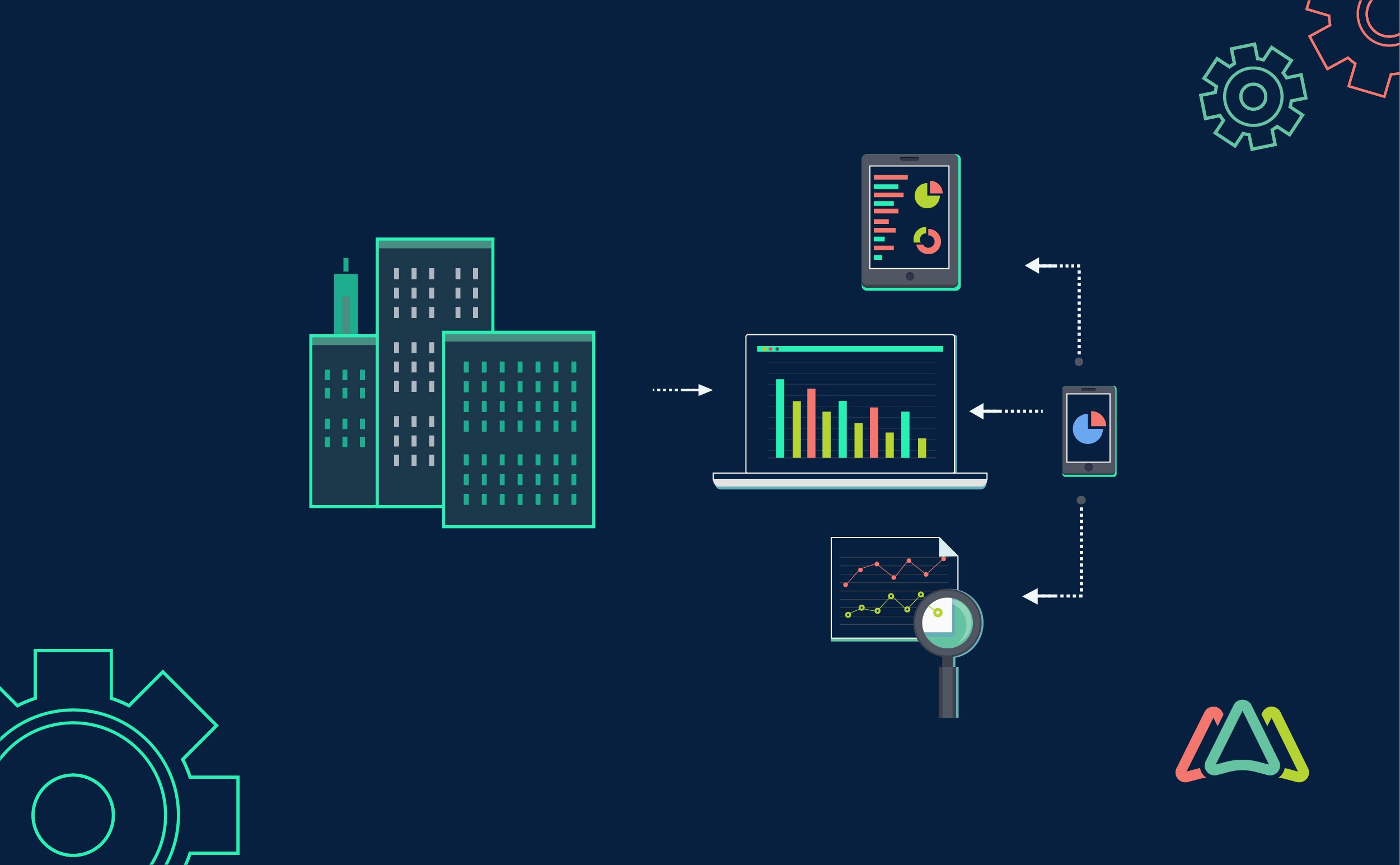
Facility Management KPIs: Measuring What Matters
According to McKinsey, facilities management accounts for 10 to 25 percent of indirect spending for companies with distributed operations such as retailers, manufacturers, and transportation and logistics making it important for them to strike a balance between cutting non-core costs and ensuring the continued performance of core operations. In such circumstances, organizations that use performance indicators to measure what matters come out on top.
Key Performance Indicators (KPIs) are vital for facility managers. They provide benchmarks to assess performance and determine the success of FM initiatives. KPIs enable facility managers to make data-driven decisions, allocate resources effectively, and continuously improve their operations.
By monitoring and analyzing KPIs, facility managers gain valuable insights into the performance of various functions, such as maintenance, energy management, occupancy, customer satisfaction, compliance, and financial performance. KPIs serve as diagnostic tools, allowing facility managers to identify areas of strength and areas that require attention or improvement.
What are Facility Management KPIs?
Facility management KPIs are quantifiable metrics or measures that reflect the performance and effectiveness of various aspects of facility operations. KPIs are carefully selected based on their relevance to an organization's short-term and long-term goals, and they provide a means to track progress, identify areas for improvement, and evaluate the success of facility management initiatives.
These indicators are specific, measurable, achievable, relevant, and time-bound (SMART), enabling facility managers to establish clear targets and benchmarks.
Benefits of Using KPIs in Facility Management
Using KPIs in facility management offers several benefits:
Performance Measurement
KPIs provide a standardized way to assess performance and track progress towards predetermined goals. They enable facility managers to objectively evaluate the success of their strategies, initiatives, and operational activities.
Data-Driven Decision Making
KPIs provide facility managers with factual and reliable data to make informed decisions. By analyzing KPI trends and patterns, facility managers can identify areas that require adjustments, reallocate resources effectively, and prioritize actions based on data-driven insights.
Continuous Improvement
KPIs serve as a benchmark for continuous improvement. By setting targets and comparing actual performance against them, facility managers can identify gaps, implement corrective measures, and drive ongoing improvements in facility operations.
Alignment with Organizational Goals
KPIs help facility managers align their activities with the strategic objectives of the organization. By selecting KPIs that reflect the priorities of the organization, facility managers ensure that their efforts contribute to the overall success of the business.
Stakeholder Communication
KPIs provide a common language for communication between facility managers and various stakeholders, including senior management, clients, occupants, and service providers. They facilitate transparent and meaningful discussions about performance, progress, and areas requiring attention or improvement.
Resource Optimization
KPIs assist facility managers in optimizing resource allocation by identifying inefficiencies, potential cost savings, and opportunities for better utilization of resources. This leads to improved operational efficiency and cost management.
Facility management KPIs encompass a wide range of areas beyond maintenance management and include financial performance, operational efficiency, customer satisfaction, compliance, and risk management. These indicators provide facility managers with objective measures to evaluate their strategies, make informed decisions, optimize resources, and improve facility performance.
Different types of Facility Management KPIs:
Operational KPIs
Operational Key Performance Indicators (KPIs) in facility management focus on assessing the day-to-day operational aspects of maintaining and managing the facility. These indicators provide facility managers with insights into maintenance efficiency, work order management, asset performance, and occupancy rates. By monitoring operational KPIs, facility managers can improve operational effectiveness, optimize resources, and improve facility performance. Here are four common operational KPIs in facility management:
KPI #1: Maintenance Backlog
The maintenance backlog KPI measures the number of pending maintenance tasks or work orders to be completed. It reflects the backlog of maintenance activities that need attention. A high maintenance backlog indicates potential issues with resource allocation, inefficient work order management, or a lack of proactive maintenance practices. By monitoring and reducing the maintenance backlog, facility managers ensure timely maintenance, minimize equipment downtime, and improve the overall operational efficiency of the facility.
KPI #2: Work Order Completion Time
The work order completion time KPI tracks the average time taken to complete work orders from the time they are requested. It measures the efficiency and responsiveness of the maintenance team in addressing and resolving maintenance issues. Monitoring this KPI helps facility managers identify bottlenecks, streamline processes, and improve overall maintenance service levels. By reducing the work order completion time, facility managers can minimize disruptions, increase customer satisfaction, and improve the overall facility experience.
KPI #3: Asset Uptime and Availability
The asset uptime and availability KPI measures the percentage of time that critical assets or systems are operational and available for use. It reflects the reliability and performance of key facility assets, such as HVAC systems, elevators, or production equipment. By tracking this KPI, facility managers can identify asset reliability issues, plan preventive maintenance activities, and ensure maximum asset uptime. Optimizing asset availability helps minimize disruptions and improve productivity.
KPI #4: Occupancy Rates
Occupancy rates KPI measures the utilization of space within the facility, typically expressed as a percentage. It provides insights into space efficiency, capacity planning, and the overall utilization of the facility. By monitoring occupancy rates, facility managers can assess space utilization trends, identify underutilized areas, and optimize space allocation. This KPI is particularly crucial for commercial real estate facilities or multi-tenant buildings. Maximizing occupancy rates helps generate revenue, optimize space usage, and ensure the financial viability of the facility.
Operational KPIs play a crucial role in ensuring the efficient and effective operation of facility management. By regularly monitoring and analyzing these indicators, facility managers can identify areas for improvement, implement proactive maintenance strategies and optimize resources.
Financial KPIs
Financial Key Performance Indicators (KPIs) in facility management focus on monitoring and evaluating the financial aspects of facility operations and provide insights into cost management, budget adherence, return on investment, and energy efficiency. By tracking financial KPIs, facility managers can make informed decisions, optimize resource allocation, and ensure financial sustainability. Here are four common financial KPIs used in facility management:
KPI #5: Cost per Square Foot
This KPI measures the total expenses incurred per square foot of the facility. It helps facility managers assess the cost-effectiveness of their operations and identify opportunities for cost reduction or optimization. By analyzing the cost per square foot over time, facility managers are able to evaluate the efficiency of resource utilization and identify areas where costs can be controlled.
KPI #6: Budget Variance
The budget variance KPI compares actual expenses against budgeted amounts. It provides insight into the accuracy of budget planning and control. A positive variance indicates that expenses are lower than budgeted, while a negative variance suggests that expenses have exceeded the budget. Facility managers can use this KPI to identify areas of overspending or underspending and take the appropriate actions to bring expenses in line with the budget.
KPI #7: Return on Investment (ROI)
The ROI KPI assesses the profitability and effectiveness of facility investments and projects. It measures the return generated compared to the initial investment. By calculating the ROI for specific initiatives, such as renovations, equipment upgrades, or energy efficiency projects, facility managers can determine the success and value generated from these investments. A positive ROI indicates that the investment has yielded positive returns, while a negative ROI suggests that the investment isn’t delivering the value that was expected.
KPI #8: Energy Consumption and Cost
Energy consumption and cost KPIs track the usage of energy resources within the facility and the associated costs. By monitoring energy consumption patterns, facility managers can identify opportunities for energy conservation and efficiency improvements. This KPI helps in evaluating the impact of energy-saving initiatives, such as upgrading to energy-efficient equipment or implementing smart building systems. By reducing energy consumption and costs, facility managers can contribute to environmental sustainability while also achieving financial savings.
Consider a facility management team that implements energy efficiency initiatives to reduce operational costs and environmental impact. They can track energy usage data and identify areas of inefficiency and implement measures such as upgrading lighting systems, optimizing HVAC settings, and implementing smart controls. Over time, they will observe a significant reduction in energy consumption and cost per square foot resulting in substantial cost savings for the facility while promoting sustainability.
Financial KPIs provide facility managers with valuable insights into the financial performance of their facilities. By regularly monitoring and analyzing these indicators, facility managers can make data-driven decisions, optimize costs, and allocate resources effectively, ultimately ensuring the financial health and success of their facility operations.
Customer Satisfaction KPIs
Customer satisfaction is a critical aspect of facility management as it directly impacts tenant retention, reputation, and overall success. Customer Satisfaction Key Performance Indicators (KPIs) in facility management focus on measuring and improving the satisfaction levels of occupants, tenants, and other stakeholders. By monitoring and addressing these KPIs, facility managers can improve service quality, responsiveness, and overall customer experience. Here are four common customer satisfaction KPIs used in facility management:
KPI #9: Service Request Response Time
The service request response time KPI measures the time taken to respond to and resolve service requests from occupants or tenants. Prompt response and resolution demonstrate a commitment to customer service and satisfaction. By monitoring and reducing the response time, facility managers can improve customer experience, minimize disruptions, and meet or exceed service level expectations.
KPI #10: Service Quality and Resolution Rate
The service quality and resolution rate KPI assesses the quality of service provided and the rate at which service issues are resolved satisfactorily. It reflects the effectiveness of the facility management team in addressing and resolving customer concerns or maintenance issues. By continuously monitoring and improving service quality and resolution rates, facility managers build trust, and maintain positive relationships with occupants and tenants.
KPI #11: Tenant Retention Rate
The tenant retention rate KPI measures the percentage of tenants who renew their leases or continue occupying the facility. It reflects tenant satisfaction, the perceived value of the facility, and the quality of services provided. A high tenant retention rate indicates strong customer loyalty and satisfaction. By actively managing and improving tenant retention rates, facility managers reduce vacancies, minimize turnover costs, and maintain stable revenue streams.
KPI #12: Feedback and Survey Results
Feedback and survey results KPI involves collecting feedback from occupants, tenants, or other stakeholders through surveys, suggestion boxes, or other feedback mechanisms. Analyzing and monitoring the results of these feedback channels provide valuable insights into customer satisfaction levels, areas for improvement, and specific concerns or suggestions. By actively seeking and acting upon customer feedback, facility managers demonstrate a customer-centric approach and are able to address issues proactively.
These customer satisfaction KPIs help facility managers gauge the effectiveness of their customer service initiatives, identify areas for improvement, and align facility operations with customer expectations. By focusing on customer satisfaction and actively managing these KPIs, facility managers can foster positive relationships with occupants and tenants, improve the facility's reputation, and ultimately contribute to long-term success in the competitive market.
Compliance and Risk Management KPIs
Compliance and Risk Management Key Performance Indicators (KPIs) in facility management focus on ensuring adherence to regulations, mitigating risks, and maintaining a safe and secure environment for occupants, employees, and assets. These indicators help facility managers monitor and assess compliance levels, identify potential risks, and implement preventive measures. By tracking and addressing these KPIs, facility managers can minimize liabilities, protect stakeholders, and ensure regulatory compliance. The following are four common compliance and risk management KPIs used in facility management:
KPI #13: Health and Safety Incidents
The health and safety incidents KPI measures the number and severity of accidents, injuries, or occupational health incidents within the facility. Tracking this KPI helps facility managers identify potential hazards, evaluate the effectiveness of safety protocols, and implement corrective actions to prevent accidents. By reducing health and safety incidents, facility managers create a safer environment for occupants, mitigate legal and financial risks, and demonstrate a commitment to employee well-being.
KPI #14: Regulatory Compliance
Regulatory compliance KPI assesses the facility's adherence to applicable laws, regulations, codes, and standards. It involves monitoring compliance with building codes, fire safety regulations, environmental regulations, accessibility requirements, and other relevant regulations. By regularly assessing regulatory compliance, facility managers can identify gaps, implement necessary measures, and ensure the facility operates within the legal framework. Demonstrating compliance not only minimizes legal risks but also contributes to the overall reputation and trustworthiness of the facility.
KPI #15: Security Breaches
The security breaches KPI tracks and measures the number and severity of security incidents or breaches within the facility. It encompasses unauthorized access, theft, vandalism, cybersecurity incidents, or any other security-related issues. Monitoring this KPI helps facility managers evaluate the effectiveness of security measures, identify vulnerabilities, and implement appropriate security protocols. By mitigating security breaches, facility managers protect occupants, assets, and sensitive information while maintaining a secure facility environment.
Consider a facility management team operating a high-security facility that requires strict adherence to regulations and risk management practices. The facility management KPIs focus on health and safety incidents, regulatory compliance, security breaches, and insurance claim frequency and severity. The team implements comprehensive safety protocols, conducts regular audits to ensure compliance and implements employee training programs. By monitoring these KPIs and proactively addressing any issues, the facility management team will be able to mitigate risks, maintain regulatory compliance, and minimize security breaches and insurance claims.
KPI #16: Insurance Claim Frequency and Severity
The insurance claim frequency and severity KPI measures the frequency and financial impact of insurance claims filed by the facility. It provides insights into the overall risk profile and the effectiveness of risk management strategies. By monitoring insurance claim data, facility managers can identify trends, assess risk exposure, and implement proactive measures to mitigate risks. By reducing claim frequency and severity, facility managers lower insurance costs, minimize disruptions, and ensure business continuity.
Compliance and risk management KPIs are crucial in maintaining a safe, secure, and compliant facility environment. By monitoring and addressing these indicators, facility managers can be proactive in identifying and mitigating risks, ensure regulatory compliance, protect stakeholders, and minimize legal and financial liabilities. Implementing robust compliance and risk management practices contributes to the long-term success and sustainability of facility operations.
Selecting Appropriate KPIs for Facility Management
Selecting relevant and meaningful KPIs helps facility managers measure progress, drive performance improvement, and align facility operations with organizational goals and objectives. The following are four things to consider when selecting KPIs for managing your facilities:
1. Align KPIs with Organizational Goals and Objectives
Understand the strategic priorities and key focus areas and align them with the overall goals and objectives of the organization to demonstrate the value of facility operations in supporting the organization's success. For example, if the organization aims to reduce costs, financial KPIs such as cost per square foot or energy consumption and cost are useful KPIs.
2. Consider Industry Standards and Benchmarks
Benchmarking against industry standards and best practices helps facility managers gain insights into how their facility performs compared to others in the industry. Facility managers can leverage industry-specific KPIs and benchmarks to assess performance, identify areas for improvement, and set realistic targets. Industry associations, research reports, and professional networks provide valuable resources for identifying relevant industry KPIs and benchmarks.
3. Determine Measurable and Actionable KPIs
It is important to select KPIs that can be measured accurately and consistently. KPIs should provide meaningful data that can be tracked and analyzed over time. Facility managers should consider the availability of data sources and the feasibility of collecting and reporting the required data. Additionally, KPIs should be actionable, which means the insights gained from tracking them should lead to actions and improvements in facility management practices.
4. Identify Leading and Lagging Indicators
Facility managers should consider both leading and lagging indicators when selecting KPIs. Lagging indicators provide insights into past performance and outcomes, such as maintenance backlog or insurance claim frequency. Leading indicators, on the other hand, help predict future performance and guide proactive decision-making. For example, work order completion time or energy consumption trends are leading indicators pointing to potential issues or areas for improvement. A combination of leading and lagging indicators provides a comprehensive view of facility performance and results in better facility management.
By considering these factors, facility managers can select the best KPIs that align with organizational goals, leverage industry benchmarks, provide measurable data, and offer insights into both past and future performance. KPIs should empower facility managers to make data-driven decisions, optimize operations, and continuously improve the performance and efficiency of their facilities.
Implement and Monitor Facility Management KPIs
Once Key Performance Indicators (KPIs) for facility management have been selected, it is essential to implement and monitor them. By following a structured approach, facility managers ensure that KPIs are tracked accurately, progress is measured consistently, and insights are derived for continuous improvement. The following are four steps to follow when implementing and monitoring facility management KPIs:
1. Collect and Analyze Relevant Data
Identify the data sources and establish a process for data collection. This involves leveraging existing systems and databases, implementing new data tracking mechanisms, and utilizing facilities management software. The data collected should be accurate, reliable, and align with the specific KPIs being measured. Regular data analysis allows facility managers to identify trends, patterns, and areas for improvement.
2. Establish Baseline Performance Metrics
Assess the current state of the facility by determining the initial performance levels of the selected KPIs. This serves as a starting point against which future performance can be compared. Baseline metrics provide a reference to evaluate the effectiveness of improvement initiatives and determine the impact of changes implemented in facility management practices.
3. Set Realistic Targets and Benchmarks
Establish specific, measurable, achievable, relevant, and time-bound (SMART) targets for each KPI. These targets should align with organizational goals and industry benchmarks, taking into account factors such as facility size, complexity, and resources available. Realistic targets motivate the facility management team, enable effective performance tracking, and drive continuous improvement efforts.
4. Use Facilities Management Software for Data Tracking and Reporting
Facilities management software has functionality and features for data tracking, reporting, and visualization. They streamline data collection processes, automate calculations, and generate comprehensive reports. Facility managers can use dashboards and visualizations to gain real-time insights into KPI performance, identify areas of concern, and communicate results to stakeholders.
If maintenance management of facilities is a high priority, using a Computerized Maintenance Management Software (CMMS) is recommended. A CMMS is software that holds maintenance information and manages the processes of maintenance operations. It helps optimize the utilization and availability of facility assets. It facilitates collaboration and transparency among team members, allowing for shared access to data and streamlined communication. Software platforms provide the ability to set up alerts and notifications, ensuring that facility managers are promptly notified of any deviations or critical issues related to KPI performance.
By following these steps and utilizing technology and software tools, facility managers can effectively implement and monitor facility management KPIs.
Challenges and Best Practices in Using Facility Management KPIs
Implementing and utilizing Key Performance Indicators (KPIs) in facility management comes with challenges. It's important to address them in order to reap the benefits. Here are four challenges with using facility management KPIs, along with best practices to overcome them:
1. Data Accuracy and Integrity
One of the primary challenges in utilizing KPIs is ensuring the accuracy and integrity of the data collected. Inaccurate or incomplete data can lead to unreliable reports and ineffective decision-making. To overcome this challenge, facility managers should implement robust data collection processes and validation mechanisms. This includes regular audits, data quality checks, and validation against reliable sources. By ensuring data accuracy and integrity, facility managers can rely on the KPIs to provide accurate insights for informed decision-making.
Best Practice: Invest in a CMMS software that automates data collection processes, reduces manual errors, and provides data validation mechanisms. Regularly train and educate the facility management team on data collection protocols to maintain data accuracy.
2. Standardized Metrics are Lacking
The absence of standardized metrics poses a challenge when implementing facility management KPI. Different organizations may use different metrics or calculation methodologies, making it challenging to benchmark performance or compare across the industry. To address this challenge, facility managers should strive to align with industry standards and best practices. Engaging with industry associations (like IFMA or BOMA), participating in benchmarking initiatives, and collaborating with peers can help establish common metrics and promote consistency in performance measurement.
Best Practice: Stay updated with industry trends, standards, and best practices. Engage in knowledge-sharing forums, conferences (like IFMA’s Facility Fusion, NFMT, etc.), and industry networks to exchange ideas and establish common metrics for facility management KPIs.
3. Stakeholder Communication and Collaboration
Effective communication and collaboration with stakeholders are essential for successful KPI implementation. Facility managers need to engage and involve key stakeholders, including occupants, tenants, senior management, and other relevant parties. Clear and transparent communication about the purpose, significance, and progress of the KPIs fosters understanding, buy-in, and support. Regularly sharing KPI results, discussing improvement strategies, and seeking feedback from stakeholders strengthen collaboration and ensure everyone is aligned towards the same goals.
Best Practice: Develop a communication plan that outlines the frequency, channels, and stakeholders involved in KPI reporting and discussions. Use visualizations and easy-to-understand reports to present KPI data to stakeholders.
4. Continuous Improvement and Adaptation
Facility management is a dynamic field, and KPIs need to be continuously reviewed and adjusted to reflect changing priorities and circumstances. As the facility evolves, new challenges may arise, and goals may shift. Facility managers should regularly evaluate the relevance and effectiveness of existing KPIs and be willing to modify or introduce new KPIs to address emerging needs. Continuous improvement requires a proactive mindset, monitoring industry trends, and being open to feedback and suggestions from the facility management team and stakeholders.
Best Practice: Establish a feedback loop and review process for KPIs. Regularly assess the effectiveness of existing KPIs, seek input from the facility management team, and adapt KPIs to align with evolving goals and industry trends.
To succeed in facility management, it is important to prioritize KPIs, collect relevant data, establish baselines, set realistic targets, and utilize technology for data tracking and reporting. By consistently monitoring and analyzing KPIs, facility managers can identify areas for improvement, implement corrective actions, and continuously improve facility performance.
TABLE OF CONTENTS
Keep Reading
Ever find yourself checking into a luxury hotel and expecting a relaxing stay, only to find a ...
11 Apr 2025
Organizations are witnessing swift changes in the business environment and confronting a ...
8 Apr 2025
Last month, news outlets and the entire internet was abuzz with the return of NASA astronauts ...
3 Apr 2025
What comes first - CMMS or predictive maintenance? If your answer is either, it is correct. ...
28 Mar 2025
Artificial intelligence (AI) talk has become commonplace. Today, engaging in business-focused ...
27 Mar 2025
Imagine a world where machines predict, diagnose, and fix their issues before they fail. This ...
25 Mar 2025
A facility maintenance plan is at the core of a facility’s operations. This organized ...
21 Mar 2025
Think of managing your maintenance operations like managing a championship sports team. Just ...
21 Mar 2025
The maintenance sector is battling a severe talent shortage that threatens to undermine ...
7 Mar 2025
Manufacturing maintenance is the backbone of industrial efficiency, ensuring machines run ...
5 Mar 2025
No one likes playing a guessing game when equipment breaks down. Yet, maintenance teams often ...
4 Mar 2025
The size of the preventive maintenance software market is discussed in millions of dollars, ...
4 Mar 2025
The organizational structure and corporate hierarchy vary from company to company. Large ...
28 Feb 2025
Maintenance procedures are essential for ensuring the longevity and reliability of machinery ...
21 Feb 2025
Sustainability is no longer just a buzzword; it's a critical component of corporate social ...
20 Feb 2025
A Computerized Maintenance Management System (CMMS) relies on accurate, well-organized data ...
18 Feb 2025
In an era where technology drives operational efficiency, Computerized Maintenance Management ...
14 Feb 2025
A Computerized Maintenance Management System (CMMS) is a key component of modern maintenance ...
13 Feb 2025
Introduction Maintenance management is the foundation of maintenance operations in industries ...
11 Feb 2025
Introduction A Computerized Maintenance Management System (CMMS) is software designed to help ...
7 Feb 2025