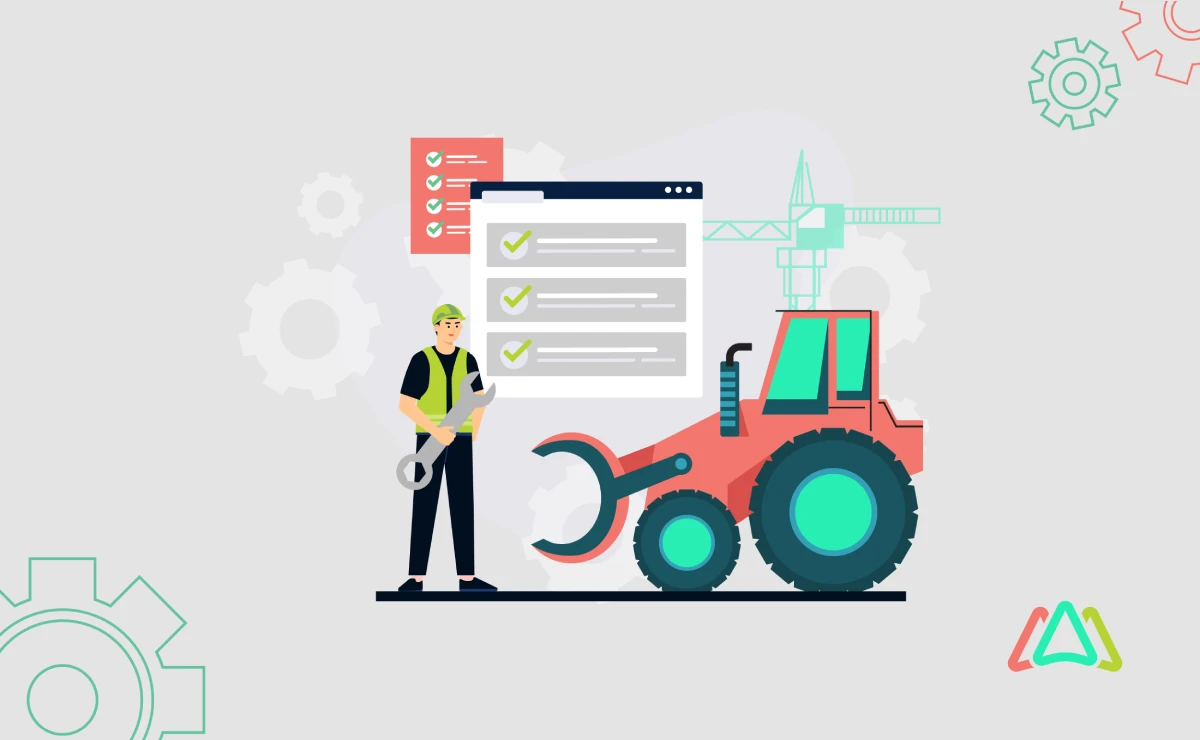
Heavy Equipment Preventive Maintenance Checklist
Heavy equipment does the “heavy lifting” and supports operations for many businesses. These machines are investments critical to business success, but they also represent significant expenses and potential risks if not properly maintained. For heavy equipment that operates under harsh conditions and heavy workloads, preventive maintenance is a must!
Preventive maintenance stands as a proactive approach to equipment upkeep, contrasting with reactive maintenance, which involves addressing issues after they arise. The significance of preventive maintenance lies in its ability to prevent costly repairs, minimize downtime, and uphold safety standards.
- Cost Reduction: By identifying and addressing potential problems early, preventive maintenance helps avoid major repairs and component replacements, saving businesses costs associated with equipment downtime and emergency repairs.
- Reducing Downtime: Unplanned equipment failures compromise project schedules, leading to delays and lost productivity. Preventive maintenance mitigates this risk by ensuring that equipment remains in optimal working condition and reduces the chances of breakdowns.
- Safety Enhancement: Well-maintained equipment is less prone to malfunctions and failures that could pose safety hazards to operators and other personnel on-site. Regular inspections and servicing help identify and rectify potential safety issues before they escalate into accidents.
- Longevity of Equipment: Preventive maintenance extends the lifespan of heavy equipment by preserving the integrity of critical components. This translates to a higher return on investment for businesses, as equipment remains operational for longer periods with reduced need for premature replacements.
A preventive maintenance checklist helps guide maintenance professionals in systematically inspecting, servicing, and documenting maintenance tasks for various types of heavy equipment. A structured checklist helps heavy equipment operators, maintenance personnel, and managers streamline the preventive maintenance process, making it more manageable and less prone to oversight. Its purpose is threefold:
- Systematic Guidance: The checklist offers a structured framework for conducting preventive maintenance tasks, ensuring that no critical components or inspection points are overlooked. It provides operators and maintenance personnel with clear guidance on the specific tasks to be performed and their recommended frequencies.
- Customization and Adaptation: While the checklist provides a comprehensive overview of maintenance tasks, it is also adaptable to suit the unique needs of different types of heavy equipment and operational environments. Maintenance professionals can tailor the checklist to align with the specific requirements of their equipment and industry.
- Proactive Maintenance Management: Businesses can adopt a proactive approach to equipment management by incorporating the checklist into their maintenance routines. Regular adherence to the checklist helps identify potential issues early, allowing for timely intervention and optimization of equipment performance and longevity.
Developing a Preventive Maintenance Plan for Heavy Equipment
1. Assessing Equipment Needs and Usage
Before implementing a preventive maintenance plan, it's important to conduct a thorough assessment of the equipment and its usage patterns. This assessment involves:
Equipment Survey
Create a comprehensive inventory of all heavy equipment, including make, model, age, and usage history. This information provides insights into the overall condition of the assets and helps prioritize maintenance efforts.
Usage Analysis
Analyze the frequency and intensity of equipment usage. Determine whether certain equipment operates continuously, intermittently, or seasonally, as this influences the frequency and type of maintenance required.
Environmental Factors
Consider the operating environment of the equipment, including factors such as temperature, humidity, dust, and terrain. Environmental conditions can impact equipment performance and maintenance needs, necessitating specific preventive measures.
Criticality Assessment
Identify equipment critical to operations and prioritize maintenance efforts accordingly. High-value or mission-critical equipment may require more frequent inspections and proactive maintenance to minimize downtime.
Conducting a comprehensive assessment provides valuable insights into equipment needs and usage patterns, enabling businesses to develop tailored maintenance plans that optimize resources and maximize equipment reliability.
2. Setting Maintenance Schedules: Daily, Weekly, Monthly, Annually
Once equipment needs and usage patterns have been assessed, the next step is to establish maintenance schedules based on predetermined intervals. Maintenance schedules typically include tasks to be performed daily, weekly, monthly, and annually:
Daily Maintenance
Daily checks focus on basic tasks such as inspecting fluid levels (oil, coolant, hydraulic fluid), checking tire pressure and condition, and conducting visual inspections for leaks or damage. These checks ensure that equipment is safe and operational before use each day.
Weekly Maintenance
Weekly maintenance tasks may include greasing moving parts, inspecting and cleaning batteries, and conducting functional tests of brakes, lights, and alarms. These checks address wear and tear that may occur during regular operation and help prevent premature failures.
Monthly Maintenance
Monthly maintenance involves more comprehensive inspections and servicing, such as replacing filters (air, fuel, oil), checking electrical connections and wiring, and inspecting hydraulic systems for leaks or damage. These tasks address longer-term wear and ensure that equipment remains in optimal condition.
Annual Maintenance
Annual maintenance tasks focus on more extensive servicing and inspections, including engine tune-ups, structural inspections, and professional assessments by certified technicians. These tasks help identify and address potential issues that may arise over time, ensuring the continued reliability and safety of equipment.
Establishing clear maintenance schedules aligned with these intervals ensures that preventive maintenance tasks are performed consistently and systematically, minimizing the risk of unexpected failures and optimizing equipment performance.
3. Tailoring Plans to Specific Equipment Types and Industries
Heavy equipment maintenance requirements can vary significantly depending on factors such as equipment type, manufacturer recommendations, and industry regulations. Therefore, it's important to tailor maintenance plans to specific equipment types and industries.
Equipment Types
Different types of heavy equipment, such as excavators, bulldozers, cranes, and trucks, have unique maintenance needs based on their design, components, and operating conditions. Tailor maintenance plans to account for these differences and address specific maintenance challenges associated with each equipment type.
Industry Requirements
Industries such as construction, mining, agriculture, and transportation may have distinct regulatory requirements or operational demands that influence maintenance practices. Ensure that maintenance plans comply with industry standards and regulations while also addressing the unique challenges faced in each industry sector.
Manufacturer Recommendations
Manufacturers often provide detailed maintenance guidelines and schedules for their equipment, including recommended service intervals and procedures. Incorporate manufacturer recommendations into maintenance plans to ensure equipment warranties remain valid and optimal performance is maintained.
The Comprehensive Heavy Equipment Maintenance Checklist
Maintaining heavy equipment requires a systematic approach to ensure optimal performance and longevity. This comprehensive checklist outlines essential daily, weekly, monthly, and annual maintenance tasks to keep equipment in its optimal condition:
1. Daily Checks
Fluid Levels
Check oil, coolant, and hydraulic fluid levels using the equipment's dipsticks or gauges.
Top up fluids as needed to ensure proper lubrication and cooling.
Tire Inspection
Inspect tires for adequate pressure using a tire gauge.
Ensure proper tread depth and look for signs of damage or wear that may affect traction or stability.
Visual Inspection
Conduct a visual inspection of the equipment for leaks, loose bolts, and signs of wear or damage.
Pay attention to areas such as hydraulic hoses, fittings, and structural components.
B. Weekly Checks
Lubrication
Grease moving parts according to manufacturer recommendations. Pay particular attention to pivot points, bearings, and other components that require regular lubrication to prevent friction and wear.
Battery Inspection and Cleaning
Inspect the battery terminals for corrosion or loose connections. Clean terminals with a wire brush and apply terminal grease to prevent corrosion and ensure a secure electrical connection.
Functional Tests
Test the functionality of brakes, lights, and alarms to ensure they are working correctly.
Check brake pads, brake fluid levels, and brake lines for signs of wear or leaks. Verify that all lights and alarms are operational for safe operation on-site.
C. Monthly Checks
Filter Replacement
Replace air, fuel, and oil filters according to manufacturer recommendations.
Clean or replace clogged filters to maintain optimal engine performance and prevent fluid contamination.
Electrical System Check
Inspect electrical connections and wiring for signs of damage or corrosion.
Tighten loose connections and repair or replace damaged wiring to prevent electrical issues that could lead to equipment malfunctions.
Hydraulic System Inspection
Inspect hydraulic hoses, fittings, and connections for leaks or damage. Check hydraulic fluid quality and level, and top up or replace fluid as needed.
Ensure proper operation of hydraulic components to maintain equipment performance and safety.
D. Annual Checks
Engine Tune-Up
Perform a comprehensive engine tune-up, including replacing spark plugs, air filters, fuel filters, and drive belts.
Adjust engine timing and idle speed as needed to optimize fuel efficiency and performance.
Structural Inspection
Inspect the equipment's frame, joints, and welds for signs of cracks, corrosion, or fatigue.
Ensure structural integrity to prevent safety hazards and maintain equipment stability during operation.
Professional Assessment
Schedule a professional assessment by certified technicians to evaluate the overall condition of the equipment.
Conduct thorough inspections, diagnostic tests, and performance checks to identify any underlying issues and address them promptly.
Recording and Documentation
Recording and documenting maintenance activities are integral aspects of an effective preventive maintenance program for heavy equipment.
A. Importance of Maintaining Records
Compliance and Regulations
Accurate maintenance records are often required to comply with industry regulations, standards, and legal requirements. Documentation demonstrates that equipment has been properly maintained, ensuring regulatory compliance and mitigating potential liability risks.
Warranty and Insurance Claims
Maintaining detailed maintenance records can support warranty claims and insurance coverage in the event of equipment failures or damage. Documentation provides evidence of adherence to manufacturer recommendations and proactive maintenance practices, strengthening warranty claims and insurance coverage.
Asset Management
Maintenance records serve as a valuable asset management tool, providing insights into the history, condition, and performance of equipment. By tracking maintenance activities, businesses can make informed decisions regarding equipment investments, replacements, and upgrades to optimize asset lifecycle management.
Predictive Analytics
Historical maintenance data can be leveraged for predictive analytics and trend analysis. By analyzing maintenance records, businesses can identify recurring issues, predict equipment failures, and implement proactive measures to prevent downtime and optimize equipment reliability.
B. Digital vs. Physical Documentation
Digital Documentation
- Accessibility: Digital documentation offers greater accessibility, allowing maintenance records to be accessed and updated from anywhere with an internet connection. This accessibility facilitates real-time collaboration among maintenance teams and stakeholders.
- Searchability: Digital records can be easily searched, sorted, and filtered based on various parameters, such as equipment type, maintenance date, or maintenance task. This searchability enhances efficiency and reduces the time required to retrieve specific information.
- Space Efficiency: Digital documentation eliminates the need for physical storage space, reducing clutter and administrative overhead associated with managing paper records. Electronic storage also minimizes the risk of loss or damage due to environmental factors.
- Integration: Digital maintenance records can be integrated with other software systems, such as inventory management or asset tracking systems, streamlining data sharing and synchronization across multiple platforms.
Physical Documentation
- Tangible Records: Physical documentation provides tangible records that can be easily reviewed and verified without the need for electronic devices or internet access. This accessibility can be advantageous in remote or offline environments where digital access may be limited.
While physical documentation offers tangible records, it poses challenges in terms of accessibility and data management, especially in remote places without internet access. Cloud-based CMMS software bridges this gap by allowing maintenance data to be entered and stored directly within mobile devices, even in offline mode. This ensures that maintenance activities can be recorded and tracked seamlessly, regardless of internet connectivity. When the device reconnects to the internet, the data automatically syncs with the cloud-based CMMS, ensuring that all records are up to date and accessible from anywhere at any time.
- Security: Physical records may offer a perceived sense of security, as they are not susceptible to cyber threats or data breaches. However, physical records are vulnerable to loss, damage, or theft, necessitating proper storage and handling procedures.
In contrast, cloud-based CMMS software offers advanced security measures to protect against cyber threats and data breaches. These include encryption protocols, user authentication mechanisms, and regular security updates to safeguard sensitive information stored in the cloud. Additionally, reputable cloud CMMS vendors adhere to industry-standard security certifications and compliance frameworks to ensure the highest level of data protection for their users. Therefore, while physical records may offer perceived security, a cloud-based CMMS provides a more robust and comprehensive security infrastructure to protect maintenance data from unauthorized access or malicious attacks.
Leveraging a CMMS to Manage Heavy Equipment Preventive Maintenance Checklist
One of the most valuable tools available for streamlining maintenance processes and ensuring compliance with preventive maintenance checklists is a Computerized Maintenance Management System (CMMS). This is how businesses can leverage a CMMS to manage their heavy equipment preventive maintenance checklist efficiently:
1. Centralized Maintenance Management
A CMMS software serves as a centralized platform for managing all aspects of maintenance operations, including preventive maintenance tasks. By storing preventive maintenance checklists within the CMMS, businesses can ensure that maintenance procedures are standardized and easily accessible to maintenance personnel across different locations.
2. Automated Scheduling and Notifications
With a CMMS, businesses can automate the scheduling of preventive maintenance tasks based on predefined intervals or usage metrics. Maintenance schedules can be generated automatically, and notifications can be sent to maintenance teams when tasks are due, ensuring timely completion and adherence to the checklist.
3. Customizable Checklists
CMMS software allows businesses to create customizable preventive maintenance checklists tailored to the specific requirements of their heavy equipment. Checklists can be configured to include equipment-specific inspection points, task frequencies, and documentation requirements, ensuring that maintenance activities are comprehensive and aligned with industry best practices.
4. Mobile Accessibility
Many modern CMMS solutions offer mobile applications that enable maintenance technicians to access and complete preventive maintenance checklists directly from their smartphones or tablets, even while working in remote areas without reliable internet access. This mobile accessibility enhances flexibility and productivity, allowing maintenance teams to record inspections, document findings, and update maintenance records in real time.
5. Data Analysis and Reporting
CMMS software provides powerful data analysis and reporting capabilities, allowing businesses to track key performance indicators (KPIs), analyze maintenance trends, and identify areas for improvement. By generating reports based on preventive maintenance checklist data, businesses can gain insights into equipment performance, maintenance costs, and compliance levels, enabling data-driven decision-making and continuous optimization of maintenance processes.
6. Integration with IoT and Predictive Maintenance
Some advanced CMMS solutions offer integration with Internet of Things (IoT) devices and predictive maintenance technologies, allowing businesses to collect real-time equipment data, monitor asset health, and predict potential failures before they occur. By leveraging IoT sensors and predictive analytics, businesses can enhance the effectiveness of their preventive maintenance efforts and minimize unplanned downtime.
Troubleshooting and Problem Resolution in Heavy Equipment Maintenance
1. Identifying Common Issues through Preventive Maintenance
Early Detection of Wear and Tear
Preventive maintenance checklists include routine inspections of critical components such as hoses, belts, filters, and moving parts. By regularly assessing these components, maintenance personnel can identify signs of wear and tear, corrosion, or deterioration before they lead to equipment failure.
Detection of Fluid Leaks
Regular checks of fluid levels and hydraulic systems as per the preventive maintenance checklist can help detect leaks or seepage early on. Timely identification of fluid leaks prevents loss of hydraulic power, overheating, and potential damage to other components.
Monitoring of Electrical Systems
Preventive maintenance checklists often include inspections of electrical connections, wiring, and battery terminals. By monitoring these components, maintenance personnel can identify loose connections, corrosion, or electrical faults that may lead to malfunctions or breakdowns.
Assessment of Tire Condition
Tire inspections are a routine part of preventive maintenance checklists. By checking tire pressure, tread depth, and condition, maintenance personnel can identify issues such as underinflation, uneven wear, or damage that may compromise equipment safety and performance.
2. Steps for Addressing Minor and Major Problems:
Immediate Action for Minor Issues
When minor issues are identified during preventive maintenance inspections, maintenance personnel can take immediate corrective actions such as tightening loose bolts, replacing worn-out filters, or lubricating moving parts. These proactive measures prevent minor issues from escalating into major problems.
Scheduled Repairs for Major Issues
When major issues are discovered during preventive maintenance checks, maintenance personnel can schedule timely repairs or replacements. By addressing major problems promptly, businesses can minimize equipment downtime and prevent costly breakdowns that disrupt operations.
Documentation and Follow-up
Preventive maintenance checklists include provisions for documenting findings and actions taken during inspections. This documentation enables maintenance personnel to track the resolution of identified issues, monitor equipment condition over time, and identify recurring problems that may require further attention or intervention.
Importance of Timely Action and Collaboration with Experts
Fast Intervention
Preventive maintenance checklists emphasize the importance of timely action in addressing identified issues. By promptly addressing maintenance concerns, businesses can prevent equipment downtime, avoid costly repairs, and maintain operational efficiency.
Collaboration with Experts
In cases where complex or specialized issues are identified, collaboration with experts such as certified technicians or equipment manufacturers may be necessary. Preventive maintenance checklists facilitate collaboration by providing clear documentation of maintenance activities and enabling communication between maintenance personnel and external experts.
Continuous Improvement
Preventive maintenance checklists serve as a foundation for continuous improvement in maintenance practices. By analyzing checklist data, identifying trends, and implementing corrective actions, businesses can enhance equipment reliability, optimize maintenance processes, and minimize the risk of future issues.
TABLE OF CONTENTS
Keep Reading
Ever find yourself checking into a luxury hotel and expecting a relaxing stay, only to find a ...
11 Apr 2025
Organizations are witnessing swift changes in the business environment and confronting a ...
8 Apr 2025
Last month, news outlets and the entire internet was abuzz with the return of NASA astronauts ...
3 Apr 2025
What comes first - CMMS or predictive maintenance? If your answer is either, it is correct. ...
28 Mar 2025
Artificial intelligence (AI) talk has become commonplace. Today, engaging in business-focused ...
27 Mar 2025
Imagine a world where machines predict, diagnose, and fix their issues before they fail. This ...
25 Mar 2025
A facility maintenance plan is at the core of a facility’s operations. This organized ...
21 Mar 2025
Think of managing your maintenance operations like managing a championship sports team. Just ...
21 Mar 2025
The maintenance sector is battling a severe talent shortage that threatens to undermine ...
7 Mar 2025
Manufacturing maintenance is the backbone of industrial efficiency, ensuring machines run ...
5 Mar 2025
No one likes playing a guessing game when equipment breaks down. Yet, maintenance teams often ...
4 Mar 2025
The size of the preventive maintenance software market is discussed in millions of dollars, ...
4 Mar 2025
The organizational structure and corporate hierarchy vary from company to company. Large ...
28 Feb 2025
Maintenance procedures are essential for ensuring the longevity and reliability of machinery ...
21 Feb 2025
Sustainability is no longer just a buzzword; it's a critical component of corporate social ...
20 Feb 2025
A Computerized Maintenance Management System (CMMS) relies on accurate, well-organized data ...
18 Feb 2025
In an era where technology drives operational efficiency, Computerized Maintenance Management ...
14 Feb 2025
A Computerized Maintenance Management System (CMMS) is a key component of modern maintenance ...
13 Feb 2025
Introduction Maintenance management is the foundation of maintenance operations in industries ...
11 Feb 2025
Introduction A Computerized Maintenance Management System (CMMS) is software designed to help ...
7 Feb 2025