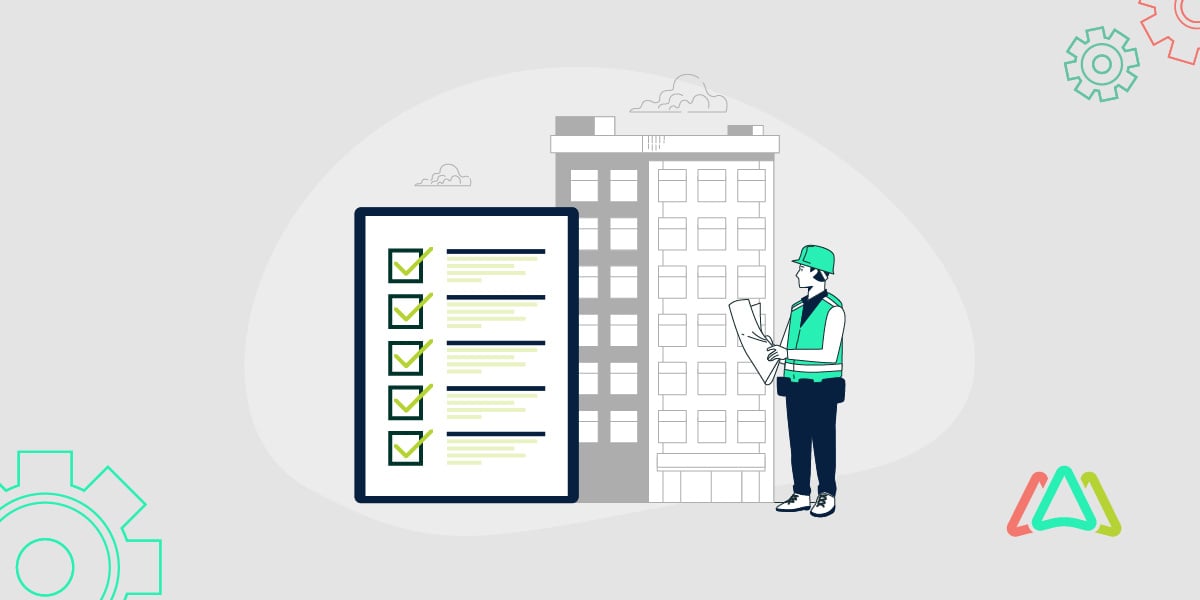
How to Create a Facility Maintenance Plan
A facility maintenance plan is at the core of a facility’s operations. This organized strategy manages and conserves assets, ensuring that asset lifespans are extended and organizations get maximum use for their investments. A facility maintenance plan is a systematic strategy for maintaining a facility's assets, making sure equipment, infrastructure, and essential systems function at an optimal level.
Preventive maintenance is a key component of a facility maintenance plan. It helps extend the life of facility equipment and assets by preventing breakdowns, failures, and costly unplanned repairs. Instead of reacting to failures, businesses can schedule maintenance proactively, improving efficiency, enhancing safety, and minimizing downtime.
A facility maintenance plan is crucial for facility managers, maintenance teams, and business owners to keep maintenance operations running smoothly, prevent costly repairs, and ensure long-term sustainability. This article will help you create an effective maintenance plan and identify common mistakes to avoid when designing and implementing it.
Before we discuss this further, we need to understand what a facility maintenance plan is and why it is important for organizations with large capital investments in facilities, fixed assets, and infrastructure.
What is a Facility Maintenance Plan?
A facility maintenance plan is a systematic strategy for maintaining a facility's assets, ensuring equipment, infrastructure, and essential systems function optimally. It guides maintenance through planned inspections, servicing, and repairs, keeping businesses ahead of the curve rather than reacting after something breaks.
An effective Facility Maintenance Plan is essential for reducing downtime, as unexpected breakdowns may be disastrous to operations. Rather than face overpriced emergency repairs, businesses can plan maintenance to keep everything operating efficiently.
Benefits of Having a Facility Maintenance Plan
Knowing the benefits of a facility maintenance plan makes it clear why one is needed. It's not just a list of things to check; it’s a way of life, a strategy to maintain all of your assets in top condition, reduce costs, and keep the day-to-day running smoothly. Well-planned maintenance means businesses avoid unnecessary downtime, maximize efficiency, and create a safer workplace. Facility Maintenance Plan Benefits:
1. Prolongs Asset Life
All equipment has a lifespan, and neglecting regular preventive maintenance can significantly shorten it. Regular maintenance that includes up-to-date inspection and servicing prevents wear and tear, ensuring that the machinery and infrastructure last longer. This allows businesses to get the most out of their investments without repeatedly purchasing expensive assets.
2. Reduces Operational Costs
Unanticipated repairs can chew through budgets quickly. In order to prevent emergent, costly breakdowns, maintenance plans allow businesses to get ahead of potential failures and repairs before they can negatively impact the workplace.
3. Improves Safety & Compliance
While poorly maintained facilities are a safety hazard, a typical maintenance plan emphasizes routine examinations of the building's fire alarms, electrical systems, and structural features to ascertain that they comply with safety codes. As a result, it leads to fewer workplace hazards, protects employees, and helps businesses avoid having to pay fines or deal with litigation associated with being non-compliant.
4. Boosts Productivity
When equipment fails, it can halt or interrupt operations, frustrating workers and costing money. A maintenance plan prevents any business interruptions and promotes the smooth running of all systems. It allows workers to focus on their tasks without interruption from incessant tech upgrades.
5. Enhances Sustainability
Well-maintained equipment operates more efficiently, using less energy and generating less waste. Whether it’s ensuring HVAC systems run at peak performance, preventing water leaks, or ensuring that machines run efficiently, a well-thought-out maintenance strategy allows businesses to prioritize their actions to improve their sustainability footprint while reducing utility costs.
Key Components of a Facility Maintenance Plan
Several key components need to be in place for a successful facility maintenance plan to manage assets effectively. However, facility managers and maintenance teams often overlook some of these elements when creating a preventive maintenance plan. Before developing your maintenance plan, make sure you review the following elements to help get you back on track.
1. Asset Inventory & Assessment
Asset Identification & Condition Assessment: The first part of a facility maintenance plan is a thorough inventory of assets. A properly structured asset inventory makes maintenance scheduling and resource allocation much easier. Assets should be categorized by type and criticality, and important details such as serial number, location, specs, images, and more should be collected. This article provides best practices for setting up an asset registry in your CMMS.
2. Preventive Maintenance Schedule
An effective facility maintenance plan is prepared with an approach of preventive maintenance on schedule. Regular inspections and services can catch issues while they are still small and spare the organization from incurring expensive repair bills.
3. Maintenance Procedures & SOPs
Maintenance procedures help standardize the performance of maintenance tasks, aiding efficiency and consistency. If you want maintenance teams to apply best practices and follow the manufacturer’s recommended maintenance schedules and tasks, documenting SOPs helps them do the right tasks the right way. Such SOPs should map out what needs to be done for day-to-day activities. Properly performed procedures minimize errors, create safety, and increase the life expectancy of key resources. CMMS software like Click Maint is instrumental in streamlining preventive maintenance tasks and ensuring that procedures are followed when completing each PM or inspection.
4. Budgeting & Resource Allocation
Budgeting and resource allocation for a well-defined maintenance plan ensure smooth operations. When a budget follows planning, funds are available for maintenance, so it does not get postponed. Having the necessary financial resources to support the maintenance plan pays off in the long run. Organizations that neglect funding planned maintenance often find that the expected savings are lost as unexpected costly repairs occur.
5. Staffing & Roles
The success of a maintenance plan relies on matching people with tasks. Efficiency and Accountability require clearly defining who is responsible for what maintenance action. It helps businesses make important decisions related to using an in-house maintenance team or outsourcing to third-party vendors..
6. CMMS Software Integration
Computerized Maintenance Management Systems (CMMS) is software that helps organizations manage and track maintenance activities like work orders, preventive maintenance, assets, parts, labor, suppliers, inspections, and more. CMMS software streamlines maintenance operations by automating work orders, using preventive measures schedules, and monitoring asset performance. Real-time updates enable companies to monitor repairs, optimize resource allocation, and minimize downtime. Having a CMMS enables maintenance teams to be more efficient, reduce equipment downtime, and avoid costly equipment breakdowns.
Steps to Create A Facility Maintenance Plan
Step 1: Evaluate Your Facility’s Needs
A thorough assessment of the current facility conditions is essential to creating a facility maintenance plan. This assessment should involve a detailed evaluation of all key facility systems, identification of potential risks and vulnerabilities, and a thorough assessment of existing maintenance requirements.
By understanding the current state of the facility and pinpointing areas that require urgent attention, you can proactively address maintenance issues before they escalate into major problems. This knowledge also allows you to allocate resources strategically, ensuring that maintenance efforts are focused on the most critical areas and that the available budget is utilized in the most efficient manner possible.
Step 2: Make an Inventory of All Assets & Equipment
An asset register detailing all buildings, locations, conditions, and equipment, along with maintenance history. Focus on the ones that are used most often and are at risk of breaking down; that way, you can ensure high-traffic systems are well-maintained.
Step 3: Declare Maintenance Strategies
Determine if you want a preventive, predictive, or reactive maintenance approach. Preventive maintenance aims to prevent breakages, predictive maintenance uses CMMS or IoT data to forecast breakdowns, and reactive maintenance deals with problems when they occur. If you want your business to run smoothly, you need balance.
Step 4: Create a Maintenance Schedule
Implement a routine maintenance schedule that addresses daily, weekly, monthly, and yearly responsibilities. Follow manufacturer recommendations and ensure high-priority assets with usage patterns receive regular servicing to minimize the risk of unexpected failures.
Step 5: Budgeting and Resource Allocation
Estimate the costs of routine servicing, repairs, and equipment upgrades to plan for maintenance expenses. Designate emergency funds to avoid costly disruptions and ensure that money constraints don’t delay needed maintenance.
Step 6: Adopt CMMS or Digital Tracking Tools
CMMS software automates maintenance tracking and manages work orders and the performance of assets in real time. This allows teams to stay one step ahead of issues, increasing efficiency and minimizing downtime by streamlining workflows.
Step 7: Train Your Team and Set Up Your SOPs
Make sure that the maintenance team is trained on best practices, safety protocols, and compliance. SOPs help standardize procedures, leading to uniformity, fewer errors, and an increased life span of critical assets.
Final Step: Measure, Analyze, & Enhance
Monitor KPIs such as downtime, maintenance expense, and the number of repairs closely. Based on these insights, make a habit of continuously improving your maintenance plan, adjusting wherever you find inefficiencies, and preventing them from happening in the future.
Key Facility Maintenance Planning Best Practices
Use Data & Analytics
Employing maintenance data and analytics enables you to forecast failures before they happen so you can make repairs proactively and avoid expensive downtime.
Perform Regular Inspections
Regular inspections uncover minor problems while they're still minor before they develop into significant failures that bring operations to a standstill.
Standardize Processes
Well-defined and repeatable maintenance processes guarantee consistency, improve efficiency, and decrease the probability of errors.
Leverage CMMS & IoT
Integrating Computerized Maintenance Management Systems (CMMS) with IoT devices helps automate maintenance tracking, improves asset monitoring, and optimizes scheduling.
Make Sure You Have an Emergency Plan
Something can go wrong at any moment, which is why a thorough emergency response plan is crucial. It is designed to respond promptly to integrated failures to minimize damage and downtime.
Common Mistakes to Avoid
Lack of Documentation
When records are not kept, businesses miss important maintenance tasks , which can lead to unnecessary breakdowns and inefficiencies. Maintenance history allows seamless future prediction.
Neglecting Preventive Maintenance
It can be easy to neglect maintenance because everything currently seems to be running well, but nobody should ever wait until equipment fails to take action; this is a costly error. This is where preventive maintenance comes into play; it helps detect minor problems before they escalate, incurring costly repair and downtime that puts businesses off-track.
Not Using a CMMS or CAFM
Maintenance tracking done manually is time-consuming and prone to errors. However, technology like a CMMS (Computerized Maintenance Management System) automates processes such as scheduling, work orders, and asset monitoring, which increases efficiency. Many organizations look to CAFM (Computer Aided Facility Management) software as an alternative to CMMS software. Organizations that don't leverage technology are often disorganized and lack real-time insights.
Poor Budgeting
When formulating budgets, it's common for businesses to underestimate the importance and costs of maintenance. This oversight can have a cascading effect, leading to unexpected higher costs due to breakdowns and the early retirement of valuable capital assets.
To avoid these risks, companies should implement robust budgeting policies. These policies should ensure that adequate financial resources are allocated to maintenance and repair plans. This holds true not only for routine, scheduled maintenance activities but also for those unexpected repairs that arise sporadically.
By proactively addressing maintenance requirements and incorporating them into the budgetary framework, businesses can safeguard their operational continuity, optimize the lifespan of their assets, and ultimately enhance their financial performance.
Conclusion
A facility maintenance plan ensures that buildings, equipment, and infrastructure remain in optimal condition. This proactive approach extends the lifespan of assets, reduces operational costs, and minimizes disruptions from unexpected breakdowns.
Preventive maintenance is key, involving regular inspections, cleaning, and servicing to identify and address potential problems before they escalate. This is more cost-effective than emergency repairs and downtime. Software applications like CMMS or CAFM software can enhance efficiency by organizing and tracking maintenance activities, and providing data for decision-making.
A well-structured plan includes routine inspections, preventive maintenance, emergency repairs, inventory management, contractor management, budgeting, regulatory compliance, and sustainability measures. This comprehensive approach extends asset lifespan, reduces costs, minimizes downtime, improves safety and compliance, and enhances asset value and performance.
In today's business environment, a well-executed facility maintenance plan is essential for protecting investments, optimizing operations, and achieving long-term success.
TABLE OF CONTENTS
Keep Reading
Ever find yourself checking into a luxury hotel and expecting a relaxing stay, only to find a ...
11 Apr 2025
Organizations are witnessing swift changes in the business environment and confronting a ...
8 Apr 2025
Last month, news outlets and the entire internet was abuzz with the return of NASA astronauts ...
3 Apr 2025
What comes first - CMMS or predictive maintenance? If your answer is either, it is correct. ...
28 Mar 2025
Artificial intelligence (AI) talk has become commonplace. Today, engaging in business-focused ...
27 Mar 2025
Imagine a world where machines predict, diagnose, and fix their issues before they fail. This ...
25 Mar 2025
Think of managing your maintenance operations like managing a championship sports team. Just ...
21 Mar 2025
The maintenance sector is battling a severe talent shortage that threatens to undermine ...
7 Mar 2025
Manufacturing maintenance is the backbone of industrial efficiency, ensuring machines run ...
5 Mar 2025
No one likes playing a guessing game when equipment breaks down. Yet, maintenance teams often ...
4 Mar 2025
The size of the preventive maintenance software market is discussed in millions of dollars, ...
4 Mar 2025
The organizational structure and corporate hierarchy vary from company to company. Large ...
28 Feb 2025
Maintenance procedures are essential for ensuring the longevity and reliability of machinery ...
21 Feb 2025
Sustainability is no longer just a buzzword; it's a critical component of corporate social ...
20 Feb 2025
A Computerized Maintenance Management System (CMMS) relies on accurate, well-organized data ...
18 Feb 2025
In an era where technology drives operational efficiency, Computerized Maintenance Management ...
14 Feb 2025
A Computerized Maintenance Management System (CMMS) is a key component of modern maintenance ...
13 Feb 2025
Introduction Maintenance management is the foundation of maintenance operations in industries ...
11 Feb 2025
Introduction A Computerized Maintenance Management System (CMMS) is software designed to help ...
7 Feb 2025
Introduction Due to a growing awareness of the need to combat climate change, the green ...
6 Feb 2025