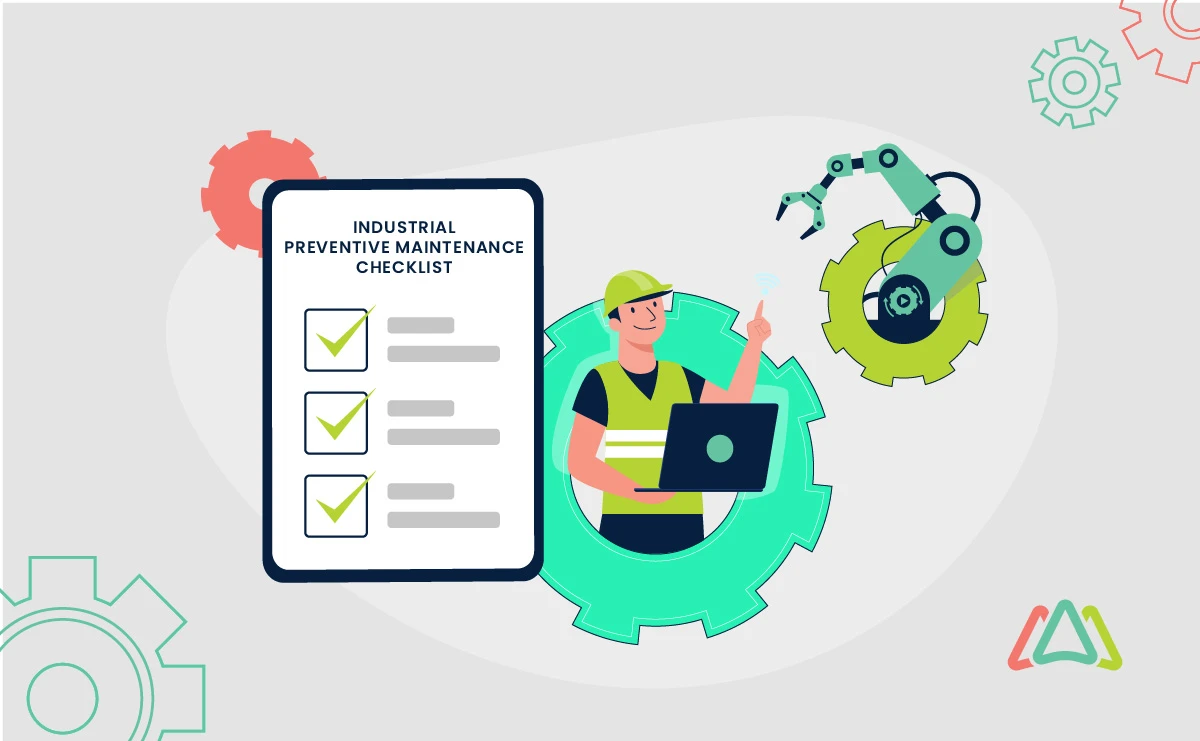
Industrial Preventive Maintenance Checklists to Build Resilience in Industrial Operations
Amidst the ceaseless hum of machinery and the relentless pursuit of output, ensuring that equipment remains operational is a challenge that industries confront daily. This is where preventive maintenance safeguards against disruptions and breakdowns.
Preventive maintenance is a proactive approach to equipment upkeep. Rather than waiting for machinery to break down and then responding reactively, preventive maintenance anticipates potential issues and addresses them before they escalate into costly repairs. In industrial settings, where downtime often means significant losses in productivity and revenue and can result in safety hazards, the importance of preventive maintenance cannot be overstated.
By systematically inspecting, servicing, and replacing components according to a planned schedule, preventive maintenance ensures that equipment operates at peak efficiency. It minimizes the risk of sudden failures, extends the lifespan of machinery, and optimizes operational performance. Moreover, by identifying and rectifying minor issues early on, industrial preventive maintenance mitigates the likelihood of more extensive, expensive repairs down the road. It enables industrial organizations to maintain a competitive edge by maximizing uptime, enhancing productivity, and controlling operational costs.
In light of the important role that preventive maintenance plays in industrial operations, this article equips industrial maintenance professionals with a comprehensive checklist for preventive maintenance. The industrial preventive maintenance checklist serves as a roadmap for implementing an effective preventive maintenance program tailored to the unique needs of industrial facilities.
From mechanical systems to electrical components, fluid systems, structural integrity, and software control systems, the checklist covers a broad spectrum of maintenance tasks essential for sustaining equipment reliability. Each component is meticulously outlined, accompanied by clear instructions, recommended frequencies, and best practices for execution.
Essential Components of an Industrial Preventive Maintenance Checklist
Industrial equipment is a complex combination of mechanical, electrical, and structural components, each playing a vital role in the smooth functioning of operations. These components require careful attention to ensure optimal performance, longevity, and equipment reliability.
1. Mechanical Systems
Mechanical systems form the backbone of industrial machinery, comprising a myriad of moving parts and components. Proper maintenance of these mechanical systems is key to prevent early wear, minimize friction, and mitigate the risk of failures. The following tasks are integral to ensuring the health and performance of mechanical systems:
Inspection and Lubrication of Moving Parts
Moving parts within industrial machinery are subjected to constant friction and wear during operation. Regular inspection and lubrication of these components are essential to reduce friction, prevent overheating, and extend the lifespan of mechanical parts. Lubricants such as oils and greases serve as a protective barrier, minimizing wear and corrosion while facilitating smooth motion.
Belt and Chain Tension Checks
Belts and chains are common components in industrial machinery, transmitting power and motion between rotating shafts. Proper tensioning of belts and chains is important to ensure efficient power transmission and prevent slippage or excessive wear. Periodic checks of belt tension and alignment help maintain optimal performance and prevent premature failure.
Bearing Inspections and Replacements
Bearings play a pivotal role in supporting rotating shafts and reducing friction between moving parts. Over time, bearings can wear out due to continuous use, contamination, or inadequate lubrication. Regular inspections of bearings for signs of wear, noise, or abnormal vibration are essential to identify potential issues early on. Timely replacement of worn or damaged bearings prevents failures and extends the service life of machinery.
Alignment and Balancing Assessments
Proper alignment and balancing of rotating equipment are critical to prevent excessive vibration, premature wear, and structural damage. Misalignment of shafts or unbalanced rotating components can lead to increased friction, bearing failures, and reduced efficiency. Periodic assessments of alignment and balancing ensure that machinery operates within specified tolerances, minimizing wear and maximizing performance.
2. Electrical Systems
Electrical systems are responsible for powering, controlling, and monitoring various processes of industrial machinery. Regular maintenance of these systems is important to prevent electrical faults, ensure compliance with safety standards, and optimize performance. The following tasks are fundamental to maintaining the health and functionality of electrical systems:
Inspection of Electrical Connections
Electrical connections are prone to loosening, corrosion, and overheating, which can lead to voltage drops, electrical arcing, and fire hazards. Regular inspection of electrical connections, terminals, and junction boxes is essential to identify signs of wear, damage, or degradation. Tightening loose connections, cleaning corroded terminals, and replacing damaged components mitigate the risk of electrical faults and ensure reliable operation.
Testing of Circuit Breakers and Fuses
Circuit breakers and fuses serve as critical safety devices, protecting electrical circuits from overloads, short circuits, and faults. Periodic testing of circuit breakers and fuses helps verify their functionality and responsiveness to abnormal conditions. Testing procedures may include verifying proper tripping currents, checking for continuity, and inspecting for signs of damage or deterioration. Properly functioning circuit protection devices minimize the risk of electrical fires, equipment damage, and personnel injury.
Calibration of Sensors and Gauges
Sensors and gauges play a vital role in monitoring various parameters such as temperature, pressure, flow rates, and levels within industrial processes. Calibration ensures the accuracy and reliability of these instruments, enabling precise control and monitoring of process variables. Periodic calibration of sensors and gauges involves comparing their readings against reference standards and making adjustments as necessary. Accurate sensor readings facilitate optimal process control, prevent deviations from desired operating conditions, and enhance overall system performance.
Verification of Power Quality
The quality of electrical power supplied to industrial equipment can impact its performance, efficiency, and longevity. Variations in voltage, frequency, harmonics, and power factor can adversely affect sensitive electronic components and motor-driven machinery. Regular verification of power quality parameters helps identify abnormalities such as voltage sags, surges, and harmonic distortions. Monitoring power quality enables proactive measures to mitigate risks, such as installing voltage regulators, harmonic filters, or power conditioning equipment. Ensuring stable and high-quality power supply enhances equipment reliability, reduces the risk of malfunctions, and improves energy efficiency.
3. Fluid Systems
Fluid systems encompass a wide range of components, including lubrication systems, coolant systems, hydraulic systems, and more. Regular maintenance of these systems is important to prevent contamination, overheating, and fluid loss, which can lead to equipment downtime and costly repairs. The following tasks are fundamental to maintaining the health and functionality of fluid systems:
Oil and Fluid Level Checks
Regular monitoring of oil and fluid levels is essential to ensure proper lubrication and cooling of industrial machinery. Insufficient oil levels can lead to increased friction, overheating, and accelerated wear of components. Conversely, overfilling fluids can cause leaks, foaming, and decreased system efficiency. Routine checks of oil and fluid levels, accompanied by timely top-ups, help maintain optimal operating conditions and extend the lifespan of equipment.
Filter Replacements
Filters play a critical role in removing contaminants, debris, and impurities from fluid systems, thereby ensuring the cleanliness of fluids. Over time, filters can become clogged or saturated, impairing their effectiveness and potentially causing damage to downstream components. Regular replacement of filters according to manufacturer recommendations is essential to maintain filtration efficiency and prevent system contamination. Timely filter replacements help preserve fluid quality, prevent premature wear of components, and minimize the risk of system failures.
Coolant System Inspections
Coolant systems are responsible for dissipating heat generated during industrial processes, thereby preventing overheating and maintaining optimal operating temperatures. Regular inspections of coolant systems, including coolant levels, circulation pumps, hoses, and radiators, are essential to ensure proper heat dissipation and prevent thermal-related failures. Checks for signs of coolant leaks, corrosion, or contamination should be performed periodically to identify potential issues early on and prevent system malfunctions.
Leak Detection and Repair
Fluid leaks pose a significant risk to equipment reliability, safety, and environmental compliance within industrial facilities. Leaks can result in fluid loss, contamination of surrounding areas, and potential hazards to personnel and equipment. Routine inspections for fluid leaks, accompanied by prompt detection and repair of leaks, are essential preventive maintenance tasks. Utilizing leak detection methods such as visual inspections, dye penetrant testing, or infrared thermography helps identify leak sources and prevent further fluid loss. Timely repair of leaks, whether through sealing, welding, or component replacement, helps avoid the risk of equipment damage and environmental pollution.
4. Structural Components
Structural components encompass a wide range of elements, including beams, columns, frames, supports, and other load-bearing structures. Regular inspection, maintenance, and repair of these components are critical to identify potential weaknesses, prevent deterioration, and maintain structural integrity. The following tasks are fundamental to maintaining the health and functionality of structural components:
Visual Inspections for Signs of Wear or Damage
Visual inspections are the first line of defense in identifying signs of wear, damage, or structural degradation. Regular visual inspections of structural components, conducted by trained personnel, help detect cracks, deformations, corrosion, or other anomalies that may compromise structural integrity. Inspections should encompass all visible surfaces, joints, welds, and connections to identify potential weak points. Prompt identification of issues allows for timely intervention and prevents the escalation of structural problems.
Weld Inspections
Welded joints are critical components in many industrial structures, providing strength and stability under load. However, welds are susceptible to defects, such as cracks, porosity, or incomplete fusion, which can compromise the structural integrity. Regular weld inspections using non-destructive testing techniques, such as ultrasonic testing or magnetic particle inspection, verify the quality and integrity of welded connections. Inspections should be performed according to industry standards and regulations to ensure compliance and safety.
Corrosion Prevention and Treatment
Corrosion is a common threat to structural components, particularly in harsh environments or corrosive conditions. Left unchecked, corrosion can weaken metal structures, leading to structural failures and safety hazards. Implementing corrosion prevention measures, such as coatings, inhibitors, or cathodic protection systems, helps to avoid the risk of corrosion and extend the life of structural components. Regular inspections for signs of corrosion, accompanied by treatment and repair, are essential preventive maintenance activities to preserve structural integrity.
Structural Stability Assessments
Structural stability assessments evaluate the load-bearing capacity and stability of industrial structures under various operating conditions. These assessments may include structural analysis, load testing, or finite element modeling to determine the structural adequacy and safety margins. Periodic stability assessments help identify potential deficiencies, assess the impact of changes in loading conditions, and ensure compliance with safety standards and regulations. Structural stability assessments are essential for maintaining a safe working environment and preventing serious failures.
5. Software and Control Systems
Software and control systems encompass a wide range of technologies, including programmable logic controllers (PLCs), supervisory control and data acquisition (SCADA) systems, human-machine interfaces (HMIs), and software applications. Regular maintenance of these systems is critical to ensure reliability, security, and compliance with operational requirements. The following tasks are fundamental to maintaining the health and functionality of software and control systems:
Update and Patch Software as Needed
Software updates and patches address vulnerabilities, bugs, and performance issues in industrial software applications and operating systems. Regularly updating and patching software ensures that systems remain secure, stable, and compatible with evolving hardware and software environments. Implementing a structured update management process, including testing updates in a controlled environment before deployment, helps minimize the risk of compatibility issues and unintended consequences. If the software is provided and supported by an outside vendor, ensure that your organization is running the latest version and that patches and updates are current.
Backup and Recovery Procedures
Data loss can have severe consequences for industrial operations, leading to downtime, loss of productivity, and regulatory non-compliance. Implementing backup and recovery procedures ensures the integrity and availability of critical data and software configurations. Regularly scheduled backups of software configurations, process data, and system settings, coupled with periodic testing of recovery procedures, help mitigate the risk of data loss and expedite recovery in the event of system failures or disasters.
Calibration of Control Instruments
Control instruments such as sensors, transmitters, and actuators play an important role in monitoring and controlling industrial processes. Calibration ensures the accuracy and reliability of control instruments, enabling precise measurement and control of process variables. Periodic calibration of control instruments, using traceable standards and calibration equipment, helps maintain measurement accuracy and compliance with regulatory requirements. Regular calibration checks identify drift or deviations in instrument readings and facilitate adjustments or replacements when needed.
Testing of Emergency Shutdown Systems
Emergency Shutdown Systems (ESDs) are important safety mechanisms designed to protect personnel, equipment, and the environment in the event of emergencies or hazardous conditions. Testing ESD systems regularly ensures their proper functionality and responsiveness to emergency situations. Functional testing of ESD systems, including simulated emergency scenarios and activation tests, verifies the effectiveness of shutdown sequences and alarm notifications. Periodic inspections of ESD components, such as emergency stop buttons, safety interlocks, and shutdown valves, ensure that they are in good working condition and ready for immediate activation when needed.
Industrial Preventive Maintenance Checklist Example
1. Mechanical Systems
Inspect and lubricate moving parts:
- Check lubrication levels and replenish as necessary.
- Lubricate bearings, gears, and other moving components according to manufacturer recommendations.
Perform belt and chain tension checks:
- Check belt tension and adjust if necessary.
- Inspect chains for wear and proper tension.
Conduct bearing inspections and replacements:
- Inspect bearings for signs of wear, noise, or vibration.
- Replace worn or damaged bearings as needed.
Perform alignment and balancing assessments:
- Check the alignment of shafts, couplings, and pulleys.
- Balance rotating components to minimize vibration and wear.
2. Electrical Systems
Inspect electrical connections:
- Check for loose connections, corrosion, or overheating.
- Tighten connections and clean terminals as necessary.
Test circuit breakers and fuses:
- Verify proper operation of circuit breakers and fuses.
- Test tripping mechanisms and replace faulty components.
Calibrate sensors and gauges:
- Calibrate temperature, pressure, and level sensors.
- Verify the accuracy of gauges and meters.
Verify power quality:
- Monitor voltage, frequency, and power factor.
- Address any deviations from acceptable levels.
3. Fluid Systems
Check oil and fluid levels:
- Monitor levels of lubricating oils, hydraulic fluids, and coolant.
- Top up fluids as necessary.
Replace filters:
- Replace oil, air, and fuel filters according to maintenance schedules.
- Clean or replace strainers and screens.
Inspect coolant systems:
- Check coolant levels and condition.
- Inspect hoses, pumps, and radiators for leaks or damage.
Detect and repair leaks:
- Inspect pipes, hoses, and fittings for leaks.
- Repair leaks promptly to prevent fluid loss and contamination.
4. Structural Components
Perform visual inspections:
- Inspect structural components for signs of corrosion, cracks, or deformation.
- Check welds for defects or discontinuities.
Conduct corrosion prevention and treatment:
- Apply protective coatings or inhibitors to prevent corrosion.
- Treat existing corrosion and repair damaged surfaces.
Assess structural stability:
- Perform load tests or structural analyses as necessary.
- Ensure that structural components meet safety and regulatory standards.
5. Software and Control Systems
Update and patch software:
- Install software updates and security patches.
- Ensure compatibility with hardware and other software components.
Backup and recovery:
- Regularly backup software configurations, databases, and critical data.
- Test backup and recovery procedures to ensure data integrity and availability.
Calibrate control instruments:
- Calibrate sensors, transmitters, and actuators to ensure accuracy.
- Verify the proper function of control loops and feedback mechanisms.
Test emergency shutdown systems:
- Conduct functional tests of emergency shutdown systems.
- Verify proper operation of alarms, interlocks, and safety circuits.
Implementation of the Industrial Preventive Maintenance Checklist
1. Training of Maintenance Personnel
Properly trained maintenance personnel are essential for the successful implementation of a preventive maintenance program. Training ensures that maintenance technicians possess the necessary knowledge, skills, and competencies to perform maintenance tasks safely and effectively. Training programs may cover a range of topics, including equipment operation, maintenance procedures, safety protocols, and the use of specialized tools and equipment.
By investing in comprehensive training for maintenance personnel, organizations can enhance workforce competency, reduce the risk of errors or accidents, and improve overall maintenance efficiency. Ongoing training and professional development opportunities enable maintenance technicians to stay abreast of emerging technologies, best practices, and regulatory requirements, ensuring continuous improvement in maintenance practices.
2. Integration of the Checklist into Daily, Weekly, and Monthly Routines
Integration of the preventive maintenance checklist into daily, weekly, and monthly routines is essential to ensure consistency and adherence to maintenance schedules. Maintenance schedules should be tailored to the specific needs and priorities of each industrial facility, taking into account factors such as equipment criticality, operating conditions, and production demands.
Daily maintenance routines may include tasks such as equipment inspections, lubrication, and basic troubleshooting to address minor issues proactively. Weekly maintenance routines may involve more comprehensive inspections, calibration checks, and preventive maintenance tasks identified in the checklist. Monthly maintenance routines may focus on in-depth inspections, equipment testing, and performance evaluations to identify trends or emerging issues.
By establishing clear maintenance schedules and incorporating the checklist into routine workflows, organizations can minimize the risk of unplanned downtime, extend equipment lifespan, and optimize maintenance resources. Regular adherence to maintenance schedules fosters a culture of accountability, teamwork, and continuous improvement, driving operational excellence across the organization.
Utilizing a CMMS to Automate and Schedule Industrial Preventive Maintenance Checklists
A CMMS serves as a central hub for managing maintenance activities, and when utilized effectively, it can automate and streamline the implementation of preventive maintenance checklists.
1. Centralized Maintenance Data Management
A CMMS provides a centralized repository for storing critical maintenance data, including equipment information, maintenance schedules, and historical maintenance records. By consolidating data in one accessible location, organizations can ensure consistency, accuracy, and transparency in their maintenance processes.
2. Automated Work Order Generation
With a CMMS, organizations can automate the generation of preventive maintenance work orders based on predefined schedules or condition-based triggers. Maintenance tasks from the preventive maintenance checklist can be converted into work orders automatically, eliminating the need for manual intervention and reducing the risk of work orders being missed.
3. Customizable Maintenance Schedules
CMMS software enables organizations to create customizable maintenance schedules tailored to the specific needs and priorities of their industrial operations. Maintenance schedules can be defined based on equipment criticality, operating conditions, and production demands. By establishing clear schedules for preventive maintenance tasks, organizations can ensure timely execution and maximize equipment uptime.
4. Resource Allocation and Optimization
With a CMMS, organizations can optimize resource allocation by assigning tasks to maintenance technicians based on their availability, skills, and location. CMMS software facilitates efficient workforce utilization, enabling organizations to allocate resources effectively and minimize idle time. By streamlining resource allocation, organizations can improve maintenance efficiency and reduce operational costs.
5. Real-time Work Tracking and Monitoring
CMMS software provides real-time visibility into maintenance activities, allowing organizations to track work progress and monitor completion status in real time. Maintenance technicians can update work orders as tasks are completed, providing supervisors and managers with up-to-date information on maintenance activities. Real-time monitoring enables organizations to identify potential bottlenecks or issues and take proactive measures to address them promptly.
6. Reporting and Analysis
A CMMS enables organizations to generate comprehensive reports and analyze maintenance data to identify trends, patterns, and areas for improvement. By analyzing maintenance data, organizations can identify recurring issues, optimize maintenance schedules, and make data-driven decisions to enhance maintenance effectiveness and efficiency.
TABLE OF CONTENTS
Keep Reading
Ever find yourself checking into a luxury hotel and expecting a relaxing stay, only to find a ...
11 Apr 2025
Organizations are witnessing swift changes in the business environment and confronting a ...
8 Apr 2025
Last month, news outlets and the entire internet was abuzz with the return of NASA astronauts ...
3 Apr 2025
What comes first - CMMS or predictive maintenance? If your answer is either, it is correct. ...
28 Mar 2025
Artificial intelligence (AI) talk has become commonplace. Today, engaging in business-focused ...
27 Mar 2025
Imagine a world where machines predict, diagnose, and fix their issues before they fail. This ...
25 Mar 2025
A facility maintenance plan is at the core of a facility’s operations. This organized ...
21 Mar 2025
Think of managing your maintenance operations like managing a championship sports team. Just ...
21 Mar 2025
The maintenance sector is battling a severe talent shortage that threatens to undermine ...
7 Mar 2025
Manufacturing maintenance is the backbone of industrial efficiency, ensuring machines run ...
5 Mar 2025
No one likes playing a guessing game when equipment breaks down. Yet, maintenance teams often ...
4 Mar 2025
The size of the preventive maintenance software market is discussed in millions of dollars, ...
4 Mar 2025
The organizational structure and corporate hierarchy vary from company to company. Large ...
28 Feb 2025
Maintenance procedures are essential for ensuring the longevity and reliability of machinery ...
21 Feb 2025
Sustainability is no longer just a buzzword; it's a critical component of corporate social ...
20 Feb 2025
A Computerized Maintenance Management System (CMMS) relies on accurate, well-organized data ...
18 Feb 2025
In an era where technology drives operational efficiency, Computerized Maintenance Management ...
14 Feb 2025
A Computerized Maintenance Management System (CMMS) is a key component of modern maintenance ...
13 Feb 2025
Introduction Maintenance management is the foundation of maintenance operations in industries ...
11 Feb 2025
Introduction A Computerized Maintenance Management System (CMMS) is software designed to help ...
7 Feb 2025