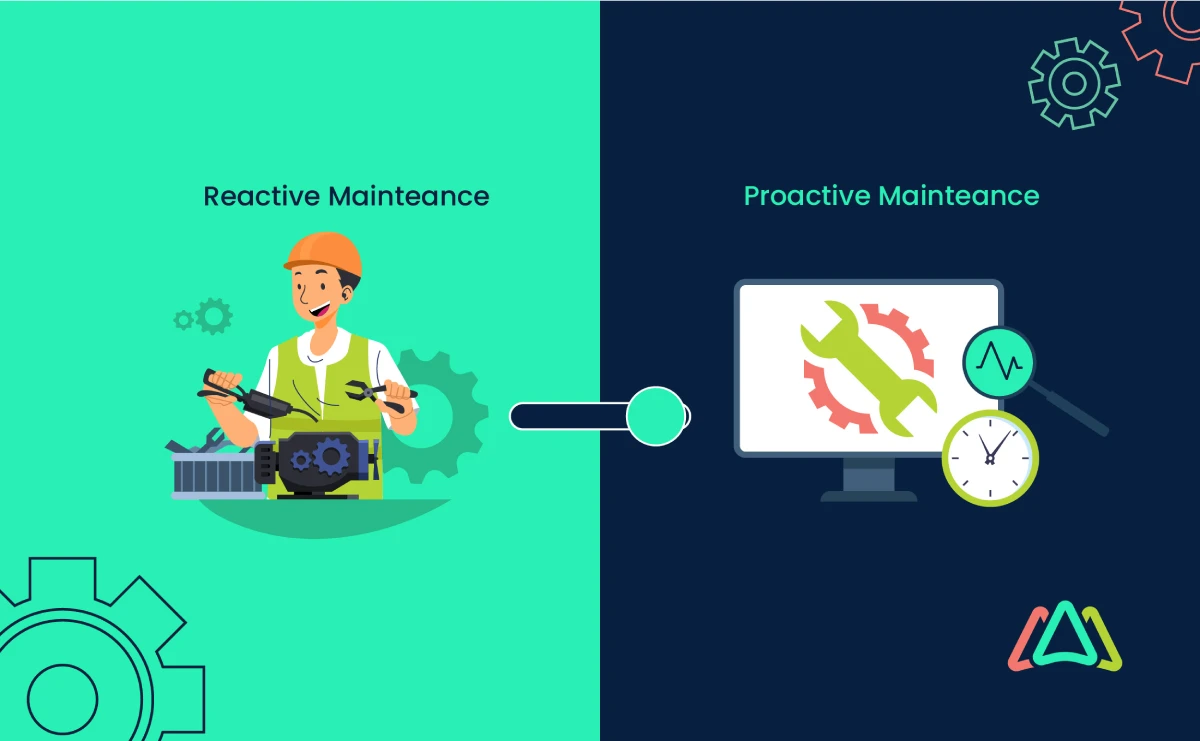
Is it Enough for SMBs to Rely Solely on Reactive Maintenance?
Small to Medium Businesses (SMBs) form the backbone of economies worldwide, driving innovation, employment, and economic growth. These organizations often face unique challenges, including budget constraints and limited resources. As a result, many SMBs find themselves leaning towards reactive maintenance due to its seemingly cost-effective and straightforward nature.
The term "reactive maintenance" refers to a maintenance strategy where repairs and maintenance activities are carried out in response to equipment failures or breakdowns. Instead of pre-scheduled interventions, organizations using reactive maintenance address issues as they arise. This approach is often seen as a quick-fix solution to immediate problems, focusing on resolving issues to bring systems back to operational status.
When is Reactive Maintenance Enough, and When Does it Fall Short?
Industries & Situations Where Reactive Maintenance May Suffice
Reactive maintenance can be considered adequate in certain industries and situations, particularly when immediate response to equipment failures is more critical than preventing them in advance. Some industries that may find reactive maintenance suitable include:
1. Service-Based Businesses
Companies that provide services rather than produce physical goods may find reactive maintenance more acceptable. Immediate repairs might be prioritized to maintain ongoing service delivery.
2. Low-Criticality Environments
In settings where equipment failure does not pose severe consequences, such as in non-hazardous office environments, the urgency for preventative measures may be diminished.
3. Limited Resource Environments
Organizations with highly constrained resources, such as startups or small businesses in their early stages, might prioritize reactive maintenance due to budgetary restrictions.
Limitations in Specific Scenarios
While reactive maintenance may be suitable in certain situations, it has inherent limitations and shortcomings that make it less effective in the long run. Some specific scenarios where reactive maintenance falls short include:
1. Increased Downtime
Relying solely on reactive maintenance can lead to extended downtime periods. The time required to identify, assess, and repair equipment failures can result in production halts, affecting overall operational efficiency.
2. Higher Costs in the Long Run
Although reactive maintenance may seem cost-effective initially, the cumulative costs of frequent repairs and potential equipment replacements can surpass the expenses associated with preventive maintenance over time.
3. Safety Concerns
In industries where safety is paramount, relying on reactive maintenance may expose workers to higher risks. Unplanned equipment failures can lead to accidents or hazardous situations that could have been prevented with proactive maintenance measures.
4. Loss of Productivity
Reactive maintenance often leads to a reactive mindset throughout the organization. This can hinder the development of a proactive culture aimed at identifying and addressing issues before they escalate, resulting in decreased overall productivity.
Understanding the contextual appropriateness of reactive maintenance is important for organizations to strike a balance between immediate problem-solving and the long-term benefits of proactive maintenance strategies.
Why Do SMBs Often Rely on Reactive Maintenance?
1. Cost Considerations
Short-Term Budget Constraints
Small to Medium Businesses (SMBs) often operate within tight budget constraints, especially in their early stages of development. Reactive maintenance appears attractive in the short term because it requires no significant upfront investment. SMBs might prioritize addressing immediate issues to keep operational costs low, allocating resources based on urgent needs rather than investing in preventive measures that seem less immediately pressing.
Lack of Perceived Immediate Benefits of Proactive Maintenance
Proactive maintenance, such as preventive or predictive strategies, involves upfront costs for inspections, monitoring systems, and planned interventions. For SMBs focused on day-to-day survival, these preventive measures might not seem immediately beneficial. The future-oriented nature of proactive maintenance can be overshadowed by the urgency of handling present challenges, leading SMBs to favor reactive approaches to save money in the short run.
2. Resource Limitations
Limited Personnel and Expertise
SMBs often operate with lean teams, where employees wear multiple hats to cover diverse responsibilities. In such resource-constrained environments, dedicating staff solely to maintenance activities might not be feasible. Consequently, reactive maintenance becomes a default choice, as it requires minimal specialized expertise and can be handled on an ad-hoc basis by existing personnel.
Time Constraints
SMBs are characterized by fast-paced environments where time is of the essence. The perceived time investment required for planning and implementing proactive maintenance strategies can deter SMBs. Reactive maintenance, with its immediate and ad-hoc nature, aligns more closely with the quick-fix mentality prevalent in resource-limited environments, where time is a precious commodity.
While cost and resource considerations might make reactive maintenance initially appealing for SMBs, understanding the long-term implications and exploring strategies to overcome these constraints is important for ensuring sustainable operations and growth.
Benefits of Solely Relying on Reactive Maintenance
1. Immediate Cost Savings
1.1 No Upfront Investment in Preventive Measures
One of the primary attractions of relying solely on reactive maintenance for Small to Medium Businesses (SMBs) lies in its immediate cost-saving aspect. Unlike proactive maintenance strategies that involve substantial upfront investments in inspections, monitoring systems, and preventive interventions, reactive maintenance requires no significant financial commitment at the outset. This makes it particularly appealing for SMBs operating within tight budget constraints, allowing them to address issues as they arise without allocating funds to pre-emptive measures.
1.2 Pay-As-You-Go Model
Reactive maintenance operates on a pay-as-you-go model, meaning that SMBs only incur costs when issues occur and repairs are necessary. This "fix it when it breaks" approach aligns with the financial reality of many SMBs, allowing them to manage costs more dynamically. The pay-as-you-go model provides flexibility in budgeting, ensuring that resources are directed specifically toward addressing immediate problems rather than being allocated for potential future issues.
2. Simplicity and Ease of Implementation
2.1 No Need for Extensive Planning
Reactive maintenance is inherently straightforward, requiring no elaborate planning or scheduling of maintenance activities. For SMBs with limited resources and personnel, the simplicity of reactive maintenance allows them to focus on day-to-day operations without the need for detailed maintenance plans. This simplicity is particularly advantageous for businesses where operational agility is important, as they can address issues as they arise without being burdened by extensive planning processes.
2.2 No Complex Scheduling
Unlike preventive maintenance, which involves scheduling regular inspections and interventions based on equipment life cycles or usage patterns, reactive maintenance operates on an as-needed basis. SMBs can avoid the complexity of developing and adhering to intricate maintenance schedules, freeing up time and resources for immediate operational needs. This lack of complex scheduling aligns with the dynamic nature of SMBs, allowing them to adapt quickly to changing priorities and circumstances.
Drawbacks of Solely Relying on Reactive Maintenance
1. Increased Downtime and Production Loss
1.1 Unplanned Disruptions
One of the significant drawbacks of relying solely on reactive maintenance is the occurrence of unplanned disruptions. When equipment fails unexpectedly, it leads to immediate disruptions in operations, causing downtime that can be detrimental to productivity. Unplanned disruptions can result in delays, missed deadlines, and customer dissatisfaction, all of which can have lasting impacts on a business's reputation.
1.2 Reactive Responses Lead to Longer Downtimes
Reactive maintenance, by its nature, involves responding to issues after they have occurred. This reactive approach often leads to longer downtimes as the diagnosis and repair process is initiated only when a problem becomes evident. In contrast, proactive maintenance allows for the identification and resolution of potential issues before they escalate, minimizing the duration of downtime and its associated negative impacts.
2. Higher Long-Term Costs
2.1 Repairs Are Often More Expensive Than Preventive Measures
While reactive maintenance may seem cost-effective in the short term due to its pay-as-you-go nature, repairs conducted after equipment failures are often more expensive than preventive measures. Reactive responses may necessitate urgent repairs, replacement of critical components, or even complete equipment overhauls, leading to higher costs than if potential issues had been addressed proactively.
2.2 Cumulative Impact on the Budget
Over time, the cumulative impact of frequent reactive responses can strain the budget of Small to Medium Businesses (SMBs). The continuous cycle of breakdowns and repairs can result in a significant financial burden, surpassing the costs associated with implementing preventive maintenance strategies. The cumulative impact extends beyond direct repair expenses to include indirect costs related to production delays, overtime payments, and potential loss of business opportunities.
Understanding and mitigating the drawbacks of relying solely on reactive maintenance is important for SMBs aiming for sustainable growth. While immediate cost savings and simplicity may be appealing, a balanced approach that incorporates proactive measures can contribute to long-term cost-effectiveness and operational resilience.
How Can Small to Medium Businesses Make Their Processes More Efficient?
1. Shift in Mindset from Reactive to Proactive
Instead of waiting for equipment failures to occur, proactive maintenance involves anticipating potential issues and addressing them before they escalate. This shift requires a cultural change within the organization, fostering a mindset that values preventive measures and long-term planning over immediate fixes.
Implementing a proactive mindset involves creating awareness among employees about the benefits of anticipating and preventing maintenance issues. Training programs and workshops can be effective in instilling a culture that values early detection and resolution of potential problems, encouraging staff to actively contribute to the maintenance process.
Proactive maintenance, specifically in the form of preventive measures, offers a range of long-term benefits for SMBs. By systematically inspecting, testing, and maintaining equipment at scheduled intervals, businesses can:
- Extend Equipment Lifespan: Regular maintenance helps identify and address wear and tear, preventing premature equipment failures and extending their overall lifespan.
- Minimize Downtime: Anticipating issues before they lead to breakdowns reduces unplanned downtime. This ensures smoother operations and minimizes disruptions to production schedules.
- Control Costs: While preventive maintenance involves upfront costs, these are often outweighed by the savings realized through reduced emergency repairs and extended equipment longevity.
- Enhance Safety: Proactively addressing potential hazards improves workplace safety. Regular inspections and maintenance reduce the risk of accidents and injuries, creating a safer working environment.
- Improve Operational Efficiency: With equipment operating at optimal levels, businesses experience improved efficiency and productivity. Preventive maintenance contributes to a smoother workflow, allowing SMBs to meet production demands more consistently.
Embracing proactive maintenance requires a commitment to long-term planning and investment, but the benefits contribute significantly to overall operational efficiency and sustainability for Small to Medium Businesses.
2. Implementation of a CMMS
SMBs can greatly enhance their maintenance processes by implementing a Computerized Maintenance Management System (CMMS). CMMS is a comprehensive software solution designed to streamline and automate maintenance operations. Key features include:
- Asset Management: CMMS software allows businesses to effectively manage and track their assets, including equipment, machinery, and facilities. This ensures a centralized database of asset information, maintenance history, and upcoming tasks.
- Work Order Management: The system enables the creation, tracking, and management of work orders. This feature ensures that maintenance tasks are efficiently scheduled, assigned, and completed, reducing downtime and improving workflow.
- Preventive Maintenance Scheduling: CMMS allows SMBs to set up and manage preventive maintenance schedules. By automating routine inspections and maintenance activities, businesses can proactively address issues before they escalate, contributing to increased reliability and reduced downtime.
- Inventory Management: CMMS helps in managing spare parts and inventory efficiently. Businesses can track stock levels, order supplies in a timely manner, and reduce costs associated with stockouts or overstocking.
- Reporting and Analytics: The system provides reporting and analytics capabilities, offering insights into maintenance performance, costs, and trends. This data-driven approach aids in making informed decisions and optimizing maintenance strategies.
3. Training and Skill Development
3.1 Empowering Staff with Maintenance Knowledge
To fully leverage the benefits of proactive maintenance, SMBs should invest in training programs to enhance the maintenance knowledge and skills of their staff. This includes providing training on the use of CMMS, equipment troubleshooting, and preventive maintenance practices. Empowering employees with the necessary knowledge equips them to identify potential issues, perform basic maintenance tasks, and contribute to the overall efficiency of the maintenance process.
3.2 Building a Proactive Maintenance Culture
Beyond technical skills, fostering a proactive maintenance culture is essential for long-term success. This involves instilling a mindset that values preventive measures and encourages employees at all levels to actively participate in maintaining equipment and facilities. Establishing regular communication channels, recognizing and rewarding proactive behavior, and incorporating maintenance goals into the overall organizational strategy contribute to building a culture where everyone understands the importance of proactive maintenance.
Implementing a CMMS and investing in training and skill development go hand-in-hand, providing SMBs with the tools and knowledge necessary to transition from reactive to proactive maintenance practices. These strategic initiatives contribute to improved operational efficiency, reduced downtime, and increased overall sustainability for Small to Medium Businesses.
TABLE OF CONTENTS
Keep Reading
Ever find yourself checking into a luxury hotel and expecting a relaxing stay, only to find a ...
11 Apr 2025
Organizations are witnessing swift changes in the business environment and confronting a ...
8 Apr 2025
Last month, news outlets and the entire internet was abuzz with the return of NASA astronauts ...
3 Apr 2025
What comes first - CMMS or predictive maintenance? If your answer is either, it is correct. ...
28 Mar 2025
Artificial intelligence (AI) talk has become commonplace. Today, engaging in business-focused ...
27 Mar 2025
Imagine a world where machines predict, diagnose, and fix their issues before they fail. This ...
25 Mar 2025
A facility maintenance plan is at the core of a facility’s operations. This organized ...
21 Mar 2025
Think of managing your maintenance operations like managing a championship sports team. Just ...
21 Mar 2025
The maintenance sector is battling a severe talent shortage that threatens to undermine ...
7 Mar 2025
Manufacturing maintenance is the backbone of industrial efficiency, ensuring machines run ...
5 Mar 2025
No one likes playing a guessing game when equipment breaks down. Yet, maintenance teams often ...
4 Mar 2025
The size of the preventive maintenance software market is discussed in millions of dollars, ...
4 Mar 2025
The organizational structure and corporate hierarchy vary from company to company. Large ...
28 Feb 2025
Maintenance procedures are essential for ensuring the longevity and reliability of machinery ...
21 Feb 2025
Sustainability is no longer just a buzzword; it's a critical component of corporate social ...
20 Feb 2025
A Computerized Maintenance Management System (CMMS) relies on accurate, well-organized data ...
18 Feb 2025
In an era where technology drives operational efficiency, Computerized Maintenance Management ...
14 Feb 2025
A Computerized Maintenance Management System (CMMS) is a key component of modern maintenance ...
13 Feb 2025
Introduction Maintenance management is the foundation of maintenance operations in industries ...
11 Feb 2025
Introduction A Computerized Maintenance Management System (CMMS) is software designed to help ...
7 Feb 2025