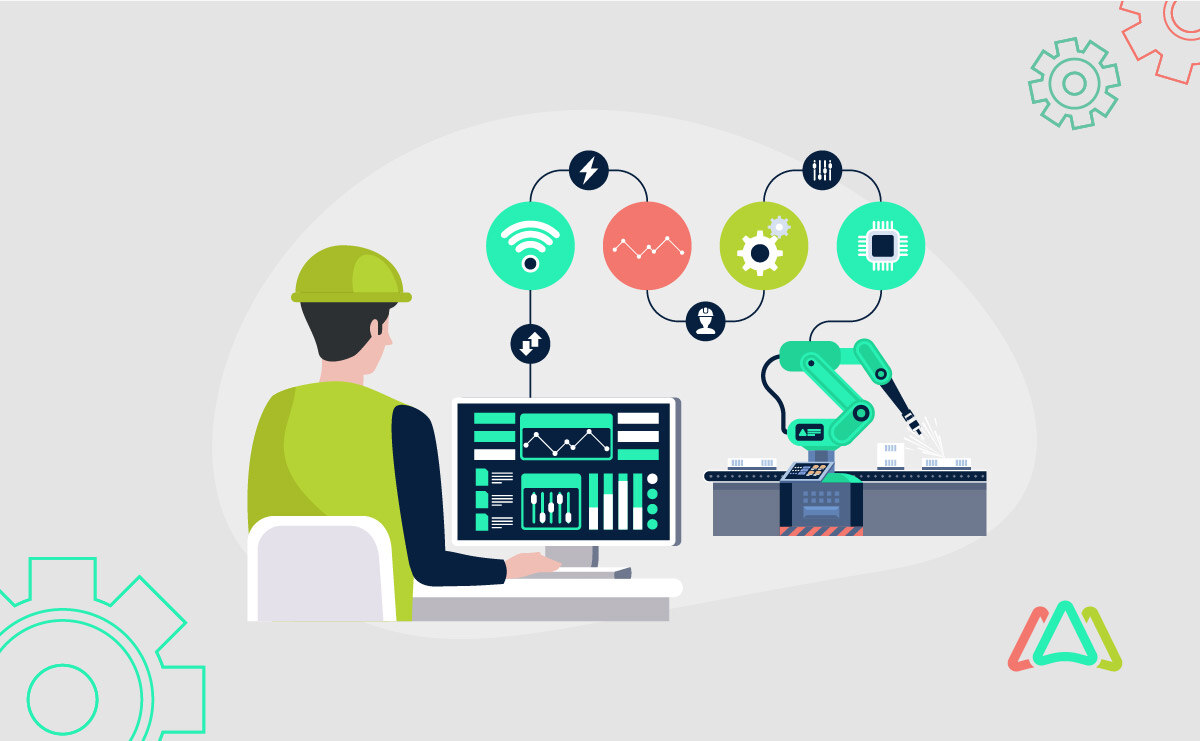
Decoding Maintenance Analytics - Uncover Hidden Patterns to Optimize Equipment Performance
Maintenance analytics refers to data analysis techniques and tools, often integrated with a Computerized Maintenance Management System (CMMS). Maintenance analytics is used to monitor, predict, and enhance the performance and reliability of equipment and assets. With CMMS, maintenance analytics can track asset health, identify patterns and trends, and support proactive decision-making that minimizes downtime, extends asset life, and reduces costs.
Companies are embracing data analytics in their maintenance operations, empowering them to transition from reactive to predictive maintenance. This shift in approach allows managers to identify potential issues before they escalate, putting preventing breakdowns and downtime,l and cutting costs. By analyzing data, maintenance departments can optimize maintenance schedules, extend asset life, and make informed decisions that enhance operational efficiency and cost savings. This article examines maintenance analytics programs and how they benefit the organizations implementing them.
What is a Maintenance Analytics Program?
Simply put, a maintenance analytics program is a structured approach designed to collect, analyze, and utilize maintenance data to improve equipment performance and reliability. These processes are made possible by combining tools, methods, and metrics to monitor asset health, predict failures, and guide data-driven maintenance strategies.
Components of a Maintenance Analytics Program
A multifactorial maintenance analytics program includes data collection, where information is gathered from sensors, maintenance logs, and CMMS systems to capture asset performance and health metrics. Following this initial step is data processing, which cleans and organizes the data input and prepares it for practical analysis. Finally, analysis tools such as machine learning models, predictive analytics software, and CMMS analytics interpret the data. Data analysis reveals patterns and insights that steer proactive maintenance decisions and optimize equipment performance.
The Role of CMMS Analytics in a Maintenance Analytics Program
CMMS analytics play a pivotal role in a maintenance analytics program. It collects and organizes maintenance data, such as work orders records, asset history, and other performance metrics. A CMMS helps identify trends, track key performance indicators (KPIs), and provide insights into asset health. These measures allow maintenance teams to make informed, data-driven decisions, instilling confidence in their choices. CMMSs help organizations optimize maintenance schedules, prioritize tasks, and enhance predictive maintenance efforts. This results in improved asset reliability and reduced operational costs.
Launching a Maintenance Analytics Project
To initiate a successful maintenance analytics project involves the following key steps:
Define Objectives and Scope:
Establish clear goals for the project. For example, include objectives such as reducing downtime, improving asset life, or enhancing operational efficiency. It is essential to outline the assets and metrics to be monitored in the process.
Assemble the Right Team:
Involve data analysts, maintenance engineers, IT personnel, and other relevant stakeholders. These are the people who can contribute expertise throughout the project.
Collect and Organize Data:
Gathering historical maintenance data, asset performance records, and sensor data if available are key to establishing a baseline. Using a CMMS helps organize and access these records.
Select Analytics Tools and Software:
Be clear when choosing the tools that align with your objectives. Many CMMS and EAM (Enterprise Asset Management) platforms come equipped with built-in analytics, predictive maintenance, or machine learning models for advanced analysis.
Implement Data Processing and Integration:
Select processes for cleaning, formatting, and integrating data from different sources to enable accurate analysis.
Run Pilot Testing:
Before launching a full-scale analysis of your data, conduct a pilot test on a subset of equipment. This test run will evaluate the effectiveness of the analytics process and allow you to make any necessary adjustments.
Analyze Results and Optimize:
After running your pilot test, interpret the findings to identify patterns and insights. This is the time to refine processes and tools to optimize asset performance and reach the project’s goals. Once done, you’ll be in a position to run an analysis of all your data.
Scale and Monitor
Scaling and monitoring maintenance analytics is crucial. It involves expanding the analytics practices across additional assets or equipment while continuously observing and adjusting the maintenance strategy based on performance data. This ongoing process ensures the analytics program remains effective, meets company goals, and evolves to meet changing operational needs and goals over time, providing reassurance about its ongoing effectiveness.
Key Metrics and KPIs for Maintenance Analytics:
Key metrics and Key Performance Indicators (KPIs) for maintenance analytics are critical for tracking equipment performance, predicting failures, and optimizing maintenance strategies. These include metrics like *Mean Time Between Failure (MTBF) and *Mean Time to Repair (MTTR). Both metrics help assess asset reliability and repair efficiency, while Downtime objectively assesses the impact of equipment unavailability.
Additional KPIs, such as Maintenance Cost per Unit of Production and Asset Utilization Rate, provide insights into an asset’s financial and operational effectiveness. For instance, a high Maintenance Cost per Unit of Production may indicate inefficient maintenance practices, while a low Asset Utilization Rate may suggest underutilization of the asset. Together, these metrics guide data-driven decisions that impact productivity and cost efficiency.
Predictive Asset Maintenance Analytics
Predictive analytics in maintenance uses data analysis and advanced tools to predict when equipment might fail before it happens. In simpler terms, it's like having a crystal ball that tells you when your equipment is going to break down. By analyzing historical data and current asset conditions, predictive analytics allows maintenance teams to perform repairs quickly, preventing unexpected breakdowns and minimizing downtime.
Benefits of Predictive Asset Maintenance Analytics:
The following are key benefits of predictive asset maintenance analytics:
- Reduces Unplanned Downtime: Identifies potential issues early to prevent unexpected equipment failures.
- Lower Maintenance Costs: Helps optimize repair schedules, reducing the need for costly emergency repairs.
- Extends Asset Lifespan: Preventive repairs and timely maintenance keep equipment in optimal condition longer.
- Improves Safety: Detects and proactively addresses risks, reducing accidents and unsafe conditions.
- Increases Operational Efficiency: Ensures assets are available and functional when needed, improving productivity.
- Guides Data-Driven Decisions: Provides objective insights for better maintenance planning and resource allocation.
Asset Health Monitoring: Enhancing Performance with Real-Time Insights
Asset health monitoring is continuously tracking equipment conditions using sensors, inspections, and performance metrics data to assess an asset's current state. This real-time monitoring helps identify issues early, allowing for proactive maintenance that minimizes downtime and extends asset life.
Using Data Analytics for Effective Asset Health Monitoring
This proactive approach lets maintenance teams schedule timely interventions, optimize repair schedules, and extend asset lifespan. The result is reducing the risk of unexpected downtime.
Analytics tools are designed to identify hidden patterns and anomalies by processing large volumes of historical and real-time data. The tools use machine learning, statistical analysis, and trend-monitoring techniques. For example, machine learning algorithms can learn normal operating behaviors for equipment and expose deviations from these patterns, which may suggest potential failures.
Statistical analysis and anomaly detection algorithms spot unusual data points, trends, or fluctuations, signaling that maintenance may be required to prevent unexpected breakdowns. By using this approach, analytics tools help maintenance teams address issues proactively.
Integrating Predictive Analytics with CMMS Analytics
Synchronizing CMMS data with predictive models improves maintenance operations by combining detailed asset history with advanced predictive insights. More specifically, CMMS data provides essential information on past maintenance actions, asset conditions, and work orders, while predictive analytic models use this data to estimate future maintenance needs. Integrating CMMS and predictive analytics allows for more accurate maintenance scheduling, efficient resource allocation, and reduced unplanned downtime. Ultimately, this leads to cost savings and improved asset reliability. In combination, CMMS and predictive models create a more proactive and streamlined maintenance process.
Conclusion
Maintenance analytics offers many benefits, from reducing unexpected downtime and lowering maintenance costs to extending asset life and enhancing operational safety. By adopting a data-driven approach, companies can optimize their maintenance schedules, make proactive decisions, and boost overall equipment performance.
Launching a maintenance analytics program or improving an existing one is a practical step toward long-term efficiency and cost savings. Begin by setting clear goals, investing in the right tools, and building a team dedicated to ongoing improvement in maintenance analytics.
TABLE OF CONTENTS
Keep Reading
Imagine you're going through a compliance audit, and the inspector asks for maintenance ...
10 Jul 2025
Maintenance managers understand that disasters are unpredictable and can have a massive ...
4 Jul 2025
Asset lifespan is a key concern for executives and maintenance and facility management teams. ...
3 Jul 2025
Your company recently invested funds and time for new CMMS software, and six months later, it ...
1 Jul 2025
As Computerized Maintenance Management Systems (CMMS) become more connected and cloud-based, ...
1 Jul 2025
Edge computing is an innovative technology that enables data to be processed at the source, ...
24 Jun 2025
Facility management has undergone a significant transformation in recent times. Take, for ...
20 Jun 2025
A facility maintenance plan is at the core of a facility’s operations. This organized ...
19 Jun 2025
In the early days, preventive maintenance could be done effectively with a trained eye and a ...
17 Jun 2025
Sticky notes fall off, whiteboard grids get wiped, and spreadsheets never beep when a ...
13 Jun 2025
Handing a slice of your maintenance workload to a contractor is less about “giving up ...
12 Jun 2025
Downtime in enterprise environments doesn’t just mean a stop in operations; it means lost ...
10 Jun 2025
Understanding equipment functionality is crucial for effective repairs. A clear, systematic ...
6 Jun 2025
Maintenance managers know that every unplanned equipment failure is more than a simple ...
5 Jun 2025
What keeps a facility running smoothly? Initially, many of us may zoom in on its equipment, ...
29 May 2025
In today's digital world, every decision needs to pass the test of strategic and operational ...
27 May 2025
The business world is very different from a decade ago. Technological advancements have grown ...
23 May 2025
Picture this: a maintenance technician inspects a complex pump system. Instead of typing a ...
20 May 2025
For most of the 20th century, maintenance teams mainly applied a reactive approach to ...
9 May 2025
Imagine visiting a manufacturing plant where maintenance technicians gather around a large ...
8 May 2025