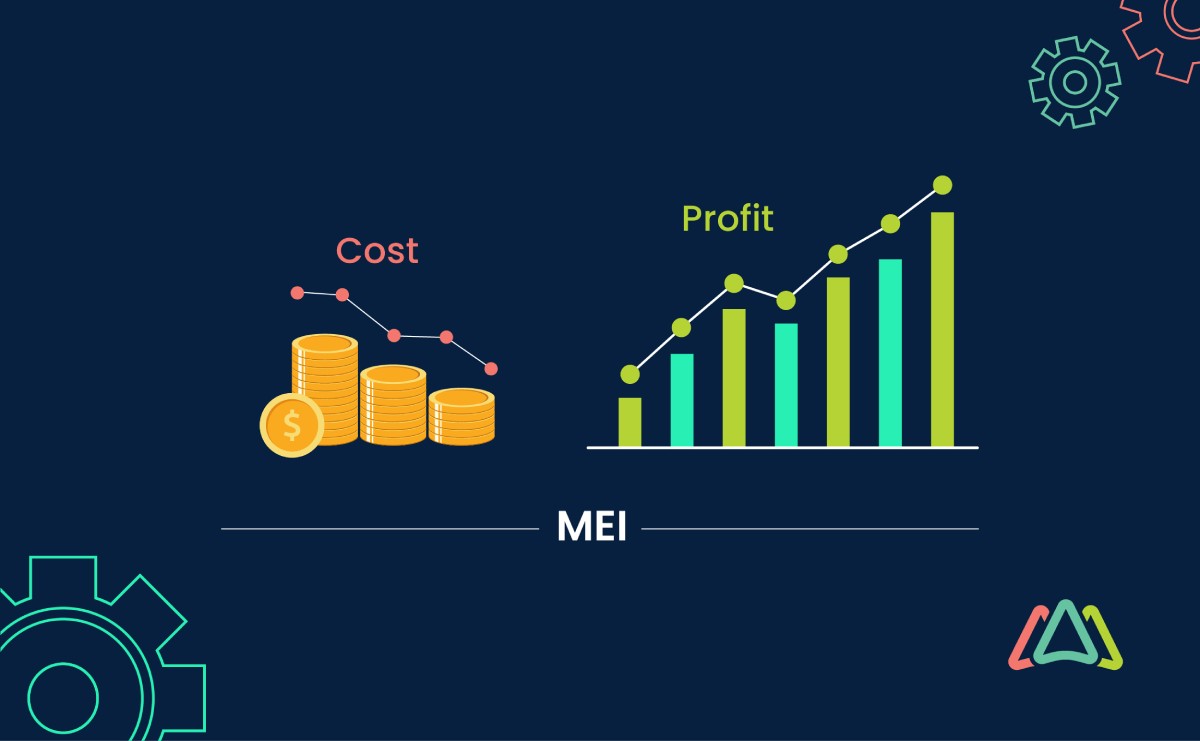
How to Use a Maintenance Excellence Index (MEI) to Reduce Costs & Increase Profits
Introduction
It goes without saying that companies across industry and business sectors are increasingly facing some very tough competition. With inflation and volatile markets, it is now more important than ever for organizations to stay on the winning side of industry competitors. This means that company owners must find new and more effective ways to reduce its costs and at the same time, increase its profits.
When thinking about ways to reduce costs and increase profits, thoughts almost always turn to having equipment that runs at optimal efficiency and with minimal downtime. Since there is no such thing as maintenance free equipment, the next best thing is to find an efficient and cost effective maintenance approach that is capable of keeping their company assets in top running condition.
In recent years, routine and effective maintenance of company assets has come to be regarded as a means to add value. Company owners have come to appreciate that through proper maintenance, equipment functions better, lasts longer and at the same time, production increases. For company owners and maintenance managers wanting to get the most from their assets, reduce costs and in turn, increase profits, there is an approach and a tool that is designed to assist in this effort.
Maintenance Excellence
To provide some background, let’s begin with an explanation of the approach. Maintenance Excellence refers to the way an organization makes use of all of its resources to maintain assets at a performance level that provides value for its customer. According to a review paper written by Jardine and Campbell (2001), there are three major objectives in achieving Maintenance Excellence: strategic, tactical and continuous improvement.
What is the Maintenance Excellence Index (MEI)?
The Maintenance Excellence Index (MEI) was first conceptualized in 2015 at the Dublin Institute of Technology with the above noted objectives in mind. Over recent years, the MEI has undergone a number of changes and refinements. In its current form, the MEI is a performance measurement tool used to assess the effectiveness and efficiency of maintenance practices within an organization. It is commonly used in industrial and manufacturing sectors to evaluate the overall maintenance management approach and identify areas in need of improvement.
Since no two operations are alike, the MEI metrics and calculation methodologies may vary depending on the industry, organization, or consulting frameworks used. As such, a MEI can be adapted to the nuances and specifics of a particular organization. Speaking generally, the MEI provides a comprehensive evaluation of maintenance activities, encompassing various factors, for example: equipment reliability, maintenance costs, maintenance planning and scheduling, inventory management, and workforce productivity. These factors are known as key performance indicators and by measuring them, the MEI helps organizations gauge the efficiency of their maintenance strategy. It can also identify potential bottlenecks or areas where optimizations can be made.
More specifically, the index typically consists of a set of key performance metrics and benchmarks that are used to assess the organization's maintenance practices against industry standards or best practices. Metrics most often used include: equipment uptime, mean time between failures (MTBF), mean time to repair (MTTR), maintenance costs as a percentage of asset value, and planned versus unplanned maintenance ratio. Again, the type of metrics used, largely depends on the industry type, size and product of an organization.
By tracking the index over time, organizations can accurately monitor the effectiveness of their current management strategy and measure progress toward reaching maintenance excellence. The ultimate goal is to optimize maintenance practices, reduce downtime, minimize costs, and improve overall operational efficiency.
How to Reduce Costs and Increase Profits with MEI?
By implementing and utilizing an MEI, companies can identify areas for improvement, optimize maintenance activities, and experience operational cost savings. The following are some suggested steps to take to leverage the MEI to reduce costs and increase profits:
1. Define Key Performance Indicators (KPIs)
Start by identifying the KPIs that are most relevant to your organization's maintenance operations. These KPIs can include metrics such as maintenance costs, equipment uptime, mean time between failures (MTBF), mean time to repair (MTTR), and overall equipment effectiveness (OEE). These indicators will serve as the basis or parameters for your MEI.
2. Establish Baseline Measurements
Collect historical data on your chosen KPIs to establish baseline measurements. This will provide a more accurate starting point for comparison and will help you identify areas with the most potential for improvement. It’s essential that the data are accurate and comprehensive to get the most accurate assessment of your current maintenance performance.
3. Develop a Scoring System
Create a scoring system that gives a weight to each KPI based on its importance to your organization's maintenance objectives. Assign higher weights to KPIs that directly impact your company’s cost reduction and profit enhancement. This can vary from one company to another. For example, if reducing equipment downtime is a priority, assign a higher weight to the equipment uptime KPI.
4. Evaluate Current Performance
Now do this with your baseline measurements by using the same scoring system. Then, calculate an MEI score for your organization's current maintenance performance. This score will be your benchmark for future evaluations and improvement efforts. Analyze the results to identify areas where maintenance processes are less than optimal and are driving up your costs.
5. Look for Improvement Opportunities
By reviewing your evaluation, you will likely be able to identify specific improvement opportunities. Areas with lower MEI scores should be your first priority since they are the ones that have the greatest potential to impact on cost reduction and profit improvement. Some opportunities for improvement could include: optimizing preventive maintenance schedules, improving spare parts management, enhancing maintenance training programs, or implementing predictive maintenance techniques.
6. Set Targets and Action Plans
Having completed your initial evaluation and identified improvement areas, you are now in a position to define realistic targets for each KPI and develop action plans to achieve those targets. Engage maintenance teams and relevant stakeholders in the goal-setting process since their cooperation and buy-in are essential to developing effective action plans. Finally, operationally define each step of the action plans. In other words, establish specific tasks, assign responsibilities, and set timelines for implementation.
7. Monitor Progress and Continuously Improve
To keep moving toward Maintenance Excellence, it is important to continue to regularly measure and track the KPIs to monitor progress towards the set targets. Analyze the results and identify any deviations or areas that require further attention. By using the insights from the MEI, you can further refine your maintenance strategies, adjust action plans if necessary, and continuously improve your maintenance practices.
8. Share and Celebrate Success
Reaching targets or making improvements that take your organization closer to reaching them are reasons to share them with the organization. Sharing and celebrating successes goes a long way in fostering a culture of maintenance excellence. It will also encourage continued focus on maintenance excellence and motivate further improvement initiatives, as needed.
Getting the Most from MEI with a CMMS
We’ve already seen how MEI as a stand alone tool can be an effective way to assess and improve maintenance performance within an organization. If you are interested in taking things up a notch, here are ways that utilizing a CMMS can augment using a MEI alone:
1. Recognize that a CMMS is a secure cloud based and robust digital system
A CMMS is a highly sophisticated system capable of handling all aspects of your organization’s maintenance management protocol. Incorporating MEI is just one of the many functions a CMMS has in its toolbox.
2. Asset historical data is already there
An important aspect of setting up and then implementing a CMMS is inputting a wide range of information into the system. Among other things, this will include: the make, model and serial number of all assets, the age of an asset, its maintenance and performance history, and more. The scope of already accessible asset data will only add to the effectiveness of the MEI in providing an evaluation of asset costs, performance and areas to improve upon.
3. Configuring your CMMS for MEI
As noted, since asset information and history are already part of the CMMS, what is left to do is to properly configure it in order to capture the data needed for the MEI. A CMMS can be customized to track relevant KPIs for your organization. This may involve creating new fields, configuring reports, or integrating with other systems or sensors to collect data. The CMMS can also be configured to provide summary data (information gathered across time) graphically in its reports.
4. Collect and analyze data
The beauty of a CMMS is these tasks can be done remotely and in real time. Data can be entered on any device that has online access. This means that maintenance technicians can enter data as they are completing their work on a piece of equipment with no waiting around until the end of the day to submit a pen and paper maintenance report. Since historical data are already in the CMMS, a report that includes a MEI score can also be generated immediately.
5. Monitor and refine
Once again, CMMSs make these processes easy to do. Once a review of the MEI reports has been done, areas of improvement can be considered. Earlier it was suggested that improvements may take the form of optimized preventive maintenance schedules, improved spare parts management, enhanced maintenance training programs, or implementation of predictive maintenance techniques. A CMMS has all of these capabilities; so there is no need to spend time “reinventing the wheel”.
6. Time is money
Compared to using a MEI as a stand alone tool, CMMS has speed in its favor. The reason why company owners take the steps needed to conduct a MEI is to find out where they stand when it comes to unnecessary costs resulting in lower profits. Imagine the added costs and lost profits involved in conducting a MEI over a period of months. A CMMS can do the same job in a small fraction of that time.
Conclusion
Overall, the Maintenance Excellence Index (MEI) offers companies a systematic framework to evaluate, benchmark, and improve their maintenance practices. By leveraging the MEI, companies can optimize their maintenance operations, reduce costs, enhance equipment reliability, and ultimately improve their overall operational efficiency and competitiveness.
By integrating a Maintenance Excellence Index with a CMMS, you can establish a systematic approach to assess maintenance performance, drive continuous improvement, and optimize the effectiveness of your maintenance operations in a timely manner. The CMMS offers the ability to utilize its own capabilities to quickly and precisely seize upon opportunities for improvement and move companies forward to achieving their goal of Management Excellence.
TABLE OF CONTENTS
Keep Reading
Ever find yourself checking into a luxury hotel and expecting a relaxing stay, only to find a ...
11 Apr 2025
Organizations are witnessing swift changes in the business environment and confronting a ...
8 Apr 2025
Last month, news outlets and the entire internet was abuzz with the return of NASA astronauts ...
3 Apr 2025
What comes first - CMMS or predictive maintenance? If your answer is either, it is correct. ...
28 Mar 2025
Artificial intelligence (AI) talk has become commonplace. Today, engaging in business-focused ...
27 Mar 2025
Imagine a world where machines predict, diagnose, and fix their issues before they fail. This ...
25 Mar 2025
A facility maintenance plan is at the core of a facility’s operations. This organized ...
21 Mar 2025
Think of managing your maintenance operations like managing a championship sports team. Just ...
21 Mar 2025
The maintenance sector is battling a severe talent shortage that threatens to undermine ...
7 Mar 2025
Manufacturing maintenance is the backbone of industrial efficiency, ensuring machines run ...
5 Mar 2025
No one likes playing a guessing game when equipment breaks down. Yet, maintenance teams often ...
4 Mar 2025
The size of the preventive maintenance software market is discussed in millions of dollars, ...
4 Mar 2025
The organizational structure and corporate hierarchy vary from company to company. Large ...
28 Feb 2025
Maintenance procedures are essential for ensuring the longevity and reliability of machinery ...
21 Feb 2025
Sustainability is no longer just a buzzword; it's a critical component of corporate social ...
20 Feb 2025
A Computerized Maintenance Management System (CMMS) relies on accurate, well-organized data ...
18 Feb 2025
In an era where technology drives operational efficiency, Computerized Maintenance Management ...
14 Feb 2025
A Computerized Maintenance Management System (CMMS) is a key component of modern maintenance ...
13 Feb 2025
Introduction Maintenance management is the foundation of maintenance operations in industries ...
11 Feb 2025
Introduction A Computerized Maintenance Management System (CMMS) is software designed to help ...
7 Feb 2025