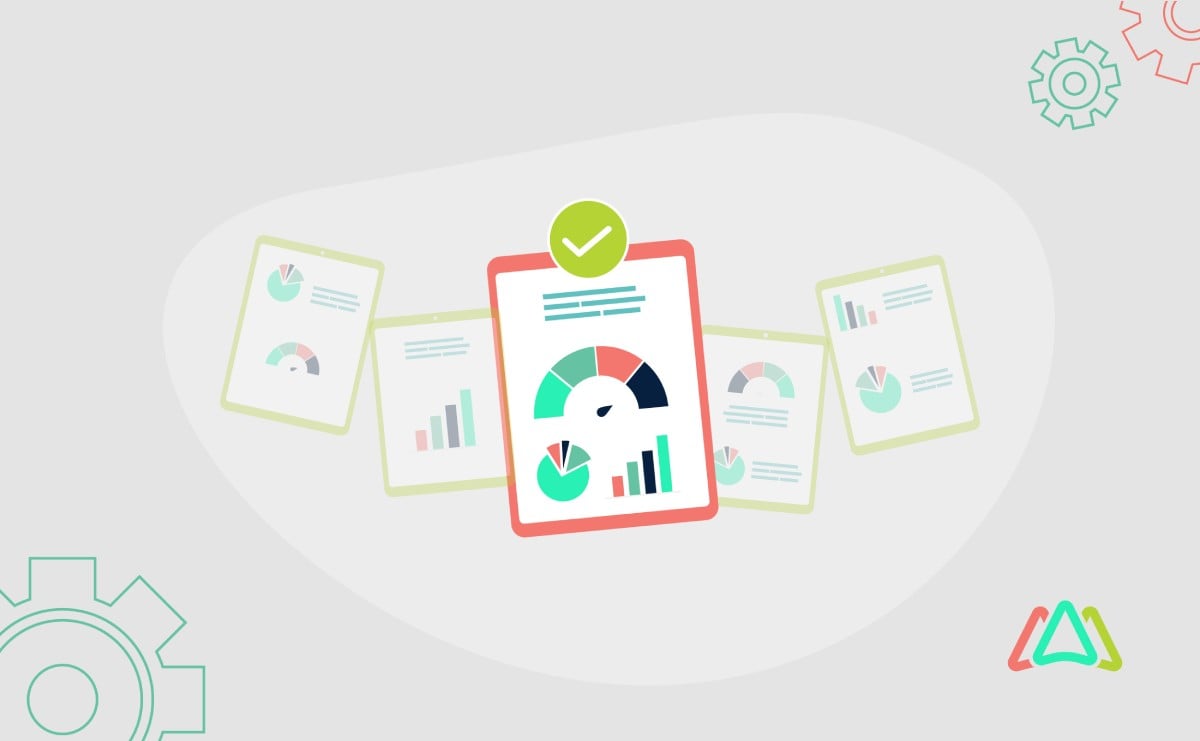
Maintenance KPIs Selection Guide to Start Your CMMS Software Implementation Journey
A Computerized Maintenance Management System (CMMS) is a software designed to streamline and improve maintenance activities. CMMS empowers businesses to proactively manage assets, work orders, and maintenance schedules, leading to improved equipment reliability, reduced downtime, and, ultimately, cost savings. To do this, CMMS serves as a centralized database, accumulating a vast amount of maintenance-related data, including asset information, work order progress, and maintenance schedules. This data is valuable but, at the same time, can be overwhelming without the right tools.
Maintenance KPIs help make sense of this vast amount of maintenance data. They are important metrics that allow maintenance managers to monitor, evaluate, and optimize their maintenance performance. KPIs provide insights into various aspects of maintenance operations, from asset reliability and cost management to safety compliance and workforce productivity. By carefully choosing and tracking these KPIs, organizations gain a comprehensive understanding of their maintenance ecosystem, identify areas for improvement, and maximize the benefits of their CMMS investment.
KPIs and Organizational Objectives
1. Identifying Organizational Objectives
Before diving into CMMS implementation, it is important to start by identifying your organization's specific goals that will determine the KPIs you select to measure. Organizations have unique priorities: minimizing downtime, reducing maintenance costs, improving asset reliability, or ensuring compliance with safety regulations.
To begin, engage with key organizational stakeholders, including members of the maintenance team and executives. Uncover and understand their pain points, expectations, and long-term objectives. By conducting thorough assessments and open discussions, you can pinpoint the objectives that matter most to your organization.
2. Aligning CMMS Implementation with Organizational Objectives
Once you've identified your organization's objectives, the next step is to align your CMMS implementation strategy with these goals. Your CMMS should not operate in isolation, it should enable achieving organizational goals. Whether optimizing asset management, streamlining work order processes, or enhancing maintenance efficiency, every aspect of your CMMS implementation should serve these overarching goals.
By aligning CMMS with organizational objectives, you ensure that your investment has a direct impact on your bottom line and strategic outcomes. This alignment creates a synergy between your technology and business strategies, allowing your CMMS to drive value and contribute to achieving your organization's mission.
3. Role of KPIs in Measuring Progress towards Objectives
Key Performance Indicators (KPIs) play a pivotal role in this process by acting as the yardsticks against which progress is measured. KPIs provide the means to track and quantify the effectiveness of your CMMS implementation efforts.
For example, if one of your objectives is to reduce maintenance costs, relevant KPIs might include "maintenance cost per unit" or "cost savings achieved through preventive maintenance." These KPIs enable you to monitor cost-related progress and make data-driven decisions to stay on course.
Essential KPI Categories to Get Started
1. Asset Management KPIs
1.1 Asset Downtime:
- Definition: The total time an asset is unavailable for production or operation due to maintenance activities or unexpected failures.
- Importance: High asset downtime can lead to production delays, increased costs, and customer dissatisfaction.
- Measurement: Track the cumulative downtime for each asset and identify trends to minimize unplanned downtime.
1.2 Mean Time Between Failure (MTBF):
- Definition: The average time elapsed between two consecutive failures of an asset.
- Importance: MTBF indicates the reliability of assets. Longer MTBF values signify more reliable equipment.
- Measurement: Calculate the MTBF by dividing the total operational time by the number of failures within that time frame.
Calculate MTBF for your use case:
Mean Time Between Failure (MTBF) Calculator
[Total Uptime (in hours) / # Number of breakdowns]
Our approach to managing work orders is radically different from other CMMS products in the market.
Learn more about the MTBF Calculator.
1.3 Mean Time to Repair (MTTR):
- Definition: The average time it takes to repair and restore a failed asset to operational status.
- Importance: MTTR reflects your organization's responsiveness to breakdowns. Lower MTTR implies quicker problem resolution.
- Measurement: Take the sum of the downtime of all repairs and divide it by the number of repairs conducted.
Calculate MTTR for your use case:
Mean Time To Repair (MTTR) Calculator
MTTR = (Total Downtime) / (Number of Repairs)
Happy with the result? If not, we could help.
Learn more about the MTTR Calculator.
These Asset Management KPIs provide insights into asset performance and reliability. By monitoring asset downtime, MTBF, and MTTR, you can proactively address maintenance needs, minimize disruptions, and optimize your maintenance processes.
2. Maintenance Performance KPIs
2.1 Work Order Completion Rate:
- Definition: Percentage of work orders completed within a specified time frame.
- Importance: This KPI measures the maintenance team's efficiency and ability to meet deadlines.
- Measurement: Calculate the ratio of completed work orders to total work orders issued.
2.2 Preventive vs. Reactive Maintenance Ratio:
- Definition: The ratio of planned preventive maintenance work orders to unplanned reactive work orders.
- Importance: This KPI indicates the degree of proactive maintenance practices.
- Measurement: Compare the number of preventive work orders to reactive ones.
2.3 Scheduled Maintenance Compliance:
- Definition: Percentage of scheduled maintenance work orders completed as planned.
- Importance: This KPI assesses the adherence to planned maintenance schedules.
- Measurement: Calculate the ratio of completed scheduled work orders to total scheduled work orders.
Calculate Scheduled Maintenance Compliance for your use case:
Schedule Compliance Calculator
[# of completed scheduled WOs on time / total scheduled WOs * 100]
Happy with the result? If not, we could help.
Learn more about the Schedule Maintenance Compliance Calculator.
3. Cost Management KPIs
3.1 Mean Maintenance Cost:
- Definition: The total maintenance expenses divided by the number of completed maintenance activities or work orders.
- Importance: Measures maintenance efficiency in terms of cost.
- Measurement: Divide total maintenance costs by the total maintenance activities or work orders completed.
Calculate the Mean Maintenance Cost for your use case:
Mean Maintenance Cost (MMC)
MMC = (Total Maintenance Costs) / (Number of Maintenance Activities)
Happy with the result? If not, we could help.
Learn more about the Mean Maintenance Cost calculator.
3.2 Maintenance Budget Adherence:
- Definition: Percentage of actual maintenance expenses compared to the allocated budget.
- Importance: This KPI evaluates how well the maintenance department manages its budget.
- Measurement: Divide actual expenses by the budgeted amount and multiply by 100.
3.3 Spare Parts Inventory Turnover Rate:
- Definition: The number of times spare parts are used and replenished within a given period.
- Importance: Indicates inventory management efficiency.
- Measurement: Divide the total value of spare parts used by the average inventory value.
4. Safety and Compliance KPIs:
4.1 Number of Safety Incidents:
- Definition: The total count of safety incidents within a specified timeframe.
- Importance: This KPI measures safety performance and helps identify potential hazards.
- Measurement: Count the number of reported safety incidents within a given period of time.
4.2 Compliance with Regulatory Standards:
- Definition: Percentage of compliance with industry or regulatory safety standards.
- Importance: Ensures adherence to legal requirements, reducing potential risks.
- Measurement: Calculate the ratio of compliant actions to total actions.
4.3 Audit Success Rate:
- Definition: Percentage of successful outcomes in safety or compliance audits.
- Importance: Demonstrates the effectiveness of safety and compliance programs.
- Measurement: Divide the number of successful audits by the total number of audits over a period of time.
5. Inventory Management KPIs
5.1 Stockout Rate:
- Definition: Frequency of parts or materials being unavailable when needed.
- Importance: High stockout rates can lead to equipment downtime and expensive rush orders.
- Measurement: Divide the number of stockouts by the total number of inventory checks.
5.2 Inventory Accuracy:
- Definition: The percentage of inventory records that match actual physical counts.
- Importance: Accurate inventory data prevents overstocking and stockouts and discourages theft.
- Measurement: Calculate the ratio of accurate items to total items in inventory.
5.3 Carrying Cost of Inventory:
- Definition: The cost of holding inventory, including storage, insurance, and depreciation.
- Importance: High carrying costs can impact the overall maintenance budget.
- Measurement: Calculate the annual cost of carrying inventory.
Check out our blog on Inventory Management KPIs to learn more.
6. Maintenance Backlog KPIs
6.1 Open Work Orders Backlog:
- Definition: The total number of open (not-completed) work orders at a specific point in time.
- Importance: Measures the backlog of maintenance tasks and helps prioritize workload.
- Measurement: Count the number of open work orders.
6.2 Backlog Aging:
- Definition: The average time work orders have been pending (open).
- Importance: Indicates the age of unresolved tasks, helping with resource allocation.
- Measurement: Calculate the average time elapsed for open work orders.
6.3 Backlog Reduction Rate:
- Definition: The rate at which the backlog is decreasing over time.
- Importance: Measures the effectiveness of backlog reduction efforts.
- Measurement: Divide the reduction in backlog by the time period.
Read our blog on Maintenance Backlogs to learn more.
7. Equipment Reliability KPIs
7.1 Overall Equipment Effectiveness (OEE):
- Definition: A comprehensive metric that assesses equipment efficiency, availability, and quality.
- Importance: Offers a holistic view of equipment performance.
- Measurement: Calculate OEE using the formula (Availability x Performance x Quality).
Calculate Overall Equipment Effectiveness (OEE) for your use case:
Overall Equipment Effectiveness Calculator
[availability * performance * quality]
Our approach to managing work orders is radically different from other CMMS products in the market.
Learn more about the Overall Equipment Effectiveness (OEE) Calculator.
7.2 Failure Rate:
- Definition: The rate at which equipment experiences failures.
- Importance: Measures equipment reliability and identifies potential issues.
- Measurement: Count the number of equipment failures in a given period.
Calculate the Failure Rate for your use case:
Failure Rate (λ)
Failure Rate (λ) = (Number of Failures) / (Total Operating Time)
Happy with the result? If not, we could help.
Learn more about the Failure Rate Calculator.
7.3 Asset Utilization Rate:
- Definition: The percentage of time an asset is actively used for its intended purpose.
- Importance: Helps identify underutilized assets and optimize resource allocation.
- Measurement: Divide actual asset usage time by potential usage time.
Read our blog on Equipment Reliability to learn more.
8. Technician Productivity KPIs
8.1 Technician Wrench Time:
- Definition: The actual time technicians spend on maintenance tasks.
- Importance: Measures technician efficiency and identifies potential bottlenecks.
- Measurement: Calculate the total time spent on maintenance tasks and divide it by the total hours worked.
Calculate Technician Wrench Time for your use case:
Wrench Time
Wrench Time = (Total Time Spent on Direct Maintenance) / (Total Work Hours)
Our approach to managing work orders is radically different from other CMMS products in the market.
Learn more about the Wrench Time Calculator.
8.2 Labor Utilization Rate:
- Definition: The percentage of available labor hours that are used productively.
- Importance: Indicates the efficiency of labor resource allocation.
- Measurement: Divide productive labor hours by total available hours.
8.3 Overtime Hours Due to Maintenance:
- Definition: The number of overtime hours worked by maintenance personnel.
- Importance: Measures the impact of maintenance workload on labor costs.
- Measurement: Sum the total overtime hours attributed to maintenance.
9. Energy Efficiency KPIs
9.1 Energy Consumption per Unit of Production:
- Definition: The amount of energy consumed per unit of product or service.
- Importance: Measures energy efficiency and its impact on operational costs.
- Measurement: Divide total energy consumption by units produced or serviced.
9.2 Energy Cost per Asset:
- Definition: The energy cost consumed by a specific asset or group of assets.
- Importance: Helps identify energy-intensive assets and opportunities for potential savings.
- Measurement: Calculate the cost of energy for each asset or asset group.
9.3 Reduction in Energy Usage through Maintenance Initiatives:
- Definition: The reduction in energy consumption achieved through maintenance-related actions.
- Importance: Indicates the effectiveness of energy-saving initiatives.
- Measurement: Compare current energy consumption to the baseline.
10. Work Order Priority KPIs
10.1 Percentage of Critical Work Orders Completed on Time:
- Definition: The percentage of critical work orders that are completed within the specified timeframe.
- Importance: Ensures that critical maintenance tasks are addressed promptly.
- Measurement: Divide critical work orders completed on time by the total critical work orders.
10.2 Percentage of Low-priority Work Orders Completed on Time:
- Definition: The percentage of low-priority work orders that are completed within the specified timeframe.
- Importance: Measures the efficiency of low-priority task management.
- Measurement: Divide low-priority work orders completed on time by the total low-priority work orders.
10.3 Average Response Time to Emergency Work Orders:
- Definition: The average time it takes to respond to emergency work orders.
- Importance: Measures the speed of response to critical maintenance needs.
- Measurement: Calculate the average response time for emergency work orders.
REVOLUTIONIZE THE WAY YOU MANAGE WORK ORDERS
Selecting KPIs Based on Your Industry and Organization's Objectives
Selecting the right Key Performance Indicators (KPIs) is not a one-size-fits-all endeavor. To realize the full potential of your CMMS, it's essential to align your choice of KPIs with your industry's unique characteristics and your organization's specific objectives. Here's how to tailor your KPI selection:
1. Understand Your Industry
- Industry Best Practices: Research industry-specific best practices and benchmarks. Different sectors, such as manufacturing, healthcare, or hospitality, may have distinct maintenance priorities.
- Compliance Requirements: Consider any industry-specific regulations and compliance standards. Compliance KPIs may be critical in ensuring adherence to these standards.
- Competitive Landscape: Analyze what KPIs your competitors or industry leaders are using. These can provide valuable insights into what metrics are essential for success.
KPI examples by industry:
Industry |
Key Performance Indicators (KPIs) |
---|---|
Manufacturing |
1. Overall Equipment Effectiveness (OEE) |
2. Downtime due to Maintenance |
|
3. Inventory Turnover Rate |
|
Healthcare |
1. Equipment Uptime |
2. Compliance with Regulatory Standards |
|
3. Patient or Staff Safety Incidents |
|
Hospitality |
1. Guest Room Availability |
2. Response Time to Guest Requests |
|
3. Energy Consumption per Occupied Room |
|
Information Technology |
1. System Uptime |
2. Mean Time to Repair (MTTR) |
|
3. Percentage of Service Level Agreement (SLA) Compliance |
|
Energy |
1. Energy Consumption per Unit of Production |
2. Energy Cost as a Percentage of Revenue |
|
3. Reduction in Energy Usage through Efficiency Projects |
|
Aviation |
1. Aircraft On-Time Performance |
2. Aircraft Turnaround Time |
|
3. Maintenance Cost per Flight Hour |
|
Construction |
1. Project Completion Time |
2. Safety Incidents on Construction Sites |
|
3. Equipment Utilization Rate |
2. Identify Organizational Objectives
- Engage Stakeholders: Collaborate with key stakeholders, including maintenance teams, operations, finance, and leadership. Understand their priorities, pain points, and desired outcomes.
- Strategic Goals: Align your KPI selection with your organization's strategic goals. For example, if your goal is to reduce costs, focus on cost management KPIs.
- SMART Objectives: Best practice is ensuring objectives are Specific, Measurable, Achievable, Relevant, and Time-bound (SMART). This clarity helps in KPI selection.
Organizational Objectives |
Key Performance Indicators (KPIs) |
---|---|
Cost Reduction |
1. Maintenance Cost per Unit |
2. Maintenance Budget Adherence |
|
3. Inventory Turnover Rate |
|
Improved Equipment Reliability |
1. Mean Time Between Failures (MTBF) |
2. Mean Time to Repair (MTTR) |
|
3. Overall Equipment Effectiveness (OEE) |
|
Safety and Compliance |
1. Number of Safety Incidents |
2. Compliance with Regulatory Standards |
|
3. Audit Success Rate |
|
Operational Efficiency |
1. Work Order Completion Rate |
2. Preventive vs. Reactive Maintenance Ratio |
|
3. Scheduled Maintenance Compliance |
|
Improved Energy Efficiency |
1. Energy Consumption per Unit of Production |
2. Energy Cost per Asset |
|
3. Reduction in Energy Usage through Maintenance Initiatives |
|
Enhanced Customer Satisfaction |
1. Response Time to Service Requests |
2. Asset Availability (for industries like hospitality) |
|
3. Guest Satisfaction Scores (for the hospitality industry) |
|
Environmental Sustainability |
1. Carbon Emissions Reduction |
2. Reduction in Hazardous Waste Generation |
|
3. Water and Energy Conservation |
3. Prioritize KPIs
- Critical vs. Supporting KPIs: Distinguish between critical KPIs that directly impact your main objectives and supporting KPIs that provide context or secondary insights.
- Balance Metrics: Maintain a balance between leading (predictive) and lagging (historical) indicators. Leading KPIs help in proactive decision-making.
Examples of SMART Objectives and Corresponding Primary and Secondary KPIs for Effective Performance Measurement:
SMART Objective |
Primary KPIs |
Secondary KPIs |
---|---|---|
Reduce Maintenance Costs by 15% within the next fiscal year. |
1. Maintenance Cost per Unit |
1. Maintenance Budget Adherence |
2. Spare Parts Inventory Turnover Rate |
2. Percentage of Preventive Maintenance Completed |
|
3. Overtime Hours due to Maintenance |
3. Work Order Completion Rate |
|
Improve Equipment Reliability with a target MTBF of 500 hours. |
1. Mean Time Between Failures (MTBF) |
1. Mean Time to Repair (MTTR) |
2. Overall Equipment Effectiveness (OEE) |
2. Failure Rate |
|
3. Scheduled Maintenance Compliance |
||
Enhance Safety and Compliance - Achieve zero reportable safety incidents this calendar year. |
1. Number of Safety Incidents |
1. Compliance with Regulatory Standards |
2. Audit Success Rate |
2. Percentage of Safety Training Completion |
|
Increase Energy Efficiency by 10% by the end of the year. |
1. Energy Consumption per Unit of Production |
1. Energy Cost per Asset |
2. Reduction in Energy Usage through Maintenance Initiatives |
2. Renewable Energy Usage |
|
3. Carbon Emissions Reduction |
||
Achieve a 95% Work Order Completion Rate for all work orders within 48 hours of request. |
1. Work Order Completion Rate |
1. Percentage of Preventive Maintenance Completed |
2. Percentage of Critical Work Orders Completed on Time |
2. Percentage of Emergency Work Orders Completed on Time |
|
3. Average Response Time to Work Orders |
3. Backlog Reduction Rate |
|
Improve Customer Satisfaction by maintaining a consistent score of 4.5 or higher in quarterly surveys. |
1. Customer Satisfaction Scores |
1. Response Time to Service Requests |
2. Asset Availability (for industries like hospitality) |
2. Number of Customer Complaints |
|
Reduce Carbon Emissions by 20% by the end of the fiscal year. |
1. Carbon Emissions Reduction |
1. Reduction in Hazardous Waste Generation |
2. Water and Energy Conservation |
2. Use of Sustainable Materials |
These tables provide a starting point for organizations to identify relevant KPIs based on industry and specific objectives.
4. Consider the CMMS Software Features
- Leverage CMMS Capabilities: Explore the capabilities of your CMMS software. Some systems may offer pre-built dashboards and reports tailored to specific KPIs.
- Customization: Determine if your CMMS allows you to customize dashboards and reports to track your chosen KPIs effectively.
5. Regularly Review and Adjust
- Dynamic Nature: Recognize that KPIs may evolve over time as your organization's objectives change or as new industry trends emerge.
- Regular Assessment: Schedule periodic reviews to ensure that your selected KPIs remain relevant and continue to drive your maintenance strategy.
6. Benchmark Performance
- Compare Performance: Benchmark your KPIs against industry standards or similar organizations. This provides context for your performance.
- Continuous Improvement: Use benchmarking data to identify areas for improvement and implement best practices from top performers.
7. Training and Communication
- Educate Teams: Ensure that your maintenance teams and relevant stakeholders understand the chosen KPIs, their significance, and how they contribute to organizational objectives.
- Open Communication: Encourage open communication and feedback regarding KPIs. Teams on the ground often have valuable insights into what metrics matter most.
Setting SMART KPIs
Understanding the SMART Criteria (Specific, Measurable, Achievable, Relevant, Time-Bound)
When it comes to selecting Key Performance Indicators (KPIs) for your CMMS, adhering to the SMART criteria pays off. SMART stands for Specific, Measurable, Achievable, Relevant, and Time-bound, and it provides a structured framework for setting meaningful and effective KPIs.
- Specific: Your KPIs should be clear and precise, leaving no room for ambiguity. They should address a particular aspect of your maintenance objectives. For example, rather than setting a vague KPI like "improve maintenance efficiency," you can make it specific by stating, "reduce mean time to repair (MTTR) by 20%."
- Measurable: To gauge progress and success, KPIs must be quantifiable. You should be able to track and measure the KPI using objective data. In the case of CMMS, this could mean tracking metrics like "work order completion rate" or "equipment downtime hours."
- Achievable: KPIs should be realistic and attainable within the given resources and constraints. While ambitious goals can be motivating, setting unrealistic KPIs can lead to frustration and decreased morale. Ensure that your team has the means and support to achieve the KPIs you set.
- Relevant: KPIs should align with your organization's goals and objectives. They should directly contribute to your overarching strategy. Ensure your selected KPIs are relevant to your industry, department, and overall mission. For instance, if cost reduction is a primary objective, relevant KPIs might focus on maintenance cost per unit or inventory turnover rate.
- Time-bound: Set specific timeframes or deadlines for achieving your KPIs. Having a clear timeframe creates a sense of urgency and accountability. For example, instead of saying "reduce downtime," specify "reduce asset downtime by 15% within the next fiscal year."
Examples of SMART KPIs for CMMS Implementation
Specific |
Measurable |
Achievable |
Relevant |
Time-Bound |
|
---|---|---|---|---|---|
Goal 1 |
Improve asset reliability through preventive maintenance. |
Increase mean time between failures (MTBF) from 100 hours to 150 hours. |
Allocate additional resources for preventive maintenance and training. |
Aligns with the goal of reducing unplanned downtime and enhancing equipment performance. |
Achieve this increase in MTBF within the next six months. |
Goal 2 |
Enhance work order completion efficiency. |
Increase work order completion rate from 75% to 90%. |
Implement CMMS software to streamline work order processes |
Supports the objective of improving operational efficiency. |
Achieve a higher completion rate within the next quarter. |
Goal 3 |
Optimize spare parts inventory management. |
Reduce spare parts stockout rate from 20% to 5%. |
Implement inventory tracking features in the CMMS. |
Contributes to cost reduction by minimizing emergency orders. |
Achieve the reduced stockout rate within the next fiscal year. |
Importance of Periodic Review and Adjustments
Setting SMART KPIs is not a one-time task; it's an ongoing process. Periodic review and adjustments ensure KPIs remain relevant and aligned with changing organizational priorities and external factors.
Regularly reviewing KPIs allows you to:
- Assess Progress: Measure your actual performance against the defined KPIs to gauge progress toward your goals.
- Identify Issues: Identify any bottlenecks, challenges, or unexpected developments that may require adjustments to your KPIs.
- Stay Aligned: Ensure that KPIs continue to align with your organization's evolving strategies and objectives.
- Motivate and Focus: Celebrate successes, use KPIs to motivate teams, and keep everyone focused on shared goals.
- Adapt to Change: Be prepared to adjust KPIs in response to changes in market conditions, technology, or customer demands.
Using CMMS to Track and Manage KPIs
1. Utilizing Reports and Analytics Feature within the CMMS
Most CMMS systems offer robust reporting and analytics capabilities. Leveraging these tools instead of spreadsheets makes data analysis easier, faster, and more effective.
- Pre-Built Reports: Many CMMS solutions provide pre-built reports tailored to common maintenance KPIs. These reports offer a quick overview of key metrics.
- Custom Reports: Customize reports to align with your specific KPIs and objectives. Tailor the data presentation to your organization's needs.
- Dashboards: CMMS dashboards offer real-time visibility into KPI trends and performance. They provide an at-a-glance view of your maintenance operations.
- Predictive Analytics: Some CMMS systems incorporate predictive analytics, allowing you to forecast equipment failures and plan maintenance proactively.
2. Monitoring KPI Trends and Deviations
Monitoring KPI trends and identifying deviations from targets is an ongoing process. Here's how to approach it:
- Regular Review: Establish a regular review schedule for KPIs. Depending on your objectives, this could be daily, weekly, monthly, or quarterly.
- Benchmarking: Compare your KPIs against industry benchmarks or best practices. Benchmarking provides context for your performance.
- Alerts and Notifications: Set up alerts within your CMMS to notify you when KPIs deviate significantly from targets. This allows for immediate action.
- Root Cause Analysis: When deviations occur, analyze the root cause to understand why they happened. Use your CMMS data to identify contributing factors.
- Continuous Improvement: KPI analysis should drive continuous improvement efforts. Use insights gained to make process enhancements, allocate resources more effectively, and refine maintenance strategies.
Implementing Corrective Actions Based on KPI Insights
Continuous improvement is at the core of effective maintenance management. Your Key Performance Indicators (KPIs) provide valuable insights into areas that require corrective actions. Here's how to implement improvements based on KPI insights:
- Data-Driven Decisions: Rely on KPI data to make informed decisions. Identify which aspects of your maintenance operations need attention based on performance trends and variations.
- Actionable Insights: Translate KPI insights into actionable steps. Develop plans and strategies that directly address the root causes of underperformance or deviations from targets.
- Cross-functional Collaboration: Collaborate across departments and involve relevant stakeholders to implement corrective actions effectively. Maintenance teams, operations, finance, and leadership should work together toward common improvement goals.
- Regular Follow-up: Continuously monitor the results of corrective actions. Evaluate whether the implemented changes are having the desired impact on your KPIs.
The synergy between a well-implemented Computerized Maintenance Management System (CMMS) and carefully selected Key Performance Indicators (KPIs) can revolutionize your maintenance operations. Embracing the SMART criteria for KPIs ensures that your goals are Specific, Measurable, Achievable, Relevant, and Time-bound, guiding you toward data-driven success. Accurate and consistent data, harnessed through CMMS reports and analytics, forms the bedrock of effective decision-making.
Moreover, benchmarking against industry standards offers invaluable insights into where improvements can be made and the heights you can reach. By committing to continuous improvement and engaging all stakeholders, you embark on a journey that not only optimizes maintenance but also elevates your organization's overall efficiency, reliability, and cost-effectiveness. In this dynamic landscape, your CMMS and KPIs are your compass, guiding you toward a future of enhanced value and success in maintenance management.
TABLE OF CONTENTS
Keep Reading
Ever find yourself checking into a luxury hotel and expecting a relaxing stay, only to find a ...
11 Apr 2025
Organizations are witnessing swift changes in the business environment and confronting a ...
8 Apr 2025
Last month, news outlets and the entire internet was abuzz with the return of NASA astronauts ...
3 Apr 2025
What comes first - CMMS or predictive maintenance? If your answer is either, it is correct. ...
28 Mar 2025
Artificial intelligence (AI) talk has become commonplace. Today, engaging in business-focused ...
27 Mar 2025
Imagine a world where machines predict, diagnose, and fix their issues before they fail. This ...
25 Mar 2025
A facility maintenance plan is at the core of a facility’s operations. This organized ...
21 Mar 2025
Think of managing your maintenance operations like managing a championship sports team. Just ...
21 Mar 2025
The maintenance sector is battling a severe talent shortage that threatens to undermine ...
7 Mar 2025
Manufacturing maintenance is the backbone of industrial efficiency, ensuring machines run ...
5 Mar 2025
No one likes playing a guessing game when equipment breaks down. Yet, maintenance teams often ...
4 Mar 2025
The size of the preventive maintenance software market is discussed in millions of dollars, ...
4 Mar 2025
The organizational structure and corporate hierarchy vary from company to company. Large ...
28 Feb 2025
Maintenance procedures are essential for ensuring the longevity and reliability of machinery ...
21 Feb 2025
Sustainability is no longer just a buzzword; it's a critical component of corporate social ...
20 Feb 2025
A Computerized Maintenance Management System (CMMS) relies on accurate, well-organized data ...
18 Feb 2025
In an era where technology drives operational efficiency, Computerized Maintenance Management ...
14 Feb 2025
A Computerized Maintenance Management System (CMMS) is a key component of modern maintenance ...
13 Feb 2025
Introduction Maintenance management is the foundation of maintenance operations in industries ...
11 Feb 2025
Introduction A Computerized Maintenance Management System (CMMS) is software designed to help ...
7 Feb 2025