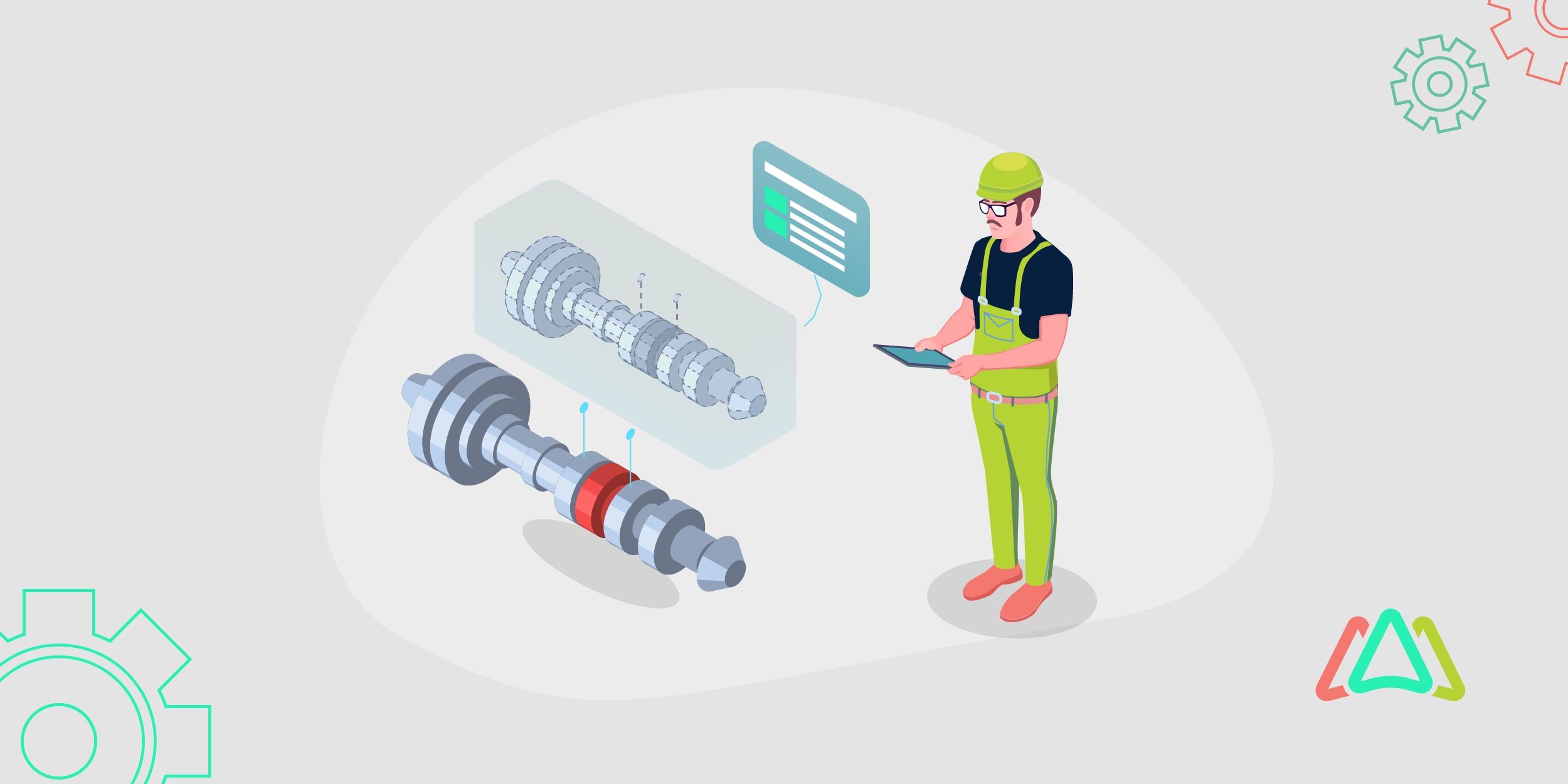
What Do Space Exploration and Maintenance Management Have in Common? The Answer Lies in Digital Twins.
Last month, news outlets and the entire internet was abuzz with the return of NASA astronauts Sunita Williams and Barry "Butch" Wilmore. Their planned one-week stay at the International Space Station (ISS) was extended to an unexpected 286 days. Through the media, we all saw the world celebrate their safe return. The astronauts' health was monitored, and support was provided, potentially using their digital twins or avatars.
The concept of digital twins gained significant traction within NASA following the Apollo 13 incident. To address the anomaly, NASA employed simulators and vehicle modeling to analyze the cause and formulate real-time solutions. This marked a pivotal moment, establishing the use of digital twins as an integral part of NASA's operations, building upon their extensive history of innovation in this field.
In 2010, decades after the Apollo 13 accident, John Vickers, at NASA's Marshall Space Flight Center, coined the term digital twins. Originating during NASA's Apollo missions, digital twins now drive advancements in personalized medicine and autonomous operations in space by simulating and forecasting future behaviors based on existing data. Tesla cars are a notable example of digital twins in action.
Digital twins are real-time virtual/digital replicas of physical objects, systems, and processes. They are increasingly prevalent in various sectors, including healthcare, manufacturing, automotive, oil & gas, transportation, and aerospace. As complexity grows globally, digital twins assist in making better-informed decisions, reducing risk, and delivering life-saving benefits when combined with scientific computing, artificial intelligence, and sensor technology.
This transformative technology is revolutionizing life on Earth, enhancing our ability to anticipate and address complex problems. It's improving our understanding of Earth, aiding in predicting natural disasters, and showing promise in improving diagnosis, treatment, and monitoring of conditions such as heart disease and diabetes. The increasing adoption of digital twins across industries and businesses, accelerated by the AI revolution, is a testament to the promising future this technology holds.
Digital twins are having a huge impact on the manufacturing sector, specifically with maintenance functions. This article delves into the growing presence of digital twins in these areas. It assesses how these functions have been able to build on the digital twin bedrock provided by space research.
Understanding Digital Twin Technology
In simplistic terms, digital twin technology is a virtual representation of a physical object—a machine, product, vehicle, or process. Data is collected from the physical object and continuously fed into the twin. Digital twins run several simulations to eventually predict future outcomes—for example, an asset’s lifespan- thus enabling predictive maintenance. A digital twin also adds efficiency to product development.
Digital twins are used in a variety of industries. In manufacturing, they are used to visualize machine tools and create virtual manufacturing cells. In the automotive industry, they are used to monitor and optimize individual cars or entire fleets. In the energy sector, digital twins are used to simulate the performance of power plants. The key feature of a digital twin is the two-way flow of information between the physical object and the virtual model, which is continuously updated with real-life data. This allows the digital twin to simulate the physical object's behavior, and this information can be used to modify the physical system. This digital twin helps optimize research and development (R&D), design, and manufacturing processes.
Types of Digital Twins
Digital twins can be categorized based on how they are applied in the context of the problem. Broadly, there are two approaches:
- Strategic
- Transactional (discrete digital twin)
Strategic Digital Twins
According to Gartner, there are three types of digital twins:
Organization Digital Twin: You need an organization digital twin to see how a business strategy responds in real time. It leverages operational data to analyze an organization's business model, make changes, and deliver customer value.
Composite Digital Twin: Designed for large industrial ecosystems, this twin integrates data from other digital twins within the system, such as production planning and execution twins.
Discrete Digital Twin: This twin relies heavily on IoT-generated data to monitor and optimize individual resources—personnel, specific products, or equipment—for example, enterprise asset management digital twins. Digital twins deployed in field services are also included.
Transactional (Discrete) Digital Twins
Transactional or discrete digital twins can be broken down into the following types:
- Component Twins: These digital replicas represent virtually individual parts within a system, such as an engine's components, offering detailed insights into their functionality.
- Asset Twins: Think of these as digital doubles. These twins serve as digital counterparts of two or more pieces of equipment within a system, enabling the analysis of their interactions and collaborative performance. They could also be just a single unit.
- System Twins: Representing the system and its components, these twins provide valuable data on performance and workflows, supporting managerial, operational, investment, and strategic decisions. Essentially, these digital twins represent how the entire unit is working.
- Process Twins: Taking a broader approach, these twins digitally replicate the environment where assets and systems operate while offering behavioral insights into asset components. They provide comprehensive information on operations and interactions across all system elements and are ideal for modeling large-scale systems like plants or complex facilities. Process twins offer a higher degree of captured digital data compared to system twins.
Key Components of Digital Twins
Digital twins have advanced due to technology progression and the widespread adoption of digital transformation and AI in business. As digital twins become more sophisticated, their applications expand to address global challenges. The current digital twin stack includes:
- IoT Sensors: Also includes Industrial Internet of Things (IIOT)
- Software: ERP, CRM, CMMS, Cybersecurity
- Data Analytics: Tools and platforms that analyze data to generate insights and drive decisions.
- AI and Machine Learning: Supports predictive analytics, predictive maintenance, autonomous decision-making, and machine intelligence
- Simulation Models: Performs scenario and sensitivity analysis to test outcomes.
Benefits of Digital Twins
From a strategic perspective, the benefits of digital twins positively impact modern-day business in the following areas. There could be more areas, and this list is not exhaustive but brief.
Simulations
Digital twin technology enables virtual testing and refinement of processes and designs to achieve desired outcomes without impacting physical assets. Certain advanced digital twins facilitate concurrent simulations, allowing engineers to analyze diverse scenarios and potential consequences. This capability optimizes product design and manufacturing while preventing operational disruptions and delays..
Time-to-Market
Digital twins play a pivotal role in expediting time-to-market by validating product designs before they are physically created and by pinpointing process failures ahead of manufacturing. This approach helps mitigate risks, accelerate product development, and enhance production workflows. Digital twins enable real-time monitoring and quality control during manufacturing by comparing virtual models to design specifications and quality standards. This early detection of defects ensures consistent product quality while minimizing rework, defects, and recalls, ultimately optimizing the production process.
Supply Chain Optimization
Digital twins optimize supply chains by providing visibility and connectivity at all stages, from raw materials to finished products. By integrating data from suppliers, manufacturers, and customers, digital twins enable the end-to-end optimization of supply chains, improving inventory management, production planning, logistics, lead times, responsiveness, and collaboration. Examples of digital twin technology optimizing supply chains could be seen during the COVID-19 pandemic and the Russia- Ukraine conflict.
Digital Twins’ Impact on Maintenance Management
The value of digital twins in enabling routine maintenance tasks is evident. However, it remains to be seen how they could shape maintenance strategies in the future. The following maintenance strategies look to make the most of them.
Predictive Maintenance with Digital Twins
Predictive maintenance exemplifies the digitalization of maintenance as a discipline. It involves employing networks or sensors to capture information about a machine. Utilizing AI and machine learning to assess anomalies that indicate potential component failures or complete breakdowns allows engineers to intervene before issues worsen.
Digital twins enable predictive maintenance by creating digital replicas of physical assets and continuously gathering real-time data from embedded sensors. This predictive capability helps schedule maintenance tasks more efficiently, minimizing costs and maximizing effectiveness. Maintenance interventions are only performed when needed rather than adhering to a fixed schedule, reducing unnecessary disruptions and labor costs. This technology shifts traditional scheduled maintenance to condition-based maintenance. Digital twins also allow the collection of historical maintenance data, allowing organizations to refine predictive models and improve overall maintenance strategies.
Remote Monitoring
Another advantage of digital twins is remote asset monitoring. Maintenance teams can remotely monitor asset performance and diagnose issues without physical inspections, which proved beneficial during the COVID-19 pandemic. Digital twin technology creates virtual replicas of assets, continuously collecting and transmitting real-time data through sensors and industrial Internet of Things devices. This data provides a comprehensive view of an asset's performance, allowing teams to monitor it globally.
Remote monitoring enables larger enterprises to consider and implement strategies for offshoring their maintenance services. Maintenance teams can analyze real-time data, compare it with benchmarks, identify potential problems, and simulate solutions without being on-site.
Asset Performance Management
Digital twin solutions also optimize asset performance by analyzing data from the original asset. Teams can simulate different scenarios, tweak parameters, and test changes in a virtual environment before implementation. Real-time data collection provides insights into asset inefficiencies, enabling informed decisions.
Advanced algorithms applied to this data optimize asset performance by continuously adjusting operations based on changing conditions. Digital twins predict maintenance needs and performance trends, allowing proactive addressing of potential issues before they impact operations.
This technology facilitates a continuous adaptive iterative cycle by constantly analyzing performance data. It enables organizations to refine models, algorithms, and operations for higher efficiency over time. Optimized performance leads to better resource utilization, reduced waste, optimized energy consumption, improved production output, and cost savings.
Asset Lifecycle Management
Digital twin technology also streamlines asset lifecycle management by mapping the entire lifecycle from design and production to operation and maintenance. Digital twins enable multiple scenario planning conditions during the design phase, leading to more robust assets from the outset. During production, they facilitate real-time monitoring and optimization.
In the operational phase, digital twins provide value through real-time performance monitoring, predictive maintenance, and remote diagnostics, prolonging asset lifespans and ensuring optimal efficiency. The data collected contributes to informed decision-making at every lifecycle stage.
Training and Simulation
Finally, digital twins assist with training and simulation by providing virtual environments where technicians can practice troubleshooting without risking actual equipment. They also help capture maintenance knowledge without relying solely on team members who may retire or become unavailable for various reasons. This knowledge management is extremely valuable in this era of maintenance talent shortages.
Benefits of Digital Twin Technology in Maintenance
The integration of digital twins into maintenance operations offers many benefits, including enhanced decision-making capabilities, substantial cost reductions, improved operational efficiency, and a notable extension of asset lifespan. These benefits are realized through the real-time accessibility of data, the implementation of predictive maintenance strategies, the adoption of condition-based scheduling, and the continuous monitoring of wear patterns.
Real-time data access allows maintenance teams to make informed decisions based on the current state of equipment rather than relying on historical data or assumptions. This leads to more effective troubleshooting, faster response times, and a reduction in unplanned downtime. Predictive maintenance, powered by digital twin technology, enables the anticipation of equipment failures before they occur. This allows for proactive maintenance interventions, minimizing downtime and optimizing maintenance schedules.
Condition-based scheduling utilizes data from the digital twin to determine the optimal time for maintenance activities. This ensures that maintenance is performed only when needed, reducing unnecessary maintenance and time wasted. Wear pattern monitoring, facilitated by the digital twin, allows for the early detection of potential problems. This enables timely interventions, preventing equipment breakdowns and extending the lifespan of assets.
These benefits are aligned with best practices in maintenance management. By providing real-time insights, enabling predictive maintenance, supporting condition-based scheduling, and facilitating wear pattern monitoring, digital twins are not merely replicating these best practices; they are elevating them to new heights, driving a paradigm shift in maintenance management, and driving higher levels of operational efficiency and asset reliability.
TABLE OF CONTENTS
Keep Reading
Ever find yourself checking into a luxury hotel and expecting a relaxing stay, only to find a ...
11 Apr 2025
Organizations are witnessing swift changes in the business environment and confronting a ...
8 Apr 2025
What comes first - CMMS or predictive maintenance? If your answer is either, it is correct. ...
28 Mar 2025
Artificial intelligence (AI) talk has become commonplace. Today, engaging in business-focused ...
27 Mar 2025
Imagine a world where machines predict, diagnose, and fix their issues before they fail. This ...
25 Mar 2025
A facility maintenance plan is at the core of a facility’s operations. This organized ...
21 Mar 2025
Think of managing your maintenance operations like managing a championship sports team. Just ...
21 Mar 2025
The maintenance sector is battling a severe talent shortage that threatens to undermine ...
7 Mar 2025
Manufacturing maintenance is the backbone of industrial efficiency, ensuring machines run ...
5 Mar 2025
No one likes playing a guessing game when equipment breaks down. Yet, maintenance teams often ...
4 Mar 2025
The size of the preventive maintenance software market is discussed in millions of dollars, ...
4 Mar 2025
The organizational structure and corporate hierarchy vary from company to company. Large ...
28 Feb 2025
Maintenance procedures are essential for ensuring the longevity and reliability of machinery ...
21 Feb 2025
Sustainability is no longer just a buzzword; it's a critical component of corporate social ...
20 Feb 2025
A Computerized Maintenance Management System (CMMS) relies on accurate, well-organized data ...
18 Feb 2025
In an era where technology drives operational efficiency, Computerized Maintenance Management ...
14 Feb 2025
A Computerized Maintenance Management System (CMMS) is a key component of modern maintenance ...
13 Feb 2025
Introduction Maintenance management is the foundation of maintenance operations in industries ...
11 Feb 2025
Introduction A Computerized Maintenance Management System (CMMS) is software designed to help ...
7 Feb 2025
Introduction Due to a growing awareness of the need to combat climate change, the green ...
6 Feb 2025