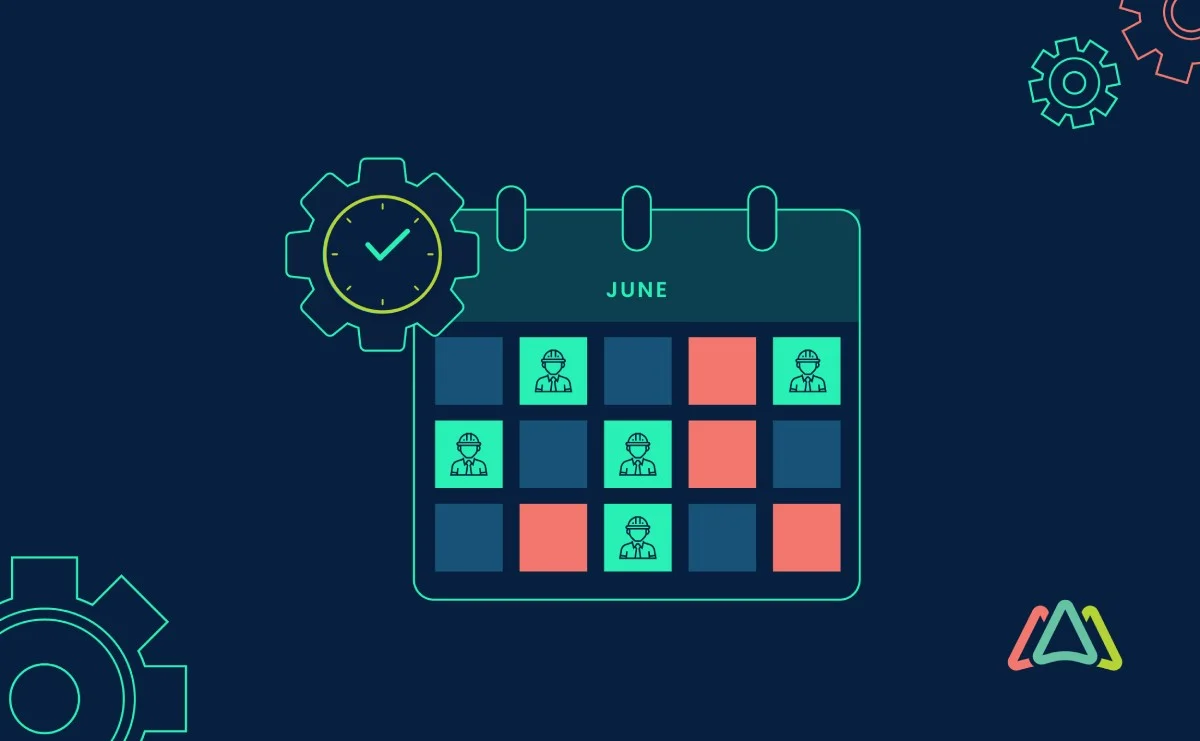
Navigating Maintenance Planning and Scheduling for Optimal Equipment Performance
When it comes to a company’s production objectives, a smoothly running operation is vital and relies on well maintained equipment and assets. However, when maintenance is not managed efficiently and effectively, operations invariably fall short of meeting their intended production targets.
Consider two scenarios: one where maintenance occurs haphazardly, leading to breakdowns, costly repairs, and halts, and another, with a systematic approach to maintenance that ensures proactive repairs and smooth operations.
While 60% of manufacturing companies worldwide still perform reactive maintenance which means responding to problems once they’ve occurred, there is now a growing trend toward preventive maintenance. 74% of Computerized Maintenance Management Software (CMMS) users believe this tool improves productivity, and 51% believe it reduces downtime.
This guide will help you transform your operations into a well-tuned performance, unveiling the power and potential of effective maintenance planning and scheduling.
What is Maintenance Planning?
Maintenance planning is a process of systematically preparing and organizing maintenance activities in a way that ensures the smooth operation of equipment and assets.
It involves assessing equipment needs, identifying maintenance tasks, determining required resources and timelines, and establishing priorities. However, maintenance planning involves other vital procedures, which are described below.
According to the 2019 Maintenance Report, aging equipment accounts for 40% of unscheduled downtime, while unexpected mechanical failure contributes to 24% of these incidents.
These statistics highlight the importance of proactive maintenance practices to mitigate the impact of aging equipment and minimize unexpected failures.
Maintenance planning optimizes maintenance activities, minimizes downtime, and enhances overall operational efficiency. By strategically planning maintenance tasks, organizations can do the following:
- Minimize equipment downtime and disruptions
- Optimize resource allocation and reduces waste
- Extend equipment lifespan and reduces the need for premature replacements
- Improve overall operational efficiency
- Enhance safety by identifying and addressing potential maintenance risks
- Reduce emergency repairs and associated costs
- Increase productivity by ensuring equipment availability when needed
- Enhance customer satisfaction through reliable and consistent operations
- Support regulatory compliance and adherence to industry standards
- Facilitate better long-term asset management and planning.
Steps in Maintenance Planning
Effective and efficient execution of maintenance activities is crucial for maintenance planning as it ensures that planned tasks are carried out promptly and accurately.
According to a report, businesses incur losses ranging from $84,000 USD to $108,000 USD for each hour of IT system downtime. This underscores the critical importance of minimizing and managing downtime effectively.
In this regard, proper maintenance also reduces disruptions to operations and maximizes resource utilization. By executing maintenance activities effectively and efficiently, organizations can optimize equipment performance, extend asset lifespan, and maintain high operational reliability and productivity.
Maintenance planning involves several essential steps to ensure the effective and efficient execution of maintenance activities. Here are the key steps involved in maintenance planning:
1. Equipment assessment
Equipment assessment, which is a comprehensive evaluation is conducted to assess the condition and maintenance requirements of the equipment and assets. It involves examining the physical condition, performance history, and potential risks or issues associated with the equipment. Organizations can identify maintenance needs such as preventative maintenance, repairs, and replacements by undertaking a complete and thorough assessment. The equipment assessment provides crucial insights into the equipment's overall health and maintenance requirements, serving as the foundation for effective maintenance planning and resource allocation.
2. Task identification
Task identification refers to identifying and specifying the specific maintenance tasks required for each piece of equipment or asset. This includes determining the actions needed to keep the equipment functioning optimally, such as inspections, repairs, lubrication, adjustments, or replacements. Task identification ensures that the maintenance plan includes all necessary maintenance operations. It also helps build a thorough list of maintenance tasks to ensure equipment performance, dependability, and lifetime.
3. Resource allocation
Resource allocation in maintenance planning involves identifying the resources needed for anticipated maintenance work. This includes hiring skilled workers, providing tools and equipment, buying spare parts and materials, and devoting enough time and money for upkeep. Effective resource allocation reduces delays and ensures maintenance jobs are completed smoothly. It also optimizes resource utilization and prevents maintenance delays caused by resource constraints.
4. Timeline and priority setting
Organizations need to establish a timeline for each maintenance task and prioritize them based on their urgency and importance. This involves considering factors such as equipment criticality, production schedules, and regulatory requirements. Maintenance planning ensures the most important and time-sensitive maintenance tasks are done first. This reduces the chance of equipment failure, disruptions, and expensive downtime. It also optimizes resource allocation, maximizing maintenance and operating efficiency.
5. Work order creation
Work order creation is the process of generating detailed instructions for each maintenance task to be conducted. It involves documenting the specific tasks to be performed, allocating necessary resources, estimating the time required, and including any special instructions or safety guidelines. Work orders serve as a roadmap for technicians, ensuring that they have all the information they need to execute the maintenance task accurately and efficiently. And detailed work orders streamline the maintenance process, enhance communication, and facilitate proper tracking and documentation of completed tasks.
What is Maintenance Scheduling?
Maintenance scheduling refers to the process of creating a well-structured and optimized timeline for carrying out maintenance tasks. It involves determining when and how often maintenance activities should be performed on equipment or assets based on factors such as equipment criticality, resource availability, production demands, and regulatory requirements.
Maintenance scheduling ensures timely maintenance chores to prevent equipment breakdowns, minimize operations disruptions, and maximize equipment uptime.
By strategically scheduling maintenance activities, organizations can do the following:
- Maintenance scheduling involves creating a timeline and order for executing planned maintenance tasks.
- When creating the schedule, consider equipment criticality, resource availability, production demands, and compliance requirements.
- Prioritize tasks based on urgency, importance, and impact on operations.
- Ensure coordination and communication between maintenance teams and other stakeholders.
- Use maintenance management software or tools to facilitate scheduling and tracking.
- Regularly review and adjust the schedule to accommodate changes and optimize resource allocation, as needed..
- Document and track completed maintenance tasks for future reference and analysis.
- Continuously improve scheduling processes based on data and feedback.
Steps in Maintenance Scheduling
Maintenance scheduling involves carefully arranging and coordinating maintenance activities within a specified timeframe. The process ensures that maintenance tasks are executed at the most suitable and efficient times. Here are the key steps in maintenance scheduling:
1. Task prioritization
Assess the urgency and criticality of maintenance tasks based on factors such as equipment condition, safety risks, production requirements, and regulatory compliance. Prioritize tasks accordingly to address high-priority and time-sensitive maintenance needs.
2. Resource availability
Evaluate the availability of necessary resources, including skilled personnel, equipment, spare parts, and tools. Ensure that the required resources are allocated and scheduled appropriately to carry out the maintenance tasks effectively.
3. Time allocation
Determine the optimal timing and duration for each maintenance task. Consider factors such as equipment availability, production schedules, and operational downtime windows. Schedule maintenance activities during planned shutdowns or periods of lower production demand whenever possible to minimize disruptions.
4. Schedule coordination
Coordinate with maintenance teams, operations departments, and other stakeholders to align the maintenance schedule with overall operational requirements. Communicate the schedule clearly to ensure everyone involved understands their roles and responsibilities.
5. Schedule review and adjustment
Regularly review the maintenance schedule to identify potential conflicts, resource constraints, or changes in operational priorities. Make necessary adjustments to accommodate unforeseen events or changing circumstances, ensuring that the schedule remains flexible and adaptable.
Importance of effective Maintenance Planning and Scheduling
Effective maintenance planning and scheduling are crucial in optimizing an organization's performance, reliability, and availability of assets and equipment. Here are some key reasons why effective maintenance planning and scheduling are essential:
1. Minimized downtime
Minimizing downtime is crucial as it prevents costly disruptions to production, maintains operational efficiency, and helps meet deadlines. Effective maintenance planning and scheduling help minimize unexpected breakdowns and equipment failures, reducing unplanned downtime. Companies can prevent significant issues by using proactive maintenance practices. This approach ensures that assets and equipment are properly maintained, improving their reliability and availability.
2. Improved equipment reliability
Effective maintenance planning and scheduling improve equipment reliability by proactively conducting preventive and predictive maintenance tasks. Organizations can avoid significant equipment failures and downtime by recognizing concerns early. Regular maintenance activities help extend the lifespan of assets and ensure their optimal performance. This approach reduces the risk of unexpected breakdowns, enhances equipment reliability, and increases overall operational efficiency.
3. Optimal resource utilization
Effective maintenance planning and scheduling optimize resource utilization by efficiently allocating labor, materials, and equipment. By identifying maintenance requirements in advance, organizations can minimize downtime, prevent overstaffing or underutilization, and ensure the availability of necessary tools and spare parts. This helps to streamline operations, reduce costs, and enhance overall productivity.
4. Cost reduction
Maintenance planning and scheduling save costs by identifying and fixing issues before they become severe problems. Preventive and predictive maintenance can save organizations money on reactive repairs and equipment replacements. Planned maintenance also allows for scheduling during planned shutdowns or low-demand periods, optimizing resource utilization and minimizing downtime. Early detection and resolution of minor issues prevent them from escalating into more significant and expensive failures.
5. Enhanced efficiency and productivity
Effective maintenance planning and scheduling integrate maintenance tasks seamlessly into operational workflows, minimizing disruptions and maximizing equipment uptime. This reduces idle time, enhances overall productivity, and improves operational efficiency.
Organizations can optimize resource allocation and reduce downtime by coordinating maintenance with production schedules and equipment availability. As a result, employees can focus on their core tasks without interruptions, production processes run smoothly, and the organization achieves higher output and efficiency, improving overall productivity.
6. Data-driven decision making
Data-Driven Decision Making in maintenance planning and scheduling involves utilizing valuable data on asset performance, maintenance history, and resource utilization. Analyzing this data helps identify equipment reliability, recurring issues, and opportunities for optimization. By leveraging these insights, organizations can make informed decisions regarding maintenance strategies, resource allocation, and process improvements. This data-driven approach enhances operational efficiency, minimizes downtime, and enables continuous improvement in maintenance practices.
Due to its numerous benefits, the market for maintenance software is experiencing rapid growth. Verified Market Research says that the CMMS Software Market was worth USD 913.58 Million in 2020 and is projected to reach USD 1,721.02 Million by 2028, with a compound annual growth rate (CAGR) of 8.41% from 2021 to 2028. This growth reflects the increasing adoption of maintenance software across industries.
Challenges of Maintenance Planning and Scheduling
Maintenance planning and scheduling can present several challenges that organizations need to address to ensure effectiveness. Below are some of the major challenges of maintenance planning and scheduling.
1. Balancing priorities
Organizations often have competing priorities, such as production demands, maintenance requirements, and resource limitations. Balancing these priorities can be challenging, as maintenance activities may need to be scheduled during production downtime or within limited time windows.
2. Lack of accurate data
Maintenance planning requires current equipment history, maintenance records, and performance measurements. Organizations may struggle to obtain and manage complete data, which can impair planning and decision-making.
3. Reactive maintenance culture
A reactive maintenance culture, where maintenance is only performed when equipment fails, can be a significant obstacle. Shifting from a reactive to a proactive approach requires a change in mindset, emphasizing preventive and predictive maintenance strategies.
4. Limited resources
Adequate resources, including skilled labor, spare parts, and equipment, are essential for effective maintenance planning and scheduling. Limited resources can pose challenges, leading to delays, inadequate maintenance coverage, and compromised equipment reliability.
5. Uncertainty and unpredictability
Equipment failures and maintenance requirements can be unpredictable, making it challenging to plan and schedule maintenance activities. Unforeseen breakdowns or emergencies can disrupt planned schedules and require immediate attention, leading to adjustments and rescheduling.
6. Communication and coordination
Effective maintenance planning and scheduling require strong communication and coordination among different stakeholders, including maintenance teams, production departments, and management. A lack of clear communication channels and coordination can result in delays, misunderstandings, and inefficient resource allocation.
7. Complex equipment and systems
Modern equipment and systems are often complex and interconnected, requiring specialized knowledge and skills for maintenance planning and scheduling. Ensuring that maintenance personnel have the necessary expertise and training to handle the complexity of equipment can be a challenge.
8. Changing business environment
Organizations operate in dynamic business environments that undergo changes such as technological advancements, market demands, and regulatory requirements. Adapting maintenance planning and scheduling to accommodate these changes can be challenging and may require frequent adjustments to strategies and processes. Addressing these challenges requires proactive measures, including the following-
- Investing in data management systems
- Fostering a culture of preventive maintenance
- Allocating resources strategically
- Enhancing communication and coordination
- Staying updated with industry trends and best practices
These challenges often arise from the complexity of coordinating multiple parties simultaneously. Consequently, schedulers require strong communication skills and sometimes unwavering determination to ensure that tasks are executed on schedule.
Best Practices for Maintenance Planning and Scheduling
Implementing best practices for maintenance planning and scheduling can significantly enhance the efficiency and effectiveness of maintenance activities. The following are some critical best practices:
1. Establish a preventive maintenance program
Implementing a preventive maintenance program based on manufacturer recommendations, industry standards, and equipment history helps identify and address potential issues before they lead to failures. This includes regular inspections, lubrication, calibration, and other proactive maintenance tasks.
2. Utilize computerized maintenance management systems (CMMS)
Implementing CMMS software enables efficient maintenance planning and scheduling by organizing and managing maintenance data, work orders, schedules, and inventory. CMMS provides real-time visibility into maintenance activities, improves data accuracy, and supports decision-making based on historical and real-time information. It streamlines maintenance processes, enhances communication, and helps optimize resource allocation, leading to more effective maintenance planning and scheduling. When selecting and implementing a CMMS or EAM system, it is crucial to consider functional and technological factors. Managing increasing data sources, aligning staffing and development resources, and modernizing legacy systems are key considerations highlighted by IT analyst IDC in order to meet the challenges of asset management effectively.
3. Conduct regular equipment assessments
Regular equipment assessments involve routine inspections, condition monitoring, and data analysis to identify signs of deterioration and emerging issues. Organizations can optimize maintenance schedules, prevent failures, and ensure reliable performance by proactively assessing equipment. These assessments minimize downtime, extend asset lifespan, and improve maintenance effectiveness.
4. Prioritize and categorize maintenance tasks
Effective scheduling requires prioritizing and categorizing maintenance work. Organizations might prioritize work by urgency and criticality to ensure quick attention. Categorizing tasks by type improves resource allocation, spares parts management, and improves response time planning- this optimizes maintenance plans, reduces downtime, and maximizes resources for the most crucial maintenance needs.
5. Develop long-term maintenance plans
Developing long-term maintenance plans involves creating comprehensive strategies for significant overhauls, equipment replacements, and upgrades. These plans align with organizational goals and objectives, enabling better budgeting, resource allocation, and scheduling of large-scale maintenance projects. This method also facilitates coordination with other departments, vendors, and suppliers executing long-term maintenance plans.
6. Optimize scheduling and coordination
Plan to conduct maintenance activities during scheduled downtimes or low-demand periods to minimize disruptions. Coordinate with other departments and stakeholders to ensure resource availability, equipment access, and effective communication. This improves efficiency, reduces conflicts, and enables smoother execution of maintenance tasks while minimizing the impact on production and operations.
7. Document and share maintenance knowledge
Documenting and sharing maintenance knowledge involves creating a centralized repository of maintenance procedures, troubleshooting guides, equipment history, and lessons learned. This knowledge-base promotes consistency and efficiency and enables continuous improvement. It facilitates the exchange of information among maintenance teams, supports training and onboarding processes, and ensures that valuable maintenance knowledge is accessible to all stakeholders, leading to improved planning and scheduling practices.
8. Foster communication and collaboration
Open communication channels enable the exchange of critical information, promote coordination, and ensure that maintenance planning aligns with the organization's goals and operational requirements. Collaboration facilitates the efficient allocation of resources, effective scheduling, and proactive decision-making. Strong communication and cooperation contribute to the overall success of maintenance planning and scheduling processes.
It's time for action!
Effective maintenance planning and scheduling are the keys to unlocking operational excellence. Organizations can ensure smooth operations and maximize asset performance by minimizing downtime, optimizing resources, and prioritizing maintenance tasks. Despite challenges, implementing best practices such as preventive maintenance programs, utilizing technology, and fostering collaboration can pave the way for success. So why wait? Embrace the power of planning and scheduling, and watch your maintenance efforts soar to new heights of efficiency and productivity!
TABLE OF CONTENTS
Keep Reading
Ever find yourself checking into a luxury hotel and expecting a relaxing stay, only to find a ...
11 Apr 2025
Organizations are witnessing swift changes in the business environment and confronting a ...
8 Apr 2025
Last month, news outlets and the entire internet was abuzz with the return of NASA astronauts ...
3 Apr 2025
What comes first - CMMS or predictive maintenance? If your answer is either, it is correct. ...
28 Mar 2025
Artificial intelligence (AI) talk has become commonplace. Today, engaging in business-focused ...
27 Mar 2025
Imagine a world where machines predict, diagnose, and fix their issues before they fail. This ...
25 Mar 2025
A facility maintenance plan is at the core of a facility’s operations. This organized ...
21 Mar 2025
Think of managing your maintenance operations like managing a championship sports team. Just ...
21 Mar 2025
The maintenance sector is battling a severe talent shortage that threatens to undermine ...
7 Mar 2025
Manufacturing maintenance is the backbone of industrial efficiency, ensuring machines run ...
5 Mar 2025
No one likes playing a guessing game when equipment breaks down. Yet, maintenance teams often ...
4 Mar 2025
The size of the preventive maintenance software market is discussed in millions of dollars, ...
4 Mar 2025
The organizational structure and corporate hierarchy vary from company to company. Large ...
28 Feb 2025
Maintenance procedures are essential for ensuring the longevity and reliability of machinery ...
21 Feb 2025
Sustainability is no longer just a buzzword; it's a critical component of corporate social ...
20 Feb 2025
A Computerized Maintenance Management System (CMMS) relies on accurate, well-organized data ...
18 Feb 2025
In an era where technology drives operational efficiency, Computerized Maintenance Management ...
14 Feb 2025
A Computerized Maintenance Management System (CMMS) is a key component of modern maintenance ...
13 Feb 2025
Introduction Maintenance management is the foundation of maintenance operations in industries ...
11 Feb 2025
Introduction A Computerized Maintenance Management System (CMMS) is software designed to help ...
7 Feb 2025