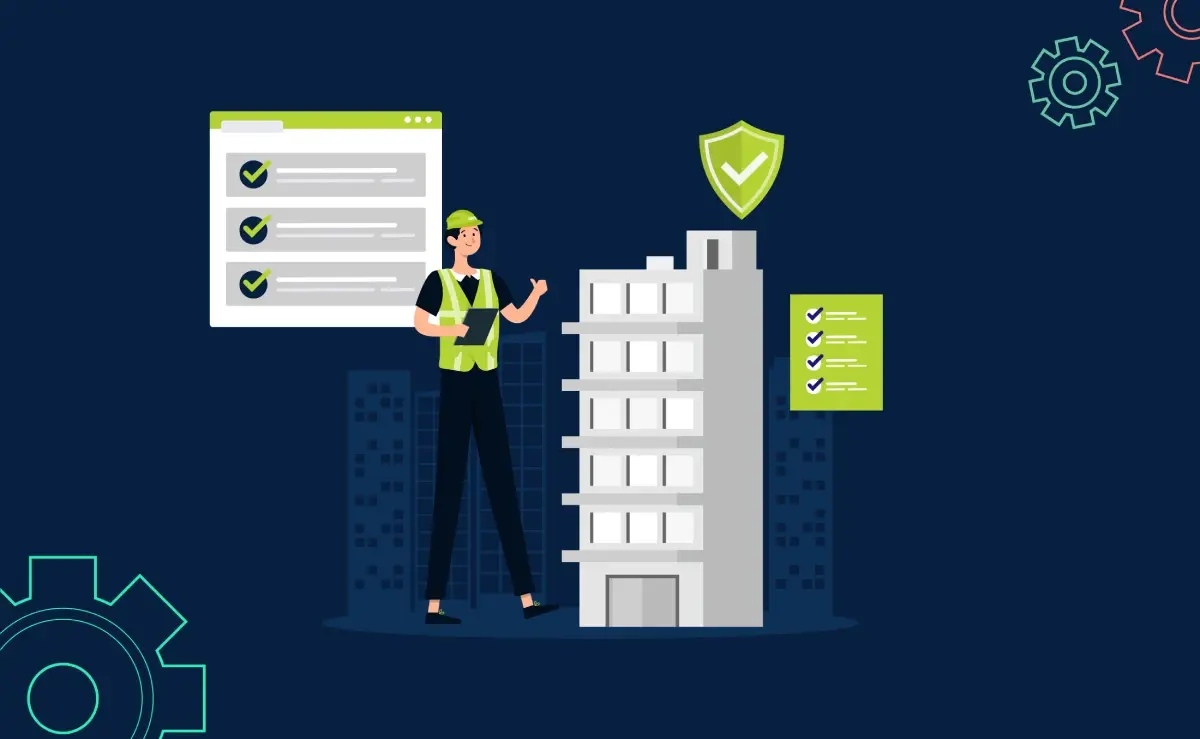
Facilities Management Maintenance Tactics: Customizing Plans for Diverse Infrastructure Needs
Facilities management ensures that buildings operate smoothly. When maintenance is a top priority, the 2023 Maintenance Engineering Report shows that 52% of companies became more cost-effective, while 41% experienced a reduction in downtime.
When you have effective facilities management, you maintain safety, efficiency, and sustainability for all stakeholders. This includes all kinds of infrastructure, from commercial skyscrapers to hospitals and industrial complexes.
However, in facilities management, one size rarely fits all. Each facility has its own unique challenges, intricacies, and critical systems. This is why customized maintenance plans are necessary to address diverse infrastructure needs.
In this blog post, we’ll discuss the importance of customized plans for diverse infrastructure needs. We’ll also explain facilities management maintenance tactics as well as the role of technology, training, and continuous improvement.
What are diverse infrastructure needs?
Diverse infrastructure needs stem from a combination of many factors, such as the type of facility, its size, usage patterns, age, location, and regulatory requirements.
So, employing only one approach to maintenance poses significant risks, namely inefficiencies, increased costs, and compromised safety.
Alternatively, tailored maintenance plans offer the following benefits:
- Cost efficiency: Customized maintenance plans will optimize resource allocation based on the company’s needs. This reduces unnecessary expenditures while maximizing the value of investments in upkeep and repairs.
- Increased lifespan of assets: Through targeted maintenance strategies, you can prolong the lifespan of your infrastructure and machinery involved in day-to-day processes. As a result, managers can reduce the frequency of replacements and costly downtime.
- Improved safety: One key advantage of customized maintenance plans is that they prioritize the upkeep of safety-critical systems and equipment. For workers with high-risk hazards at work, regular and bespoke maintenance minimizes the likelihood of accidents, failures, and regulatory non-compliance.
Different Requirements for Each Type of Facility
- Commercial Buildings: Commercial building maintenance often focuses on optimizing energy efficiency to ensure tenant comfort and preserve aesthetic appeal. This may involve:
- Regular Heating, Ventilation, and Air Conditioning (HVAC) system inspections
- Façade cleaning
- Elevator maintenance
- Parking lot upkeep
- Healthcare Institutions: Maintenance in healthcare facilities is critical for patient safety, regulatory compliance, and the uninterrupted delivery of care. Maintenance tasks should include:
- Rigorous sanitation protocols
- Servicing of medical equipment
- Maintenance of life support systems
- Compliance with regulations such as the National Fire Protection Association (NFPA).
- Educational Institutions: While schools and universities need to create conducive learning environments, they must also ensure the safety and well-being of students and faculty. So, educational institutions need to frequently conduct:
- HVAC system maintenance
- Playground safety inspections
- Routine classroom equipment checks
- Compliance assessments for educational facility codes and standards.
- Industrial Sites: As locations that aim to optimize production efficiency, industrial sites want to prevent equipment downtime and ensure workplace safety. Therefore, companies need to ensure that the following are routinely done:
- Machinery servicing
- Predictive maintenance
- Checks for compliance with Occupational Safety and Health Administration (OSHA) regulations
How to Develop a Customized Maintenance Plan
Depending on your industry, customizing plans for diverse infrastructure needs must be a priority. You might even need to consult a facility manager’s playbook to get all the steps.
Here’s a general overview of how you can develop a bespoke maintenance plan for your facility:
Conduct a Thorough Assessment
Check your current plans and systems. An assessment typically involves two key steps:
1. Site Inspections and Audits
Regular site inspections and audits are conducted to evaluate the facility's current condition, identify potential hazards, and assess the performance of critical systems and equipment.
These inspections may be carried out by internal maintenance teams or external specialists. They may include visual inspections, equipment testing, and data collection using tools such as infrared thermography or vibration analysis.
2. Identify Critical Assets and Their Maintenance Needs
Your facility’s critical assets are those essential for its operation. Critical assets may include HVAC systems, electrical infrastructure, fire suppression systems, production machinery, or other components crucial for safety, productivity, or regulatory compliance.
Understand each asset’s maintenance needs by speaking with those on your production floor. The workers who use those critical assets will be the most familiar with the machine. You can also consult with each machine's assigned mechanic.
Set Priorities
Once the assessment is complete, the next step is prioritizing maintenance tasks based on their impact on the facility's operations, safety, and compliance. This involves:
- Conducting a risk assessment to identify potential risks and hazards associated with equipment failures, environmental factors, or regulatory non-compliance.
- Prioritize and allocate resources to critical maintenance tasks that directly impact core functions and compliance, addressing these needs before less urgent, non-critical tasks.
- Implementing risk management strategies to mitigate identified risks and prevent potential issues.
Create a Maintenance Schedule
Photo by Field Engineer, sourced from Pexels
With priorities established, the next step is to create a structured maintenance schedule that outlines the frequency and timing of inspections, preventive maintenance, and repairs.
When creating your maintenance schedule, make sure you:
- Determine how often inspections and routine maintenance activities should be performed. This is based on equipment manufacturer recommendations, regulatory requirements, and historical performance data.
- Identify the seasonal factors, environmental conditions, and operational demands that might affect your schedule. For example, you might need to schedule HVAC systems maintenance for summer cooling or winter heating or conduct preventive measures ahead of peak production periods.
Implement Maintenance Strategies
Implementing effective maintenance strategies is crucial for ensuring the reliability, longevity, and efficiency of facility operations.
Here are three approaches to maintenance:
- Preventive Maintenance: This aims to maintain equipment reliability. Preventive maintenance proactively addresses potential issues through scheduled inspections, lubrication, cleaning, and parts replacement. You can set up preventive maintenance schedules by considering each step involved or find resources that can give you a complete checklist, such as a heavy equipment preventive maintenance checklist.
- Predictive Maintenance: An approach that uses data analysis and condition monitoring to anticipate equipment failures before they occur, enhancing preventive maintenance.
- Reactive Maintenance: Although this may be less cost-effective than preventive or predictive maintenance, it still addresses equipment failures as they happen, minimizing downtime with prompt repairs. However, it is not proactive like the other types of maintenance, so production may suffer if teams are not trained or prepared.
Train Staff for Effective Maintenance
A key part of the successful implementation of proactive maintenance strategies is a trained and equipped workforce.
You need to ensure that your maintenance teams are equipped with skilled technicians and that they receive ongoing training, which is essential for effective maintenance management. Another option is to consider outsourcing a maintenance plan, possibly with the supplier of your machinery.
Encourage Continuous Improvement and Feedback
To refine your maintenance strategies, you need to develop a continuous improvement plan.
You can do this by receiving feedback through regular reviews and evaluations of maintenance plans and by analyzing key performance indicators (KPIs).
Here are KPIs you need to look at to identify areas for improvement:
- Equipment uptime
- Maintenance costs
- Response times
Moreover, you should stay updated with industry trends and regulations to ensure that your company’s maintenance practices are effective and compliant.
These are a couple of modern solutions you should consider incorporating into your maintenance plans:
- Use Computerized Maintenance Management Systems (CMMS): The best CMMS software streamlines maintenance workflows, tracks work orders, manages inventory, and generates reports. There are also CMMS applications that maintenance technicians can use on their phones to gain real-time access to work orders, equipment manuals, and maintenance schedules.
Check out the List of
Best CMMS Software
by Research.com
- Adopt Eco-friendly Maintenance Techniques: Aside from ensuring a reduced carbon footprint, eco-friendly maintenance techniques can help reduce costs in the long run. For example, retrofitting existing equipment and systems with energy-efficient technologies can reduce energy costs.
Develop the Right Facility Management Tactics
In conclusion, a bespoke maintenance management strategy is necessary to ensure that buildings run smoothly, safely, and efficiently.
Creating these plans involves thorough assessments, prioritizing critical tasks, and using preventive, predictive, and reactive maintenance. You can optimize your maintenance efforts by training skilled technicians, fostering continuous improvement, and leveraging technology like CMMS.
Remember to stay updated with industry trends and adopt eco-friendly practices to improve your operational performance and sustainability further.
TABLE OF CONTENTS
Keep Reading
Ever find yourself checking into a luxury hotel and expecting a relaxing stay, only to find a ...
11 Apr 2025
Organizations are witnessing swift changes in the business environment and confronting a ...
8 Apr 2025
Last month, news outlets and the entire internet was abuzz with the return of NASA astronauts ...
3 Apr 2025
What comes first - CMMS or predictive maintenance? If your answer is either, it is correct. ...
28 Mar 2025
Artificial intelligence (AI) talk has become commonplace. Today, engaging in business-focused ...
27 Mar 2025
Imagine a world where machines predict, diagnose, and fix their issues before they fail. This ...
25 Mar 2025
A facility maintenance plan is at the core of a facility’s operations. This organized ...
21 Mar 2025
Think of managing your maintenance operations like managing a championship sports team. Just ...
21 Mar 2025
The maintenance sector is battling a severe talent shortage that threatens to undermine ...
7 Mar 2025
Manufacturing maintenance is the backbone of industrial efficiency, ensuring machines run ...
5 Mar 2025
No one likes playing a guessing game when equipment breaks down. Yet, maintenance teams often ...
4 Mar 2025
The size of the preventive maintenance software market is discussed in millions of dollars, ...
4 Mar 2025
The organizational structure and corporate hierarchy vary from company to company. Large ...
28 Feb 2025
Maintenance procedures are essential for ensuring the longevity and reliability of machinery ...
21 Feb 2025
Sustainability is no longer just a buzzword; it's a critical component of corporate social ...
20 Feb 2025
A Computerized Maintenance Management System (CMMS) relies on accurate, well-organized data ...
18 Feb 2025
In an era where technology drives operational efficiency, Computerized Maintenance Management ...
14 Feb 2025
A Computerized Maintenance Management System (CMMS) is a key component of modern maintenance ...
13 Feb 2025
Introduction Maintenance management is the foundation of maintenance operations in industries ...
11 Feb 2025
Introduction A Computerized Maintenance Management System (CMMS) is software designed to help ...
7 Feb 2025