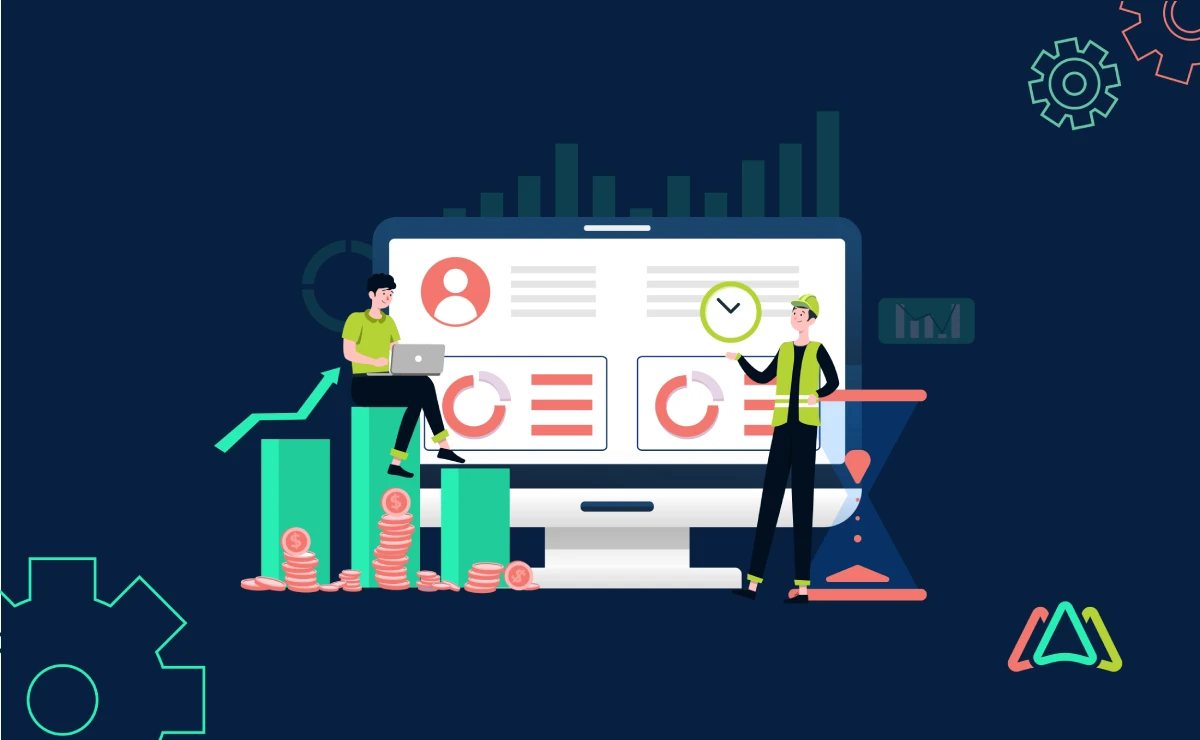
How to Make an ROI Case for CMMS Software Without Maintenance History
Introduction
There are no two ways about it. Acquiring a Computerized Maintenance Management System (CMMS) takes time and money. Not surprisingly, pitching investing in a CMMS to the C-Suite is challenging at the best of times. In almost every case, you can expect to hear, “I’m open to the idea; just show me the ROI.” Seems reasonable, but how do you create an ROI case when there is no documented maintenance history to rely on? After all, one of the reasons you’re looking for a CMMS in the first place is so you can easily access maintenance history for your assets and facilities and know what the company is spending on maintenance. So, where does this leave a facility manager with CMMS experience convinced that the software will improve the company’s operation? To be successful, the facility manager’s pitch to the CEO has to have more substance than gut intuition, especially when the CEO is a numbers person.
The above situation is not unique. Facilities and maintenance leaders are often challenged with the dilemma of finding a convincing way to demonstrate to their C-suite that a CMMS will greatly benefit their company’s operations and bottom line. Here, we will present a plan that fits the described scenario and can be applied to any RIO case supporting a CMMS investment. The plan provides a systematic pathway that will take a CEO from focusing solely on the investment to understanding how CMMS software will streamline operations, optimize preventive maintenance, and, ultimately, save time, money, and resources.
Understanding the Need
Companies that rely on manual maintenance management have maintenance operations that are fragmented, reactive, and prone-to-errors. Without a CMMS, maintenance managers face frequent breakdowns, expensive repairs, inefficient scheduling, stockouts, and rush orders for parts. They also unnecessarily spend long hours compiling maintenance reports using multiple data sources with questionable reliability.
Furthermore, managing work orders using manual processes presents problems for maintenance managers and their teams. Apart from the time it takes to write up several work orders daily, additional time is needed to dispatch them to maintenance operators. Since time is money, CMMS software eliminates unnecessary time lags by generating and dispatching work orders within seconds. And here’s one final timesaving point about automated work orders. With CMMS-generated work orders, maintenance teams can communicate with their managers while on assignment and sign off on the task once it is completed. All can be done remotely, thus eliminating the time it takes to track down the facility manager.
Unlike a CMMS, manual maintenance management lacks efficiency and organization. The result is increased downtime, costly emergency repairs, and resource drain. Investing in a CMMS can significantly benefit your company's operations and bolster its bottom line by streamlining maintenance processes such as centralizing data, scheduling tasks, and tracking equipment performance. Considered together, these CMMS features lead to improved asset reliability and uptime.
A CMMS helps optimize resources, reduce downtime, and extend equipment lifespan by providing real-time insights into maintenance activities, These, in turn, lower maintenance costs. The CMMS’s ability to offer proactive maintenance prevents unexpected breakdowns, minimizing costly emergency repairs and enhancing overall operational efficiency. Finally, the system's reporting and analytics capabilities allow facility managers to make data-driven decisions. A CMMS software’s reporting capabilities make it possible to identify maintenance trends that will inform resource allocations more efficiently and, in turn, refine maintenance strategies.
Investing in a CMMS will undoubtedly enhance operational effectiveness, contribute to long-term cost savings, and improve profitability for your company. Now, let’s build an ROI case for a wary and cost-conscious CEO, beginning with a brief preamble to set the stage.
The Role of CMMS Software
CMMS software forms the backbone of efficient maintenance management by centralizing all data, automating work order management, and facilitating preventive maintenance scheduling. With CMMS software, tasks such as tracking assets, managing inventory, and analyzing maintenance trends become streamlined and transparent. By harnessing the power of preventive maintenance, CMMS software empowers maintenance leaders to address issues proactively, minimizing disruptions and extending the lifespan of critical assets. In addition to all the benefits just described, it takes the guesswork out of making informed decisions, whether creating schedules, ordering parts, checking inventories, or assessing the viability of assets.
Crafting the ROI Case
While the benefits of CMMS software are clear, communicating its return on investment (ROI) to upper management requires a strategic approach. In the absence of a documented maintenance history, the focus should be on the following potential cost savings and operational improvements that CMMS software can deliver:
Reduced Downtime
Without a CMMS, downtime from equipment failures or unplanned maintenance is inevitable. Implementing preventive maintenance schedules through CMMS software can significantly reduce downtime, ensuring uninterrupted operations and maximizing productivity. This is mainly due to the CMMS-driven proactive and streamlined workflow approach. More specifically, by centralizing data on equipment history, performance metrics, and maintenance schedules, the system makes it possible for maintenance teams to anticipate potential issues before they escalate into costly breakdowns.
To that end, the CMMS has automated alerts and reminders letting users know when preventive maintenance tasks such as inspections, lubrication, and part replacements should be scheduled, therefore minimizing the risk of unexpected failures. As was noted previously, the CMMS optimizes work order management by assigning tasks, tracking progress, and managing spare parts inventory, ensuring timely completion of maintenance activities. The CMMS provides facility managers with enhanced visibility into equipment health. Companies can proactively address maintenance needs, mitigate downtime, and maximize equipment reliability and uptime through streamlined maintenance processes.
Extended Asset Lifespan
A lack of a preventive maintenance program often leads to premature equipment failure and the need for costly replacements. With CMMS software, assets are maintained according to manufacturer recommendations, leading to longer lifespans and reduced capital expenditures.
Delving into this deeper, a CMMS centralizes an organization’s data on asset history, performance, and maintenance schedules. With this data, the system enables maintenance teams to implement timely preventive maintenance tasks, such as inspections, lubrication, and component replacements, based on actual usage and condition rather than arbitrary schedules. This proactive approach minimizes wear and tear, reduces the likelihood of unexpected failures, and helps identify potential issues before they escalate.
In the absence of documented maintenance history reports, managers should rely on recent anecdotal evidence. Pull a couple of examples of when equipment unexpectedly broke down. Calculate the financial impact related to the breakdown that could have been avoided through proper preventive maintenance. For manufacturing companies, a good example might be a piece of production machinery. Figure out how many hours the machine was down, and what the cost of downtime was for each hour. Also, include any costs associated with rush ordering parts and overtime pay required to pay technicians to get the asset back online. Two examples of equipment failure that resulted in lost production, overtime pay, and rush orders might justify the investment on their own.
Improved Compliance
Compliance with regulatory standards is paramount in industries such as education. CMMS software enables maintenance and facility managers to track and document maintenance activities, ensuring safety and compliance with environmental regulations.
A CMMS improves compliance by providing a centralized platform for managing regulatory requirements, documentation, and audit trails. There is no longer a need to track down information by spending hours sifting through filing cabinets. Instead, a CMMS allows companies to establish standardized maintenance procedures that align with industry regulations and internal policies. By automating task scheduling and reminders, the CMMS ensures that critical maintenance activities are performed on time, reducing the risk of non-compliance penalties.
A CMMS enables comprehensive tracking of maintenance activities, including work orders, inspections, and repairs, generating detailed reports for regulatory agencies and auditors. Once again, with real-time visibility into compliance status and historical data readily available, companies can more effectively demonstrate adherence to regulatory standards, mitigate compliance risks, and maintain operational integrity.
In the absence of documented maintenance history, managers should refer back to the most audit the company underwent. The CEO or others involved in the approval process will remember the resources and time spent to collect the information needed to satisfy the audit requirements. If the company was penalized with any fines or penalties, be sure to highlight ways a CMMS software could have prevented them.
Enhanced Resource Allocation
Manual maintenance management processes are resource-intensive and prone to errors. By automating work order management and inventory tracking, CMMS software frees up staff time and reduces the risk of oversights or duplication of efforts.
A CMMS provides real-time visibility into maintenance activities, equipment status, and workforce availability. The system informs maintenance and facility managers on priorities through comprehensive data tracking and analysis, efficiently allocates resources, and optimizes maintenance task scheduling. By centralizing information on equipment history, maintenance schedules, and spare parts inventory, the CMMS helps maintenance teams make informed decisions about resource allocation, ensuring that the right people and materials are available when needed.
Additionally, the system streamlines communication and collaboration among maintenance teams, enabling better coordination and utilization of available resources. By facilitating data-driven decision-making and improving collaboration, a CMMS enhances resource allocation, minimizing downtime, reducing costs, and maximizing operational efficiency.
In the absence of maintenance history, point to how a CMMS automates workflows such as escalating critical work orders, routing specific tasks to the right maintenance team or technician based on category, notifications of parts to order and upcoming PMs, and overdue work orders. Compare these built-in automated capabilities to the time and vulnerabilities that are present with the status quo.
Data-Driven Decision Making
CMMS software provides valuable insights into maintenance trends, asset performance, and resource utilization. A CMMS collects and stores vast amounts of information on equipment performance, maintenance history, work orders, and inventory levels, among other metrics. Through advanced reporting and analytics features, the CMMS can generate customizable reports and dashboards highlighting key performance indicators, trends, and areas for improvement.
By leveraging this data, decision-makers gain valuable insights into asset reliability, maintenance costs, and resource utilization, enabling them to make informed decisions about maintenance strategies, equipment investments, and resource allocation. Additionally, the system can forecast maintenance needs based on historical data and predictive analytics, allowing companies to address potential issues before they impact operations proactively. A CMMS empowers organizations to optimize maintenance processes, minimize downtime, and improve operational efficiency through data-driven decision-making.
Presenting the Case
When presenting the ROI case for CMMS software to a CEO, it's essential to tailor the message to resonate with their priorities and concerns. Although not having a documented maintenance history available poses a challenge, it is not insurmountable.
Gear the presentation toward the potential for a rapid ROI, citing industry benchmarks and case studies where applicable. Also, consider leveraging external expertise or industry best practices to bolster your argument. This is where it is helpful to engage with vendors or consultants specializing in CMMS implementation that can provide insights and recommendations tailored to your facility's unique needs.
Use the following points as an outline to structure an RIO case presentation:
Tangible Cost Savings
Emphasize the potential savings achievable through reduced equipment downtime, minimized emergency repairs, optimized maintenance labor, and extended asset lifespan. Quantify these savings based on industry benchmarks to demonstrate the tangible financial benefits of implementing a CMMS.
Improved Operational Efficiency
Discuss how a CMMS streamlines maintenance workflows, enhances resource allocation and improves overall operational efficiency. Highlight specific examples of how the system automates repetitive tasks, increases productivity, and enables better coordination among maintenance teams, leading to time and cost savings across the organization.
Regulatory Compliance
Highlight how a CMMS helps ensure regulatory compliance by maintaining accurate records, tracking maintenance activities, and facilitating audits. Emphasize the potential cost savings associated with saving time, avoiding non-compliance penalties and fines, and the reputational benefits of demonstrating adherence to industry standards and regulations.
Data-Driven Decision-Making
Illustrate how a CMMS enables data-driven decision-making by providing real-time insights into maintenance performance, equipment health, and resource utilization. Showcase the system's reporting and analytics capabilities, demonstrating how they empower decision-makers to identify trends, optimize maintenance strategies, and allocate resources more effectively, ultimately driving bottom-line results.
Scalability and Growth
Highlight the CMMS platform's scalability and its ability to support the organization's growth objectives. Discuss how the system can adapt to evolving business needs, accommodate increased asset volumes, and integrate with other business systems to drive continuous improvement and support long-term success.
Maintenance and facility managers tasked with improving operational efficiency and reducing costs without the help of reliable software is challenging. Companies considering investing in CMMS software need to understand that it’s an impactful decision and a strategic imperative. There benefits of a CMMS are plenty; the ability to centralize maintenance data, automate work order management, and facilitate preventive maintenance scheduling. The benefits come from optimized resources, minimized downtime, and enhanced asset performance. All of these directly and positively affect an organization’s bottom line.
In making the case for CMMS software to a CEO, focus on the potential ROI, emphasizing the tangible cost savings, operational efficiencies, and long-term benefits such an investment can yield. With a compelling argument backed by data and industry expertise, the merits of CMMS software become undeniable, paving the way for a more efficient and sustainable future for the facility.
TABLE OF CONTENTS
Keep Reading
Ever find yourself checking into a luxury hotel and expecting a relaxing stay, only to find a ...
11 Apr 2025
Organizations are witnessing swift changes in the business environment and confronting a ...
8 Apr 2025
Last month, news outlets and the entire internet was abuzz with the return of NASA astronauts ...
3 Apr 2025
What comes first - CMMS or predictive maintenance? If your answer is either, it is correct. ...
28 Mar 2025
Artificial intelligence (AI) talk has become commonplace. Today, engaging in business-focused ...
27 Mar 2025
Imagine a world where machines predict, diagnose, and fix their issues before they fail. This ...
25 Mar 2025
A facility maintenance plan is at the core of a facility’s operations. This organized ...
21 Mar 2025
Think of managing your maintenance operations like managing a championship sports team. Just ...
21 Mar 2025
The maintenance sector is battling a severe talent shortage that threatens to undermine ...
7 Mar 2025
Manufacturing maintenance is the backbone of industrial efficiency, ensuring machines run ...
5 Mar 2025
No one likes playing a guessing game when equipment breaks down. Yet, maintenance teams often ...
4 Mar 2025
The size of the preventive maintenance software market is discussed in millions of dollars, ...
4 Mar 2025
The organizational structure and corporate hierarchy vary from company to company. Large ...
28 Feb 2025
Maintenance procedures are essential for ensuring the longevity and reliability of machinery ...
21 Feb 2025
Sustainability is no longer just a buzzword; it's a critical component of corporate social ...
20 Feb 2025
A Computerized Maintenance Management System (CMMS) relies on accurate, well-organized data ...
18 Feb 2025
In an era where technology drives operational efficiency, Computerized Maintenance Management ...
14 Feb 2025
A Computerized Maintenance Management System (CMMS) is a key component of modern maintenance ...
13 Feb 2025
Introduction Maintenance management is the foundation of maintenance operations in industries ...
11 Feb 2025
Introduction A Computerized Maintenance Management System (CMMS) is software designed to help ...
7 Feb 2025