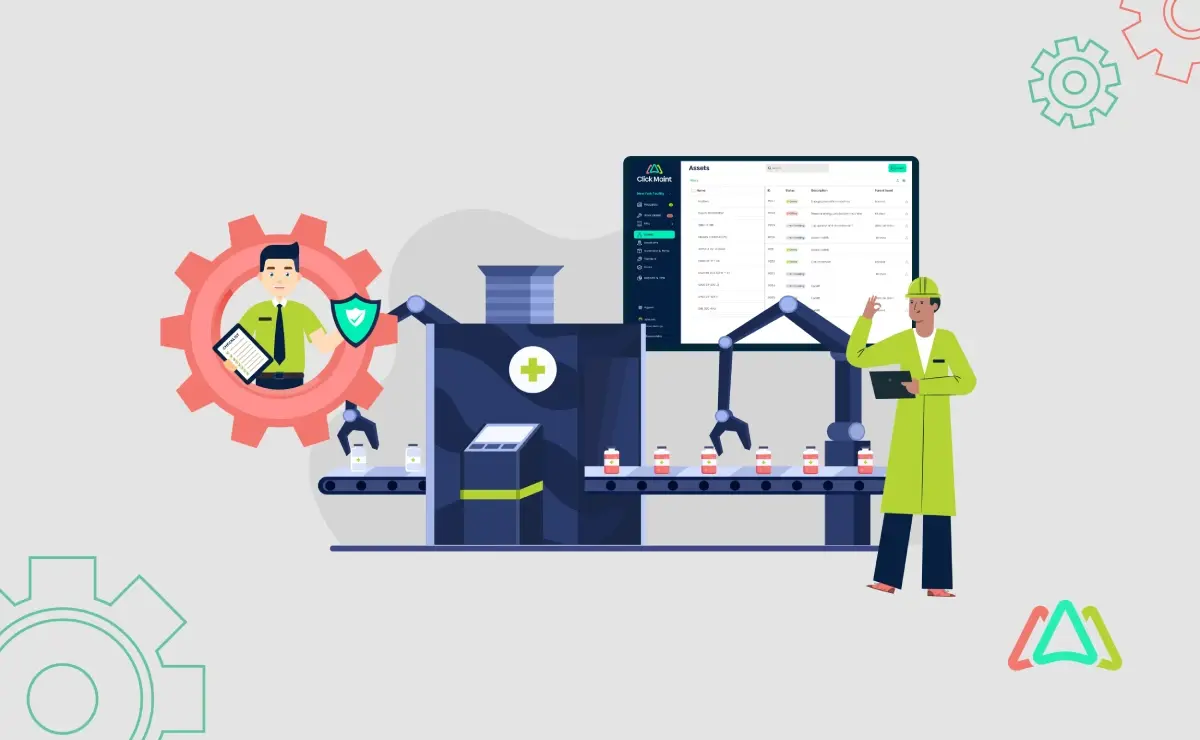
Maximizing Equipment Uptime and Compliance with CMMS in Pharmaceutical Manufacturing
Introduction
In the pharmaceutical industry, equipment uptime isn't just a matter of operational efficiency; it's a critical factor that directly impacts consumer safety and regulatory compliance. According to research by the TWI Institute, the average manufacturing plant experiences 15 hours of downtime per week. B2B research company Aberdeen estimates that the average business loses $260,000 per hour of downtime, amounting to over $2 million per year (as cited by Forbes). This staggering figure underscores the importance of maintaining continuous, reliable equipment operations. Pharmaceutical manufacturers rely on complex machinery and stringent compliance requirements. Advanced machinery is essential for ensuring the quality and consistency of pharmaceutical products, while adherence to regulations such as FDA guidelines and Good Manufacturing Practices (GMP) is a must. Failure to meet these standards can result in costly recalls, fines, and damage to a company's reputation.
A solution to these challenges is the implementation of a Computerized Maintenance Management System (CMMS). CMMS software streamlines maintenance processes and ensures comprehensive compliance documentation, making it an essential tool for maximizing equipment uptime and adhering to rigorous regulatory standards. This article explores how CMMS software transforms maintenance management in pharmaceutical manufacturing, offering a pathway to enhanced operational efficiency and regulatory adherence.
Understanding Equipment Uptime in Pharmaceutical Manufacturing
Equipment uptime is a measure of the time during which machinery is operational and producing goods without interruption. In the pharmaceutical industry, maintaining high equipment uptime is vital due to the sector's reliance on precise, consistent production processes. Equipment downtime can lead to significant production delays, potential loss of product quality, and increased costs associated with repairs and replacements. Given the industry’s stringent regulatory requirements, any lapse in equipment performance can also lead to compliance issues and potential regulatory penalties.
Ensuring optimal equipment uptime presents several challenges. Unplanned downtime is a major issue, often arising from unexpected equipment failures or breakdowns. These disruptions halt production lines, leading to costly delays and extended repair times. Unplanned downtime not only prevents manufacturers from delivering products on time but also affects the quality of the final product, as continuous disrupted workflow often fails to yield consistent operational qualities. According to Pharma magazine, a major cause of unplanned downtime is equipment failure and breakdowns that occur unexpectedly, as well as the lack of maintenance to keep equipment functioning properly. Waiting until equipment fails before repairing it leads to higher maintenance costs and long periods of unplanned downtime, resulting in missed production goals. Other reasons for unplanned downtime include the unavailability of spare parts. All of these causes for unplanned downtime can be monitored and reduced with CMMS software.
Introduction to CMMS
A Computerized Maintenance Management System (CMMS) is a software solution designed to streamline and automate maintenance management tasks. It centralizes maintenance data, facilitating efficient tracking and management of equipment and assets. Core functions of a CMMS include maintenance scheduling, which ensures timely and routine upkeep of machinery; work order management, which organizes and tracks maintenance requests and tasks; and inventory control, which monitors and manages spare parts and materials.
Implementing a CMMS software has many benefits. It enhances maintenance efficiency by automating routine tasks and providing real-time insights into equipment performance, leading to reduced downtime and lower repair costs. Additionally, CMMS improves compliance management by ensuring accurate record-keeping and documentation, which is important for meeting regulatory requirements. Overall, a CMMS helps optimize maintenance operations, boost productivity, and maintain high standards of operational excellence.
How CMMS Maximizes Equipment Uptime
CMMS software plays a major role in maximizing equipment uptime through several key features. One of its primary functions is facilitating preventive maintenance. By automating the scheduling of regular maintenance tasks, CMMS ensures that equipment is serviced before minor issues escalate into major problems. This proactive approach reduces the likelihood of unexpected downtimes and helps maintain optimal equipment performance.
Another significant benefit of CMMS is real-time monitoring. It continuously tracks equipment performance and operational metrics, providing instant alerts when abnormalities or potential issues are detected. These alerts enable maintenance teams to address problems swiftly, preventing equipment failures and minimizing disruption to production schedules.
Additionally, CMMS supports predictive maintenance (PdM) by analyzing historical data and performance trends. This analysis helps identify patterns that may indicate impending equipment failures. By leveraging this information, CMMS allows maintenance teams to schedule interventions based on predicted needs rather than relying solely on fixed intervals. This approach not only extends the lifespan of equipment but also enhances overall operational efficiency by addressing issues before they cause significant downtime.
Compliance Requirements in Pharmaceutical Manufacturing
In pharmaceutical manufacturing, strict regulatory standards are essential to ensure the safety and efficacy of products. Key regulations include the U.S. Food and Drug Administration (FDA) guidelines and Good Manufacturing Practices (GMP). The FDA oversees drug safety and efficacy, mandating rigorous testing and quality control to protect public health. GMP, established by the FDA, provides a framework for manufacturing practices, ensuring that products are consistently produced and controlled according to quality standards.
Maintaining compliance with these regulations presents significant challenges for pharmaceutical companies. One major hurdle is meticulous record-keeping; companies must maintain comprehensive documentation of all production processes, quality control measures, and maintenance activities. This documentation is required to demonstrate adherence to regulatory standards during inspections and audits. Additionally, regular audits, both internal and external, are required to verify compliance, which can be resource-intensive and disruptive to operations. Companies must also navigate evolving regulations and standards, requiring ongoing updates to their compliance procedures and practices. Balancing the need for strict adherence with operational efficiency demands robust systems and processes, making effective compliance management a critical aspect of pharmaceutical manufacturing.
Ensuring Compliance with CMMS
CMMS software ensures compliance in the pharmaceutical industry by automating and streamlining key processes. Automated record-keeping maintains accurate, up-to-date records of all maintenance activities, eliminating human error and ensuring complete documentation needed for regulatory requirements. CMMS simplifies regulatory audits by providing easy access to comprehensive maintenance logs and compliance reports, making verification straightforward for auditors. By centralizing documentation, CMMS facilitates smoother, more efficient audits.
Additionally, CMMS systems enforce Standard Operating Procedures (SOPs) by integrating them into workflows, ensuring consistent performance of maintenance tasks. Automating SOPs helps maintain compliance with regulations such as GMP, reducing the risk of regulatory breaches and enhancing overall operational efficiency.
CMMS Implementation Best Practices
Implementing a Computerized Maintenance Management System (CMMS) effectively requires careful planning and execution. Selecting the right CMMS software is important, especially for pharmaceutical manufacturing. Choose a system that aligns with industry-specific needs, such as compliance with regulatory standards and the ability to handle complex maintenance schedules. Look for features like automated record-keeping, real-time monitoring, and integration capabilities with other systems.
Integration with existing systems, such as Enterprise Resource Planning (ERP) and quality management systems, is essential for seamless operations. A CMMS that integrates well with ERP systems can streamline data flow between maintenance and other business functions, enhancing overall efficiency. Integration with quality management systems ensures that maintenance activities are aligned with quality control processes, aiding in compliance and improving operational consistency.
Training and adoption are critical for successful CMMS implementation. Provide comprehensive training for staff to ensure they understand how to use the system effectively. Encourage widespread adoption by demonstrating the benefits of the CMMS, such as improved maintenance efficiency and compliance management. Engage employees early in the process and address any concerns to ensure a smooth transition. By focusing on these best practices, organizations can maximize the value of their CMMS and achieve better maintenance outcomes.
Overcoming Common CMMS Objections
When considering the implementation of a Computerized Maintenance Management System (CMMS), several common objections may arise. One primary concern is the cost. While the initial investment in a CMMS might seem substantial, it's important to view it as a strategic investment rather than an expense. Exploring the demo version might be a good option in this scenario. Well-implemented CMMS can significantly reduce maintenance costs, improve equipment uptime, and enhance operational efficiency, ultimately delivering a high return on investment through increased productivity and reduced downtime.
Another concern is the perceived complexity of CMMS. Many fear that the system will be too complex to manage effectively. However, modern CMMS solutions often feature user-friendly interfaces and customizable dashboards designed to simplify navigation and operation. Additionally, most providers offer robust support options, including training sessions, user manuals, and customer support, to help users become proficient with the system.
Change management is also a critical factor. To ensure a smooth transition to a new CMMS, involve key stakeholders early in the process and communicate the benefits clearly. Provide comprehensive training to staff and establish a phased implementation plan to address potential issues gradually. By managing these concerns proactively, organizations can facilitate a successful CMMS adoption and realize its full benefits.
Conclusion
In summary, a Computerized Maintenance Management System (CMMS) is essential for optimizing equipment uptime and ensuring regulatory compliance in pharmaceutical manufacturing. By facilitating preventive maintenance and predictive maintenance, automating record-keeping, and simplifying audits, CMMS addresses key challenges and enhances operational efficiency. Pharmaceutical manufacturers are encouraged to adopt CMMS to reap these benefits and achieve long-term improvements in both equipment performance and compliance. As Peter Drucker aptly put it, "The best way to predict the future is to create it." Embracing CMMS not only safeguards current operations but also paves the way for future success in an ever-evolving industry.
TABLE OF CONTENTS
Keep Reading
Imagine you're going through a compliance audit, and the inspector asks for maintenance ...
10 Jul 2025
Maintenance managers understand that disasters are unpredictable and can have a massive ...
4 Jul 2025
Asset lifespan is a key concern for executives and maintenance and facility management teams. ...
3 Jul 2025
Your company recently invested funds and time for new CMMS software, and six months later, it ...
1 Jul 2025
As Computerized Maintenance Management Systems (CMMS) become more connected and cloud-based, ...
1 Jul 2025
Edge computing is an innovative technology that enables data to be processed at the source, ...
24 Jun 2025
Facility management has undergone a significant transformation in recent times. Take, for ...
20 Jun 2025
A facility maintenance plan is at the core of a facility’s operations. This organized ...
19 Jun 2025
In the early days, preventive maintenance could be done effectively with a trained eye and a ...
17 Jun 2025
Sticky notes fall off, whiteboard grids get wiped, and spreadsheets never beep when a ...
13 Jun 2025
Handing a slice of your maintenance workload to a contractor is less about “giving up ...
12 Jun 2025
Downtime in enterprise environments doesn’t just mean a stop in operations; it means lost ...
10 Jun 2025
Understanding equipment functionality is crucial for effective repairs. A clear, systematic ...
6 Jun 2025
Maintenance managers know that every unplanned equipment failure is more than a simple ...
5 Jun 2025
What keeps a facility running smoothly? Initially, many of us may zoom in on its equipment, ...
29 May 2025
In today's digital world, every decision needs to pass the test of strategic and operational ...
27 May 2025
The business world is very different from a decade ago. Technological advancements have grown ...
23 May 2025
Picture this: a maintenance technician inspects a complex pump system. Instead of typing a ...
20 May 2025
For most of the 20th century, maintenance teams mainly applied a reactive approach to ...
9 May 2025
Imagine visiting a manufacturing plant where maintenance technicians gather around a large ...
8 May 2025