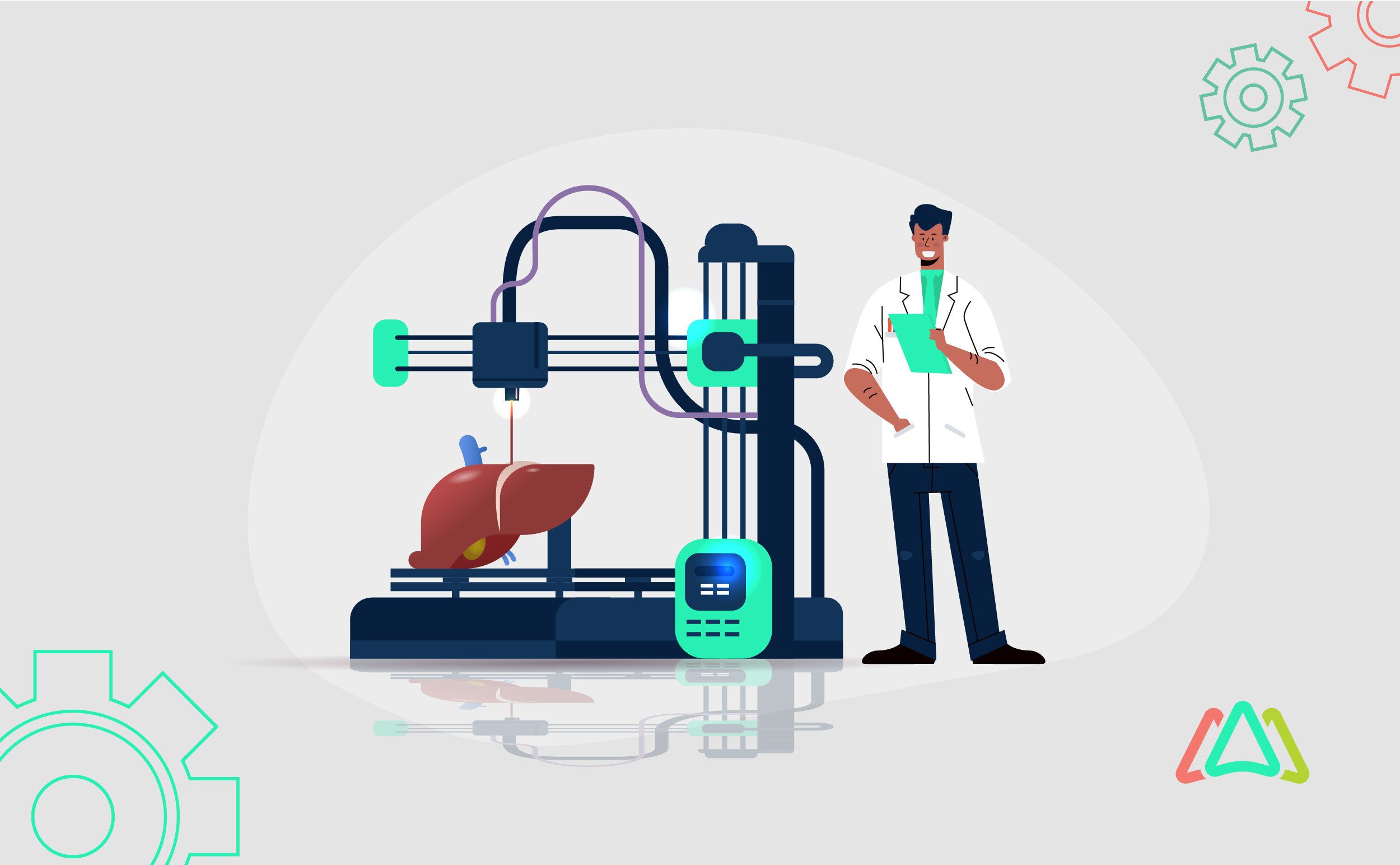
The Role of Additive Manufacturing in the Production of Medical Devices
As with much of the production of many products, Additive Manufacturing (AM) is being used to optimize the manufacturing of medical devices. This groundbreaking technology, also known as 3D printing, allows manufacturers to create highly customized medical devices tailored to individual patient needs. From prosthetics to implants, additive manufacturing is transforming the healthcare landscape, offering unprecedented levels of customization and precision.
This article delves into the remarkable advancements made possible through additive manufacturing in the medical field, examining its impact on patient outcomes, cost-effectiveness, and the future of healthcare.
Introduction to Additive Manufacturing
Additive manufacturing, also known as 3D printing, is revolutionizing the medical device manufacturing industry. This innovative technology allows for the layer-by-layer construction of three-dimensional objects from digital designs. Unlike traditional manufacturing methods, additive manufacturing offers unprecedented flexibility in creating complex, customized medical devices.
Key Advantages
- Precision: Additive manufacturing enables the production of intricate designs with high accuracy.
- Customization: Each device can be tailored to a patient's unique anatomy.
- Cost-effectiveness: Reduced waste and the ability to produce products on-demand at lower production costs.
Applications in Healthcare
Additive manufacturing is transforming various areas of medicine, from orthopedics to dentistry. It's particularly valuable in creating patient-specific implants, prosthetics, and surgical guides, enhancing treatment outcomes and patient comfort.
The Rise of Additive Manufacturing in Healthcare
Over the past decade, additive manufacturing has seen exponential growth in healthcare applications. According to a report by MarketsandMarkets, the medical devices 3D printing market is expected to grow from USD 2.7 billion in 2022 to USD 6.9 billion by 2028, at a compound annual growth rate (CAGR) of 17.1%. This rapid adoption is driven by the increasing demand for personalized healthcare solutions and advancements in 3D printing technology - aptly complemented by the precise tailoring of implants, prosthetics, and other devices to each patient's unique anatomy, significantly improving comfort and functionality.
Refined Clinical Results
Customized medical devices improve patient outcomes by enhancing comfort, reducing the risk of complications, and speeding up recovery times. For instance, a study published by the Journal of Orthopaedic Surgery and Research found that patient-specific 3D-printed implants resulted in fewer postoperative complications and higher patient satisfaction compared to off-the-shelf devices.
Cost Efficiency and Production Speed
3D printing streamlines the production process, reducing material waste and labor costs. It enables rapid prototyping and on-demand manufacturing, allowing healthcare providers to produce devices quickly and efficiently. This speed is particularly crucial in emergency situations where custom devices are needed urgently.
Regulatory Challenges and the Road Ahead
As additive manufacturing in healthcare advances, regulatory bodies are adapting to ensure safety and efficacy. The U.S. Food and Drug Administration (FDA) has issued guidance on 3D-printed medical devices, paving the way for wider adoption. However, challenges remain in standardizing processes and validating long-term performance of these innovative devices.
Looking ahead, the integration of advanced materials, AI-driven design, and further improvements in biocompatibility will expand the range of 3D-printed devices, particularly in bioprinting, where living tissues and organs are being developed.
Rapid Adoption of Additive Manufacturing in Healthcare Solutions
Customization: A Game-Changer for Medical Devices
Customization is the core advantage that additive manufacturing brings to medical devices. Traditional manufacturing methods often produce devices in standardized shapes and sizes, which may not fit all patients optimally. AM allows manufacturers to create patient-specific devices, tailored to an individual’s anatomy or condition. This has transformed areas such as:
Prosthetics
With 3D printing, prosthetics can be custom-made to fit each patient’s unique physical structure, ensuring better comfort, functionality, and aesthetics. Organizations like Enable the Future are using 3D printing to create affordable, custom prosthetics for amputees.
Orthopedics
AM has facilitated the development of patient-specific implants for orthopedic surgeries, including knee and hip replacements. Custom implants reduce surgery time, improve fit, and enhance recovery. The Smith+Nephew VERILAST knee replacement system, for example, uses 3D printing technology to create customized joints.
Dental Devices
Dentists are now using AM to create customized crowns, bridges, and dental implants, significantly improving accuracy and reducing turnaround time. Align Technology’s Invisalign clear aligners are one of the most well-known 3D-printed dental products, produced to fit individual patient’s teeth.
Transforming Patient Care Through Personalization
Additive manufacturing is revolutionizing healthcare by enabling unprecedented customization of medical devices. This technology allows for the creation of tailor- made solutions that perfectly fit each patient's unique anatomy and needs. In prosthetics, 3D-printed limbs offer improved comfort and functionality, enhancing the quality of life for amputees. Orthopedic implants can now be designed to match a patient's bone structure precisely, leading to better outcomes and faster recovery times. In dentistry, additive manufacturing facilitates the production of custom- fitted crowns, bridges, and aligners, streamlining treatment processes and improving patient satisfaction. As this technology continues to evolve, it promises to unlock new possibilities in personalized healthcare, making medical devices more effective, comfortable, and accessible than ever before.
Benefits of Customization with 3D Printing in Healthcare
Enhanced Patient Outcomes
3D printing technology enables the creation of tailor-made medical devices that perfectly fit each patient's unique anatomy. This customization leads to improved comfort, faster recovery times, and reduced risk of complications. For example, personalized prosthetics and orthotic devices can significantly enhance mobility and quality of life for patients with limb differences.
Cost-Effective Solutions
While initial investment in 3D printing technology may be substantial, the long-term benefits often outweigh the costs. Customized devices can reduce the need for multiple fittings or revisions, ultimately saving time and resources. Additionally, on- demand production minimizes inventory costs and waste, making healthcare more efficient and sustainable.
Accelerated Innovation
The flexibility of additive manufacturing allows for rapid prototyping and iteration in medical device design. This accelerates the development of new, innovative solutions to complex medical challenges, potentially revolutionizing patient care across various specialties.
Applications of 3D Printing in Medical Devices
Customized Implants and Prosthetics
3D printing revolutionizes the creation of personalized medical devices. Using patient-specific data, manufacturers can produce tailor-made implants and prosthetics that perfectly fit an individual's anatomy. This precision enhances comfort, functionality, and overall patient outcomes.
Surgical Planning and Training
Additive manufacturing enables the production of accurate anatomical models for pre-surgical planning. Surgeons can practice complex procedures on 3D-printed replicas, reducing operating time and improving success rates. These models also serve as valuable educational tools for medical students and residents.
Dental Applications
In dentistry, 3D printing facilitates the rapid production of custom dental implants, crowns, and aligners. This technology streamlines the fabrication process, reducing patient wait times and improving the accuracy of dental restorations.
Challenges and Limitations
While the potential is vast, complications remain in regulatory approval, material biocompatibility, and scaling production. However, as these hurdles are overcome, 3D printing will likely become an integral part of healthcare, ushering in a new era of personalized medicine and improved patient care.
Regulatory Hurdles
Despite its potential, additive manufacturing in medical devices faces significant regulatory challenges. The FDA's stringent approval process for custom devices can be time-consuming and costly, potentially slowing innovation. Ensuring consistent quality and safety standards across 3D-printed products remains a critical concern for regulatory bodies.
Technical Constraints
While 3D printing offers unprecedented customization, it also has limitations. Certain materials may not be suitable for medical use, and achieving the necessary precision for intricate devices can be challenging. Additionally, the production speed of additive manufacturing may not always meet urgent medical needs, especially for large-scale production.
Cost Considerations
Though customization brings benefits, it often comes at a higher price point. The initial investment in 3D printing technology and specialized materials can be substantial, potentially limiting accessibility for smaller healthcare providers or patients in resource-constrained settings.
Benefits for Patients and Surgeons
The advantages of custom surgical guides extend beyond the operating room. Patients experience faster recovery times and decreased risk of complications. Surgeons benefit from increased confidence and reduced stress during complex procedures. One orthopedic center reported a 30% decrease in revision surgeries after implementing custom guides for hip replacements, highlighting the significant impact of this additive manufacturing application.
Case Studies of Additive Manufacturing in Healthcare
Custom Surgical Guides: Revolutionizing Orthopedic Procedures
Custom surgical guides, created through additive manufacturing, are transforming orthopedic surgeries. These patient-specific tools enhance precision and reduce operating time, leading to improved outcomes. For example, according to an analysis of 32 studies overall, the use of 3D-printed anatomical models in surgery reduced time by an average of 62 minutes. Meanwhile, 3D-printed surgical guides saved, on average, 23 minutes in the operating room.
Personalized Prosthetics
Additive manufacturing has revolutionized the production of custom prosthetics. In a notable case, a young amputee received a 3D-printed prosthetic arm designed to grow with her, significantly improving her quality of life. This approach reduced costs by 90% compared to traditional methods.
Customized Implants
Another groundbreaking application involves patient-specific implants. A team at NYU Langone Health successfully created a 3D-printed tracheal splint for a newborn with a life-threatening airway disorder. The customized implant, perfectly tailored to the infant's anatomy, allowed for normal growth and breathing.
Surgical Planning Models
3D-printed anatomical models have proven invaluable in complex surgeries. In a high-profile case, surgeons used a precise 3D-printed model to plan and practice a delicate spinal surgery, resulting in a successful outcome for a patient with a rare spinal deformity.
The Future of 3D Printing in Healthcare
Revolutionizing Patient Care
As additive manufacturing technology advances, its potential to transform healthcare is immense. 3D printing is poised to revolutionize patient care by enabling the rapid production of customized medical devices, prosthetics, and even bio-printed tissues. This technology allows for unprecedented personalization, improving patient outcomes and quality of life.
Emerging Applications
The future holds exciting possibilities for 3D printing in medicine. Researchers are exploring bioprinting organs for transplantation, creating patient-specific drug delivery systems, and developing advanced surgical planning tools. These innovations promise to reduce healthcare costs, minimize surgical risks, and accelerate recovery times.
Conclusion
Additive manufacturing is revolutionizing the medical device industry through unprecedented customization capabilities. By embracing this technology, medical device manufacturers can provide patients with personalized solutions that dramatically improve outcomes and quality of life. The potential for innovation is limitless - from patient-specific implants to on-demand surgical tools. To stay competitive, it's crucial to integrate 3D printing into your product development and manufacturing processes. By partnering with additive manufacturing experts and investing in the right equipment, manufacturers will be well-positioned to deliver cutting-edge medical devices tailored to individual patient needs. The future of healthcare is personalized, and additive manufacturing is the key to unlocking its full potential.
Implementing a CMMS (Computerized Maintenance Management System) can support additive manufacturing initiatives by ensuring efficient equipment maintenance reducing downtime while ensuring regulatory compliance. Discover how Click Maint CMMS can support your medical device manufacturing processes with advanced preventive maintenance solutions.
TABLE OF CONTENTS
Keep Reading
Ever find yourself checking into a luxury hotel and expecting a relaxing stay, only to find a ...
11 Apr 2025
Organizations are witnessing swift changes in the business environment and confronting a ...
8 Apr 2025
Last month, news outlets and the entire internet was abuzz with the return of NASA astronauts ...
3 Apr 2025
What comes first - CMMS or predictive maintenance? If your answer is either, it is correct. ...
28 Mar 2025
Artificial intelligence (AI) talk has become commonplace. Today, engaging in business-focused ...
27 Mar 2025
Imagine a world where machines predict, diagnose, and fix their issues before they fail. This ...
25 Mar 2025
A facility maintenance plan is at the core of a facility’s operations. This organized ...
21 Mar 2025
Think of managing your maintenance operations like managing a championship sports team. Just ...
21 Mar 2025
The maintenance sector is battling a severe talent shortage that threatens to undermine ...
7 Mar 2025
Manufacturing maintenance is the backbone of industrial efficiency, ensuring machines run ...
5 Mar 2025
No one likes playing a guessing game when equipment breaks down. Yet, maintenance teams often ...
4 Mar 2025
The size of the preventive maintenance software market is discussed in millions of dollars, ...
4 Mar 2025
The organizational structure and corporate hierarchy vary from company to company. Large ...
28 Feb 2025
Maintenance procedures are essential for ensuring the longevity and reliability of machinery ...
21 Feb 2025
Sustainability is no longer just a buzzword; it's a critical component of corporate social ...
20 Feb 2025
A Computerized Maintenance Management System (CMMS) relies on accurate, well-organized data ...
18 Feb 2025
In an era where technology drives operational efficiency, Computerized Maintenance Management ...
14 Feb 2025
A Computerized Maintenance Management System (CMMS) is a key component of modern maintenance ...
13 Feb 2025
Introduction Maintenance management is the foundation of maintenance operations in industries ...
11 Feb 2025
Introduction A Computerized Maintenance Management System (CMMS) is software designed to help ...
7 Feb 2025