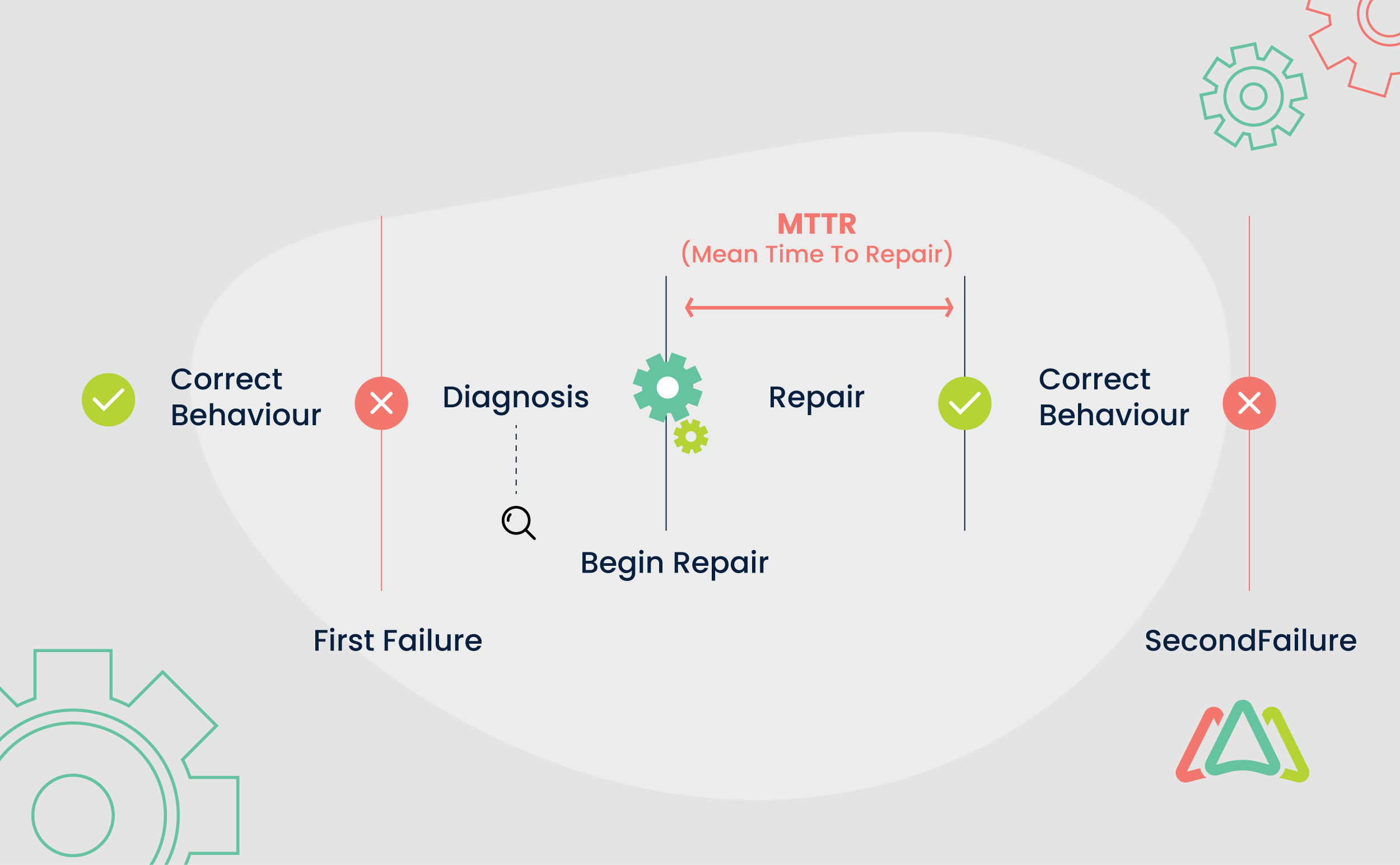
Understanding Mean Time to Repair (MTTR) for Optimal Maintenance
Mean Time To Repair (MTTR) Calculator
MTTR = (Total Downtime) / (Number of Repairs)
Happy with the result? If not, we could help.
Maintenance management ensures the smooth operation of any organization, be it a manufacturing facility, a data center, or a fleet of vehicles. It's the backbone that keeps everything running smoothly. Within maintenance management, Mean Time to Repair or MTTR is an important metric that determines how efficiently operations are running.
MTTR is the measure of an organization’s maintenance efficiency. It tells how swiftly the maintenance team can get things back on track when something goes wrong. The lower the MTTR, the fasterr the organization can recover from unexpected equipment failures, reduce downtime, and minimize the associated costs.
Why does MTTR matter so much in maintenance management?
The answer lies in its direct impact on an organization's operational efficiency and bottom line. Here are a few reasons why MTTR is important:
1. Minimizing Downtime
Downtime is costly. It leads to production delays, lost revenue, and frustrated customers. A shorter MTTR means less downtime, which, in turn, translates to more productivity and revenue.
2. Optimizing Resource Allocation
Understanding MTTR helps in allocating resources more effectively. Maintenance managers can schedule maintenance tasks, assign the right technicians, and stock the necessary spare parts more effectively knowing the MTTR, thereby reducing unnecessary costs.
3. Enhancing Equipment Reliability
A focus on reducing MTTR often leads to more reliable equipment. This can prolong the lifespan of assets, reducing the need for premature replacements.
4. Improving Customer Satisfaction
In industries such as healthcare and hospitality where downtime affects customer service or patient care, a lower MTTR ensures that customers experience fewer disruptions, leading to higher customer satisfaction.
What is Mean Time to Repair (MTTR)?
Mean Time to Repair (MTTR) is a measure that quantifies the average time it takes to restore a piece of equipment or system to its operational state after a failure or breakdown. Essentially, MTTR reflects the efficiency of your maintenance team in responding to and resolving unplanned maintenance issues.
Imagine a manufacturing facility where a machine suddenly breaks down. MTTR provides insights into how quickly that machine can be brought back online, minimizing production disruptions and associated costs. It encompasses various stages, from detecting the problem to diagnosing it, obtaining any necessary spare parts, and completing the repair.
Components of MTTR
MTTR can be broken down into three distinct components, each contributing to the overall time it takes to restore a piece of equipment or system:
1. Detection Time
This is the duration between the moment a problem occurs or a failure is reported and the moment it is detected by your maintenance team. Detecting issues swiftly is crucial, as it allows for a faster response and minimizes the overall MTTR.
2. Diagnostic Time
Once the issue is detected, your team must diagnose the problem to determine its root cause accurately. This phase involves troubleshooting, testing, and analyzing the equipment or system to pinpoint the issue. Reducing diagnostic time is dependent on the expertise of your technicians and the availability of diagnostic tools.
3. Repair Time
Repair time is the actual time it takes to fix the problem and restore the equipment to operational status. It encompasses tasks such as replacing faulty components or parts, calibrating systems, and performing any necessary maintenance or adjustments. Reducing repair time can significantly impact overall MTTR and downtime.
Understanding these individual components of MTTR allows maintenance managers to identify areas for improvement in their maintenance processes.
MTTR Formula and Calculation
Calculating MTTR is relatively straightforward and involves a simple mathematical formula:
MTTR = (Total Downtime) / (Number of Repairs)
Here's how it works:
- Total Downtime: This represents the cumulative amount of time that equipment or systems are not operational due to maintenance-related issues. It includes the time from when the problem is first detected until the equipment is fully repaired and functioning as intended.
- Number of Repairs: This indicates how many instances of repairs or unplanned maintenance interventions have occurred during a specified period.
Dividing the total downtime by the number of repairs gives the Mean Time to Repair. This figure provides a clear and quantifiable measure of the maintenance team's efficiency in resolving equipment failures.
Try calculating MTTR for your maintenance operation:
Mean Time To Repair (MTTR) Calculator
MTTR = (Total Downtime) / (Number of Repairs)
Happy with the result? If not, we could help.
How to make the most of the MTTR Calculator:
- Calculate MTTR regularly to track changes in repair performance over time. Frequent assessments can help identify trends and areas for improvement.
- MTTR should only consider unplanned downtime and repairs. Exclude any scheduled maintenance activities or planned downtime from your calculations.
- MTTR can be calculated for a single asset or a group of assets. Determine the scope of what you want to measure with MTTR. Are you calculating it for specific equipment, an entire department, or the organization as a whole? Define the scope in advance.
- If you notice a consistent increase in MTTR, conduct root cause analysis to identify the reasons behind prolonged repair times. Addressing these root causes can lead to shorter repair times.
- Maintain a historical record of MTTR calculations in your CMMS to monitor trends and performance over time. Historical data helps with trend analysis and decision-making.
- Compare your calculated MTTR values with industry benchmarks and organization's historical data if available.
Relationship Between MTTR and Downtime
MTTR and downtime are intricately connected:
1. Direct Correlation
A shorter MTTR means less downtime, while a longer MTTR results in more extended periods of equipment inactivity.
2. Financial Implications
Downtime carries substantial financial implications, including lost revenue, increased labor costs, and potential penalties for service-level agreements not met. An organization's ability to minimize these costs is closely tied to how well it controls MTTR.
3. Operational Stability
Maintaining a low MTTR ensures operational stability. Unplanned downtime has ripple effects throughout an organization, affecting supply chains, production schedules, and customer commitments. A well-managed MTTR helps safeguard against these disruptions.
Factors Affecting MTTR
Mean Time to Repair (MTTR) is not a static number. Many factors can influence it, either positively or negatively. The following are key factors that affect MTTR:
1. Equipment Complexity & Documentation
The complexity of the equipment or assets being maintained has a direct impact on MTTR. More sophisticated machinery often requires more time for diagnosis and repair due to intricate components and specialized knowledge. The availability and comprehensiveness of technical documentation, such as manuals and schematics, can significantly influence MTTR. Clear and easily accessible documentation can expedite troubleshooting and repairs.
2. Availability of Spare Parts
Maintaining an up-to-date and well-organized inventory of spare parts is important. Not having critical spare parts on hand can lead to extended downtime due to wait times on orders. The reliability of the suppliers in delivering spare parts on time can affect MTTR. Long lead times and delays in obtaining required parts can extend the repair process.
3. Technician Skills and Experience
The skill level and expertise of your maintenance technicians play a pivotal role in MTTR. Highly skilled technicians can diagnose and repair issues more efficiently. Regular training and development programs can enhance technician skills and keep them up-to-date with the latest equipment and best practices for repairs.
4. Maintenance Processes and Procedures
Standardizing maintenance processes and procedures can lead to shorter MTTR. When technicians follow consistent steps for diagnosis and repair, they work more efficiently. A structured approach to root cause analysis can prevent recurrent issues, ultimately reducing MTTR over the long term. Effective communication among maintenance team members, as well as with other departments, ensures a smoother workflow and faster issue resolution.
5. Preventive vs. Reactive Maintenance
Organizations that prioritize preventive maintenance tend to have lower MTTR. Regular inspections and maintenance activities help identify and address issues before they lead to critical failures. Relying solely on reactive maintenance, where maintenance is done only when equipment fails, often results in longer MTTR. This is because technicians are spending most of their time troubleshooting and diagnosing failures that could have been prevented. Reactive maintenance results in unnecessary downtime.
Improving Mean Time to Repair (MTTR)
Improving MTTR requires a holistic approach that addresses various aspects of the organization’s maintenance operations. The following are some actionable strategies to reduce MTTR and optimize maintenance processes:
1. Identifying Bottlenecks in the Maintenance Process
1.1 Root Cause Analysis
Start by analyzing historical data to identify recurring issues and their underlying causes. Understanding the root causes of frequent breakdowns can help organizations address them more effectively.
1.2 Workflow Assessment
Evaluate the flow of the maintenance process. Identify stages where delays or inefficiencies commonly occur. Pinpointing these bottlenecks enables maintenance professionals to focus their improvement efforts.
1.3 Team Feedback
Engage the maintenance team in discussions about their experiences and challenges. They often have valuable insights into where improvements can be made that may not be apparent through historical data analysis.
2. Investing in Technician Training and Skill Development
2.1 Continuous Learning
Provide ongoing training opportunities to technicians. This includes technical skills training, as well as soft skills like communication and problem-solving.
2.2 Certifications
Encourage technicians to obtain relevant certifications in their field. Certified technicians are often more proficient at diagnosing and repairing equipment.
2.3 Knowledge Sharing
Foster a culture of knowledge sharing within the maintenance team. Experienced technicians can mentor newer ones, passing on valuable insights and expertise.
3. Implement Predictive Maintenance Technologies
3.1 Sensor Technology
Utilize sensors and IoT devices to collect real-time data from your equipment. This data can be analyzed to predict when equipment is likely to fail, allowing for more proactive maintenance.
3.2 Predictive Maintenance Software
Invest in predictive maintenance technologies that can analyze data patterns and alert you to potential issues well before they become critical.
3.3 Condition Monitoring
Implement condition monitoring techniques to continuously assess the health of your equipment. This can help identify early warning signs of impending failures.
4. Inventory Management for Spare Parts
4.1 Just-In-Time Inventory
Adopt a just-in-time approach to spare parts management. Manage inventory cost by maintaining a balance between having critical parts on hand while not overstocking, which can tie up capital.
4.2 Supplier Relationships
Cultivate strong relationships with suppliers to ensure prompt delivery of spare parts. Consider vendor-managed inventory arrangements to streamline procurement.
4.3 Asset Criticality Analysis
Prioritize spare parts and inventory based on the criticality of assets. Use the equipment criticality assessment matrix to focus on keeping essential components and parts readily available.
5. Standardizing Maintenance Procedures
5.1 Create Maintenance SOPs
Develop standardized operating procedures (SOPs) for common maintenance tasks. These SOPs should outline the steps for diagnosis, repair, and documentation.
5.2 Checklists
Provide technicians with detailed checklists for each maintenance task. Preventive Maintenance checklists ensure that no steps are missed during maintenance, reducing errors and MTTR.
5.3 Continuous Improvement
Encourage feedback from technicians and incorporate their suggestions for procedure improvements. Regularly update procedures based on lessons learned.
Leveraging a CMMS for MTTR Improvement
Computerized Maintenance Management Systems (CMMS), are software solutions designed to facilitate and optimize maintenance management. These systems have evolved significantly over the years and now offer a wide range of features to support maintenance teams in their efforts to reduce MTTR and enhance overall operational efficiency.
Here's how a CMMS software contributes to MTTR improvement:
1. Asset Management
CMMS software provides a centralized database for managing all your assets, including equipment details, maintenance history, and documentation. Technicians can quickly access information about the equipment they are working on, aiding in faster diagnosis and repair.
2. Work Order Management
CMMS allows for the efficient creation, tracking, and assignment of work orders. When equipment issues arise, maintenance personnel can generate work orders promptly, with all the details documented making it easier and faster to complete the repair.
3. Preventive Maintenance Scheduling
CMMS enables maintenance planning and scheduling based on time or usage thresholds. This proactive approach helps prevent unexpected breakdowns, ultimately reducing MTTR.
4. Inventory and Spare Parts Management
Efficient inventory management is critical for reducing MTTR. CMMS systems can track spare parts and inventory levels, ensuring that necessary components are readily available for repairs. Further, if parts need to be ordered, many CMMS systems can help process purchase orders directly to suppliers.
5. Work Order Documentation
Maintenance technicians can document their work within the CMMS, recording details of repairs, parts used, and any additional notes. This documentation aids in future troubleshooting and maintains a historical record of maintenance activities.
6. Reporting and Analytics
CMMS software generates reports and provides analytical insights into maintenance performance. By analyzing these reports, organizations can identify patterns, spot recurring issues, and make data-driven decisions to further reduce MTTR. Many CMMS platforms provide MTTR metrics making it easy for managers to compare performance monthly, quarterly or annually and see how their team is improving over time.
7. Mobile Accessibility
Modern CMMS solutions offer work order apps, allowing technicians to access work orders, equipment details, and documentation while in the field. This mobility improves response times and MTTR significantly.
8. Integration Capabilities
CMMS integration allows other enterprise software, such as Enterprise Resource Planning (ERP) systems and IoT platforms to talk to the CMMS, further enhancing data sharing and more comprehensive reporting.
TABLE OF CONTENTS
Keep Reading
Ever find yourself checking into a luxury hotel and expecting a relaxing stay, only to find a ...
11 Apr 2025
Organizations are witnessing swift changes in the business environment and confronting a ...
8 Apr 2025
Last month, news outlets and the entire internet was abuzz with the return of NASA astronauts ...
3 Apr 2025
What comes first - CMMS or predictive maintenance? If your answer is either, it is correct. ...
28 Mar 2025
Artificial intelligence (AI) talk has become commonplace. Today, engaging in business-focused ...
27 Mar 2025
Imagine a world where machines predict, diagnose, and fix their issues before they fail. This ...
25 Mar 2025
A facility maintenance plan is at the core of a facility’s operations. This organized ...
21 Mar 2025
Think of managing your maintenance operations like managing a championship sports team. Just ...
21 Mar 2025
The maintenance sector is battling a severe talent shortage that threatens to undermine ...
7 Mar 2025
Manufacturing maintenance is the backbone of industrial efficiency, ensuring machines run ...
5 Mar 2025
No one likes playing a guessing game when equipment breaks down. Yet, maintenance teams often ...
4 Mar 2025
The size of the preventive maintenance software market is discussed in millions of dollars, ...
4 Mar 2025
The organizational structure and corporate hierarchy vary from company to company. Large ...
28 Feb 2025
Maintenance procedures are essential for ensuring the longevity and reliability of machinery ...
21 Feb 2025
Sustainability is no longer just a buzzword; it's a critical component of corporate social ...
20 Feb 2025
A Computerized Maintenance Management System (CMMS) relies on accurate, well-organized data ...
18 Feb 2025
In an era where technology drives operational efficiency, Computerized Maintenance Management ...
14 Feb 2025
A Computerized Maintenance Management System (CMMS) is a key component of modern maintenance ...
13 Feb 2025
Introduction Maintenance management is the foundation of maintenance operations in industries ...
11 Feb 2025
Introduction A Computerized Maintenance Management System (CMMS) is software designed to help ...
7 Feb 2025