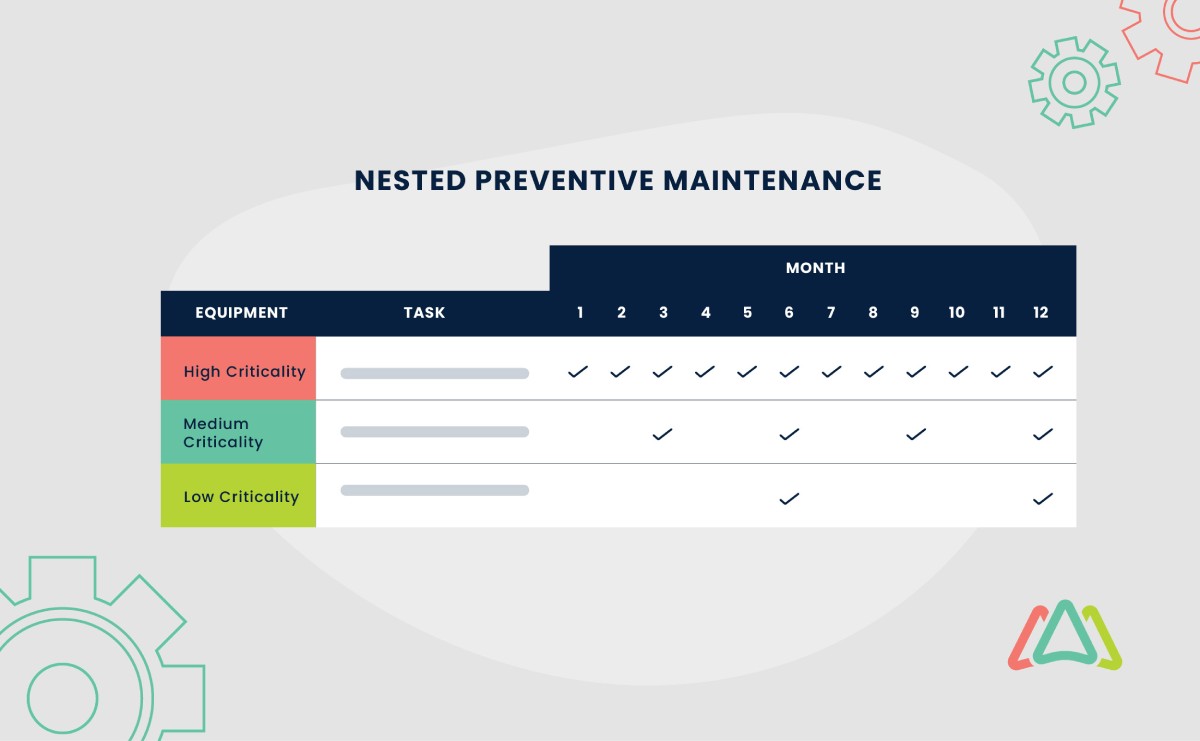
What is Nested Preventive Maintenance and What are the Benefits?
Preventive Maintenance lays the foundation for efficient equipment upkeep by proactively addressing potential issues before they escalate. Nested Preventive Maintenance takes this concept to the next level, introducing a strategic approach that categorizes equipment into nested levels based on criticality and assigns tailored maintenance tasks and intervals.
This approach allows organizations to allocate maintenance efforts more efficiently. High-criticality equipment may receive more frequent inspections and maintenance, while less critical assets can follow longer intervals, reducing the overall workload and costs. Nested PMs are especially relevant for organizations with extensive and diverse inventories of equipment, as it helps prioritize maintenance tasks and optimize resource allocation.
What is Nested Preventive Maintenance?
Nested Preventive Maintenance (Nested PM) is an advanced maintenance management strategy that takes the principles of traditional Preventive Maintenance to a higher level of efficiency and effectiveness. With Nested PM, equipment is organized into nested levels based on their criticality to the organization's operations. Each nested level is then assigned a unique maintenance plan, consisting of specific tasks and intervals tailored to the equipment's needs. This hierarchical approach enables businesses to optimize their maintenance efforts, focusing more resources on high-priority assets and reducing maintenance frequency for less critical assets.
How does Nested Preventive Maintenance Differ from Traditional Preventive Maintenance?
The key distinction between Nested Preventive Maintenance and traditional PM approaches lies in its approach to maintenance scheduling and task allocation. Traditional PM typically follows a one-size-fits-all approach, where all equipment undergoes the same maintenance tasks at fixed intervals, regardless of its criticality. This can lead to suboptimal resource allocation, with valuable time and effort expended on equipment that’s less critical, while critical assets may not receive adequate attention.
Nested preventive maintenance, on the other hand, acknowledges that not all equipment is equally critical to operations. By categorizing equipment into nested levels, it introduces a tiered maintenance structure that addresses the unique needs of each level. This approach ensures that the most critical equipment receives more frequent inspections and maintenance, while less critical equipment follows longer intervals. As a result, businesses can achieve a better balance between resource allocation and equipment performance, leading to increased efficiency and reduced downtime.
Step-by-Step Guide to Designing a Nested Preventive Maintenance Plan
Designing a Nested Preventive Maintenance (Nested PM) plan requires careful consideration and a structured approach. Here's a step-by-step guide to help you create an effective nested preventive maintenance plan:
Step 1: Assess Equipment Criticality and Priority
- Identify all the equipment and assets within the organization.
- Categorize the equipment based on their criticality to business operations.
- Determine which assets have a high impact on production, safety, and regulatory compliance, and which are less critical.
- Create a priority list, ranking the equipment from most critical to least critical.
Step 2: Define Nested Levels and Intervals
- Establish nested levels based on the priority list. High-criticality equipment will be placed in higher nested levels, while less critical assets will be in lower nested levels.
- Determine the maintenance intervals for each nested level. Factors to consider include equipment usage, manufacturer recommendations, historical maintenance data, and regulatory requirements.
Step 3: Identify Maintenance Tasks for Each Level
- Define the specific maintenance tasks that are relevant and necessary for each nested level of equipment.
- Tailor the tasks to address the unique needs and potential failure points of each asset. High-criticality equipment may require more comprehensive inspections and even condition-based monitoring, while less critical equipment may have simpler tasks.
Step 4: Create a Detailed Schedule and Checklist
- Develop a detailed maintenance schedule that outlines the frequency of inspections and maintenance activities for each asset in each nested level.
- Create checklists for each maintenance task, specifying the steps to be followed and any required tools or materials.
- Use a Computerized Maintenance Management System (CMMS) for help with scheduling and task management. A CMMS can send automated reminders for upcoming maintenance tasks, ensuring timely execution and record all activities so they can easily be reported on later.
Step 5: Implement the Plan and Train Personnel
- Communicate the Nested PM plan to all relevant personnel, including maintenance teams, equipment operators, and management. Ensure everyone understands the importance of Nested PM and the roles they play in order for it to be a success.
- Train maintenance personnel on the new maintenance tasks and procedures specific to each nested level. Provide them with the necessary resources and tools to carry out their duties effectively.
Step 6: Monitor and Improve
- Regularly monitor the performance of the Nested PM plan. Keep track of maintenance activities, equipment downtime, and any issues encountered during inspections.
- If available and applicable, use data collected from IoT sensors, predictive maintenance tools, and other technologies to inform decision-making and identify opportunities for improvement.
- Continuously review and update the Nested PM plan based on changing business needs, equipment performance data, and feedback from maintenance teams.
Below is the example of a comprehensive maintenance schedule for nested preventive maintenance for a manufacturing facility:
Factors to Consider in Developing a Nested PM Strategy
Developing a comprehensive Nested Preventive Maintenance (PM) strategy requires careful consideration of various factors that influence the effectiveness and efficiency of the maintenance plan. By understanding these factors, organizations can tailor their Nested PM approach to meet the specific needs of their equipment and operations. Here are four important factors to consider when developing a Nested PM strategy:
1. Equipment Complexity and Age
The complexity and age of equipment play an important role in determining its maintenance requirements. Older equipment may require more frequent inspections and maintenance due to wear and tear. Complex machinery with intricate components might demand specialized skills and thorough assessments. By categorizing equipment based on complexity and age, organizations can allocate appropriate resources and prioritize maintenance tasks accordingly in the Nested PM plan.
The Nested Preventive Maintenance Benefit
Nested preventive maintenance allows organizations to focus more attention on older or complex equipment, ensuring their reliability and performance. Critical equipment can receive more frequent inspections and preventive maintenance, reducing the risk of breakdowns and costly repairs.
2. Environmental and Operational Conditions
The environment in which equipment operates greatly impacts its maintenance needs. Harsh environmental conditions, such as extreme temperatures, humidity, dust, or exposure to corrosive substances, can accelerate equipment deterioration. Similarly, heavy usage and demanding operational conditions can increase wear on machinery. Understanding these factors enables the development of maintenance intervals and tasks that suit the equipment's specific operating environment.
The Nested Preventive Maintenance Benefit
Nested PM enables organizations to tailor maintenance schedules and tasks based on the equipment's exposure to environmental and operational stresses. This proactive approach helps extend equipment lifespan and reduce downtime due to environmental damage.
3. Manufacturer Recommendations and Warranty Requirements
Manufacturers often provide specific maintenance guidelines and warranty requirements for their equipment. Adhering to these recommendations ensures that the warranty remains valid and may lead to better equipment performance. Additionally, following manufacturer guidelines helps organizations avoid any actions that might void warranties and result in additional expenses.
The Nested Preventive Maintenance Benefit
Nested PM incorporates manufacturer recommendations into the maintenance plan, guiding maintenance personnel on best practices. By adhering to these guidelines, organizations can safeguard equipment warranty coverage and optimize performance.
4. Regulatory Compliance and Industry Standards
Compliance with regulatory requirements and industry standards is important for safe and efficient operations. Different industries may have specific regulations and standards related to equipment maintenance, safety, and environmental impact. A Nested PM strategy should align with these standards to ensure legal compliance and ethical business practices.
The Nested Preventive Maintenance Benefit
Nested PM enables organizations to assign appropriate maintenance frequencies and tasks to equipment to meet regulatory standards. Regular inspections and documentation facilitate compliance audits and promote a culture of safety and ethical operations.
3 Potential Challenges and Solutions
Implementing a Nested Preventive Maintenance strategy brings about numerous benefits, but it may also present some challenges that organizations need to address to ensure its success. Identifying and resolving these challenges will pave the way for a smooth and effective transition to nested preventive maintenance. The following are some common challenges and solutions:
1. Initial Implementation Costs and Resource Allocation
Challenge
Upfront costs associated with implementing Nested PM, such as acquiring condition monitoring equipment, investing in maintenance software, and training personnel, can be significant. Organizations may also face challenges in allocating sufficient resources to kickstart the program.
Solution
To overcome this challenge, organizations should conduct a cost-benefit analysis to demonstrate the long-term advantages of Nested PM. Highlighting the potential cost savings, reduced downtime, and extended equipment lifespan can garner support from stakeholders. Getting funding from senior management or exploring financing options can help in securing the necessary resources for implementation.
2. Data Management and Analysis for Nested PM
Challenge
Nested PM generates a vast amount of data from various equipment inspections, condition monitoring, and maintenance tasks. Managing and analyzing this data efficiently can be challenging, especially if the organization lacks the necessary data management tools and expertise.
Solution
Implement a robust Computerized Maintenance Management System (CMMS) or Enterprise Asset Management (EAM) software to streamline data management. These systems help in organizing maintenance data, scheduling tasks, and generating reports for analysis. Data analytics tools can assist in identifying patterns and trends, enabling predictive maintenance to prevent equipment failures proactively.
3. Overcoming Resistance to Change and Embracing a Proactive Maintenance Culture
Challenge
Shifting from a traditional preventive maintenance approach to Nested PM requires a cultural change within the organization. Resistance to change from maintenance teams can be a problem that needs to be confronted in order for the new approach to succeed..
Solution
Involve maintenance personnel in the decision-making process to foster a sense of ownership and commitment. Implementing a gradual transition, starting with a pilot project, allows the organization to showcase the positive outcomes of applying nested preventive maintenance. Recognition and rewards for proactive maintenance practices can encourage a culture that embraces change and continuous improvement.
Embracing Nested Preventive Maintenance
Nested Preventive Maintenance is not just a buzzword; it is a transformative approach that challenges traditional notions of one-size-fits-all maintenance strategies. By aligning maintenance efforts with equipment importance, nested preventive maintenance ensures that resources are deployed where they matter most, maximizing reliability, and minimizing operational disruptions.
Nested preventive maintenance empowers organizations to tailor maintenance practices precisely, nurturing equipment to perform at its peak capacity. Applying nested preventive maintenance is not just limited to manufacturing. Its benefits extend to a variety of industries like healthcare, higher education, energy and utilities, government entities and more. Adoption requires planning and change, but the rewards in many cases are well worth the time and effort.
TABLE OF CONTENTS
Keep Reading
Ever find yourself checking into a luxury hotel and expecting a relaxing stay, only to find a ...
11 Apr 2025
Organizations are witnessing swift changes in the business environment and confronting a ...
8 Apr 2025
Last month, news outlets and the entire internet was abuzz with the return of NASA astronauts ...
3 Apr 2025
What comes first - CMMS or predictive maintenance? If your answer is either, it is correct. ...
28 Mar 2025
Artificial intelligence (AI) talk has become commonplace. Today, engaging in business-focused ...
27 Mar 2025
Imagine a world where machines predict, diagnose, and fix their issues before they fail. This ...
25 Mar 2025
A facility maintenance plan is at the core of a facility’s operations. This organized ...
21 Mar 2025
Think of managing your maintenance operations like managing a championship sports team. Just ...
21 Mar 2025
The maintenance sector is battling a severe talent shortage that threatens to undermine ...
7 Mar 2025
Manufacturing maintenance is the backbone of industrial efficiency, ensuring machines run ...
5 Mar 2025
No one likes playing a guessing game when equipment breaks down. Yet, maintenance teams often ...
4 Mar 2025
The size of the preventive maintenance software market is discussed in millions of dollars, ...
4 Mar 2025
The organizational structure and corporate hierarchy vary from company to company. Large ...
28 Feb 2025
Maintenance procedures are essential for ensuring the longevity and reliability of machinery ...
21 Feb 2025
Sustainability is no longer just a buzzword; it's a critical component of corporate social ...
20 Feb 2025
A Computerized Maintenance Management System (CMMS) relies on accurate, well-organized data ...
18 Feb 2025
In an era where technology drives operational efficiency, Computerized Maintenance Management ...
14 Feb 2025
A Computerized Maintenance Management System (CMMS) is a key component of modern maintenance ...
13 Feb 2025
Introduction Maintenance management is the foundation of maintenance operations in industries ...
11 Feb 2025
Introduction A Computerized Maintenance Management System (CMMS) is software designed to help ...
7 Feb 2025