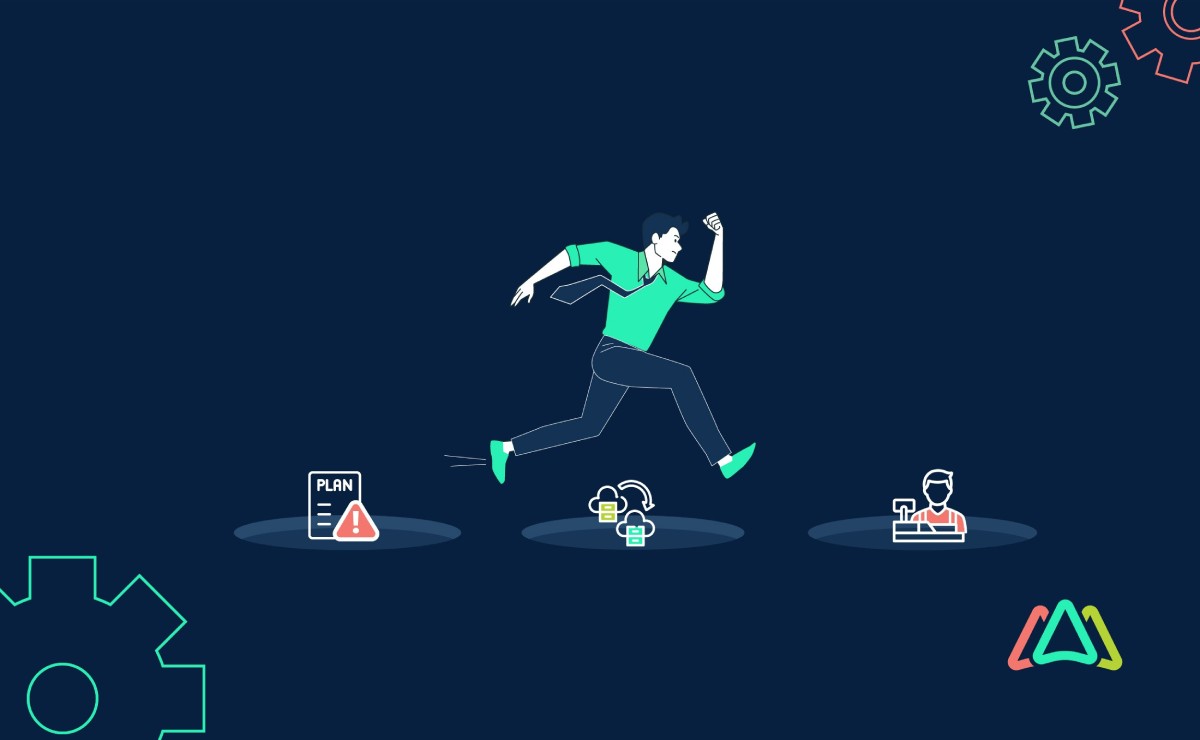
5 CMMS Implementation Pitfalls & Ways to Avoid Them
Introduction
As more businesses implement Computerized Maintenance Management Systems (CMMS), maintenance and facilities professionals expect bigger returns and value. Factors driving demand for CMMS are the competitive and often tenuous economic climate. Maintenance professionals recognize the software’s ability to enhance operational efficiency and asset management. This is attractive to companies wanting to increase their margins and sharpen their bottom line. Its ability to schedule maintenance, reduce downtime, and extend the lifespan of equipment offers a path for organizations to achieve these goals. Overall, the prospect of increased productivity, reduced operational costs, and enhanced asset reliability make adopting a CMMS an exciting proposition for businesses aiming to elevate their maintenance practices.
Yet despite all the good reasons businesses have for moving forward with a CMMS, many embrace unrealistic expectations by expecting the software to be an instantaneous panacea for all their operational challenges. Unrealistic expectations can lead to disappointment. CMMS is a tool but not a magic bullet. Instead, long-term success requires a realistic understanding of their capabilities, proper implementation, and planning, decision-making, training, and utilization.
5 Common CMMS Implementation Pitfalls
CMMS implementation can be complex. In fact, studies have shown that CMMS implementation failure rates range from 50-70%, depending on the source. The good news is implementation failure is avoidable. The purpose of this article is to highlight five pitfalls that commonly arise during implementation and provide ways to avoid them.
Insufficient Planning:
Proper planning is crucial when investing in a CMMS software because it will ensure that the software chosen will be the one that offers the most significant potential for an organization once it is successfully implemented. Moreover, it sets the blueprint for how a company will move forward in its maintenance operations. Effective planning involves understanding an organization's maintenance needs, establishing clear objectives, and aligning the CMMS capabilities with its overall business goals. The best chance of success happens when the planning phase is more comprehensive. It requires identifying key stakeholders, allocating resources, and establishing a realistic timeline for implementation. Thorough planning is multi-pronged by developing data migration strategies, staff training programs, and integration with existing systems, ensuring a smooth transition and minimizing disruptions to daily operations. By investing time and effort in meticulous planning, organizations can optimize the benefits of their CMMS, streamline maintenance processes, improve asset reliability, and ultimately enhance operational efficiency and cost-effectiveness. Poor planning can occur when organizations fail to pay more attention to the complexity of CMMS implementation or the need to allocate more time and resources for planning.
How to avoid planning pitfalls:
Mistakes during this vital planning stage can be avoided when organizations:
- Conduct a thorough assessment of organizational needs and requirements before selecting a CMMS.
- Develop a comprehensive project plan with a realistic timeline, budget, and resource allocation.
- Involve key stakeholders from various departments in considering all relevant perspectives of the planning phase.
Inadequate Data Migration:
Proper CMMS data migration is crucial when implementing a CMMS because it is pivotal in ensuring the seamless transition and accurate representation of historical and operational data. As is the case with any software, when errors occur during this vital stage, it cannot be expected to perform as it should. A CMMS can only be as good as the data it is fed. The phrase “garbage in / garbage out” makes this point.
More specifically, a CMMS relies heavily on comprehensive and reliable information about an organization’s assets, maintenance schedules, work orders, and other critical aspects of the maintenance process. Effective data migration involves transferring existing data into the new system and preventing data loss, inconsistencies, or inaccuracies that could compromise the integrity of the CMMS. A successful data migration strategy is fundamental for successfully integrating a CMMS, ensuring that the system functions as intended based on complete and error-free data and delivers the expected benefits to the organization. Unfortunately, the software will fail to perform as designed when organizations do not recognize the importance of accurate and complete data migration from existing systems to the new CMMS.
How to avoid data migration errors or inadequacies:
Critical mistakes during the data migration phase can be avoided when organizations:
- Prioritize data cleansing and validation before migration to ensure data accuracy.
- Develop a detailed data migration plan and test the migration process in a controlled environment before going live.
- Work closely with the CMMS provider and get advice on best practices for data collection, use their import templates, and involve them in the process (don’t go at it alone).
- Provide adequate training for personnel involved in the data migration process.
Lack of User Training:
CMMS training is crucial for several reasons. To begin, practical training ensures that users, primarily maintenance personnel and facility managers, can maximize the utilization of the CMMS software. Well-trained personnel can unlock the software’s full potential in streamlining maintenance processes and optimizing equipment management. Proper training enhances users' proficiency in navigating the system, inputting data accurately, and interpreting the generated reports. These proficiencies reduce the risk of errors and improve overall data integrity. Effectively trained users are better equipped to troubleshoot issues, increasing the system's reliability and minimizing downtime. Besides these practical elements, CMMS training helps to promote a culture of accountability and collaboration, as team members are more likely to share a common understanding of procedures and best practices. Investing in comprehensive CMMS user training results in increased efficiency, cost savings, and improved maintenance outcomes for organizations across various industries. Inadequate training is a common pitfall when organizations assume users will quickly adapt to the new system without proper guidance.
How to avoid user-training pitfalls:
Inadequate user training can have far-reaching consequences, including improper use of the CMMS software, unnecessary errors, and users’ reluctance to use it routinely. These pitfalls can be avoided when organizations:
- Work directly with the CMMS provider to get access to all available training resources. Most software providers will have webinars, videos, and articles that are easily accessible (24/7). Make sure all users know how to access these resources.
- Develop a comprehensive training program for end-users at all levels.
- Customize training sessions based on different user roles and their specific needs within the CMMS.
- Address post-implementation challenges and provide ongoing support and resources like user manuals and tutorials.
Resistance to Change:
Resistance to change refers to the challenges and obstacles that organizations may encounter when implementing or transitioning to a new CMMS software or making significant changes to an existing system. It can manifest in various forms, including employee reluctance to adopt new technology, lack of understanding or training on the new system, fear of job displacement, and ingrained habits associated with traditional maintenance practices. Employees may resist adopting new technologies due to fear of the unknown, concerns about job security, or a need for more understanding about the benefits of the CMMS. Resistant employees often prefer to stay with a way of doing things they feel most comfortable with. This is akin to the belief, “Why fix what isn’t broken.” Successfully addressing resistance is crucial for organizations to fully realize the potential advantages of CMMS and streamline their maintenance processes.
How to avoid resistance to change pitfalls:
The consequences of user resistance to change must be considered. This particular pitfall can be avoided when organizations:
- Communicate the benefits of the CMMS clearly to all stakeholders.
- Involve employees in the decision-making process and address their concerns proactively.
- Implement a change management strategy that includes regular communication, feedback mechanisms, and incentives for embracing the new system.
- Incentivize and reward users for adopting the CMMS.
Inadequate Vendor Support:
A CMMS is a sophisticated and powerful tool designed to streamline a company’s maintenance operations. At the same time, these systems aren’t always “plug and play.” On the contrary, successful implementation requires time and resources to implement appropriately so that the software can achieve the many benefits it offers. Additional support often depends on an organization’s existing maintenance management framework. Furthermore, CMMS customers usually require assistance with troubleshooting, upgrades, expansions, and other support-related issues. This is when vendor support is vital to the software’s long-term viability and customer satisfaction.
Inadequate vendor support occurs when the provider fails to meet its customers' expectations and requirements regarding training, technical support, troubleshooting, and resolution of issues. It also presents itself in delayed response times, lack of expertise in addressing complex problems, insufficient documentation, or general unresponsiveness to customer queries. Inadequate vendor support can lead to frustration, prolonged downtime, and potential disruptions to business operations. Having to struggle with unresolved issues leaves company owners feeling unsupported and questioning the value of their investment in a vendor's products or services.
How to avoid inadequate vendor support:
A CMMS represents a commitment in money, time, and resources. Although vendor support may not be the first item on a buyer’s checklist, it should not be overlooked. Inadequate vendor support can be avoided when organizations:
- Select a reputable vendor with a track record of successful implementations and ongoing support. User reviews and customer references are great ways to verify if the CMMS provider delivers a high level of support.
- Determine upfront if there are additional costs for vendor support and, if so, what the terms are.
- Clearly define expectations for support services in the contract.
- Establish a communication channel with the vendor and ensure a responsive support system is in place for promptly addressing issues.
Conclusion
CMMS software offers an exciting opportunity to scale up an organization’s maintenance management operations. Because of its financial outlay, time, and resource cost, selecting the right CMMS for your organization requires some planning and due diligence. Frustration and dissatisfaction can be avoided by addressing the common pitfalls through careful planning, comprehensive training, effective communication, and collaboration with a reliable vendor. By paying careful attention to these issues, organizations can increase the likelihood of a successful CMMS implementation.
TABLE OF CONTENTS
Keep Reading
Ever find yourself checking into a luxury hotel and expecting a relaxing stay, only to find a ...
11 Apr 2025
Organizations are witnessing swift changes in the business environment and confronting a ...
8 Apr 2025
Last month, news outlets and the entire internet was abuzz with the return of NASA astronauts ...
3 Apr 2025
What comes first - CMMS or predictive maintenance? If your answer is either, it is correct. ...
28 Mar 2025
Artificial intelligence (AI) talk has become commonplace. Today, engaging in business-focused ...
27 Mar 2025
Imagine a world where machines predict, diagnose, and fix their issues before they fail. This ...
25 Mar 2025
A facility maintenance plan is at the core of a facility’s operations. This organized ...
21 Mar 2025
Think of managing your maintenance operations like managing a championship sports team. Just ...
21 Mar 2025
The maintenance sector is battling a severe talent shortage that threatens to undermine ...
7 Mar 2025
Manufacturing maintenance is the backbone of industrial efficiency, ensuring machines run ...
5 Mar 2025
No one likes playing a guessing game when equipment breaks down. Yet, maintenance teams often ...
4 Mar 2025
The size of the preventive maintenance software market is discussed in millions of dollars, ...
4 Mar 2025
The organizational structure and corporate hierarchy vary from company to company. Large ...
28 Feb 2025
Maintenance procedures are essential for ensuring the longevity and reliability of machinery ...
21 Feb 2025
Sustainability is no longer just a buzzword; it's a critical component of corporate social ...
20 Feb 2025
A Computerized Maintenance Management System (CMMS) relies on accurate, well-organized data ...
18 Feb 2025
In an era where technology drives operational efficiency, Computerized Maintenance Management ...
14 Feb 2025
A Computerized Maintenance Management System (CMMS) is a key component of modern maintenance ...
13 Feb 2025
Introduction Maintenance management is the foundation of maintenance operations in industries ...
11 Feb 2025
Introduction A Computerized Maintenance Management System (CMMS) is software designed to help ...
7 Feb 2025