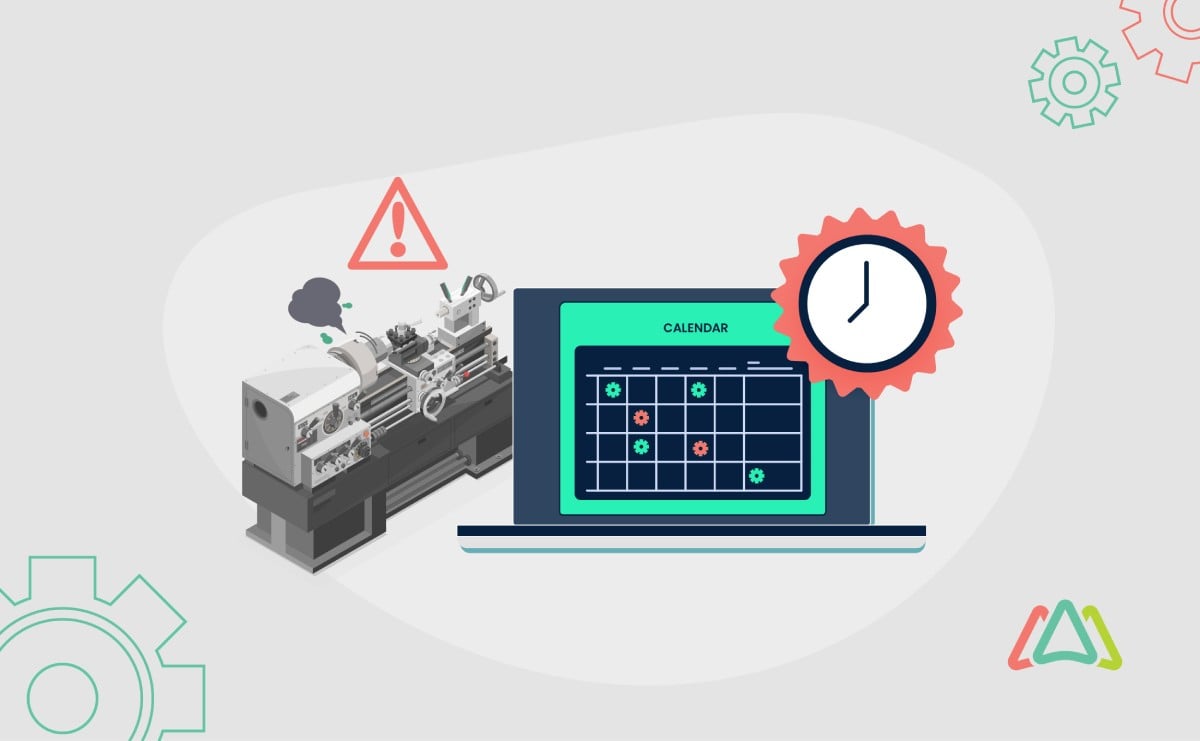
Taking Strategic Pauses with Planned Downtime
Planned downtime is a methodical approach designed to optimize maintenance activities Managing planned downtime effectively is an important factor in maintaining industrial equipment and processes for optimal performance and longevity.
The terms "planned downtime" and "scheduled downtime" are often used interchangeably, and sometimes cause confusion. However, a clear distinction exists between the two. Scheduled downtime refers to any pre-scheduled interruption in operations, including both planned and unplanned events. On the other hand, planned downtime specifically refers to scheduled pauses initiated intentionally for maintenance purposes.
Example:
- Scheduled Downtime: A manufacturing facility plans a routine maintenance shutdown every quarter to inspect and replace components as needed.
- Planned Downtime: Within the scheduled downtime mentioned above, there is a specific period designated for overhauling a critical machine to prevent potential failures.
What is Planned Downtime?
Planned downtime stands as a deliberate and scheduled interruption in normal business operations, strategically implemented for maintenance, repairs, or improvements. Its primary purpose is to enhance the overall reliability and efficiency of industrial processes and equipment. Unlike reactive approaches to maintenance, planned downtime allows organizations to take a proactive stance, addressing potential issues before they escalate into critical failures.
In essence, planned downtime is a preemptive measure that aims to minimize disruptions by strategically allocating time for necessary maintenance tasks. By adhering to a predetermined schedule, organizations can avoid the chaos and financial repercussions associated with unexpected breakdowns.
Planned Downtime vs. Unplanned Downtime
While both planned and unplanned downtime involve interruptions in regular operations, they differ significantly in their nature and consequences. Unplanned downtime is characterized by unforeseen events such as equipment failures, malfunctions, or emergencies, leading to sudden and often prolonged halts in production. In contrast, planned downtime is a proactive choice, allowing organizations to orchestrate controlled pauses for maintenance purposes.
Example:
- Unplanned Downtime: A manufacturing line halts abruptly due to a critical machine malfunction, leading to unexpected production delays.
- Planned Downtime: The same manufacturing line is temporarily halted according to a pre-scheduled maintenance plan, ensuring the timely inspection and upkeep of machinery.
Key Components of Planned Downtime
Planned downtime involves several integral components that contribute to its effectiveness:
- Scheduled Timing: The timing of planned downtime is meticulously chosen to cause minimal disruption to regular operations. It often aligns with periods of low production demand or during planned shutdowns.
- Comprehensive Planning: A well-thought-out plan is essential, detailing the specific maintenance tasks to be carried out, the required resources, and the estimated duration of the downtime.
- Communication: Transparent communication with all stakeholders is vital. This includes informing employees, suppliers, and customers about the scheduled downtime, its purpose, and any potential impact on services or deliveries.
- Risk Mitigation: Identifying potential risks and developing contingency plans are critical components. This ensures that any unforeseen issues during the planned downtime can be addressed promptly, minimizing disruptions.
Understanding these key components is essential for organizations looking to leverage planned downtime effectively, ultimately contributing to the overall success of their maintenance strategies.
The Role of Planned Downtime in Maintenance Management
1. Scheduled Inspections
Planned downtime allows for meticulous inspections of equipment and machinery. By scheduling regular check-ups, organizations can detect and rectify minor issues, preventing them from evolving into major disruptions. These inspections serve as a proactive measure to ensure the health and functionality of critical assets.
2. Equipment Overhauls
Periodic overhauls during planned downtime involve comprehensive assessments and refurbishments of machinery. This strategy aims to extend the lifespan of equipment, enhance performance, and mitigate the risk of unexpected breakdowns. Through strategic planning, organizations can efficiently incorporate equipment overhauls into their maintenance schedules.
3. Predictive Maintenance
Planned downtime facilitates the integration of predictive maintenance strategies. Leveraging technology such as sensors and monitoring systems, organizations can collect real-time data on asset conditions. This data allows for predictive analysis, enabling the identification of potential issues and the scheduling of downtime for targeted maintenance before failures occur.
Benefits of Planned Downtime
1. Improved Equipment Reliability and Performance
One of the primary advantages of planned downtime lies in its ability to improve equipment reliability. By systematically pausing operations for scheduled maintenance, organizations can address wear and tear, identify potential issues, and conduct necessary repairs or replacements. This proactive approach ensures that equipment functions at optimal levels, reducing the likelihood of unexpected breakdowns and minimizing the associated downtime.
Scheduled inspections and overhauls during planned downtime provide the opportunity to fine-tune machinery, calibrate components, and implement adjustments that contribute to sustained reliability. The result is a more robust and dependable industrial infrastructure capable of meeting production demands consistently.
2. Cost Savings and Operational Efficiency
Planned downtime proves to be a cost-effective strategy in the long run. By investing time and resources in scheduled maintenance activities, organizations can avoid the substantial financial implications of unplanned downtime. Unforeseen breakdowns often lead to emergency repairs, costly replacements, and lost production time—all of which can be mitigated through the systematic implementation of planned downtime.
Additionally, the optimized performance of well-maintained equipment contributes to increased operational efficiency. Reduced energy consumption, improved product quality, and minimized waste are among the operational benefits derived from the proactive management of equipment through planned downtime.
3. Extended Equipment Lifespan
Planned downtime plays a pivotal role in extending the lifespan of industrial equipment. Regular maintenance, overhauls, and inspections during scheduled downtime allow organizations to identify and rectify wear and tear, replace worn-out components, and implement upgrades. This proactive care ensures that equipment operates within optimal parameters, reducing the risk of premature failure and ultimately prolonging the overall lifespan of assets. In the long run, this leads to a higher return on investment as organizations maximize the utility of their equipment.
Planning and Scheduling Planned Downtime
1. Creating a Maintenance Schedule
Frequency of Planned Downtime:
Establishing the frequency of planned downtime is influenced by factors such as equipment specifications, usage intensity, and the nature of industry operations. Striking the right balance between too much and not enough planned downtime ensures that equipment is consistently maintained without disrupting operational continuity.
Determining Optimal Timing:
The timing of planned downtime is an art that requires precision. Organizations must consider production cycles, demand fluctuations, and external factors such as market trends. Aligning planned downtime with periods of lower production demand or during scheduled maintenance windows ensures minimal impact on overall productivity. Determining the optimal timing demands a nuanced understanding of the specific operational context.
2. Coordination with Production Schedules
Efficient coordination between planned downtime and production schedules is important for maintaining a seamless workflow. Organizations must align the timing and duration of planned downtime with production cycles to minimize disruptions. Collaborative planning with production managers and teams ensures that maintenance activities do not compromise output targets. This synergy enables a harmonious balance between equipment upkeep and operational productivity.
3. Communication with Stakeholders
Transparent communication is a cornerstone of successful planned downtime implementation. Engaging with stakeholders, including employees, suppliers, and customers, ensures that everyone is informed about the scheduled maintenance activities. Clear communication about the purpose, duration, and potential impact of planned downtime fosters understanding and allows stakeholders to make informed decisions. This proactive approach to communication builds trust and minimizes the likelihood of surprises or misunderstandings.
Best Practices for Successful Planned Downtime
1. Risk Assessment and Mitigation
1.1 Identifying Potential Risks
Organizations must meticulously identify potential risks associated with the planned maintenance activities. These risks range from unexpected equipment complications to supply chain disruptions. By anticipating these challenges, teams can proactively strategize and develop effective solutions.
1.2 Developing Contingency Plans
A robust risk assessment should be accompanied by well-defined contingency plans. Should unforeseen issues arise during planned downtime, having contingency plans in place allows organizations to respond swiftly and decisively. These plans may involve alternative approaches, spare parts availability, or rapid response teams. The ability to adapt and mitigate risks in real-time is a hallmark of effective planned downtime management.
2. Utilizing Technology and Data
2.1 Computerized Maintenance Management Software (CMMS)
CMMS software streamlines the planning, execution, and tracking of maintenance activities. It helps create a centralized repository for maintenance data, enabling teams to plan and schedule downtime with precision. Additionally, CMMS facilitates the analysis of historical data, empowering organizations to refine and optimize their maintenance strategies over time.
2.2 IoT Sensors for Predictive Maintenance
Incorporating Internet of Things (IoT) sensors into equipment provides real-time data on its condition. These sensors enable predictive maintenance by continuously monitoring key parameters, predicting potential failures, and triggering maintenance activities before issues escalate. This proactive approach not only minimizes unplanned downtime but also optimizes the efficiency of planned maintenance by addressing issues precisely when needed.
3. Employee Training and Skill Development
Investing in the training and skill development of maintenance teams is a fundamental best practice. Well-trained personnel not only execute planned downtime activities more effectively but also contribute to the overall success of maintenance strategies. Training should encompass the use of new technologies, safety protocols, and efficient teamwork. A skilled workforce ensures that planned downtime is not only a routine procedure but a well-executed and continuously improving process.
In conclusion, successfully planned downtime is grounded in meticulous risk assessment, facilitated by technology and data-driven insights, and bolstered by a skilled and well-prepared workforce. Implementing these best practices ensures that planned downtime becomes a strategic asset, contributing to the overall success and resilience of maintenance management strategies.
Moreover, planning and scheduling planned downtime requires a delicate balance between maintenance needs and production demands. Crafting a well-thought-out maintenance schedule, coordinating with production cycles, and maintaining open communication with stakeholders are key elements that collectively contribute to the successful integration of planned downtime into the operational fabric of an organization.
TABLE OF CONTENTS
Keep Reading
Ever find yourself checking into a luxury hotel and expecting a relaxing stay, only to find a ...
11 Apr 2025
Organizations are witnessing swift changes in the business environment and confronting a ...
8 Apr 2025
Last month, news outlets and the entire internet was abuzz with the return of NASA astronauts ...
3 Apr 2025
What comes first - CMMS or predictive maintenance? If your answer is either, it is correct. ...
28 Mar 2025
Artificial intelligence (AI) talk has become commonplace. Today, engaging in business-focused ...
27 Mar 2025
Imagine a world where machines predict, diagnose, and fix their issues before they fail. This ...
25 Mar 2025
A facility maintenance plan is at the core of a facility’s operations. This organized ...
21 Mar 2025
Think of managing your maintenance operations like managing a championship sports team. Just ...
21 Mar 2025
The maintenance sector is battling a severe talent shortage that threatens to undermine ...
7 Mar 2025
Manufacturing maintenance is the backbone of industrial efficiency, ensuring machines run ...
5 Mar 2025
No one likes playing a guessing game when equipment breaks down. Yet, maintenance teams often ...
4 Mar 2025
The size of the preventive maintenance software market is discussed in millions of dollars, ...
4 Mar 2025
The organizational structure and corporate hierarchy vary from company to company. Large ...
28 Feb 2025
Maintenance procedures are essential for ensuring the longevity and reliability of machinery ...
21 Feb 2025
Sustainability is no longer just a buzzword; it's a critical component of corporate social ...
20 Feb 2025
A Computerized Maintenance Management System (CMMS) relies on accurate, well-organized data ...
18 Feb 2025
In an era where technology drives operational efficiency, Computerized Maintenance Management ...
14 Feb 2025
A Computerized Maintenance Management System (CMMS) is a key component of modern maintenance ...
13 Feb 2025
Introduction Maintenance management is the foundation of maintenance operations in industries ...
11 Feb 2025
Introduction A Computerized Maintenance Management System (CMMS) is software designed to help ...
7 Feb 2025