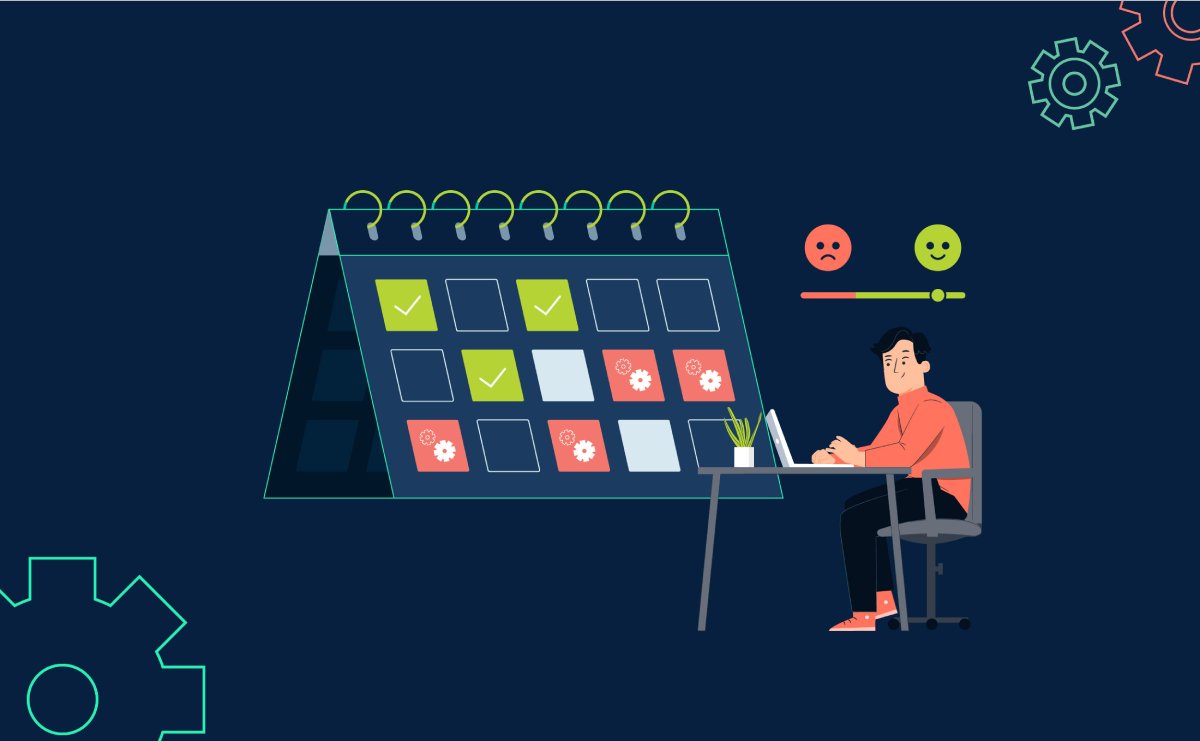
Preventive Maintenance and Employee Satisfaction: A Win-Win Approach
Preventive maintenance is a systematic and planned approach to upkeep machinery, equipment, and facilities. Its importance in organizations is multifaceted, starting with cost savings and operational efficiency. By addressing potential issues before they escalate, preventive maintenance minimizes downtime, ensuring key assets are available and running. This not only safeguards the bottom line by reducing emergency repair costs but also contributes to extended equipment lifespan, maximizing the return on investment.
Beyond financial considerations, preventive maintenance plays a pivotal role in enhancing safety within the workplace. Proactively identifying and rectifying potential hazards significantly reduces the risk of accidents. This not only protects employees but also ensures compliance with stringent safety regulations, shielding organizations from legal repercussions and reputational damage.
A strategic approach to maintenance is not merely about preserving machinery; it is about fostering a conducive work environment that nurtures employee well-being and professional growth. Factors such as job security, career advancement opportunities, and the work environment influence employee satisfaction. In parallel, the concept of work-life balance has gained prominence as employees seek equilibrium between their professional and personal lives. A healthy work-life balance fosters employee well-being, reducing stress and burnout while simultaneously increasing productivity and job satisfaction.
Understanding the relationship between preventive maintenance and employee satisfaction requires a closer look at the daily experiences of the workforce. Unplanned equipment breakdowns and the resulting chaos can contribute to heightened stress levels, impacting job satisfaction adversely. On the flip side, a well-executed preventive maintenance program introduces predictability into the work environment, alleviating stress by minimizing unexpected disruptions. This predictability contributes to improved work-life balance as employees can plan their tasks and personal commitments better.
The Link between Preventive Maintenance and Employee Satisfaction
A well-executed preventive maintenance program can directly contribute to a positive work environment in the following ways:
1. Reduced Stress and Workload
Minimized Emergency Repairs:
One of the primary stressors in many workplaces arises from the unpredictability of emergency repairs. Unexpected breakdowns not only disrupt workflow but also escalate stress levels among employees tasked with resolving these issues promptly. Preventive maintenance acts as a preemptive strike against these emergencies by identifying and addressing potential problems before they escalate. This not only minimizes the need for urgent, high-pressure interventions but also cultivates a sense of control and stability among employees. Knowing that the equipment they rely on is well-maintained fosters a more relaxed and proactive work environment.
Predictable Work Environment:
Stress is lower when work is predictable. When machinery operates reliably and consistently, employees can carry out their tasks without the looming uncertainty of unexpected breakdowns. Employees thrive in an environment where they can anticipate and plan their activities without the constant threat of unforeseen disruptions. A workplace that operates smoothly due to effective preventive maintenance breeds a culture of confidence, reducing stress and increasing overall job satisfaction.
2. Improved Work-Life Balance
Predictable Schedules:
One of the key elements contributing to employee satisfaction is the ability to maintain a healthy work-life balance. Preventive maintenance plays a pivotal role in this by contributing to the establishment of predictable schedules. When equipment is regularly maintained, and downtime is minimized, employees can adhere to more reliable and consistent work hours. This predictability allows them to plan their personal lives with greater certainty, allowing them to spend more time with family and friends and engage in more activities outside of work.
Time for Skill Enhancement and Training:
A well-structured preventive maintenance program not only reduces the time spent on emergency repairs but also opens up avenues for employees to engage in skill enhancement and training. With the assurance that equipment is well-maintained, employees can allocate time to upskill, attend training sessions, or pursue professional development opportunities without the constant pressure of imminent breakdowns. This not only contributes to the growth of individual employees but also enhances the overall competence of the workforce, creating a positive feedback loop of job satisfaction.
Building a Preventive Maintenance Culture with Communication and Training
Effective communication and comprehensive training are pivotal elements for the successful integration of preventive maintenance into an organization's culture, which requires that your employees understand and actively participate in the preventive maintenance process.
1. Ensuring Employee Understanding of Preventive Maintenance
Training Programs:
To bridge the knowledge gap and empower employees, organizations should invest in comprehensive training programs centered around preventive maintenance. These programs should not only educate staff on the importance of maintenance but also provide practical insights into identifying potential issues, understanding maintenance schedules, and using relevant tools and technologies. By fostering a culture of continuous learning, organizations can ensure that employees are equipped to contribute proactively to the success of the preventive maintenance program.
Clear Communication Channels:
Transparent and open communication channels are essential for disseminating information about preventive maintenance. Organizations should establish clear lines of communication to convey maintenance schedules, updates, and any changes in procedures. This ensures that every team member is well-informed, reducing confusion and fostering a sense of collective responsibility. Clear communication also encourages a proactive mindset, with employees feeling confident in reporting potential issues and participating actively in maintaining a smooth workflow.
2. Involving Employees in the Process
Recognizing Employee Expertise:
Employees possess invaluable, first-hand insights into the equipment they operate daily. Recognizing and leveraging this expertise is important for the success of any preventive maintenance program. Organizations should actively involve employees in the decision-making process, seeking their input on equipment performance, potential issues, and improvement suggestions. By valuing and incorporating the knowledge of frontline staff, organizations not only enhance the effectiveness of preventive maintenance but also boost employee morale and engagement.
Encouraging Feedback:
Feedback mechanisms are essential for continuous improvement. Organizations should create avenues for employees to provide feedback on the preventive maintenance processes. Whether through regular meetings, surveys, or dedicated suggestion boxes, soliciting input from employees fosters a culture of collaboration and shared responsibility. Actively responding to feedback not only demonstrates an organization's commitment to employee well-being but also ensures that the preventive maintenance program evolves in tandem with the changing needs of the workforce.
Measuring the Impact
After implementing a preventive maintenance program that emphasizes communication, training, and employee involvement, it becomes imperative for organizations to gauge its impact.
1. Equipment Uptime
Monitoring equipment uptime is not just a metric for machinery; it is a direct reflection of how well a preventive maintenance program is meeting the needs of the workforce. Increased equipment uptime means less disruption to daily tasks, allowing employees to work more efficiently and with fewer interruptions. A consistent and reliable workflow positively influences the overall work atmosphere, reducing stress levels among employees. As the equipment becomes more dependable, employees can take pride in their work environment, leading to a boost in job satisfaction.
2. Maintenance Costs
The financial health of an organization is intertwined with employee satisfaction. Effective preventive maintenance, while incurring some upfront costs, aims to reduce the overall maintenance expenditure over time. When maintenance costs decrease, organizations have more resources to invest in employee benefits, training programs, and other initiatives that contribute to a positive work environment. This financial stability fosters a sense of security among employees, enhancing their job satisfaction and overall commitment to the organization.
3. Regular Surveys
Implementing regular employee satisfaction surveys is a valuable tool for assessing the human side of the preventive maintenance program. These surveys can include targeted questions related to the impact of maintenance on their daily tasks, stress levels, and overall job satisfaction. By consistently gathering feedback, organizations can identify areas for improvement and measure changes in employee sentiment over time. Positive shifts in responses can be indicative of the program's success in positively influencing the work environment.
4. Exit Interviews
Exit interviews are a strategic way to gather insights from departing employees. By specifically addressing questions related to their experiences with equipment reliability, workload, and the overall work environment, organizations can gain valuable perspectives on the preventive maintenance program's impact. Analyzing trends in exit interview feedback can provide actionable insights for refining the program and addressing any lingering issues that may be affecting employee satisfaction.
CMMS: Making Maintenance Managers’ Work Easier
The adoption of a Computerized Maintenance Management System (CMMS) is a game-changer as it centralizes maintenance information, automates workflows, and facilitates the efficient management of assets and equipment. A CMMS can significantly reduce the amount of manual tracking preventive maintenance tasks managers need to do.
1. Efficient Scheduling and Planning
CMMS allows maintenance managers to schedule and plan preventive maintenance tasks with precision. Automated scheduling ensures that maintenance activities are carried out at optimal times, minimizing disruptions to regular operations. This efficiency translates to a more predictable work environment for employees, reducing the stress associated with unexpected equipment breakdowns.
2. Resource Optimization
With CMMS, organizations can optimize resource allocation by tracking inventory levels, managing spare parts, and efficiently assigning tasks. This not only reduces downtime but also ensures that maintenance teams are well-equipped to handle tasks promptly. Employees benefit from this optimization as it contributes to a smoother workflow, enhancing overall job satisfaction.
3. Historical Data Analysis
CMMS stores comprehensive historical maintenance data, enabling organizations to analyze equipment performance over time. This data-driven approach allows for proactive decision-making, identifying patterns, and addressing potential issues before they escalate. The proactive nature of CMMS contributes to a more stable work environment, reducing the workload and stress on employees.
4. Real-Time Visibility
Remote Monitoring leverages Internet of Things (IoT) technology to provide real-time visibility into equipment performance. Maintenance managers can monitor key metrics and receive instant alerts about potential issues, allowing for rapid response. This proactive approach not only minimizes downtime but also alleviates the pressure on maintenance teams, contributing to a more relaxed work atmosphere.
5. Data-Driven Decision Making
Remote Monitoring systems generate a wealth of data about equipment health and performance. Maintenance managers can use this data to make informed decisions, prioritize tasks, and allocate resources effectively. By leveraging the power of data, organizations create a more efficient and responsive maintenance process, positively impacting employee satisfaction through the reduction of disruptive incidents.
Achieving a win-win approach through preventive maintenance involves cultivating an environment where employees thrive. The interconnectedness of efficient maintenance practices and employee satisfaction is undeniable, creating a synergy that propels organizations toward success. As organizations embark on this journey, closing thoughts center on the holistic impact of preventive maintenance:
- Operational Excellence and Employee Well-being: Preventive maintenance is not just a strategy for operational excellence; it is a commitment to fostering employee well-being. By minimizing disruptions, reducing stress, and enhancing work-life balance, organizations create a positive and harmonious workplace where employees can flourish.
- Long-Term Sustainability: Embracing preventive maintenance is an investment in long-term sustainability. The reduction in emergency repairs, optimized resource allocation, and improved equipment uptime contribute to financial stability. This, in turn, enables organizations to invest in employee development, further solidifying the foundation for sustained success.
- Continuous Improvement: The journey towards a win-win approach is a dynamic one. Organizations must embrace a mindset of continuous improvement, utilizing feedback mechanisms, and staying abreast of technological advancements. By staying proactive and adaptive, organizations can navigate challenges and continually enhance the positive impact of preventive maintenance on both operations and employee satisfaction.
TABLE OF CONTENTS
Keep Reading
Ever find yourself checking into a luxury hotel and expecting a relaxing stay, only to find a ...
11 Apr 2025
Organizations are witnessing swift changes in the business environment and confronting a ...
8 Apr 2025
Last month, news outlets and the entire internet was abuzz with the return of NASA astronauts ...
3 Apr 2025
What comes first - CMMS or predictive maintenance? If your answer is either, it is correct. ...
28 Mar 2025
Artificial intelligence (AI) talk has become commonplace. Today, engaging in business-focused ...
27 Mar 2025
Imagine a world where machines predict, diagnose, and fix their issues before they fail. This ...
25 Mar 2025
A facility maintenance plan is at the core of a facility’s operations. This organized ...
21 Mar 2025
Think of managing your maintenance operations like managing a championship sports team. Just ...
21 Mar 2025
The maintenance sector is battling a severe talent shortage that threatens to undermine ...
7 Mar 2025
Manufacturing maintenance is the backbone of industrial efficiency, ensuring machines run ...
5 Mar 2025
No one likes playing a guessing game when equipment breaks down. Yet, maintenance teams often ...
4 Mar 2025
The size of the preventive maintenance software market is discussed in millions of dollars, ...
4 Mar 2025
The organizational structure and corporate hierarchy vary from company to company. Large ...
28 Feb 2025
Maintenance procedures are essential for ensuring the longevity and reliability of machinery ...
21 Feb 2025
Sustainability is no longer just a buzzword; it's a critical component of corporate social ...
20 Feb 2025
A Computerized Maintenance Management System (CMMS) relies on accurate, well-organized data ...
18 Feb 2025
In an era where technology drives operational efficiency, Computerized Maintenance Management ...
14 Feb 2025
A Computerized Maintenance Management System (CMMS) is a key component of modern maintenance ...
13 Feb 2025
Introduction Maintenance management is the foundation of maintenance operations in industries ...
11 Feb 2025
Introduction A Computerized Maintenance Management System (CMMS) is software designed to help ...
7 Feb 2025