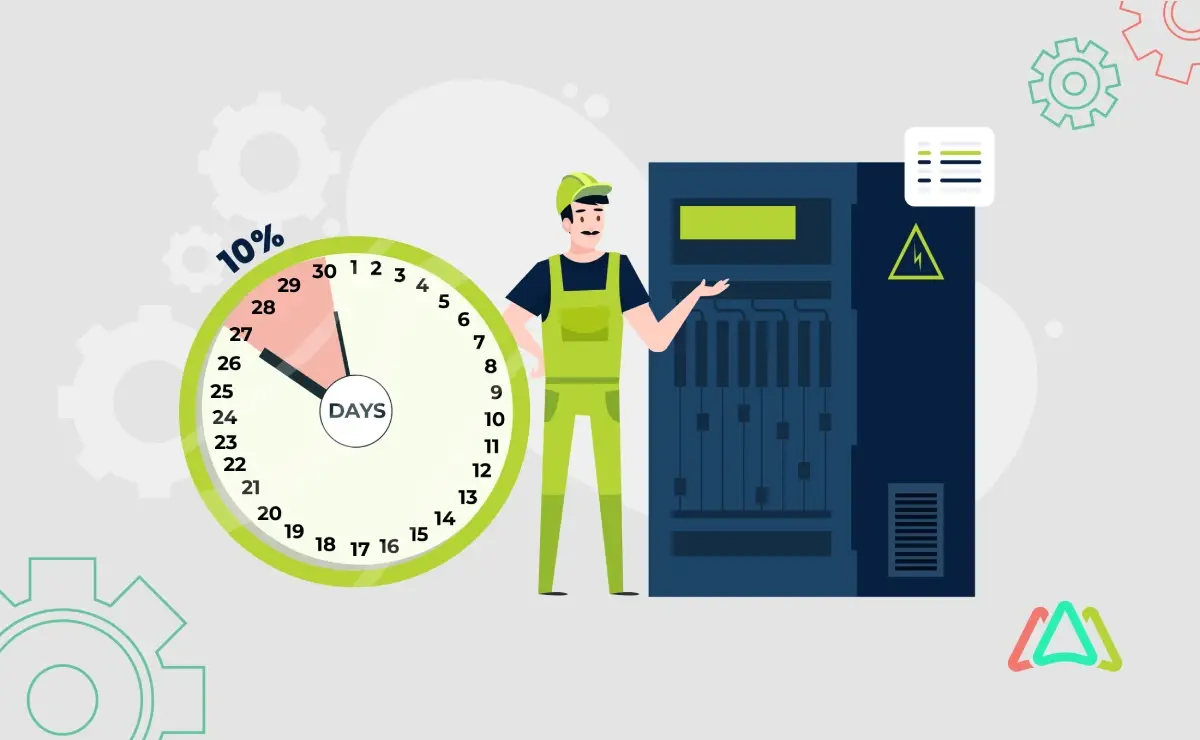
The Rule of 10 Explained and How it Applies to Preventive Maintenance
What is Preventive Maintenance?
Preventive maintenance refers to the systematic approach of carefully maintaining equipment, machinery, and assets through scheduled inspections, repairs, and replacements. Unlike reactive maintenance, which addresses issues after they occur, preventive maintenance aims to prevent breakdowns and failures by identifying and addressing potential problems before they disrupt operations. This cautious strategy involves regular tasks such as lubrication, cleaning, calibration, and parts replacement to keep equipment in optimal working condition.
The concept of preventive maintenance has roots dating back to ancient civilizations, where early forms of maintenance were practiced to keep essential tools and machinery operational. However, modern preventive maintenance practices began to take shape during the Industrial Revolution in the 18th and 19th centuries. As industrialization advanced, the need for efficient maintenance strategies became apparent to ensure the reliability and productivity of machinery in factories and manufacturing plants.
Over time, preventive maintenance evolved alongside technological improvements and management principles. Today, preventive maintenance is a cornerstone of asset management across various industries, from manufacturing and transportation to healthcare and facilities management. The benefits of preventive maintenance are numerous and influence various aspects of business operations.
Here are some of the benefits of preventive maintenance:
Reduced Downtime: By addressing potential issues before they escalate, preventive maintenance minimizes unplanned downtime, ensuring continuous production and service delivery.
Extended Equipment Lifespan: Regular maintenance tasks such as lubrication, cleaning, and part replacements help prolong the lifespan of equipment and assets, reducing the need for premature replacements.
Improved Safety: Well-maintained equipment operates more safely, reducing the risk of accidents and injuries in the workplace.
Cost Savings: Preventive maintenance helps avoid costly repairs and replacements by addressing issues early and preventing major breakdowns.
Enhanced Operational Efficiency: Optimal equipment performance achieved through preventive maintenance contributes to improved productivity and operational efficiency.
The Rule of 10 in Preventive Maintenance
The Rule of 10 in preventive maintenance emphasizes the importance of performing maintenance activities within a narrow timeframe around their scheduled due dates to maximize effectiveness. This rule dictates that all preventive maintenance tasks should ideally be completed within 10% of their designated timeframe. For example, if a preventive maintenance task is scheduled to be completed in 30 days, adhering to the rule of 10 would require that the task should ideally be completed within 27 days, which is within 90% of the timeframe. This consistency in timing helps to maintain optimal operating conditions for the equipment and ensures that preventive maintenance efforts yield maximum benefits.
Benefits of Adhering to the Rule of 10
Adhering to the Rule of 10 in preventive maintenance offers numerous benefits for organizations seeking to optimize equipment performance and reduce operational risks. Firstly, strict adherence to scheduled maintenance activities within a narrow time frame ensures that assets receive timely attention and care. This approach minimizes the likelihood of unexpected failures, mitigating the risk of costly downtime and production losses. By maintaining optimal operating conditions for equipment, organizations can prolong asset lifespan and maximize their return on investment.
Additionally, the Rule of 10 helps to standardize and streamline maintenance practices, minimizing variation in the execution of preventive tasks. This consistency in timing enhances equipment reliability by addressing potential issues before they escalate. Moreover, by ensuring a culture of discipline and accountability in maintenance scheduling, organizations can improve overall operational efficiency and reduce the likelihood of compliance-related issues.
Real-World Examples Demonstrating the Effectiveness of the Rule of 10
Numerous real-world examples have illustrated the effectiveness of the Rule of 10 in preventive maintenance across different industries. In the manufacturing sector, companies that comply with maintenance schedules consistently report reduced downtime and heightened equipment reliability. By prioritizing proactive maintenance measures, these organizations not only optimize operational efficiency but also strengthen their competitive edge in the market.
Similarly, in the healthcare industry, hospitals and medical facilities that implement disciplined maintenance practices experience fewer equipment failures and smoother operational workflows. By adhering to maintenance routines guided by the Rule of 10, these institutions ensure the continuous delivery of critical services while minimizing disruptions.
Preventive Maintenance Compliance
Compliance with preventive maintenance schedules is important for maintaining the reliability, safety, and efficiency of equipment and assets. Adhering to scheduled maintenance tasks ensures that machinery and facilities receive the necessary attention at regular intervals, minimizing the risk of unexpected breakdowns and costly downtime. Moreover, compliance helps organizations meet regulatory requirements and industry standards, safeguarding against potential legal and financial repercussions.
Implementing the Rule of 10 - A Key Strategy in Preventive Maintenance Compliance
Implementing the Rule of 10 represents a key strategy in achieving preventive maintenance compliance, ensuring that maintenance tasks are performed within a narrow timeframe around their scheduled due dates. This principle dictates that all preventive maintenance activities should ideally be completed within 90% of their designated timeframe, emphasizing the importance of timely execution.
One key benefit of ensuring preventive maintenance compliance with the Rule of 10 is improved equipment reliability. By completing maintenance tasks within the specified timeframe, organizations can address potential issues before they escalate, reducing the risk of unexpected failures and costly downtime. This proactive approach to maintenance helps to maintain optimal operating conditions for equipment, ultimately enhancing its reliability and longevity.
Moreover, adherence to the Rule of 10 enhances operational efficiency by minimizing variation in the execution of maintenance activities. Consistently performing tasks within the prescribed time frame streamlines maintenance processes and ensures that resources are allocated effectively. This disciplined approach promotes a culture of accountability and reliability within maintenance teams, leading to smoother operations and improved overall performance. Ensuring preventive maintenance compliance with the Rule of 10 is essential for maximizing the effectiveness of maintenance programs. By completing tasks consistently on time, organizations can enhance equipment reliability, minimize downtime, and optimize operational efficiency.
Challenges in Implementing the Rule of 10
Implementing the Rule of 10 in preventive maintenance comes with its set of challenges and considerations. One major challenge is the need for effective coordination and communication across teams to ensure the timely completion of maintenance tasks.. Additionally, resource availability, such as manpower and equipment, must be carefully managed to support the adherence to maintenance schedules. Furthermore, unforeseen disruptions, such as emergencies or equipment breakdowns, may pose challenges to maintaining the prescribed maintenance intervals.
Preventive Maintenance Software - CMMS
Computerized Maintenance Management Software (CMMS) is a powerful tool designed to streamline maintenance processes and optimize asset performance. CMMS software like Click Maint provides organizations with the capability to plan, schedule, track, and manage all aspects of preventive maintenance activities efficiently. Furthermore, CMMS systems have powerful reporting capabilities that make it easy for maintenance leaders to monitor preventive maintenance compliance and how well the maintenance team is performing against the rule of 10.
Key Features and Functionalities
Asset Management: CMMS allows organizations to create a centralized database of assets, including equipment, machinery, facilities, and infrastructure, enabling easy access to asset information and maintenance history.
Work Order Management: These systems facilitate the creation, assignment, and tracking of work orders for preventive maintenance tasks, ensuring timely completion and documentation of maintenance activities.
Scheduling and Planning: Users can schedule preventive maintenance tasks based on predefined criteria, such as time-based intervals or asset usage metrics, and generate maintenance schedules to optimize resource allocation and minimize downtime.
Task Management: CMMS enables users to define and manage preventive maintenance tasks, ensuring that all necessary activities are performed according to schedule.
Reporting and Analytics: These systems generate comprehensive reports and analytics on maintenance activities, asset performance, compliance levels, and maintenance costs, providing valuable insights for decision-making and continuous improvement.
Integration and Collaboration: Many preventive maintenance software systems offer integration capabilities with other business applications, such as enterprise resource planning (ERP) systems, facilitating data sharing and collaboration across departments.
Integrating Preventive Maintenance Software to Prioritize the Rule of 10
Integrating preventive maintenance software to prioritize the Rule of 10 is a strategic approach that empowers organizations to streamline their maintenance practices and optimize asset performance. This innovative solution combines the principles of preventive maintenance with advanced software capabilities to ensure that maintenance tasks are completed within a narrow timeframe around their scheduled due dates, in accordance with the Rule of 10.
One of the primary advantages of integrating preventive maintenance software is the ability to automate and optimize maintenance schedules. Another key benefit is the ability to track compliance with the Rule of 10 more effectively. These applications offer comprehensive reporting capabilities enabling organizations to monitor task completion rates, identify trends, and measure adherence to maintenance schedules. By tracking key performance indicators (KPIs) such as task completion times and overdue tasks, organizations can ensure that the Rule of 10 is consistently prioritized and enforced.
Finally, preventive maintenance software facilitates collaboration and communication across maintenance teams, enhancing overall efficiency and effectiveness. With features such as mobile access and real-time notifications, maintenance technicians can access task information and updates from anywhere, ensuring that no task falls through the cracks. Integrating preventive maintenance software to prioritize the Rule of 10 offers numerous benefits for organizations seeking to optimize their maintenance practices. By automating scheduling, providing actionable insights, tracking compliance, and facilitating collaboration, these software solutions empower organizations to maximize asset performance and minimize downtime effectively.
TABLE OF CONTENTS
Keep Reading
Ever find yourself checking into a luxury hotel and expecting a relaxing stay, only to find a ...
11 Apr 2025
Organizations are witnessing swift changes in the business environment and confronting a ...
8 Apr 2025
Last month, news outlets and the entire internet was abuzz with the return of NASA astronauts ...
3 Apr 2025
What comes first - CMMS or predictive maintenance? If your answer is either, it is correct. ...
28 Mar 2025
Artificial intelligence (AI) talk has become commonplace. Today, engaging in business-focused ...
27 Mar 2025
Imagine a world where machines predict, diagnose, and fix their issues before they fail. This ...
25 Mar 2025
A facility maintenance plan is at the core of a facility’s operations. This organized ...
21 Mar 2025
Think of managing your maintenance operations like managing a championship sports team. Just ...
21 Mar 2025
The maintenance sector is battling a severe talent shortage that threatens to undermine ...
7 Mar 2025
Manufacturing maintenance is the backbone of industrial efficiency, ensuring machines run ...
5 Mar 2025
No one likes playing a guessing game when equipment breaks down. Yet, maintenance teams often ...
4 Mar 2025
The size of the preventive maintenance software market is discussed in millions of dollars, ...
4 Mar 2025
The organizational structure and corporate hierarchy vary from company to company. Large ...
28 Feb 2025
Maintenance procedures are essential for ensuring the longevity and reliability of machinery ...
21 Feb 2025
Sustainability is no longer just a buzzword; it's a critical component of corporate social ...
20 Feb 2025
A Computerized Maintenance Management System (CMMS) relies on accurate, well-organized data ...
18 Feb 2025
In an era where technology drives operational efficiency, Computerized Maintenance Management ...
14 Feb 2025
A Computerized Maintenance Management System (CMMS) is a key component of modern maintenance ...
13 Feb 2025
Introduction Maintenance management is the foundation of maintenance operations in industries ...
11 Feb 2025
Introduction A Computerized Maintenance Management System (CMMS) is software designed to help ...
7 Feb 2025