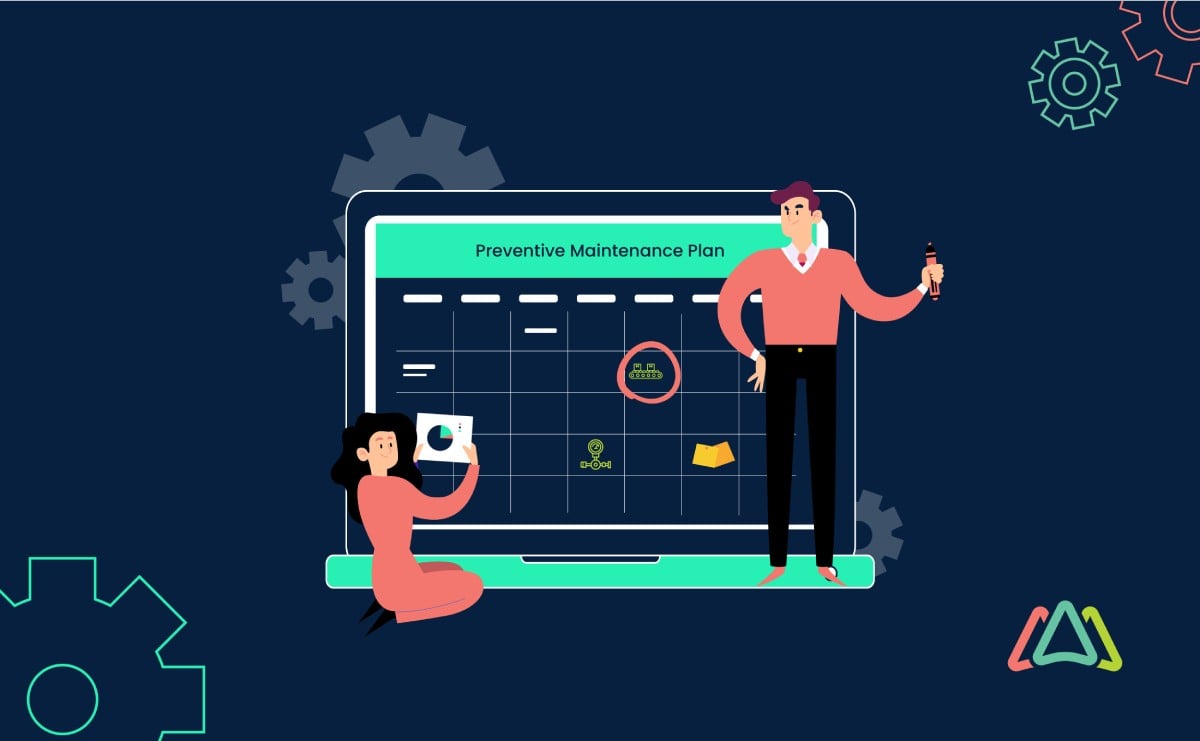
Preventive Maintenance Optimization: Making the Most of Preventive Maintenance
The operational efficiency of equipment and machinery is an important factor that directly influences the success of an organization reliant on them. Preventive maintenance is a fundamental maintenance management strategy for improving the health, reliability, and longevity of assets.
Preventive maintenance serves as a proactive shield against unexpected equipment breakdowns and failure. Unlike reactive maintenance, which addresses breakdowns after they occur, preventive maintenance aims to prevent these issues from arising in the first place. It involves scheduled inspections, routine upkeep, and component replacements, all designed to prevent failures and breakdowns before they occur. This approach not only saves valuable time but also minimizes the adverse impacts of unexpected downtime which disrupts production and revenue.
Preventive Maintenance Optimization (PMO) takes the practice of preventive maintenance to a new level. PMO is not just about performing routine tasks; it's about doing them as efficiently as possible. Preventive Maintenance Optimization involves analyzing data, evaluating risks, and tailoring maintenance plans to suit specific equipment and operational context.
Rather than adhering to generic maintenance schedules, PMO considers the individual characteristics of each asset. This includes usage patterns, environmental conditions, historical failure data, and manufacturer recommendations. By doing so, organizations can maximize the benefits of preventive maintenance while minimizing unnecessary disruptions and costs.
What is Preventive Maintenance Optimization?
Preventive Maintenance Optimization can be defined as the process of refining and fine-tuning traditional preventive maintenance practices to achieve higher levels of efficiency, cost-effectiveness, and equipment reliability. It involves the strategic utilization of data, risk assessment, and tailored maintenance plans to ensure that maintenance activities are performed precisely when needed, minimizing downtime and maximizing the lifespan of assets.
Objectives of Preventive Maintenance Optimization
The primary objectives of Preventive Maintenance Optimization go beyond the traditional goals of standard preventive maintenance. They include:
1. Efficiency Improvement
Optimization aims to eliminate unnecessary maintenance activities that do not contribute significantly to equipment reliability. By focusing efforts where they matter most, organizations can allocate resources more efficiently.
2. Downtime Minimization
Through data-driven decisions and predictive analytics, optimization reduces unplanned downtime by addressing potential issues before they lead to equipment failures.
3. Customization for Variability
Different assets have different operating conditions and patterns. Optimization tailors maintenance schedules to accommodate these variations, ensuring that each asset's needs are met without under or over-maintaining.
4. Risk Mitigation
By identifying critical components and potential failure points, optimization helps mitigate risks associated with equipment failure, safeguarding both personnel and productivity.
Benefits of an Optimized Preventive Maintenance Program
The benefits of implementing an optimized Preventive Maintenance (PM) program are substantial and far-reaching. The following are the key advantages that preventive maintenance optimization brings:
1. Cost Savings
Optimized preventive maintenance programs reduce unnecessary maintenance costs while ensuring critical components receive the attention they require. This results in reduced spending on spare parts, labor, and equipment repairs.
2. Improved Reliability
By addressing potential issues before they become major problems, optimization leads to higher equipment reliability. This, in turn, translates into smoother operations with less disruption to production processes.
3. Extended Equipment Life
Regular, well-timed maintenance increases the lifespan of equipment, postponing the need for replacement. This helps organizations realize the full value of their assets, maximizes ROI, and prevents premature decommissioning.
4. Data-Driven Decision Making
Optimization relies on data analysis to make informed decisions. This data-driven approach improves decision-making accuracy and reduces guesswork.
5. Operational Continuity
With minimized unplanned downtime and better equipment reliability, optimization ensures consistent operations, meeting production targets and maintaining customer satisfaction.
6. Improved Safety
Reliable equipment is safer to operate. Optimization contributes to a safer work environment by minimizing the risk of accidents caused by equipment failures.
Key Elements of Preventive Maintenance Optimization
To understand Preventive Maintenance Optimization, it's important to also understand and implement its core elements. The following are the important components that lay the foundation for a successful optimization strategy.
1. Data Collection and Analysis
1.1 Gathering Historical Maintenance Data
The foundation of optimization is rooted in historical data. Collecting and analyzing maintenance records provides insights into the performance of assets over time. This data allows maintenance professionals to identify recurring issues, assess the effectiveness of past maintenance efforts, and spot patterns that might indicate potential problems.
1.2 Utilizing Condition Monitoring Technologies
In addition to historical data, real-time data and insights should be used. Condition monitoring techniques such as the use of sensors and IoT devices offer continuous data streams about equipment health. These technologies enable organizations to detect subtle changes in performance and identify issues before they escalate.
1.3 Predictive Analytics for Informed Decision-Making
Leverage advanced analytics and predictive modeling to help predict when maintenance is most likely required. Predictive maintenance (PdM) uses historical data, real-time monitoring, and algorithms to predict equipment failure probabilities, enabling proactive action.
2. Risk Assessment and Prioritization
2.1 Identifying Critical Equipment and Assets
Not all equipment has the same impact on operations. Identifying critical assets that have a significant influence on production or safety is important. These high-impact assets demand more attention and precision in maintenance planning.
2.2 Evaluating Failure Consequences and Likelihood
Understanding the consequences of potential failures and the likelihood of those failures occurring is important for preventive maintenance optimization. Equipment validation helps validate and allocate resources to where they are most needed, addressing high-risk components first.
2.3 Creating a Risk Matrix for Prioritization
A risk matrix is a visual tool that maps equipment criticality against failure consequences and likelihood. The equipment criticality assessment matrix aids in prioritizing maintenance activities, and focuses resources toward high-impact, high-risk assets.
3. Customized Maintenance Plans
3.1 Time-Based vs. Condition-Based Maintenance
Optimization involves a shift from rigid time-based maintenance to condition-based maintenance. Instead of adhering to fixed schedules, maintenance activities are triggered based on the actual condition and performance of the equipment.
3.2 Tailoring Schedules to Equipment Usage and Environment
Each asset operates under unique conditions. Tailoring maintenance schedules to account for factors like equipment usage, environmental conditions, and operational context ensures that maintenance occurs at the most opportune moments.
3.3 Incorporating Manufacturer Recommendations
Equipment manufacturers provide guidelines for maintenance intervals and practices. Preventive maintenance optimization involves integrating these recommendations with actual real-life data and conditions to create a comprehensive maintenance plan.
Incorporating these key elements forms the cornerstone of Preventive Maintenance Optimization. By adopting a data-driven approach, prioritizing assets strategically, and customizing maintenance schedules, organizations lay the groundwork for a maintenance strategy that not only improves efficiency but also maximizes equipment performance and reliability.
Steps to Achieve Preventive Maintenance Optimization
Preventive Maintenance Optimization requires a systematic approach that embraces data-driven decision-making and continuous improvement. The following are key steps that help maintenance teams get there.
1. Data-driven Decision Making
1.1 Utilizing Maintenance Management Software
An efficient way to handle the influx of data is through a dedicated maintenance management software. This software centralizes information, streamlines communication, and provides a comprehensive view of equipment health and maintenance history. This central hub enables better decision-making by offering a clear overview of all assets and their maintenance requirements. Examples of maintenance management software are; CMMS, EAM, CAFM and APM.
1.2 Establishing KPIs and Performance Benchmarks
Key Performance Indicators (KPIs) and benchmarks serve as guiding metrics for an organization’s maintenance strategy. Define measurable objectives that align with your organizational goals. These could include metrics like Mean Time Between Failure (MTBF), Overall Equipment Effectiveness (OEE), and maintenance cost as a percentage of asset value.
1.3 Continuous Monitoring and Adjustment of Strategies
Optimization is an ongoing process. Regularly monitor asset performance, collect data, and analyze trends to identify areas that require improvement. Adjust the maintenance strategies based on real-time insights and lessons learned from past maintenance actions.
2. Reliability-Centered Maintenance (RCM)
2.1 Identifying Failure Modes and Consequences
The first step in RCM involves a comprehensive understanding of your equipment's failure modes. Identify potential ways in which your assets can fail and the consequences of each failure. This analysis provides insights into the potential impact of failures on safety, operations, and costs. By categorizing failure modes, maintenance professionals can direct their attention to the most critical areas.
2.2 Selecting Appropriate Maintenance Strategies
Once failure modes are identified, the next step is to select the most appropriate maintenance strategy for each. RCM categorizes maintenance into several strategies, including:
- Run-to-Failure (RTF): Suitable for assets with low consequences of failure or those that are cost-effective to replace.
- Scheduled Restoration (SR): Planned maintenance activities that restore equipment to optimal condition.
- Scheduled Discard (SD): Replacing equipment at fixed intervals before failure.
- Predictive Maintenance (PdM): Utilizing real-time data to predict when maintenance is needed.
- Preventive Maintenance: Time-based (or meter-based) maintenance to prevent failure before it occurs.
Choosing the right strategy for each failure mode depends on factors such as consequences and the likelihood of occurrence.
2.3 Implementing Proactive Measures to Mitigate Risks
Implementing RCM doesn't end once you’ve selected your strategies. It involves proactively taking measures to mitigate identified risks. This includes:
- Design Improvements: Enhance equipment design to reduce the occurrence of failure.
- Procedural Changes: Modify operating procedures to minimize risks associated with specific failures.
- Training and Education: Ensure that personnel are trained to recognize early signs of potential failures.
- Monitoring and Inspection: Implement condition monitoring technologies to detect changes in equipment health and performance.
- Contingency Plans: Develop plans to respond effectively if a failure does occur despite preventive efforts.
Reliability-Centered Maintenance not only improves the reliability of assets but also optimizes maintenance efforts. By focusing resources on critical failure and implementing measures to mitigate risks, organizations can achieve a more efficient and effective maintenance strategy.
3. Maintenance Interval Optimization
3.1 Analyzing Failure Patterns and Trends
The foundation of Maintenance Interval Optimization lies in data analysis. By scrutinizing historical maintenance data and failure patterns, you can gain insights into the typical life cycles and failure trends of your assets. This analysis helps identify common points of failure and determine if there are specific timeframes or usage conditions when failures tend to occur more frequently.
3.2 Adjusting Maintenance Frequency for Efficiency
Armed with data, the next step is to adjust maintenance frequencies accordingly. Rather than adhering to rigid time-based schedules, consider shifting toward condition-based maintenance. If a failure typically occurs after a certain number of operating hours or cycles, adjust your maintenance interval to align with these patterns. This ensures that maintenance occurs just when it's most needed, optimizing asset reliability.
3.3 Balancing Cost-Effectiveness and Asset Performance
While optimizing maintenance intervals can improve asset performance, it's essential to strike a balance between performance and cost-effectiveness. Over-maintenance can lead to unnecessary downtime and increased maintenance costs. On the other hand, not enough maintenance increases the risk of unexpected failures. Therefore, optimizing intervals involves aligning maintenance schedules with both the operational needs of your organization and the financial constraints.
Consider the criticality of the asset, the consequences of failure, and the costs associated with maintenance. This information should guide you in finding the optimal balance between maintenance frequency and operational efficiency.
Preventive Maintenance Optimization Implementation Challenges and Solutions
The road to Preventive Maintenance Optimization is not without its challenges. Implementing a new approach to maintenance requires overcoming various obstacles, but with careful planning and strategic solutions, these challenges can be transformed into stepping stones towards success. The following are common challenges faced during Preventive Maintenance Optimization and ways to overcome them.
1. Resistance to Change
1.1 Communicating the Benefits of Optimization
- Challenge: Transitioning from traditional maintenance practices to new methods is often met with resistance from employees accustomed to the familiar routine.
- Solution: Transparent and effective communication is key. Clearly articulate the benefits of optimization, such as improved equipment performance, reduced downtime, and increased job satisfaction due to decreased emergency repairs. Illustrate how the change aligns with the company's overall goals, fostering buy-in from employees.
1.2 Involving Stakeholders and Employees in Decision-Making
- Challenge: Employees and stakeholders might be more receptive to changes when they have a say in decision-making.
- Solution: Create a collaborative environment where employees and stakeholders are involved in the optimization process. Gather insights from frontline workers who have valuable knowledge about equipment behavior. Their input can shape the optimization strategy, resulting in solutions that are more practical and feasible.
2. Data Quality and Availability
2.1 Addressing Data Gaps through Additional Monitoring
- Challenge: Incomplete or unreliable data can hinder the accuracy of optimization efforts.
- Solution: Invest in additional data collection methods, such as installing sensors and monitoring devices on critical equipment. These devices provide real-time insights into asset health, contributing to more accurate predictions and informed decision-making.
2.2 Ensuring Data Accuracy and Reliability
- Challenge: Relying on inaccurate or inconsistent data can lead to misguided decisions.
- Solution: Implement data quality control measures. Regularly audit and validate collected data to ensure its accuracy and reliability. Invest in data analysis tools that help identify outliers and anomalies, allowing you to filter out erroneous data points.
3. Resource Allocation
3.1 Optimizing Workforce Utilization
- Challenge: Redirecting resources toward optimization might strain existing workforce capacities.
- Solution: Focus on skill development and cross-training to enable employees to handle a wider range of maintenance tasks. This flexibility in workforce allocation allows for more efficient distribution of resources without overburdening specific teams.
3.2 Budgeting for Advanced Technologies and Training
- Challenge: Incorporating new technologies and training programs can strain budgets.
- Solution: Emphasize the long-term benefits and potential cost savings derived from implementing advanced technologies and providing training. Budget for these investments as part of the optimization strategy, considering them as essential tools for achieving greater efficiency and asset performance. Work with vendors and suppliers to assist with building a business case that shows ROI so funding will be approved from executives.
How CMMS Elevates Preventive Maintenance Optimization
A CMMS provides the digital infrastructure needed to implement and execute Preventive Maintenance Optimization effectively. It transforms preventive maintenance from a reactive process into a proactive, data-guided strategy that improves equipment performance, minimizes downtime, and drives overall operational excellence. Here's how a CMMS helps in achieving optimization:
1. Centralized Data Management
A CMMS serves as a centralized repository for all maintenance-related data, including equipment details, maintenance history, work orders, and schedules, and parts and inventory. This centralization makes it easier to access and manage information, reducing time spent searching for records and pulling data for reports. By having a comprehensive view of equipment maintenance history, organizations can identify patterns, failure trends, and determine optimal maintenance intervals.
2. Data-Driven Decision Making
CMMS software allows you to analyze historical maintenance data and real-time equipment health information. With this data-driven approach, you can identify potential failures, evaluate the effectiveness of past maintenance tasks, and make informed decisions about adjusting maintenance intervals. Predictive analytics derived from CMMSs enable proactive actions, helping to prevent equipment failures and minimize unplanned downtime.
3. Task Scheduling and Automation
CMMS platforms provide tools for scheduling and automating preventive maintenance tasks. These systems send out automated notifications to maintenance teams when tasks are due, ensuring that maintenance is performed at the right time. Automation eliminates the risk of overlooking critical tasks and keeps maintenance schedules on track, leading to optimal equipment performance.
4. Workforce Efficiency
By automating task assignment, a CMMS optimizes workforce utilization. Maintenance teams receive clear instructions and priorities, leading to more efficient allocation of resources. Most CMMS systems have calendar views or planning boards which make it easy to assign work to teams and technicians. Technicians can focus on completing tasks rather than spending time on administrative work, resulting in improved productivity.
5. Asset Tracking and Inventory Management
CMMS platforms often include asset tracking and inventory management functionalities. This ensures that the right parts and materials are available for maintenance tasks. Further work orders associated with specific assets include a Bill of Materials (BOM) which clearly lays out the parts and materials used to maintain assets and inventory levels on hand. By integrating inventory management software with preventive maintenance, organizations can reduce downtime caused by lack of necessary components.
6. Performance Analysis and Reporting
A CMMS generates reports and analytics related to maintenance activities, equipment performance, and downtime trends. KPIs and metrics like MTTR, MTBF, planned vs reactive maintenance, TCO, and total cost of downtime can be reported fairly easily from most CMMS platforms. These insights allow for continuous improvement and informed decision-making. Organizations can identify areas that require optimization, track the effectiveness of their strategies, and fine-tune their preventive maintenance plans accordingly.
7. Compliance and Documentation
For industries with regulatory requirements, a CMMS aids in compliance management. It helps track maintenance activities and ensures that equipment maintenance aligns with safety and regulatory standards. Most CMMS platforms allow maintenance managers to pull detailed audit trails on all maintenance activities. This documentation not only helps avoid penalties but also contributes to a safer work environment.
8. Continuous Improvement
Through the analysis of data, performance metrics, and trends, a CMMS facilitates continuous improvement in preventive maintenance strategies. Organizations can identify successful practices, make adjustments based on data insights, and fine-tune their optimization efforts over time.
The impact of Preventive Maintenance Optimization is far-reaching. Not only does it optimize asset performance, but it also improves workplace safety and boosts profitability. By reducing unplanned downtime, minimizing repairs, and maximizing equipment reliability, businesses can achieve a balance between operational goals and financial sustainability.
TABLE OF CONTENTS
Keep Reading
Ever find yourself checking into a luxury hotel and expecting a relaxing stay, only to find a ...
11 Apr 2025
Organizations are witnessing swift changes in the business environment and confronting a ...
8 Apr 2025
Last month, news outlets and the entire internet was abuzz with the return of NASA astronauts ...
3 Apr 2025
What comes first - CMMS or predictive maintenance? If your answer is either, it is correct. ...
28 Mar 2025
Artificial intelligence (AI) talk has become commonplace. Today, engaging in business-focused ...
27 Mar 2025
Imagine a world where machines predict, diagnose, and fix their issues before they fail. This ...
25 Mar 2025
A facility maintenance plan is at the core of a facility’s operations. This organized ...
21 Mar 2025
Think of managing your maintenance operations like managing a championship sports team. Just ...
21 Mar 2025
The maintenance sector is battling a severe talent shortage that threatens to undermine ...
7 Mar 2025
Manufacturing maintenance is the backbone of industrial efficiency, ensuring machines run ...
5 Mar 2025
No one likes playing a guessing game when equipment breaks down. Yet, maintenance teams often ...
4 Mar 2025
The size of the preventive maintenance software market is discussed in millions of dollars, ...
4 Mar 2025
The organizational structure and corporate hierarchy vary from company to company. Large ...
28 Feb 2025
Maintenance procedures are essential for ensuring the longevity and reliability of machinery ...
21 Feb 2025
Sustainability is no longer just a buzzword; it's a critical component of corporate social ...
20 Feb 2025
A Computerized Maintenance Management System (CMMS) relies on accurate, well-organized data ...
18 Feb 2025
In an era where technology drives operational efficiency, Computerized Maintenance Management ...
14 Feb 2025
A Computerized Maintenance Management System (CMMS) is a key component of modern maintenance ...
13 Feb 2025
Introduction Maintenance management is the foundation of maintenance operations in industries ...
11 Feb 2025
Introduction A Computerized Maintenance Management System (CMMS) is software designed to help ...
7 Feb 2025