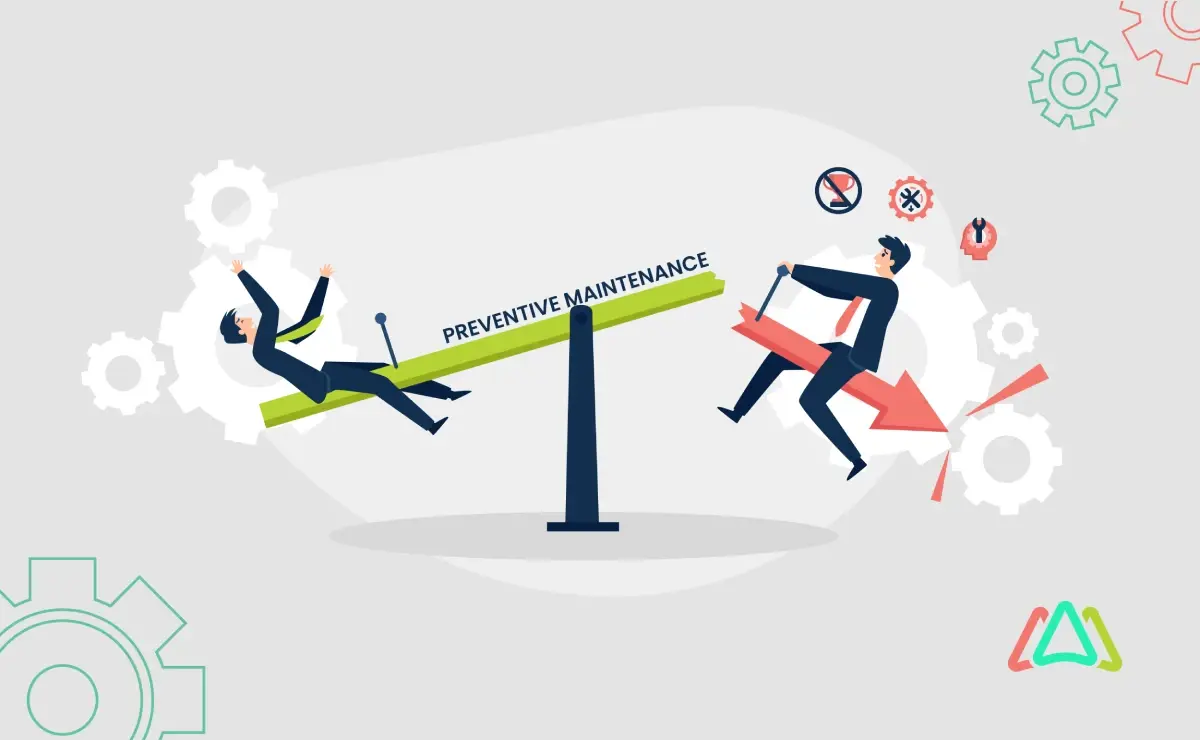
The Preventive Maintenance Paradox: Why Some Companies Do Not See the Results?
A substantial amount of literature exists discussing the topic of preventive maintenance. Various sources, including books, blogs, websites, videos, and podcasts, emphasize the necessity and importance of preventive maintenance in successful maintenance management strategies. Without effective preventive maintenance, maintenance operations suffer, leading to increased costs, downtime, loss of productivity, and missed market opportunities – all of which can negatively impact a business.
Preventive maintenance has received significant endorsement not only in terms of literature but also from companies that have adopted it. One would expect businesses to prioritize making their preventive maintenance programs successful. However, this is not always the case. In his book on preventive maintenance, Terry Wireman references a survey conducted on approximately 5,000 companies over a 40-year period (1965 to 2004). The results revealed that the majority were unsatisfied with their preventive maintenance program's effectiveness. A paradox, indeed. What explains this contradiction? Why does preventive maintenance as an effective maintenance strategy end up receiving poor traction and adoption? Is it like doing regular exercise, perhaps? We all understand that exercise is beneficial for our health, but only a few do it regularly.
A Comprehensive Survey on Preventive Maintenance
Terry Wireman, famous for his research and expertise on maintenance management best practices, explores this paradox well in his published series, “Maintenance Strategy.” In Volume I of the Maintenance Strategy series, titled ‘Preventive Maintenance,’ Wireman references a survey to measure the effectiveness of preventive maintenance programs in 5,000 companies.
Effectiveness is measured by the ability to plan and schedule at least 80% of maintenance activities one week in advance. This benchmark indicates that an organization is transitioning from a reactive culture to a more proactive one.
The first survey covering 5,000 companies was done in 1965. (Figure 1.1)
1965 Survey (Figure 1.1)
Source: Preventive Maintenance, Maintenance Strategy Series, Volume I (5,000 companies survey)
2004 Survey (Figure 1.2)
Source: Preventive Maintenance, Maintenance Strategy Series, Volume I (5,000 companies survey)
Another survey in 2004 (Figure 1.2) produced similar results. Interestingly, the percentage of respondents who deemed their preventive maintenance program ineffective remained nearly constant between the two surveys conducted 40 years apart (1965 and 2004). This raises the question: Why has there been no significant progress in improving the effectiveness of company maintenance programs?
Wireman’s research presents the following three reasons that contribute to this lack of progress.
1. Preventive Maintenance Activities Don’t Get Recognition
Preventive maintenance activities are often overlooked due to their low profile and visibility. To transition from a reactive to a proactive preventive maintenance approach, companies must first overcome this obstacle. In a reactive culture, the "hero technician" who can quickly fix problems is highly valued, leading technicians to believe that preventive maintenance activities are not as important. This issue can only be resolved when upper and mid-level managers demonstrate their appreciation for preventive maintenance activities over the "fix it fast" and “save the day” reactive approach. Without management’s support, technicians will continue to recognize and associate high value to reactive maintenance activities like troubleshooting and fixing it when it breaks. Management needs to communicate the cost savings and impact on the organization and maintenance personnel’s jobs that come with preventive maintenance in order to get buy-in from the team. Communication needs to be ongoing to change the culture and mindset of the maintenance team.
2. Lack and Shortage of Maintenance Skills
Another challenge is the lack of basic maintenance skills among technicians in many companies in the study. They often cannot identify developing problems with equipment components, perform basic lubrication tasks, or make proper adjustments to their assigned equipment. Consequently, even when an organization's structure and culture are conducive to change, these skill deficiencies still hinder the success of a preventive maintenance program.
3. Lack of Discipline in Implementing a Preventive Maintenance Program
The third obstacle is the absence of a disciplined development process for preventive maintenance. It is easy for companies to pay lip service to preventive maintenance or claim that it is ineffective in their industry. However, examples of successful preventive maintenance strategies can be found in every industry.
For instance, Engineered Systems Magazine featured an article on maintaining proper humidity levels in facilities—a typical preventive maintenance function—emphasizing that not maintaining humidity levels properly through preventive maintenance can cost companies thousands, even millions of dollars.
An auto supplier in the US successfully implemented a preventive maintenance program to reduce equipment breakdowns and improve productivity. The PM program helped the company reduce conveyor system incidences by 48%, equipment downtime by 24%, and clear out its overdue work order backlog.
The impact of an effective preventive maintenance program on a company's bottom line is significant. In a Business Week article, it was noted that an electronics manufacturer developed a fixed pattern for preventive maintenance tasks and reinforced them through constant repetition. As a result, electrical breakdowns have been reduced by 80% since 1990, leading to millions of dollars in savings. These examples demonstrate how preventive maintenance can contribute to a company's profitability.
Does the Preventive Maintenance Paradox Still Exist Today?
The year is 2024, and the world has become increasingly modern and digital. Software is now an integral part of daily life, as predicted by Marc Andreessen, who once said that software would eat the world. Indeed, since 2004, the world has been transformed by software. In this software-driven era, one may question whether preventive maintenance programs have found acceptance and effectiveness. While it appears that they have, to some extent, room for improvement.
Preventive maintenance software and Computerized Maintenance Management Systems (CMMS) have become mainstream, with businesses of all sizes adopting strategic digital projects that enable preventive maintenance programs. The global pandemic in 2020 further accelerated this trend. Additionally, the United States is on the verge of a manufacturing renaissance, creating an environment conducive to effective preventive maintenance plans aimed at enhancing business effectiveness.
However, despite these positive developments, the 2024 survey conducted by Limble CMMS revealed some intriguing findings. The survey, titled "The State of Maintenance in Manufacturing and Facilities," examined the main challenges faced by 252 manufacturing and facility maintenance professionals. Although the survey did not directly measure the effectiveness of preventive maintenance programs, two questions within the study yielded noteworthy results.
One question asked participants about their top challenges. Interestingly, downtime and breakdowns emerged as a primary concern, along with skill shortages and aging infrastructure. A significant number of maintenance professionals are utilizing preventive maintenance strategies to address downtime issues. In terms of challenges, 51% were affected by downtime and breakdowns, while 78% relied on preventive maintenance to solve these problems.
It is interesting to note that, despite the reliance on preventive maintenance to address breakdowns, it appears not to be effectively addressing the challenge. This may indicate a need for further consideration behind the numbers. The primary point being emphasized is that the problem or paradox of preventive maintenance programs may still persist and has not been entirely resolved. On the flip side, there is no doubt that adopting a preventive maintenance program and using software like a CMMS to manage it is a step in the right direction. It can reduce costs, improve productivity, and avoid costly breakdowns and interruptions in production.
To learn more, check out our article on the Top 5 Benefits of Preventive Maintenance Software.
TABLE OF CONTENTS
Keep Reading
Imagine you're going through a compliance audit, and the inspector asks for maintenance ...
10 Jul 2025
Maintenance managers understand that disasters are unpredictable and can have a massive ...
4 Jul 2025
Asset lifespan is a key concern for executives and maintenance and facility management teams. ...
3 Jul 2025
Your company recently invested funds and time for new CMMS software, and six months later, it ...
1 Jul 2025
As Computerized Maintenance Management Systems (CMMS) become more connected and cloud-based, ...
1 Jul 2025
Edge computing is an innovative technology that enables data to be processed at the source, ...
24 Jun 2025
Facility management has undergone a significant transformation in recent times. Take, for ...
20 Jun 2025
A facility maintenance plan is at the core of a facility’s operations. This organized ...
19 Jun 2025
In the early days, preventive maintenance could be done effectively with a trained eye and a ...
17 Jun 2025
Sticky notes fall off, whiteboard grids get wiped, and spreadsheets never beep when a ...
13 Jun 2025
Handing a slice of your maintenance workload to a contractor is less about “giving up ...
12 Jun 2025
Downtime in enterprise environments doesn’t just mean a stop in operations; it means lost ...
10 Jun 2025
Understanding equipment functionality is crucial for effective repairs. A clear, systematic ...
6 Jun 2025
Maintenance managers know that every unplanned equipment failure is more than a simple ...
5 Jun 2025
What keeps a facility running smoothly? Initially, many of us may zoom in on its equipment, ...
29 May 2025
In today's digital world, every decision needs to pass the test of strategic and operational ...
27 May 2025
The business world is very different from a decade ago. Technological advancements have grown ...
23 May 2025
Picture this: a maintenance technician inspects a complex pump system. Instead of typing a ...
20 May 2025
For most of the 20th century, maintenance teams mainly applied a reactive approach to ...
9 May 2025
Imagine visiting a manufacturing plant where maintenance technicians gather around a large ...
8 May 2025