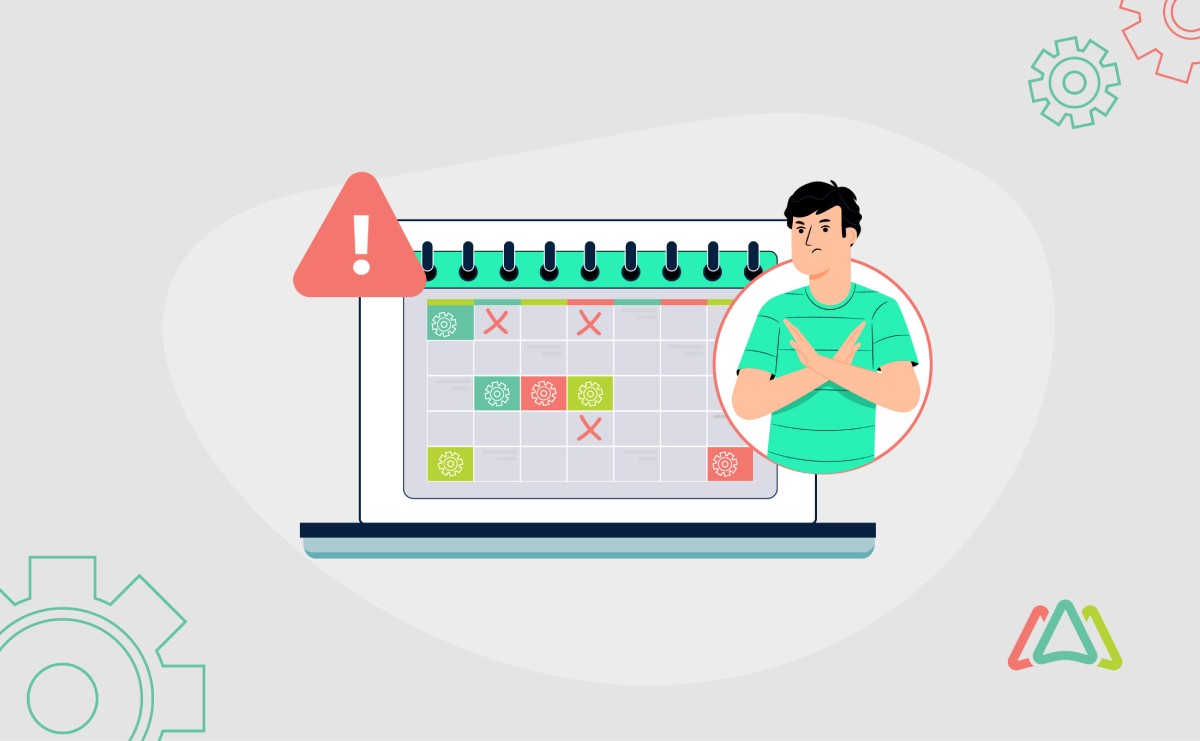
Common Mistakes to Avoid in Preventive Maintenance Planning
Consider a CNC (Computer Numerical Control) machine in an automotive manufacturing plant. This machine plays an important role in shaping and cutting components with precision. Without preventive maintenance, there's a risk of wear and tear on essential components, such as the cutting tool or the spindle. A sudden failure could not only result in costly repairs but also lead to significant downtime, impacting the entire production schedule. However, with a well-thought-out preventive maintenance plan, regular inspections, lubrication, and timely replacement of components can be scheduled, ensuring the CNC machine operates at its optimal efficiency, preventing unexpected breakdowns, and ultimately contributing to a smoother production process.
In industries where every minute of downtime translates to potential losses, preventive maintenance planning is essential. The following are reasons why preventive maintenance planning is so important:
Cost Savings: Investing in preventive maintenance may seem costly, but in the long run, it's a strategic move that saves money. Regular inspections and timely replacements prevent major breakdowns, eliminating the need for expensive emergency repairs.
Increased Equipment Lifespan: Just as regular health check-ups contribute to a longer and healthier life, preventive maintenance ensures that machinery enjoys an extended lifespan. This, in turn, maximizes the return on investment for expensive manufacturing equipment.
Enhanced Operational Efficiency: Unplanned downtime can throw a wrench into even the most efficient manufacturing processes. Preventive maintenance keeps the wheels turning smoothly, minimizing disruptions and allowing for consistent operational efficiency.
Minimized Downtime: Downtime is the arch-nemesis of productivity. By addressing potential issues before they escalate, preventive maintenance significantly reduces the risk of unexpected breakdowns, thereby minimizing downtime and keeping production schedules on track.
This article delves into the nuances of preventive maintenance planning, dissecting common mistakes that often undermine its effectiveness. Understanding potential pitfalls and learning from them will provide insights into optimizing your preventive maintenance strategies. The ultimate goal is to empower manufacturing professionals to implement robust plans that not only prevent costly disruptions but also contribute to the overall efficiency and longevity of their equipment.
Common Mistakes in Preventive Maintenance Planning
1. Lack of Comprehensive Asset Inventory
Importance of an Updated Asset Inventory:
In some ways, a manufacturing plant is like a well-organized orchestra. What if the conductor suddenly realizes an important instrument is missing? An updated and accurate asset inventory (or registry) ensures that every piece of equipment is accounted for. Neglecting this is like playing a symphony without a clear plan, leading to confusion and potential breakdowns.
- Example: In a pharmaceutical facility, a missing entry in the asset inventory for a critical mixing vessel can lead to production delays. The absence of this equipment in the preventive maintenance schedule will result in unexpected downtime and significant financial losses.
Consequences of Incomplete Asset Information:
Incomplete asset information is like navigating a ship through turbulent waters with an outdated map. The consequences are far-reaching – delayed maintenance schedules, unforeseen breakdowns, and increased downtime. Without a comprehensive view of assets, maintenance workers are going blind when performing preventive maintenance, leaving the organization vulnerable to avoidable disruptions.
- Example: An aerospace manufacturer will suffer severe setbacks if an incomplete asset inventory fails to include a vital calibration tool. The absence of this tool in the preventive maintenance plan can lead to inaccuracies in the production process, causing defective components and subsequent expensive recalls.
2. Inadequate Risk Assessment
The Role of Risk Assessment in Preventive Maintenance:
Imagine a tightrope walker without a safety net – that's akin to maintenance planning without adequate risk assessment. Risk assessment is the safety net that identifies and prioritizes potential failures. Without it, maintenance plans lack direction, and resources may be misallocated, leaving critical equipment exposed to preventable risks.
- Example: In the energy sector, a failure to assess the risk of transformer insulation degradation can result in a catastrophic failure. A robust risk assessment will prompt timely preventive measures, avoiding extensive damage and downtime.
Common Errors in Risk Assessment:
Consider risk assessment as a radar system for potential maintenance challenges. However, errors in this system can lead to misinterpretation. Underestimating failure impact or overlooking emerging risks are common errors and should be included for accurate risk evaluation.
- Example: A manufacturing plant may experience major setbacks if it underestimates the risk of conveyor belt failure. The subsequent breakdown will halt production, making the cost of emergency repairs exceed the expense of a well-planned preventive maintenance approach.
3. Incorrect Frequency of Maintenance Tasks
Balancing Over-Maintenance and Under-Maintenance:
Think of maintenance frequency as a pendulum – swinging too much in either direction disrupts the operational rhythm. This segment explores the perils of over-maintenance, akin to over-watering a plant, and the dangers of under-maintenance, similar to neglecting a garden. Achieving the right balance is essential for optimizing operational efficiency.
- Example: In an automotive assembly line, over-maintenance of robotic welding arms will result in unnecessary wear on critical components and added costs for unnecessary maintenance tasks. Conversely, under-maintenance of the conveyor system may lead to unexpected breakdowns, disrupting the entire production schedule.
Tailoring Frequencies to Equipment Types:
Not all equipment ages at the same pace. Tailoring maintenance frequencies to the unique demands of each asset is often neglected but critical. Customization ensures that your preventive maintenance schedule aligns with the diverse needs of your machinery.
- Example: In a food processing plant, a generic maintenance schedule can lead to over-servicing of non-critical equipment, diverting resources from the essential refrigeration units. Tailoring frequencies based on equipment types helps optimize resources and extend the lifespan of critical assets.
4. Ignoring Manufacturer Guidelines
Importance of Following Manufacturer Recommendations:
Manufacturer guidelines are the roadmap to equipment longevity. Ignoring them is like driving with a blindfold on. Aligning with the wisdom of those who crafted the machinery ensures optimal performance and minimizes the risk of unexpected failures.
- Example: A manufacturing company can face extensive downtime and costly repairs if it ignores the recommended lubrication intervals for industrial motors. Adhering to manufacturer guidelines will prevent premature wear and tear.
Consequences of Deviating from Guidelines:
Deviating from manufacturer guidelines can lead to a domino effect of issues – compromised warranties, accelerated wear, and compromised safety. Ignoring these guidelines can result in unexpected costs.
- Example: In the aviation industry, a deviation from the recommended maintenance schedule for aircraft engines can result in a mid-flight failure. Adhering to the manufacturer's guidelines will help avert the catastrophic consequences of this deviation.
5. Insufficient Training for Maintenance Teams
The Impact of Well-Trained Teams on Preventive Maintenance:
Inadequate training compromises the effectiveness of preventive maintenance efforts. There is a direct correlation between well-trained teams and the success of your maintenance strategy.
- Example: In a manufacturing facility, a lack of training on vibration analysis can lead to misinterpretation of equipment health. A well-trained team will be able to identify early signs of impending failure, allowing for timely intervention and preventing extensive damage.
Training Program Best Practices:
Continuous education and hands-on experience ensure maintenance teams are equipped to tackle the challenges posed by modern machinery.
- Example: A maintenance team in a power generation plant needs to undergo specialized training on infrared thermography. This will empower them to identify overheating issues in electrical panels, preventing potential fires and electrical failures.
6. Neglecting Documentation and Record-Keeping
Importance of Documentation in Preventive Maintenance:
Documentation is the unsung hero of preventive maintenance. It helps in tracking maintenance history, facilitating audits, and providing insights for future improvements.
- Example: In a chemical processing plant, inadequate documentation can lead to confusion about the last valve replacement. This could result in a chemical spill during maintenance, causing environmental damage and regulatory fines.
Implementing Effective Record-Keeping Systems:
Explore strategies, tools, and technologies that can elevate your documentation game, turning it from a mundane task into a proactive tool for improving maintenance strategies.
- Example: A manufacturing company that adopts a CMMS will not only improve accessibility to historical data but also facilitate predictive analysis, allowing for more informed decision-making in preventive maintenance planning.
7. Overlooking Environmental Factors
Considering Environmental Conditions in Maintenance Planning:
Machines don't operate in a vacuum; they are subject to environmental influences. From temperature variations to humidity levels, this section emphasizes the need to incorporate environmental factors into your maintenance plans to ensure resilience in the face of changing conditions.
- Example: In a mining operation, overlooking the corrosive effects of high humidity on equipment will lead to premature equipment failure. Integrating environmental considerations into the maintenance plan will extend the lifespan of the machinery.
Adapting Plans to Environmental Changes:
The climate isn't static, so your maintenance plans shouldn’t be either. Adapting preventive maintenance plans to dynamic environmental changes ensures that the equipment remains robust and resilient under varying conditions.
- Example: A solar power facility needs to adjust its preventive maintenance schedule during periods of heavy sandstorms. This proactive adaptation prevents dust accumulation on solar panels, maintaining optimal energy production.
8. Lack of Continuous Improvement
The Role of Continuous Improvement in Preventive Maintenance:
Preventive maintenance isn’t a one-and-done task; it's an ongoing process. The vital role of continuous improvement in refining maintenance strategies helps businesses stay ahead of evolving challenges and ensures that their approach remains effective in the long run.
- Example: A manufacturing plant that implements a feedback mechanism that encourages maintenance technicians to suggest improvements will reduce unplanned downtime and increase overall equipment efficiency.
Establishing a Feedback Loop for Optimization:
Creating a feedback loop that establishes a system that enables learning from past experiences, incorporating feedback, and optimizing preventive maintenance plans for sustained success fosters continuous improvement.
- Example: An automotive assembly line with a regular review process where maintenance teams share insights on equipment performance will build an iterative feedback loop that will significantly reduce both maintenance costs and downtime.
Using a CMMS for Effective Preventive Maintenance Planning
Effective preventive maintenance planning is the backbone of operational success in any industry. To achieve this, organizations can adopt a set of best practices that include asset management, risk assessment, adherence to guidelines, continuous training, documentation, environmental considerations, and regular review for continuous improvement. The integration of Computerized Maintenance Management Systems (CMMS) plays a pivotal role in making these best practices not only feasible but also more efficient and streamlined.
1. Comprehensive Asset Inventory Management
Maintaining a comprehensive asset inventory is fundamental to effective preventive maintenance. A systematic approach to managing assets ensures that organizations have a clear understanding of their equipment, allowing for more precise planning and resource allocation.
A CMMS provides a centralized platform for managing comprehensive asset inventories. It facilitates the creation and maintenance of a detailed record for each piece of equipment, including specifications, maintenance history, barcode or QR code tagging, and associated documentation. With real-time updates and accessibility, a CMMS ensures that the asset inventory remains accurate and up-to-date.
2. Thorough Risk Assessment Analysis
By identifying and prioritizing potential risks, organizations can allocate resources efficiently and implement targeted preventive measures to mitigate the impact of equipment failures.
CMMS software enables organizations to implement thorough risk assessment analysis by integrating risk analysis tools. This allows for the identification and prioritization of potential failures based on historical data, equipment condition, and other relevant factors. By centralizing this information, a CMMS aids in developing a more nuanced understanding of potential risks.
3. Adherence to Manufacturer Guidelines
Organizations should prioritize following recommended maintenance procedures and intervals as outlined by equipment manufacturers. This adherence not only optimizes performance but also minimizes the risk of unexpected failures.
CMMS solutions streamline adherence to manufacturer guidelines by providing a platform to document and track these guidelines for each piece of equipment. Alerts and notifications within the CMMS ensure that maintenance tasks align with the manufacturer's recommendations, preventing deviations that may lead to equipment failures.
4. Continuous Training and Skill Development for Maintenance Teams
Continuous training and skill development are essential for ensuring that maintenance teams are equipped to handle evolving technologies and challenges. A well-trained workforce enhances the effectiveness of preventive maintenance efforts and contributes to the overall success of maintenance programs.
CMMS platforms support continuous training and skill development by providing a centralized repository for training materials and resources. It allows organizations to schedule and track training sessions directly within the system, ensuring that maintenance teams are well-equipped with the latest knowledge and skills.
5. Robust Documentation and Record-Keeping Practices
Robust documentation and record-keeping practices provide a historical perspective on equipment maintenance. Accurate and detailed records facilitate informed decision-making, enable effective troubleshooting, and support compliance with regulatory requirements.
CMMS solutions serve as a digital hub for robust documentation and record-keeping. Maintenance teams can log detailed information about each maintenance task, providing a comprehensive history of equipment maintenance. The digital format ensures easy retrieval and analysis of data, fostering proactive decision-making.
6. Environmental Considerations in Maintenance Plans
Considering environmental factors in maintenance plans acknowledges that equipment operates in varying conditions. Integrating environmental considerations into maintenance strategies allows organizations to adapt their plans to external factors, ensuring equipment resilience and reliability.
CMMS platforms facilitate the incorporation of environmental considerations into maintenance plans. By integrating weather data and environmental conditions, organizations can adjust maintenance schedules to account for factors like temperature and humidity. This adaptability ensures that maintenance activities align with the specific conditions in which equipment operates.
7. Regular Review and Adaptation for Continuous Improvement
Regularly reviewing and adapting preventive maintenance plans is essential for continuous improvement. Organizations should embrace a culture of ongoing evaluation, utilizing feedback loops to identify areas for enhancement and staying agile in response to evolving operational needs.
CMMS plays an important role in the regular review and adaptation of preventive maintenance plans. Through data analytics and reporting features, organizations can assess the effectiveness of their plans, identify areas for improvement, and implement changes. The CMMS acts as a feedback loop, allowing for continuous refinement and optimization of maintenance strategies.
Implementing these best practices in preventive maintenance planning establishes a foundation for operational excellence. Each practice contributes to the overall reliability, efficiency, and resilience of assets. While adherence to these principles is valuable, organizations should also leverage technology solutions, such as Computerized Maintenance Management Systems (CMMS), to streamline and enhance these best practices for optimal results. Through a holistic approach, organizations can proactively manage their assets, reduce downtime, and achieve sustainable success in their maintenance initiatives.
TABLE OF CONTENTS
Keep Reading
Ever find yourself checking into a luxury hotel and expecting a relaxing stay, only to find a ...
11 Apr 2025
Organizations are witnessing swift changes in the business environment and confronting a ...
8 Apr 2025
Last month, news outlets and the entire internet was abuzz with the return of NASA astronauts ...
3 Apr 2025
What comes first - CMMS or predictive maintenance? If your answer is either, it is correct. ...
28 Mar 2025
Artificial intelligence (AI) talk has become commonplace. Today, engaging in business-focused ...
27 Mar 2025
Imagine a world where machines predict, diagnose, and fix their issues before they fail. This ...
25 Mar 2025
A facility maintenance plan is at the core of a facility’s operations. This organized ...
21 Mar 2025
Think of managing your maintenance operations like managing a championship sports team. Just ...
21 Mar 2025
The maintenance sector is battling a severe talent shortage that threatens to undermine ...
7 Mar 2025
Manufacturing maintenance is the backbone of industrial efficiency, ensuring machines run ...
5 Mar 2025
No one likes playing a guessing game when equipment breaks down. Yet, maintenance teams often ...
4 Mar 2025
The size of the preventive maintenance software market is discussed in millions of dollars, ...
4 Mar 2025
The organizational structure and corporate hierarchy vary from company to company. Large ...
28 Feb 2025
Maintenance procedures are essential for ensuring the longevity and reliability of machinery ...
21 Feb 2025
Sustainability is no longer just a buzzword; it's a critical component of corporate social ...
20 Feb 2025
A Computerized Maintenance Management System (CMMS) relies on accurate, well-organized data ...
18 Feb 2025
In an era where technology drives operational efficiency, Computerized Maintenance Management ...
14 Feb 2025
A Computerized Maintenance Management System (CMMS) is a key component of modern maintenance ...
13 Feb 2025
Introduction Maintenance management is the foundation of maintenance operations in industries ...
11 Feb 2025
Introduction A Computerized Maintenance Management System (CMMS) is software designed to help ...
7 Feb 2025